Introduction: Hand Made Acoustic Guitar
Hello everyone,
thank you for visiting my guide to building an acoustic guitar. This is my first proper acoustic guitar that I built using the traditional guitar materials. I made my first guitar 6 years ago when I was 18, but I made it out of plywood so I didn’t count it as my first…
This guitar was made for my younger brother for his surprise 21st birthday gift. I had to keep it a secret from him when I was building, coming up with excuses to why I was in my workshop so much and why I couldn’t tell him what I was working on. I managed to get it finished, a week before his birthday. We were staying at a festival and he asked me to bring my guitar with me when I arrived, but I put his new guitar inside instead. The reaction was priceless! I will put a video at the bottom of the big reveal.
I hope this guide will be helpful if you are looking to making your own guitar. I am by no means an expert in luthiery. If it wasn’t for reading Jonathans Kinkead’s book “Build your own Acoustic Guitar” https://www.amazon.co.uk/Build-Your-Own-Acoustic-Guitar/dp/0634054635 and watching loads of videos, I would never have finished it. I would highly recommend you purchase the above book as it give you every step you need to make your very own acoustic guitar. I am posting this as a prime example that it can be done by following the book.
Right! I’ve been rambling… Lets get to it!
Supplies
Tools needed:
Various hand planes
Set of Chisels
Various grits of sandpaper
Palm Router
Dremel
Router bits
Fret saw
Wood Glue
Masking Tape
C and F clamps… Lots of them
Pillar Drill
Power drill
Drill bits
Bandsaw (Preferably with a 120mm + height)
Steel Rule
Engineers Square
Vernier Caliper
Hand Files, Needle files, Shinto Saw Rasp
Contour Profile Gague
Clothes pegs
Wooden Mallet
Vice
Circle cutter
Bridge clamp
Fret cutter pliers
Fret file
Fret rocker
Fret hammer
Radius sanding block
Inferred Thermometer
Thermocouple reader.
Large Drum sander (If you’re lucky enough to own one. You don’t need one, it just really helps!)
Gunstock Oil (Beretta Tru Oil)
Tack Cloth
Pack of Lint Free Cloths
Lighter Fluid
Jigs and Fixture (Made or Purchased)
If this is your first time building an Acoustic guitar, I would recommend buying a kit. This will allow you build the guitar without the optional jigs and fixtures that are expensive to buy and difficult to make.
Side bender Jig with silicone heating blanket (Not required if you have a kit)
Shooting Board (Not required with kit)
Plate joining jig (Not required with kit)
Mortice and Tenon Router Jig (Recommended)
Guitar Mold (Highly recommend, with or without a kit)
Fret sawing jig (Optional)
Go Bar deck (Optional)
Router binding Jig (Recommended but not essential)
Side bending slats
Material and Hardware:
You should have everything you need from a kit but I will brake it down for you.
Guitar plans and template
Matched back and sides (Recommend to use Indian rosewood. Recommend getting this as a kit because the sides will be pre bent. This will help with one of the most difficult tasks.
Soundboard (Recommend to use Spruce. Get this in a kit because they will be joined like the back)
Rosette of your choice
Binding and purfling
Fretboard blank (Recommend to use ebony)
Fretboard side and face dots
Fret wire (Get this pre bent to the radius you require)
Neck blank (Use mahogany)
Truss rod
Headplate
Bridge (Use ebony like the fretboard. Get this pre made online)
Bridge plate (Used to add strength to the bridge from the inside. Use an offcut of the top or back)
Bridge pins
Nut and saddle (Can be made out of bone but a lot easier to buy plastic ones online)
Heal and tail block (Mahogany)
Bracing material (Made out of spruce)
Back bracing/reinforcement (Made from mahogany)
Threaded Inserts
Kerfing
Tuning pegs
Strap buttons
Pickguard (Optional)
Step 1: Choosing Your Material
If you are buying the material as a kit, you can skip this step.
I find the best way to choose your guitar material is to pick it out at a store by hand. If you're lucky like me, you might have a guitar material supplier not far from where you live. I live in the south of the U.K in Portsmouth and I purchased my material from David Dyke Guitar material suppliers near Hastings. It’s about 2.5 hours’ drive from me. The reason it’s better to pick your material out by hand is because your get to see, feel, smell, hear the wood that you’ll be using. This is very different from buying the material online because you cant be sure that the material you pick, is the same material that is in the stock photo. Plus you don’t get to see all the beautiful detail in the wood. It is important that you do the right checks when picking out material. Like kicking a tyre when looking for a new car…that’s what you’re supposed to do…right?
There is a thing called the tap test. This is where you lightly pinch the top of one of the soundboard pieces, about 2-3 inches from the top and using the other hand, tap in different areas of the piece. Providing you have a good soundboard, you should hear a bell like ring as you bring your ear to the wood. There is no direct science to this by what you are listening for is the resonance of the soundboard. I find the longer the ring and the more bell like sound, the better. If it sound dull and not like a bell at all…don’t buy it.
Step 2: Joining the Plates
If you are buying the material as a kit, you can skip this step.
Right, on to the interesting stuff.
When you buy your wood, the top and the back will be in two book matched pieces. You have to join these pieces together. The first part to this is to make sure that the two edges that you want to glue together, are flat and parallel to each other. The best way to do this is to use a shooting board. A shooting board is a workbench appliance, used in combination with a hand plane, to position and hold the wood while trimming and squaring up the edges and ends.
You can find plenty of YouTube videos on how to make this.
Once the plates are flat and parallel you can now glue them together. This is done in many different ways but this is the way I did it. I made a plating joining jig like the one below. Its pretty simple to make and very self-explanatory. The way it works is by the four offset cams that are around the plate. Once the top clamp in on, you turn the cams anti-clockwise for the left cams and clockwise for the right cams. This pushes the plates together by applying high clamping pressure.
Step 3: Thicknessing the Wood
Then next step is to thickness the wood using a hand plane or a drum sander. A drum sander is the easiest way to thickness the wood because it will accurately take off small or large amounts of material in a short amount of time. These machines can range from £950 – £2500, depending on the size you get. I can’t afford that at the moment, but I hope to get one soon.
So we are going to go with the hand plane. The finished thickness of these pieces are always debatable and depends on the type of material you go for. You can look online to make your own judgment on what thickness to go for, but if you want to follow me then these are the sizes I went for:
Top (Spruce) – 3.0mm to 3.2mm
Back (Indian Rosewood) – 2.5mm to 2.7mm
Sides (Indian Rosewood) – 2.0mm to 2.3mm
Step 4: Bending the Sides
This stage is probably one of the most nerve-racking parts the building a guitar. Things can be very unpredictable when it comes to using heat with wood. It doesn’t have to be very difficult, as long as you put in the correct preparation and safety precautions in place.
If you are buying the material as a kit, you can skip this step (See where I’m going with this?)
You will need to buy or make your own side bending jig. This is quite difficult to make and again there are plenty of videos online that will show how to make one. Once you have the jig, you will need to purchase two silicone heating blankets, designed for heating guitar sides. Arguably the best brand for this is Keenovo. They make silicone heated blankets for all sorts of things. The ones you need are a 6” x 36” blanket and a waist blanket at 150mm x 200mm. Both of these blankets will need the control panels. You will also need two metal spring steel slats to help support the wood during the bending process.
You need a blanket for the waist so that you can focus on heating and bending the waist, without heating and drying out the rest of wood and burning it.
This is how you should prep the wood:
1. Spray the wood with lots of water and let it soak in.
2. Wrap the wood in a backing sheet to help seal in the moisture and help stop the sap from the wood from staining the wood.
3. Then wrap it in aluminium foil.
Then you should layer the wood and blankets in this order from bottom to top.
1. Spring steel metal slat
2. Long silicone blanket
3. Insert the thermocouple
4. Wood wrapped in baking sheet and foil.
5. Waist blanket
6. Final spring steel metal slats
7. This should all be secured with a few clothes pegs.
I don’t have much footage of the bending procedure so I will attached a very helpful video from lmi on to properly bend acoustic guitar sides.
https://www.youtube.com/watch?v=2Qdt4C1hRGA&t=143s
Step 5: Head and Tail Blocks
Once the sides have been bent correctly, you need to insert them into the guitar mould. Use the spreader clamps to push the sides against the inside of the mould to hold them in place securely. Now you can make a start on the Head and Tail blocks.
These blocks are used to hold the sides in shape to the hold and hold everything together. The tail block is the higher block from the two because it will be glued to the bottom of the guitar sides where the guitar is at its largest. The head block will secure the top and is also used to route out the mortice joint that will attach the neck.
You will need to cut these blocks into the correct sizes before they can be glued to the sides. Follow the sizes on your chosen guitar plans and then cut them out on a band saw, table saw or hand saw. The only important sizes will be the length and the width; the length being the most important out of the two.
Before they can be glued, you need to make sure that the sides have been cut to length. You can do this by using the mould as a guide and cut them to length by using a hand saw. Don’t worry too much is the sides don’t meet perfectly, the top will be covered by the neck and the bottom will have an end graft.
It is important that you understand that the guitar top is flat and the back is tapered. This means that when you glue the blocks, you have to make sure that the top face of the blocks are flush with the guitar top.
Secure these blocks with wood glue and clamps.
Step 6: Profiling the Sides
Like I mentioned in the last step, the back is tapered, so you need to profile the sides to match the tapered profile of the back when you glue it down. The best way I found to do this is to trace the plans of the side template and the tape the template to the inside of the sides of the mould. This way you can use this as a guide to follow when you are removing material. Check out the video above where you can see I am using a chisel and a hand plane to remove the material to the template. Make sure you finish with a sanding block.
Step 7: Gluing the Kerfing
If you purchased pre made kerfing, this step will be really simple. Kerfing is used to give the top and the back, a strong platform to clamp to. If you didn’t have this, all the top and the back will have to rest on will be the edge of sides. The video above shows a time lapse of this step.
Step 8: Cutting Out the Plates
Just for the record, when I say "plates", I mean the top and the back. Its just easier to say plates. You need to cut out the “plates” using a band-saw. The best way to prep for this is to trace around a template of the top and back and band saw oversize around that. Make sure that you use the center line of the plates inline with the center of the template. When I cut the top, I forgot this step and cut the top flush with the line. This made things really difficult when it came to gluing on the top to the sides. So make sure you cut them just oversize so you can route the excess away using a flush bearing cutter.
Step 9: Rosette and Sound Hole
This step, you will need some sort of circle cutter. I used a Dremel attachment from Stewmac for this. I had to drill a hole in the center of the sound hole, the same size as the center rotation pin. That became the rotation point when using the tool. I made a few test cuts on a scrap piece of wood and when I thought I had the right adjustments, I made the cut with the circle cutter using a small cutter bit. When I made the cuts, I backed off a bit and removed the tool, multiple times so that there were no sawdust getting stuck under the tool, which will make it not level. Check out the video above on how I did this step.
When you are finished, test the fit with the rosette and when you're happy with it, apply some wood glue and glue it into place.
When the rosette has dried, you will need to plane or sand it flat with the top. You can do this with a finger plane or a sanding block.
Step 10: Back Bracing
The back bracing is used to support the back and give it strength. Yes that’s basically it!
I made a simple clamping jig to glue the bracing to the back. I took a large piece of plywood and screwed down a frame to fit the plates. I then used more of the material I used to make the frame, to use as clamps. It works pretty well and it is so much cheaper than buying a go-deck board.
Once you have glued the braces to the back, you need to start profiling them down using a small plane and some chisels. Basically you are trying to clean them up and make them look nice. I have added a little video above showing how i did this.
Step 11: Gluing on the Back
To do this, you will need wood glue and as many clamps as you can find. You will need to keep the body in the mould so that is stays in the right shape while you are gluing. Apply glue to the edges of the sides and all along the kurfing, locate the back where it needs to be and then start clamping all the way around the back. Once you have finished clamping the body, leave the glue to dry for 24 hours or follow the instructions on the bottle.
Step 12: Top Bracing
For this step you are doing a similar step to the back bracing. You need to trace the templates from your plans for the braces and cut them out on the band saw. Once you have cut them out, you can then start gluing them to the top using the same method as before. Once the glue has set and you can remove it from the clamping jig, you carve the bracing in the same design as your plans.
Step 13: Closing the Box
This step is very exciting. Its time to glue on the soundboard top to the rest of the body, also known as “Closing the Box”. You need to do this method, the same as when you glued on the back. Apply glue to the side edges and kurfing, line up the soundboard with the side edges and then start clamping. Make sure that your clamps don’t mark or dent the wood. You can protect the wood by putting something softer than the clamps, between the clamp and the wood. A couple of layers of card is usually a good one.
Let that set for at least 24 hours and then remove the clamps. Now you can remove the body from the guitar mould.
Step 14: End Graft
This step with fix the problem of the sides not meeting perfectly together at the bottom of the guitar. An end graft or sometimes called a butt wedge is a piece of wood that gets inserted into a routered out pocket. Its primary function is to finish the guitar with no gaps on the join of the sides but its other function is for decoration also. You can fit the but wedge with some perfling to match your bindings to give it a extra look.
The way to do this is to use two pieces of flat wood and stick them to the back of the guitar in an angled position using double sided sticky tape. I used a jig I made that is adjustable to have any kind of end graft you want. Once you have your template in place. You need to use your Dremel and a small cutter and route out the pocket by using the wood as a guide. You can see this in more detail from the photos and videos above.
Step 15: Side Squaring and Binding Prep
Before you can route out the binding channels, you need to make sure the sides are flat and square with the top and back. There are many ways to do this step. The easiest way I found is to use the spring steel slats you used to protect the sides while bending. You can glue sandpaper to the slats and use that to sand the body of the guitar. This works well because you can get to the waist curve easier. If you were to use a flat sanding block, you wouldn’t be able to sand the curved edges. Check the sides with an engineering square until you’re happy with it.
Step 16: Binding Channels
This step can be done in many ways. The method I will show you, I think is the best method you could use. You can buy this jig from Stewmac Luthier Supplies or Elmer Guitars. Elmer guitars jig is cheaper. The arch of the guitar top, and especially the back, will change the router alignment. Without a binding cutter jig, a standard router base will tilt, causing the routed channel to be too deep or too shallow; the bindings won't fit right. The Binding Router Jig keeps the router vertical for a square ledge. Bindings fit correctly. Check the diagram above to better understand the problem.
The Solution!
This jig turns your laminate router into a floating cutter. As you move the body of the instrument into the cutter, your router glides vertically to follow the body's top edge. Bindings fit correctly, so you won't have to scrape them too thin.
When you using this tool, you will need to make sure the guitar sides are square to the base. You can do this with a large engineering square. Once the guitar is fixed to the jig base and square, you can then set up the binding cutter jig. You will have to choose the right cutter to match your binding that you want. Once you have the correct cutter, you can make some test cuts with a scrap piece of wood. Once you are satisfied, you can start cutting. It is very important that your cutters are sharp, otherwise you could tear out the grain or send your guitar across the room. The best cutters to buy in my opinion is Radian Tools. They do a recess cutter made specifically for cutting binding channels. Check out the video to see how I did this.
Step 17: Bending the Binding and Purfling
Once you are happy with your binding channels, you can start bending the binding and purfling to fit to your binding channels. Remember the guitar template you used to bed the sides? Well it works well with bending sides too!! I have a steamer iron that I bought for about £10 online and it works great for bending small pieces of wood.
Start by taping all of the binding and purfling together in one strip. Then tape one end of the set to the end of the bending jig. Start up the steamer and heat the wood. As the wood starts to wilt, tape it down and continue to you have all of the wood taped down to the jig. Keep heating the wood for a further 5 minutes and leave to set for about 24 hours. Once you remove the tape, the binding and purfling should be in the shape of a guitar!
Step 18: Gluing the Binding and Purfling
This step is simple in theory but fiddly in practice. From the diagram above you can see how the binding is installed. If you are using wooden binding and purfling, you can use normal wood glue for this. You will need some specialized binding tape to hold down the binding when gluing. Masking tape will work but you will run the risk of ripping out wood fibers with the tape and you don’t want that. Firstly you need to cut the binding to size. You can do this by taping one end of the binding down in the right position and continue along until you are at the other end. You can then mark off the binding where to cut to size.
Do this in sections, glue tape, glue tape. Work your way along the body until you reach the end. Once the binding is glued and taped down. You can use rope, small bicycle inner tubes or large rubber bands to clamp down the binding. Wrap the chosen material around the whole of the guitar. This will ensure full clamping contact on the binding.
Step 19: Neck Scarf Joint and Heal Block
The first step in creating the neck is to cut the scarf joint and the heal block. A scarf joint is the process of cutting the wood blank at an angle between 10º - 17º and then flipping the wood and then gluing it back down. This will give you, what looks like a headstock. You then need to plane the faces down so you get the proper join. The heal block is quite simple. You need to cut the other end of the wood black into three pieces, big enough to make a heal. You need to then glue the pieces together and let them set. You should be left with what looks similar to the diagram above.
Step 20: Mortise and Tenon
A mortise and tenon joint is the method of joining two pieces of wood together. Woodworkers have been using this method for thousands of years to join two pieces of wood together, mainly when the adjoining pieces connect at right angles. In its most basic form, a mortise and tenon joint is both simple and strong. We will be using this method to join the neck and the body together. The mortise will be on the body and the tenon will be on the neck. This step is quote difficult if you don’t have the correct jig for the job. I would highly recommend that you get a mortise and tenon jig from LMI to do this. I have attached a link from LMI where you can buy the jig and they will give you the information on how to use their jig to get the perfect mortise and tenon join for your guitar. You will need to make sure that the base of the body where the mortise will be routered out, is completely flat. This is important because you need to make sure that you have a good fit from the neck and the body. You can do this by using a flat sanding block and sand the surface in a circular motion. Check the surface with an engineering square on both axis.
Once the mortise and tenon joint had been done. It is important to check the fit and make sure you are happy with how it fits. By doing the previous step of getting the surface flat, you shouldn't have much trouble with the fit of the neck and the body.
Step 21: Fretboard
In this step, you need to make sure your fretboard is completely flat before you start. You can do this using a hand plane. After this you need to determine which side you want to have as the viewed side of the fretboard.
Nearly all fretboards have a radius and you need to create that radius using lots of different methods. The simplest method I found was to buy a radius sanding block (I chose 16” radius) and glue some sand paper to the radius. Once that is done you need to clamp the fretboard to a bench using double sided sticky tape and clamp a fence on one side of both sides of the fretboard to stop the sanding block from running off the fretboard. Chalk up the fretboard and begin running the sanding block along the fretboard. Your aim is to create a radius all along the fretboard. You should be left with a thin, straight, white chalk line in the middle of the fretboard. This is how you know that the fretboard has the correct radius.
The next part is to cut the fret slots. The easiest method I found without buying an expensive gig is to have these 5 things:
· Fret chart (You can get this from Stewmac, the have an online calculator)
· Fretsaw
· Vernier Caliper
· Engineers square
· Stanley Blade
This is the method.
Step one – Check the length of the first fret using the fret calculator.
Step two – Take your Vernier caliper and open it up to the same length as first fret on the calculator.
Step three – Mark the fretboard with the sharp edge of the Vernier to get an accurate length for the first fret.
Step four – Take your engineer square and the Stanley blade and mark a straight line where you marked with the Vernier. You should have straight marked line on the fretboard.
Step five – With some tape, mark the depth on the fretsaw so you don’t saw too deep.
Step six – Take your fretsaw, follow the marked line and cut to the depth of the tape on the saw. You should have a perfectly straight line to the right depth on the fretboard.
Complete these steps on each of the fret slots. Each of the frets slots will get closer together.
Step 22: Gluing the Fretboard to the Neck
You can do this step in many ways. Some people like to use large rubber bands that you can get from stewmac, some like to use small bike inner tubes as the same thing. On this occasion, I just used a 2x1” piece of wood, the length of the neck and clamping them together with c clamps. Once you are confident that you have the fretboard in the right place, you can clamp it tight between the neck and the 2x1 and let it dry for 24 hours.
When the fretboard is on, you will need to cut a slot to fit the nut. Measure the nut you will be using and the cut the slot using a fret saw. Check the fit with the nut to see how it fits.
Step 23: Carving the Neck
This is one of the more difficult tasks on a guitar build to begin with but once you get stuck in, you know exactly what to do and it wont seem as daunting as you may think.
The first part to start will be shaping the headstock. I did this by printing out a template of the headstock design I wanted, gluing it to the headstock and then cutting it on the bandsaw. I then cleaned it up with sand paper and files until I was happy with how it look. There is no right or wrong way to do this, it will just come down to personal preference. Once the headstock is done, you can drill the holes for the tuning pegs. You can follow the template for the hole positions.
The next stage is to profile the neck to the fretboard. This step wasn’t too difficult. I clamped my neck in a table vice and used a hand plane to take away the bulk of the material and then finished it up with a sanding block until I met the edge of the fretboard. Although the fretboard is tapered, it still has a flat side, so it is important that the neck and the fret board are flat but not parallel to the other side of the neck and fretboard.
This is the fun part….Carving the neck! If you are following the book on how to make your own guitar, it will tell you that the neck is thinner at the headstock end and thicker at the heel end. It will give you the finished thickness you need for both ends. I found the best way to make sure that you carve the neck to the correct thickness is to use a large rod file and file down a notch in the neck to the correct depth by using the Vernier Caliper to check the size. You can do this on the headstock end and the heal end. This tip is helpful because it will give you a rough guide on how deep you need to carve.
You need to use a large file rasp or like what I use in the video above, a bought a dragon rasp from eBay. It is basically a series of saw blades, mounted in the shape of a large file. It has a medium and high coarse sides and makes light work of removing material. You can use the rasp in a forward and backward motion and it will take a lot of material away. You need to follow the notches that you made with the file. Once you get closer to the final size, you can rotate the rasp and use the finer side to finish the neck off. Once you are satisfied you have the neck contour, you need to use sandpaper to remove the coarse surface caused by the rasp. This will also help you finish of the necks contour and make it nice and smooth.
If you have another acoustic guitar, you can use that as a guide by using the contour profile gauge and measure the necks profile to match the neck you are carving. Once you are almost finished, a good method is to use sandpaper and pull it side to side like a flossing action and have fall contact on the neck. This should you can a more rounded surface.
The last part is the heel. The heel is more of personal preference compared to the neck because you will not be holding onto the heel. Its more of tying to make it look nice. Follow the same videos and photos that I did to get an idea of what to do and how you might like it to look. You might want to add a heel cap to your guitar. I like to use an offcut from the back for this. It complements the body of the guitar. Trace the top of the heel and cut out of the piece on the bandsaw. Glue the piece down and profile it using files and sandpaper.
Step 24: Gluing the Fretboard and Bolting the Neck to the Body
This part is very exciting. Now it starts to look like a guitar. If you are going for a bolt on neck like me. You need to drill the holes for for the threaded inserts on the neck and the the trough holes for the heel block on the body.
The first step will be to drill the two holes on the body. You will need to drill where the mortise is. Drill two holes, equally apart, just a bit bigger than the diameter of the bolts you will be using. Next you need to insert your neck to the body and try and mark the holes you drilled onto the tenon of the neck. You can use a center punch or a pencil. Put the center punch through the hole and hit it with a small block of wood. You will struggle to hit it with a hammer. This should leave you with two holes marked in the right position for you to drill your holes on the neck.
Drill the holes on your tenon of the neck, the right size drill for the threaded inserts you have chosen and then screw in those inserts. Test the fit by putting on the neck and bolting it on. Now you need to glue on the fretboard. Take off the neck, apply some glue underneath the fretboard, bolt on the neck, and clamp the fretboard down from inside the soundhole with a few c clamps.
Remove the excess glue while its still wet and let sit for 24 hours before you remove the clamps.
Step 25: Bridge
Next you need to carve the bridge. Unfortunately this is a step I missed out because I bought my bridge pre-made....I know..bad isn't it! You can do the same if you want as there a loads to buy on the internet. If you want to make yours, you can find the videos you need to help you on YouTube.
Step 26: Final Sanding
Before the oiling process, you need get the guitar in the best finish you can. The best way to do this is to start with sanding the whole of the guitar, minus the fretboard and the bridge, with a low grit of sandpaper. Something like 240 grit. The sand the guitar again with a slightly higher grit in the 400s. You want repeat this until you have reached a grit of about 2000.
Pay attention to finish of the guitar and focus on getting rid of large scratches and micro scratches. All of these will be enhanced when you apply the oil.
A good tip with the Spruse top is to spray it with water and then let it dry. This will bring up some of the impurities and help you level the wood when sanding.
If you small dents or marks on the wood from dropping something on it...like i did. I learnt a cool tip with a soldering iron and a damp cloth. Put the damp cloth on the area where the dent is and press the hot soldering iron on the cloth. This will create steam which will hopefully swell the wood and make the dent disappear. Once you've done it enough times and it works, you can then sand that area flush with the rest of the wood.
Once you are satisfied with the finish, use some lighter fluid on a lint free cloth to clean and remove any nasties from the guitar.
Step 27: Gluing on the Bridge
Before you glue the bridge, you need to locate it in the right location. You can follow your guitar plans. A good way to do this is to make a copy of the guitar top. Cut out the bit of the fretboard and stick it to the body of the guitar. The plans will show the six holes you will need to drill to string up the guitar. Use a center punch and make the hole positions. Once you take off the template, you will have the hole positions. Drill the holes to the right drill size and now you are ready to clamp. You will need to buy a bridge clamp. You can get the same one as me which is really good i found. I bought it off eBay for about £7. The clamp is pretty self explanatory to use but you can follow the images above. Apply the glue to the underside of the bridge. Put on the clamp and screw in the bolts. Get the bridge lined up and then tighten the bolts. Place the small pieces of wood to protect the bridge and then clamp up the other bolts. Remove the excess glue and let it set for 24 hours. When it dries, remove the clamp and scrap away any remaining glue.
Step 28: Oiling the Guitar
You have now completed all of the woodwork for the guitar!! This next part will take a lot of patience and persistence. In order to achieve the best finish with this oil, you will need to apply about 15 coats of oil. That's right, 15! In between each coat, you will have to wait about 5-6 hours for it to dry before you apply another coat. This whole process will take about 2-3 weeks so you will have to be patient.
You need to mask the fretboard and the bridge before you begin. Masking is the process of using masking tap to cover the masked areas so that they don't get oil applied on them. The bride and the fretboard are the only parts that stay a natural raw finish. Take your time with this so that you apply the tape properly.
Once the guitar has been masked, you need to hang the guitar from the ceiling. Use a metal hanger and cut off the hook end. Use some wire heat shrink on the hook to protect the guitar from getting scratched. Tie some strong rope to the hook and then tie it to a loop on the ceiling. Give the rope a strong tug so to test the strength.
Once you are happy the rope and hook, you can start on the tools and equipment needed for the job. You will need to make a "mouse" to apply the oil. In luthiery terms, a mouse is a round pad made out of lint free cloths. You can tie the end with an elastic band. You will need to wear gloves when applying the oil so you don't mark the oil finish. So you have the oil, the mouse and the gloves. The last thing to do is to use a tac cloth to pick up all of the dust from guitar so it doesn't get under the finish.
The technique:
Apply the oil to the mouse and hit it against a block of wood to rinse out the pad. The key to applying the oil is to apply it as thin as possible. You need to apply it thinly so that the oil drys properly and so it is also flat with the rest of the finish. It also wont look as good think thick layers in between each other.
You should start with the top and apply the oil in a circular motion. Take care when around the bridge and the fretboard. You can hold on to the neck to help keep the guitar still when applying the oil.
Next do the sides in the same way. Then the back, heel and the the headstock. You can do all of this while holding onto the the neck. To do the neck, whilst still having stability, do can use press on the fretboard, on the masked side and apply the oil up and down the neck.
Now comes the patient part. You must wait about 4-6 hours for the oil to dry, or until the finish is no longer sticky. When you are ready to apply the next coat, use another tac cloth to get rid of the dust.
Do this between 12 and 15 times until you are happy with the finish. Its a very exciting part because the guitar will look better with each coat. When the last coat has been applied, you should wait between 1-2 weeks for the finish to cure and then you can take the guitar off the rope.
Step 29: Nut and Saddle
If you buy the nut and saddle pre made, they should come with the slots for the strings. You will need to glue in the nut but not the saddle. Apply some glue to the nut and and insert it into your nut slot and move it into position. The saddle should fit into the saddle slot on the bridge but it may need sanding down to fit.
Step 30: Tuning Pegs and Strings
Now comes the final stage, putting on the strings. You will need to put on the tuning pegs first. The tuning pegs are quite simple. You will have a set of right pegs and a set of left pegs. If you start with the right side, the pegs should point right..obviously, and the large gear or the case part on the bottom. This will leave you with the left sides. Each tuning peg will come with a small screw. You will need to drill and small hole to fit the screw. I find the best way to drill in the right place is to put in the tuning peg, line it up and the with a centre punch, mark where inside the small whole of the tuning peg. This should leave you with a small guide to where to drill the hole. Do this on all six holes. Drill the hole, insert the peg and then wind the screw in.
Next you will need to put in the strings. Before you do this, you will need to make sure the bridge pins fit properly. The bridge pins are tapered, so you will need to make the holes tapered too. The best way to do this is to get a tapered reamer too. They make these specially for guitar building. Use the reamer on the holes and check the fit with the pins. Keep trying until you are satisfied with the fit.
Now you can string up the guitar. You shouldn't need my help with this step :)
Step 31: The Big Reveal
As I said at the beginning, I made this guitar for my brothers 21st birthday and i thought you might like to see the video of when i revealed it to him :)
I hope you guys enjoyed my tutorial on how to make an acoustic guitar from scratch.
I have entered the instrument contest with this instructable, so it would mean the world to me if you could vote for me :)
Please follow my pages
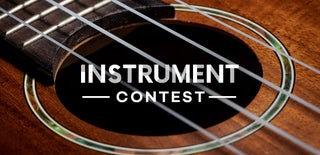
First Prize in the
Instrument Contest