Introduction: Handmade Copper Fork
This is an instructable documenting the making of a copper fork I gave to my sister for Christmas this year. Whilst on holiday in Denmark 2 years ago I made a copper fork which my sister has always admired. So, this year, for Christmas I decided to make her one and document the process.
Originally I made the fork without any power tools since that was what I had available on holiday. This time around the process was much the same other than an electric drill rather than a hand brace drill.
Please take a look at the video above which shows the project from start to finish.
Step 1: Tools
The tools you need for this project are fairly limited. I had most of the tools already but the slightly more specific tools (often used in jewellery making) I got from Cookson Gold, you can also find them on Amazon or eBay too.
Tools include:
Step 2: Materials
There are only 3 materials that make up the fork:
- A piece of 1.5mm thick copper plate for the fork head (my material is actually gilding metal, a copper alloy which is 95% copper and 5% Zinc)
- A piece of wood for the handle
- 2 brass pins to connect the fork head to the handle
Step 3: Bench Peg
A bench peg is a tool often used by jewellers. It makes it easier to work with and cut small pieces of metal. I made mine from a scrap of MDF and secured it to a table with a G clamp. To make the peg I drilled a 10mmø hole about 15cm from one end of the MDF. Next I cut two lines to meet that hole, creating a tapering slot as you can see in the above image.
This is a super simple alternative to spending £5 on a pre-made peg, but I suppose if you don't already own a G clamp perhaps it isn't such a bad deal!
Step 4: Choose Your Fork
I started by finding a fork shape and size that I liked and thought would suit my sister well. The picture above shows the copper fork I made two years ago alongside a range of forks I had in my cutlery drawer. You'll notice that the copper fork has a slightly unique prong formation. I did this because I thought it would offer greater strength to the prongs, although now I'm not sure it is necessary. However, I quite like the design and haven't seen it elsewhere so decided to make the new one with the same formation.
Step 5: Trace and Cut
Taking your chosen fork as a guide trace out the fork head shape onto the copper. The reasons I only cut the fork head rather than the entire fork were:
- To save on material
- A much deeper adjustable saw frame would have been required
When cutting the copper ensure that you are sitting low down with your work just below eye level. This ensures you keep your saw at 90º to your work and helps you to follow your markings. You should saw with long even strokes, this will also prevent saw blade snapping. When cutting tight corners and curves you are best off pivoting the metal rather than the saw blade. As you'll see in my video I didn't always demonstrate a brilliant sawing technique.
Have patience! This is by far the hardest and longest part of the project, it took me a good few hours to cut out the fork head but that final stroke really was satisfying.
Once it is cut out quickly going round it with a set of needle files will ensure a nice clean smooth finish. You could also use some sand paper.
Step 6: The Handle
I've done a bit of spoon carving recently and really enjoyed working with green (recently cut) wood. Whilst walking the dogs I came across a damaged sapling. Using my pocket Swiss army knife I cut the sapling and striped the smaller branches off.
Once I got the piece home I striped the bark off and trimmed the piece of wood to the size of the handle required. I decided to go for a slightly more slender handle with this fork than the one I made first time around.
To secure the fork head to the handle a slot needs to be sawn into which the fork head will fit. Luckily, the saw blade from my Swiss army knife creates just the right sized slot. I also rounded off the end of the handle to create a more comfortable detail.
Step 7: Hammer Time
To create the curved profile of the fork head I beat the copper with a ball pein hammer. To help this process you can carve a recess into a scrap of wood with a crook knife. Using this recess you can beat the copper into a variety of curves and form the fork head. I really like the beaten copper aesthetic so I hammered both sides all over.
Step 8: Bring It Together
The last step is join the fork head to the handle, this is done with two brass pins. Position the head in the slot in the handle. Drill a hole all the way through (handle, copper, handle). Use a drill bit the same diameter as the brass pin you are using. Once you have drilled one place a pin through the hole. This will make sure the position is maintained when you drill the next hole.
Once both holes are drilled and both pins are inserted, trim the pins so that about 1-2mm is protruding. Place the fork on something hard, an anvil if you have one, and carefully tap the protruding pins. Make sure you hit directly down on to the pin so that it doesn't bend off centre. Keep taping until the pin takes on a mushroom shape. This way the pin will be locked in to place and will hold the fork head in the handle slot. For extra security you could use some epoxy. However, I have been using the original fork for 2 years (almost everyday) without any problems and that is just held with two brass pins.
I hope you have found this instructable useful, please leave me any comments or questions you have.
Happy making!
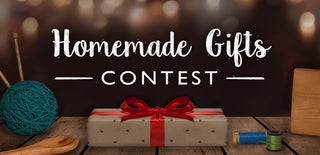
Participated in the
Homemade Gifts Contest 2017
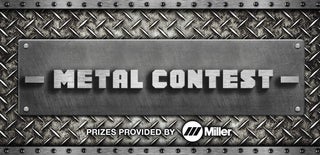
Participated in the
Metal Contest 2017