Introduction: Hanging Cam Stand
In this day and age we all seem to be recording every movement either for keepsakes or for some chance to be a youtube sensation. Ask a hundred kids and seventy-five will tell you they want to be a youtube star some day. It's this same allure that got me started with recording the things I make around my shop.
Not having ever been a part of the video scene, I didn't know much about camera set ups or the importance of good camera placement to catch that perfect angle. I'm not now an expert, but I have learned a few things. One of those important lessons is that you need a sturdy foundation for a camera. Camera tripods are a fantastic way to get the stability you need but they come at a price: a huge footprint. My tripod alone, fully extended from the floor, has a 36" diameter base. It's a tripping hazard and in my small shop can be quite awkward to place, not to mention how cumbersome getting that perfect shot can be!
The other important note to add to this is how dangerous those tripod stands can be, especially in a workshop. I'm not talking about tripping hazards, I'm talking about dangerously trying to align a shot while putting yourself in a position you wouldn't normally be in so that you can take advantage of that shot. This is something that is quite regular for me on my lathe, and it is, quite honestly, an accident that was bound to eventually happen.
Enter my hanging cam stand. Now, in particular places in my shop where that 3' diameter no go zone makes filming at best difficult and worst, dangerous and impossible, I have a hands free, no footprint area I can easily move around in. I have a nearly perfect shot as I can easily position my camera in multiple ways that can get closer to the action without being a hindrance.
Materials List
- 3/4" copper pipe, length will be dependent on needs
- 3/4" dowel rod, length will be equal to the copper pipe
- 3/4" dowel rod, 4 1/2"
- Scrap 2x4x(length will be equal to the dowel rod)
- Sunpak 5858 Tripod Head (or an equivalent head): https://amzn.to/2GPIOJV
- Scrap 1x4x6"
- Scrap hardwood 1x4x16"
- #6 2 1/2" bolt (threaded up to the head)
- (2) #6 T-Nut
- (2) #6 Washers
- (2) 5/16" T-Nut
- (2) 5/16" x 3" carriage bolts
- 5/16" x 2" carriage bolt
- 5/16" washer
- 5/16" lock nut (or lock washer and nut)
- 81 mm magnet with a metal backing (I got mine from Harbor Freight)
- NIBCO 3/4" 1-Piece (Solid) Socket PVC Flange
- (10) #6 1/2" rounded head sheet metal screws
- Thread locker
- Glue
Metric Equivalents
- 20mm copper pipe, length will be dependent on needs
- 20mm dowel rod, length will be equal to the copper pipe
- 20mm dowel rod, 11.5cm
- 4cm x 9cm x (length will be equal to the dowel rod)
- Sunpak 5858 Tripod Head (or an equivalent head): https://amzn.to/2GPIOJV
- Scrap 38mm x 89mm x 15cm
- Scrap hardwood 38mm x 89mm x 40cm
- 4mm x 65mm bolt (threaded up to the head)
- (2) 4mm T-Nut
- (2) 4mm Washers
- (2) 8mm T-Nut
- (2) 8mm x 80mm carriage bolts
- 8mm x 50mm carriage bolt
- 8mm washer
- 8mm lock nut (or lock washer and nut)
- 81 mm magnet with a metal backing (I got mine from Harbor Freight)
- 20mm PVC Flange
- (10) 4mm rounded head sheet metal screws
- Thread locker
- Glue
Tools Needed
- Grinder/hacksaw
- Miter saw/handsaw
- Tablesaw
- (optional) Hot glue gun
- Drill press/Drill
- 3/8", 3/32", 3/16", 3/4" drill bits
Tools I Used (Optional)
- Framing Square
- Drill press vice
As an amazon associate I earn from qualifying purchases.
Step 1: Making the Dowel Extension
This project is able to telescope to the desired height, and then locked. In this first step, we need to make the dowel extension, which is basically just splitting the dowel in half and re-gluing about an inch (2.5cm) on both the top and bottom. A small bolt will fill this channel later and allow the extension to slide up and down with the re-glued section working as static stops.
The overall length of my hanging cam stand is about 40 inches (101cm), so that means I need to make my 3/4" (20mm) dowel about 20 inches (50.5cm) long. I took a scrap 2x4x20" (4cm x 9cm x 50.5cm) and made several passes to create a groove that was exactly equal or a hair less than my dowel. After I cut out the groove on the scrap wood I squeezed the dowel rod into the groove.
Using a few drops of hot glue would be good at this point to keep the dowel in the jig while you run it through the tablesaw, or you could use another scrap of wood behind the dowel rod jig to chase it. You'll want to do this as not doing either of those two things will allow the rod to push through and come back at you dangerously. Find the dead center of the rod, center it on the tablesaw blade and cut that dowel in half.
Once the dowel is split in half, cut two pieces of scrap wood into 1" (2.5cm) long by 3/4" (20mm) wide with a depth of about 3/16th of an inch (4.75mm). The thickness of this groove between the two glued points will need to be able to run the #6 2 1/2" (4mm x 65mm) bolt, but not so thick that your new dowel assembly won't fit in the copper tube.
About the best way I can suggest doing this is by setting your table saw and running the scrap of wood about 3/4th's the way through, turning off the saw and removing the board, then cutting the lengths of scraps to size.
If you watch the video you'll see that I used a combination of hot glue and wood glue to form this newly slotted dowel rod. It's not necessary but it certainly makes it much easier than trying to clamp the wood and waiting for it to dry.
Step 2: Cutting the Copper Tube, Checking the Fit
Cut the copper tube so that it's the same size as your newly made dowel rod. I used my miter saw but it can very easily be done with a hacksaw.
This is a small step in this instructable, but it is absolutely CRUCIAL! It MUST slide freely inside of the tube. If you find that it doesn't, grab some sandpaper, a chair, maybe a snack...and sand sand sand until it moves freely. If you find that the tube slides way too freely without any friction at all (holding it up and it slides right out onto the floor effortlessly), you need to go back a step and make those inside spacers a little thicker.
Also, make sure the #6 2 1/2" bolt (4mm x 65mm) slides easily inside of the newly created dowel slot.
Step 3: Cutting Out the Head Plate
Now it's time to cut out the head plate, or the plate where the tripod sits and the dowel fits in to. I'm leaving a picture with a quarter next to it so that you can set it to scale with your printer*. This is a very simple design that I spent very little time with, but so far it works well. I will say this, measure your camera length. My camera is 5 inches (13mm) long. If yours is longer, cut out the pattern, cut in half between the two circles and glue one side to your hardwood block. Attach the other half of the paper a slight ways down from the other to make up for the size. Beware though, this is the only mount that I've tested. I do not know how it'll act with any other sizes, although I don't think it should be a problem.
Very simply put, drill a hole through both holes on the template. These holes will be 3/4" (20mm). Press an awl, or nail into the center X before you drill (so your drill bit doesn't wander) and be sure to keep your hole as straight as possible. The body will need to be cut out on a bandsaw or some type of handsaw. There are also cuts that will need to be made on both sides, up to the hole you drilled (3:18 in the video), but do NOT do that now, even though I did it in the video. I had to deal with chip out that could have ruined the entire thing.
* If I take the image and print it at in landscape at 40% reduced size, I can line a quarter up perfect to the quarter on the page.
Step 4: Fitting the Plate With the Dowel Rods
Now let's put the dowels in and see how we're doing.
In one of the holes we're going to put the 3/4" dowel that's 4 1/2 inches (11.5cm). The tripod head will slide onto that rod and will be tightened by the knob that came with it. I strongly recommend buying the Sunpak 5858 as it is the one that worked with mine. Please don't get upset later if you chose a different tripod head and these plans don't fit it.
The new dowel rod with the slot in it that we created...that goes in the other hole. If either don't fit right, pull out that sand paper and make it so that it fits in there snugly, but not too loose. If both work well...Good! Let's move on.
Step 5: Adding the Bolt and Locking Knobs
Now let's drill out the lock hole in the copper pipe. We'll be using the #6 2 1/2 (4mm x 65mm) bolt and the (2) #6 (4mm) t-nuts. This is a step that you will NOT see in the video as I upgraded the lock, post upload. I'll be providing links to the updated set up here that will not be available elsewhere...you are lucky instructable patron!
In this step we will create knobs that will work in tandem with the bolt through the copper and your newly created dowel rod. Creating knobs could be an entirely different instructable altogether and can encompass many different tools. In this project I will make the knobs about as simple as I can make them using squares instead of circles.
First, take your hardwood and cut 1 3/4" (4.5cm) squares. Draw diagonals and in the center, drill holes in both that are larger than the t-nut barrel, on the underside. Press both into the holes, tap on the tops with a hammer, or heck, a brick, and pull the t-nut off. You'll see 4 indentations. Drill those indentations enough to get the prong width in and then press the t-nuts into the wood squares. Drill a couple of holes next to each t-nut and put a #6 1/2" (4mm) rounded head sheet metal screws in each hole, securing the t-nut.
Next, grab your bolt and put thread locker on the threads under the head and thread the bolt through face of the nut so that it protrudes out of the back of the knob. Add a #6 (4mm) washer to the bare wood side and push the bolt through both the copper tube and your new dowel rod center, adding another #6 (4mm) washer on the opposite side. Put the second knob on by running the bolt through the wood side this time and out the nut on the opposite side. Be sure to follow these instructions very carefully as t-nuts can push themselves out if you don't put them in correctly.
Step 6: Locking Knobs on the Camera Head Plate
I didn't make a video on the locking knobs for the camera head plate, but it's the same as step 5 locking knobs for the telescope, except that you will be using a large t-nut (5/16" (8mm)) and 5/16 x 3" (8mm x 80mm) carriage bolts. As far as drilling out the holes on the side for the locking part of the plate, I measured in 3/8" by 3/8" (9.5mm x 9.5mm) using a 3/8" drill bit (9.5mm) in the video. WATCH the video, it makes this process much more self explanatory.
After drilling the holes, cut through to the other holes drilled on top using a bandsaw. This kerf opening will allow the hole to squeeze and lock the shaft you put in. Another important note is that while I used pine for this cam head plate, I strongly encourage you to use a hardwood for strength.
Step 7: Creating a Magnetic Base
Let's make a magnetic base! The magnetic base is what will attach to your camera stand which will attach to a piece of steel on your ceiling, and if you use the materials that I used, it will be super easy.
You're going to need:
- 81 mm magnet with a metal backing
- NIBCO 3/4" 1-Piece (Solid) Socket PVC Flange (20mm PVC Flange)
- 5/16" x 2" (8mm x 50mm) carriage bolt
- 5/16" (8mm) washer
- 5/16" (8mm) lock nut (or lock washer and nut)
- (6) #6 1/2" (4mm) rounded head sheet metal screws
I'm using a Socket PVC Flange here, but you could get away with a square with a slightly larger 3/4" (20mm) hole drilled into it. Run the carriage bolt through both the flange and the magnet and add a washer. I used a lock washer and nut because that's what I had on hand, you can use just a locking nut.
Once this is put together, move on to the next step.
Step 8: A Little Heat and a Few Screws...
I heated up the copper because I was just a little smaller in diameter than the flange. This, I think, is good. By heating up the copper I was able to get a more perfect fit which makes the over all piece much more solid. You could use a propane torch, like I am here, a fire pit or the heating coils on your stove. There's not much more to say about that.
Afterwards I predrilled 6 holes big enough for #6 (4mm) screws to fit in I then put my screws in.
Step 9: Finished!
One thing I'm not going to add (for obvious reasons) is how to attach metal to your ceiling or cabinets for this to hang on. In a shop, it should be pretty easy to come up with a solution.
I've used many materials and tried my hardest to make this as economical as I can, even trying to substitute copper with conduit, which was a failure due to how thick the walls in the conduit is.
If you liked this, please give me some love! Either way, give me a comment and let me know how I can make this better.
Thank you!
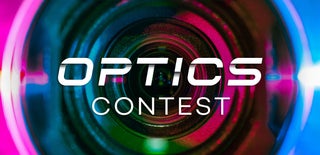
Participated in the
Optics Contest