Introduction: Heating Plate for SMD Soldering – Simple, Small and Low Cost
After my last use of my modified 1.5kW hot plate I decided there had to be a better way. I had already retrofitted a decent power controller to the hot plate but it was still slow to heat and I had to dig out a thermometer to check temperature. The large 200mm (8") diameter seemed crazy for soldering boards that are only 30x10mm.
A search showed a nice device from Weller – but at just under $1000 I could not justify the expense. There is a good instructable using a large (100mm square) aluminium block with a cartridge heater and control system. Looks good but is quite bulky and a fair bit of work to make the controller. I looked at cartridge heaters (but none were small diameter), and then wondered about temperature measurement – and the solution appeared. A soldering iron heater is both small diameter and has a thermocouple. And (the good bit) – I can plug it into my existing soldering iron controller.
A check back to the Weller device showed that it worked in the same way – i.e. plugged into their soldering iron controller. The Weller device has a plate area of 50 x 80 mm, is 80W and a max temperature of 200C. It would be good to have a bit higher temperature range and use a more standard 50W iron controller. A quick back of the envelope sum, assuming heat loss is proportional to area and temperature suggested that a 40mm (1.5”) diameter plate should get over 300C with 50W.
If you don’t already have a 50W (or more) solder station I will say “why not?”. The irons get up to usable temperature much faster, the bits last longer, and soldering is much more consistent as the temperature is controlled within a degree or so of the ideal for the job. They are available on ebay at very low cost and I was staggered at the low cost of the irons and heating elements. This SMD heating plate costs a couple of percent of the Weller plate and has a higher temperature range.
In broad terms the heating plate is a piece of aluminium around 40mm diameter (or equivalent rectangular area), thick enough to take a soldering iron heater element, and set into some thermally insulating material.
My soldering iron controller is one I designed some years ago, and uses the Antex TC50 iron. I was also aware that the cheaper Zytronic irons would work – also 24V and have similar thermocouple. I did not find these but found irons for a 936 controller at around $3 – and then just the element for half that (on ebay).
Step 1: Parts, Some Learning, and Options
In broad terms for this project you will need:
- 24v 50W soldering iron element
- Aluminium block with a hole for the iron element
- Enclosure
- Insulation
- Silicone pad for top surface
- 24v soldering iron controller (not shown)
Some Learning
I ended up buying a few more bits than planned – and did some learning in the process that I thought I should list to save you the trouble.
- The cheap (HAKKO clone) irons and controllers come in two types. One uses a thermistor as the temperature sensor and the other uses a K type thermocouple. These are not interchangeable and might account for some of the ‘poor’ experience that appears in the forums.
- The thermistor heating element is sold with the code A1321 and the thermocouple element with code A1322. These are sometimes used to differentiate the irons.
- The thermistor type controllers have a calibrate adjustment as thermistors are not close tolerance devices and each iron will be slightly different.
- Not all the irons/elements are 50W. I bought a ‘50W’ A1322 (clone) element and the heater resistance was 15 ohms – so max around 38W – but will be less as the resistance increases with temperature.
- A $3 iron with the 5 holes plug was the thermocouple type.
- The $3 iron (thermocouple type) appeared to be giving a high temperature reading. I first thought they might have been using J type TC rather than K. Later realised it was because the bit was not copper (it was very magnetic – steel?). I measured over 100C drop to the tip. The bit to element fit was rubbish – 4.3mm ID bit and 3.9mm OD element – so 0.2mm air gap (if even). This will not have helped! So get some copper bits if you want to use the iron.
Options
My suggestion would be:
If you already have a controller – get a spare 50W iron and take the element out for the heating plate.
If you don’t have a controller – get a 50W soldering station (and a spare iron because you will want to use this for conventional soldering as well).
A last option, if you have a thermocouple type controller is to get a K type thermocouple probe and a 24V 50W cartridge heater. The latter are not expensive as they are used in 3D printers. You will have to work out the wiring.
Step 2: Initial Test
I wanted to check my sums were OK before spending time on a nice finished product. So I got some scrap 3mm (actually 1/8”) aluminium and cut a couple of pieces, the larger was 38 x 30mm. This was 90% the area of my target 40mm dia – so close enough. I held these together in a vice and drilled a hole 3.9mm diameter. If you don’t have a 3.9mm bit then use a 4mm and sandwich 0.1mm of paper between the plates. Make sure you bit is in good condition as you don’t want to drill oversize. See photo for the test setup. The base was a ceramic fibre insulation soldering pad (ebay UK around $4).
I held the plates down using a screwdriver and measured the plate temperature driving the element at 24V. The current only got up to 1.7A, or around 40W but the plate got over 275C. So a little short of my target but still high enough for soldering.
Step 3: Final Design
Note that the design I used was only possible because I had access to good metalwork facilities. However simpler and just as effective systems could be made based on the initial test system. Use a couple of pieces of 3mm plate and add some 2mm screws to hold them together and mount on some insulation in a box.
The box was size 50x80x20mm with interlocking top and bottom halves and screwed end plates. I had a piece of aluminium turned to 38mm dia and 12mm high. I drilled a hole 4mm from the bottom with diameter 3.8mm (and 3.9mm for the first 10mm). This gave a good fit for the element (removed from a $3 iron). However the element was too long for the box (or the box is too small – depending on your perspective) so I cut off 5mm from the end where the wires come out using a diamond cut-off wheel.
I then had a 40mm hole milled the box upper half. This could have been done by hand but cnc is easier and better finish. I then cut the 12mm insulation to fit the box and cut a pocket to fit the aluminium piece. I used a knife to make most of the pocket and a Permagrit 18mm round file to make a snug fit with the aluminium piece 3mm higher than the box. The latter was so I could cut a piece of 3mm silicon (ebay $5) to fit the top.
Wiring was tight as I wanted to keep as much of the inside of the box filled with insulation. I had noted the lead colours before removing the element from the iron.
If I were doing this again I would:
- Look for a larger box with similar height so I would not have to shorten the element
- Make the aluminium block smaller to speed up the heating time and increase the maximum temperature.
Overall I am very pleased with this addition to my soldering armoury. It is a great help soldering no-lead SMD packages. I set the plate to 150C so this covers the first part of the reflow temperature profile and then use a hot air gun at 250C (with the PCB on the heating plate) to complete the soldering. When I am happy the solder has flowed I remove the hot air gun and move the PCB onto the silicon to cool. See video above.
The box does heat up a bit despite the internal insulation. Adding silicone to the top surface does not help as it stops the box losing heat! So I rest the unit on the silicon sheet I had left over.
Also pleased the parts gave me change from $20.
Mike
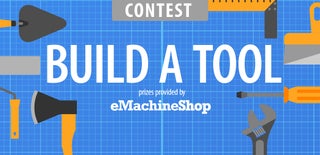
Participated in the
Build a Tool Contest 2017