Introduction: Helicopter - Battery/Solar - Wire Bending
A helicopter sculpture made of copper wire with motor driven rotor.
This helicopter could be in your room somewhere on a shelf and the rotor makes its revolutions at low speed … in any case an eye-catcher!
Inspired by my work on the "Wire Puzzle" and "Wire Puzzle II", I was looking for a bigger challenge in terms of wire crafting. On the Internet I found a solar-powered wire helicopter from the company Opitec. The design seemed to me to be in need of some improvement and so I started to work to design this project to my own conception.
For this project you should have a little experience with soldering and it requires some patience, because not always everything succeeds immediately sufficiently well.
As this wire strength is relatively easy to work with, it doesn't matter if you need a second or third try to get a satisfactory result for one or another part.
Supplies
Motor:
- DC 6/12V 30RPM Micro Motor
- Motor dimensions: Ø 12mm x 26mm (height)
- Shaft dimensions: Ø 3mm x 10mm (length)
Such a motor - connected to a 9V battery - provides a pleasant number of revolutions of the rotor.
Battery:
- 9V bloc
- 9V battery clip
- Of course, other battery powers (1.5V, 3V or 6V) are also possible, which would then have to be connected via the socket. Accordingly, the rotor revolutions are lower. I personally like it very much with a 1.5 V AA battery. These slow rotations are sufficient … and it does not make so much noise!
Solar panel (optional):
- Rated Maximum Power: 2.2 W
- Voltage: 6V
- Dimensions: 145 x 115 mm
Plug:
- Ø 5.5 x 2.1 mm
Jack:
- 3 pole, Ø 5.5 x 2.1mm
Soldering
- switching wire Ø 0,22 mm
- soldering iron
- solder
- flux
- small metal file
- a „third hand“ and clamps to fix the wires
Step 1: Preparing Wire
For this first step you need:
- cable with copper wire 1.5 mm², approx. Ø 1,4 mm (in total almost 4 m)
- 4 pieces of cable of approx. 24 cm length (parts F and G)
- cutter
Some time ago I bought single-core wire from the DIY store because it saves me the work of removing a single wire from a multi-core power cable. From my previous wire projects I still had plenty of cable left over.
On the photo 4m of cable are shown ... approximately the length needed to build the helicopter!
We start with 4 pieces of copper wire each about 24 cm long. Then carefully cut the sheathing piece by piece with a cutter knife. This is unfortunately a bit fiddly.
Try not to damage the wire core when stripping and bend it as little as possible. Small bends are difficult to remove and damage to the wire surface will spoil its appearance … this also valid for the all further cuts.
Step 2: Wire Bending
For the next step you need:
- heli_templates.pdf
- cable with copper wire 1.5mm², approx. Ø 1,4 mm
- wire cutter, pliers
Note:
- The essential, large parts are bent and dimensionedwith the help of the templates. Other parts such as most of the cross braces (D, J, I, K, L, M, N, S,T), must - after the large parts have been soldered - be cut according to the real dimensions.
- The pdf printout "heli_template.pdf" differs in some details from the view on the photos. The changes had to be made during the work on this project when many of the parts were already soldered. The following parts were changed or added:
- A (2x) was lengthened to prevent tipping backwards.
- S and T as motor mount
- P (rear wing)
Make a printout of "heli_templates.pdf".
To be sure that the printout of "heli_templates.pdf" has been made in the correct size, a check should be done exemplarily by measuring the template of the rotor (length 23,5cm)! Minimal differences (+- 5mm) do not matter! The worst thing that can happen is that the helicopter will become slightly smaller or larger overall, as it would refer to all parts in the same way.
Basically, I must mention at this point that it is not possible to maintain 100% dimensional accuracy in this project.
Start with bending the parts F and G, each 2x. Put the wire on the template and bend it with your fingers according to the template. The protruding wire is cut. Make sure that two nearly identical parts are formed.
Do the same with parts A (2x), B (2x), C (2x), E (2x), H (1x). Do not bend the curves with pliers, but carefully with your fingers.
Only for the parts that require right angle bends (Q and P), it is appropriate to do this carefully with pliers.
Step 3: Soldering Main Parts
For the next steps you need:
- copper wire 1.5 mm², approx. Ø 1.4 mm
- pliers
- soldering iron
- solder
- clamps
- soldering grease
The soldering as a whole was not easy. Copper has a very high thermal conductivity. Holding one end of the wire with your fingers is hardly possible because it gets too hot very quickly. So you have to fix the wires exactly with the help of one or more clamps.That is pretty fiddly and it does not always succeed at first go.
As I explained above, after completion I had to realize that the helicopter tipped backwards due to the skids being too short. Therefore I had to make a lengthening. Starting from bent side, the solder joints remain in the same place!
To improve the flow properties of the solder, it is useful to apply soldering grease to the solder joints. It is important that the wire parts are as close together as possible.
Steps:
- solder the 2 parts B to the 2 parts A
- solder the 2 parts E to the 2 parts B
- solder the 2 parts C to the 2 parts E and the 2 parts B
- solder the 2 parts F to the parts B and E
- solder the 2 parts F to part E
- solder the 2 parts G to part E
- solder the 2 parts F to part E
- solder part H to the ends of parts G and F
- solder part P to the end the 2 parts F
- solder part R to H
Maybe it is easier to orientate yourself by the pictures after all ;-)
If a solder joint has become too thick, you can carefully trim it with a small metal file.
Step 4: Soldering Cross Braces
As I mentioned above, the dimensions of the cross braces must be taken based on the created conditions.
To be able to fix the wire for a cross brace with a clamp, it is advantageous to cut the wire longer than necessary. After soldering, the protruding wire is cut off and reworked with a file if necessary.
Step 5: Motor Mount
For this step you need:
- approx. 25 cm copper wire (2x), 1.5 mm², approx. Ø 1.4 mm
- DC 6/12V 30RPM Micro Motor
- pliers (wire cutter)
The installation of the motor had caused me some problems. As I did not want to solder it to the bars, I had to find another solution. So I came to the double winding of the motor with the copper wire and the fastening from two sides. It could then be pulled out to the top, which does not matter for our type of battery operation.
But first a base must be created on which the battery can be placed. Parallel to part E, a cross brace is soldered (at a distance of approx. 6mm) as you can see in the first 3 fotos.
To avoid a short circuit, you should isolate parts N and E in the middle under the motor as a precaution. In my case it was not necessary.
The shown templates S and T are only symbolic. The windings must be created directly at the motor.
Place the motor flat in the middle of the wire and bend the wire (quite tight) 2x around the motor. Then bend it together and spread it to the width of the helicopter tail (as it is shown in the pictures).
Step 6: Rotor Installation
Now you need:
- copper wire, 1.5 mm², approx. Ø 1.4 mm, about 15-20 cm
- pliers
- soldering iron
- solder
- flux
- small metal file
- a „third hand“ and/or clamps to fix the wires
The rotation of the two-bladed rotor of the helicopter makes the charm of this project after completion.
Finding a way to connect the rotor to the motor's drive shaft was not easy. I could have printed a connecting piece on my 3D-printer, of course. But I wanted to use wire as the basic material for it, if possible.
Finally, I came up with the idea of winding the drive axle tightly with wire. Due to the fact that the drive axle has a flattened side and the wire adapts to it, spinning of the rotor will not be possible.
The shown template O is only symbolic. The winding must be created directly at the axle of the motor.
Take the motor and the wire and wrap the wire very tightly around the drive axle as shown in the pictures, about 7 turns. Then cut off what is too much on the top side. Cut off the wire at the bottom so that about 20mm remains. We need these 20mm to integrate this adapter into the rotor. Place the connecting piece between the wires of the rotor as shown in the pictures. Because of the optics, try to make the soldering even on both sides.
Step 7: Base
For this step you need:
- 3D Printer
- switch: Ø 6mm, 2 pole
- power jack, 3 pole, Ø 5.5 x 2.1mm
- 9V bloc
- 9V battery clip
- wrench 7 and 8 mm
This base will hold the battery, wiring, on/off switch, and a power jack to connect a solar cell or other battery size.
I first designed the base with Tinkercad and then printed it with my 3D printer. A base can of course also be made from thin plywood.
I didn't include any holes for this base to mount the helicopter (different from what you see in the pictures. Note: for my base, I was of course able to include the holes and include them in the printing). For others it makes no sense, because every helicopter will turn out differently.
Before you fix the helicopter and start wiring, you need to install the on/off switch and the power jack.
Step 8: Attach Helicopter
To attach the helicopter to the base you need:
- the copper wire in use or floral wire, 4x ca. 5cm
- drilling machine
- drill, Ø 2mm, (depends on the thickness of the wire you will use to attach the helicopter. If you use e.g. thin floral wire, a Ø 1 mm drill is sufficient)
- pliers
Place the helicopter on the base so that the skids are centered. Make markings for the drill holes on the left and right side of part B, as well as in front of and behind the skids. Now drill the holes with a Ø 1 or Ø 2mm drill bit.
After the holes are made, you can now insert the prepared wires into the holes and twist them from the back side.
Step 9: Wirering
For this step you need:
- switching wire, Ø 0,22 mm, different colors
- soldering iron
- solder
- flux
Take off the rotor during soldering so that it is not bent.
First solder a red (+) and a black wire (-), each about 25-30 cm long, to the corresponding poles of the motor. Now put the motor into the mount and insert the black and red wires through the hole in the center of the base.
As the description of a wiring is very complex, I have attached some pictures, which in my opinion say more than words.
The wiring is configured so that when a battery or solar cell is connected to the AC/DC socket, the internal power supply is switched off.
I hope you'll succeed in building this helicopter and have fun making it!
Update 2022-11-25
I was pleased to see that this "wire helicopter" met with some interest. Thanks for all the comments and suggestions for changes! Two of the suggestions came regarding the power cables, "that pair of dangling wires". Routing these in some way so that they are as invisible as possible was not something I considered at all while assembling the helicopter!
I like the suggestion of TihiTihi and Pascal78 (see comments) and would like to propose it here as an alternative. I hope that I have got it right!
From the positive pole of the motor leads a copper wire (the copper wire from which the helicopter is built, about 9 cm) - with a slight offset at the motor - vertical into the base. This is connected there with the existing red wire, which leads to the on/off switch. Make sure that it does not touch part B!
The negative pole of the motor is connected to the nearest copper wire (part E or N) by the shortest way. Then, in the base, solder the black wire coming from the socket to the fixing wire, which, of course, must be conductive.
Step 10: Material Variations
You may want to use a different wire material or a different base color ...here are some 3D rendered suggestions!
Step 11: Video
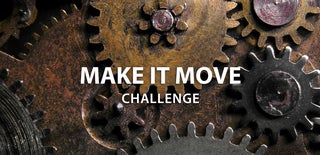
First Prize in the
Make it Move Challenge