Introduction: High Quality PowerBank From Dead Laptop Batteries
The cells in ‘dead’ laptop batteries still have life left in them for lower current applications. For example 18650 cells from ‘dead’ Dell battery packs are good for powering LED torches.
I decided I needed a powerbank for a 6 hour cycle challenge. This is just a tiny bit longer than my smartphone will power the screen and GPS for my maps and tracking app. I looked on ebay and was concerned that the quoted ratings for the powerbanks were obviously false (and crazy). Some of the reviews were quite negative and claimed the use of ‘fake’ batteries and so on. None of the feedback said what I wanted to know – i.e. how much it would charge a battery of a given capacity. I then realised that I happened to have all the parts required to make a very good unit in my scrap box! The cells came from a Dell Latitude D400 laptop that are flat rather than round – so better packing. I had bought a charger and booster electronics module for another project that ended up with a different system. I then looked around for a suitable enclosure and found an old 2.5” laptop drive USB enclosure. To my delight it looked like 4 cells plus the electronics would fit snugly with only a mm to spare. Perfect, and suddenly a ‘must do’ project.
As well as showing this main project I will give pointers to how other configurations might be put together – including the more common 18650 cells. Electronics modules are available on ebay for £2 so if you have the other parts you can make a great powerbank for much less than buying one – and know it will do the job required.
Specification of the powerbank built here:
- Cell capacity: 4x 1400mahr (i.e. 5600mahr)
- Charge current: 0.6A at 5v
- Discharge current: 1A at 5v
- Size: 127 x 75 x 12 mm
- Weight: 211g
The picture above shows the parts for the main project:
- Ex laptop lithium cells
- Electronics module
- Enclosure
If you want a powerbank with enough capacity to fully charge your mobile then the powerbank needs cells with roughly double the mobile battery capacity. The reason for the higher capacity is that the powerbank cell voltage (around 3.7v) has to be boosted to 5v to supply the charger. At say 80% efficiency we will end up with 0.8 * 3.7 / 5 or about 60% of the mahr. There is also a small loss in the charging process.
Before going further - a word of warning. Lithium batteries hold a good deal of energy and if mishandled or overcharged or short circuited they will overheat and can explode and catch fire. There is always a point in assembly where one is soldering a wire to a live battery – so check, double check and check again.
Step 1: Background
I do not view the electronics module to be a DIY option both due to their complexity and the availability of low cost pre-built modules. The electronics module needs to have several key circuits. One circuit will manage the charging – often using a TP4056 chip. A switched mode circuit will boost the cell voltage to 5v when it auto-detects a USB device being connected. The last, and arguable most important circuit, is the battery protection unit that will isolate the battery if the voltage gets too high (overcharge protection) or goes too low (overdischarge protection). This often uses a DW01 6 pin chip combined with a 8205A dual MOSFET.
For powerbank modules search on ebay for ‘powerbank module’. There are also many kits that have the electronics and enclosure and just need batteries installing. These mostly use the 18650 cells. Search on ‘powerbank DIY’. Photos above show some of the kits on ebay (Note: none have been tested by the author).
Please take great care when opening up the ‘dead’ laptop battery to access the cells. In particular make sure any metal objects used to not come in contact with the cells. One must avoid a short circuit at all costs. YouTube has some examples of laptop batteries being opened.
Step 2: Initial Test Powerbank
My first unit just used two cells. I had to wire these in parallel. Before doing so one must check they are at the same voltage. If one is charged and the other discharged (or dead) then when connected a high current will flow with potentially ‘unintended consequences’. If they are more than say 0.05v different then balance them by connecting a resistor around 1ohms to the pair of positive or negative connectors and leave for as long as required to get into balance.
The positive terminals were already connected with thin metal strip. I used metal strip conductors from another battery pack to connect the negative terminals. See photo above. After soldering the strip it was folded over to give a neat assembly.
I then connected the electronics module. I soldered red and black wires first the module (+ve and -ve respectively). Then I checked the cells polarity. This can be confusing as in some cases the metal can is positive rather than negative as with dry cells. After soldering one wire to the cells then check and double check there is the appropriate voltage on the other terminal before soldering the other wire to it.
We now have a viable powerbank. It doesn’t get much easier than this! I plugged in a micro USB lead and a red LED came on showing charging. This changed to green at the end of the charge with a cell voltage of just under 4.2v – which is fine. I then connected my mobile charging lead to the USB ‘A’ socket and the powerbank raised my mobiles charge level from 50% to 86% - i.e. just over a third of the capacity. The two cells had a combined nominal capacity of 2800mahr – that is similar to my mobile – so not quite the 50% that might have been achieved with new cells – but good enough. The low voltage protection came in at around 2.6V. I would not want lower than this. After the cutout the cell voltage rose quickly to 3.7v suggesting that there was still some capacity left. The 4 cell unit would do a better job of accessing the capacity as the current per cell will be half and hence the impact of the internal resistance reduced.
This initial unit would have satisfied my needs and I promptly ordered another electronics module so I could make up a 2 cell bank. For enclosure I will fold up some stiff card and cover the lot with some large size heat shrink tube. Note the inclusion of a piece of insulating material between the cells and the electronics module. The insulation on cells is quite thin and hence no harm to add an additional layer for safety. I used some thin FR4 PCB with the copper removed. Note that the standard 1.6mm FR4 PCB can the split down thinner by carefully inserting a chisel into one corner.
Step 3: 4 Cell Powerbank
This, professional looking, unit required a little more work.
First the pack of 4 cells was made up. Two pairs were wired in parallel, after balancing as above. From a space consideration it looked preferable to connect the positive sides together in the middle of the pack with the negative terminals at the opposite ends. One of the pairs of cells had a thermal overload fuse in line. There was (just) room so it seemed good sense to retain this.
With the positive terminal of the two pairs connected the pairs were balanced before connecting the two negative terminals together. Note the additional insulation where the black wire goes around the end of the cells. This will give extra protection against unintended abuse.
For the wiring I used 20awg silicone wire. This has a higher temperature rating and hence is a bit safer than standard PVC insulated wire.
I then found that the USB socket on the module was too high to fit in the case end cover. The original 2.5” drive controller had a low profile connector and hence I swapped these over – with a little filing of the main locating pins. Both PCBs were double sided with through hole plating. Hence the availability of a desoldering iron (heated sucker) makes this considerably easier (these are not too costly and a worthwhile investment). I also checked that there was adequate space for the sockets sprung arms that engage with the USB plug to move and that the board at this point was ground and hence a short would not occur.
I thought itwould be good to have a single two colour LED for the charging red/green. Checking the module the LEDs had their anodes connected so I could use a common anode dual LED. These are not so easy to find but as luck would have it there was one on the 2.5” drive board. It was nice to see that Murphy’s Law was not applying to this project. I then removed the onboard SMD dual LED so the new LED would be a bit brighter. I added a blue LED for the discharge indication. This was bright enough in parallel with the onboard LED. Some careful drilling delivered holes for the two LEDs and for the micro USB socket. The board was positioned to use the existing ‘USB A’ hole.
I then added some insulating material (from scrap FR4 PCB with the copper removed) to both separate the electronic module from the cells and take up the 1mm space and hence hold the electronics module in place.
With everything fitting OK I soldered a red wire to the module, then connected the black lead from the cell pack to the module, and lastly after appropriate checking soldered the red wire to the cells thermal protection fuse.
All was carefully assembled into the enclosure and job done.
Step 4: Testing
Note that even if the batteries are fully charged the unit will not deliver power until there has been some charge current. The act of charging resets the discharge part of the battery protection circuit.
The first step was to charge the pack. This can take a while with the 0.6A set on the module. The LED changed from red to green to show the charge complete.
I then connected my mobile – that had a starting charge of 50%. The powerbank took this up to 100% over about an hour.
Then ran my mobile down to 25% and reconnected the powerbank (without any charging). The powerbank shut off when it had brought the mobile battery up to 77%. So overall the powerbank has capacity to fully charge my mobile's 2600mah battery. Looks like a win to me.
Mike
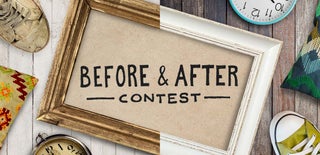
Participated in the
Before and After Contest 2017
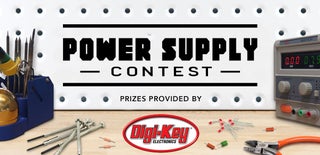
Participated in the
Power Supply Contest