Introduction: (Holy Moly)
Materials
bristol board
carpenter's glue (waterproof)
good two part 5 minute epoxy
sandpaper (60,80,100,150 and 220 grits)
premium exterior varnish
two sided tape
rubbing alcohol
1 1/4" re-enforced dremel cutting disks
3"X 20"X1/8" steel
1/8" brazing rod
3"X7"X1/8" hard wood (four pieces)
Tools
1X30" belt sander
buffing compounds
buffing wheels (for drill press)
compasses
drill buffing pads
drill press
drum sanding kit
french curves
painters tape
palm sander
pencil
plain and/or squared paper
punch
quick clamps
rotary tool
scroll saw
side cutters
spring clamps
utility knife
various files
various high-speed drills
Safety Equipment
ear plugs
good face mask
leather gloves
safety glasses
Step 1:
The start of making a knife is an idea. Sketch your idea on paper and perfect it. Once satisfied ( which can take days) finalize the template on bristol board, and cut it out with a utility knife. Hold the template to see if it feels OK, if not; back to the drawing board for adjustments.
Step 2:
Step 3:
For the serrations on the top swag edge of the knife, use a punch to mark the center points on the pencil line, and drill the holes before starting to cut out the knife.
Step 4:
Start cutting the steel with your rotary tool and the re-enforced cutting disks (the cheap thin ones do not last very long, but you still will go through a few of the re-enforced ones). Start at a slow speed, until you get a groove cut and the you can increase the speed (cut as close as you can to your lines, it will save you time later). Do not press hard, but let the weight of your tool give you the pressure.
Step 5:
Finally the knife is cut out; now to use the 1X30" belt sander, drum sanding kit, and files to clean up the outline of the knife. Mark where you want your pins in the handle, use your punch and drill 1/8" holes for your pins; also drill divots in the tang of your handle (this helps the epoxy to stick to the scales of the handles). I wanted allot of decorative milling on my blade so I used my drill press and various size high speed bits for the holes.
Let's clean it up. Using the 1X30 belt sander put a 22 degree edge on the knife and the one side of the swage edge. Sand with the rust, patina, and scratches out of the steel using sandpaper up to 150 grit (usually I sand down to at least 800 grit, but I wanted a rustic look on this knife). Only sand the tang with the 80 grit sandpaper, as you do not want it polished and the epoxy will not adhere.
Step 6:
Next polish the steel using first the black polishing compound and a sisal buffing wheel on the drill press ( use medium to hard pressure going against the rotation of the wheel). Second use the white polishing compound and a spiral sewn buffing wheel (use medium to hard pressure going against the rotation of the wheel). Finally the blue polishing compound and a loose buffing wheel (use medium to light pressure going with the rotation of the wheel).
If this were not a decorative knife, and one was going to use it; the knife would be heat treated at this point and then re-polished.
Step 7:
The handle is the next stage. Cut the three pieces of the brazing rod about 3/4" long, rounding off the edges, and flute the cut pins. Cut two pieces of the 1/8" dark oak, and two pieces of the 1/8" white birch, 2 3/4"X7" (you can use only two pieces of any hard wood about 1/4" thick rather than go this method). Sand each piece flat on both sides, using 80 grit sandpaper. Laminate a piece of each of the oak and birch using a good waterproof carpenters glue and clamps.
Once dry, using two sided tape; tape the birch sides of your scales together. place the tang of the knife on the stack of boards and outline the tang with a pencil. Cut the shape of the handle, using a scroll saw, leaving an extra 1/8" outside of the lines, for finial shaping and sanding later.
Step 8:
Put a scrap backer board on your drill press, then your stack of scales. Use the tang of the knife to locate the first position for the first pin and drill through the hole in the tang using a 1/8" bit through the stack of scales. Push one of your pins though the tang and into the first hole in your scales (to keep it in position). Drill your second hole through the tang and through the scales, push in your second pin, and finally drill the third hole.
Step 9:
Separate the two sets of knife scales, clean and sand off any glue left by the tape. and clean the knife tang using rubbing alcohol.
At this point your should have the front part of the scales shaped and sanded as once they are glued in place you will not be able to finish this area. Also cover the blade of the knife with painters tape up to where the scales are going to start. This makes cleaning up any glue easier to clean-up, and stops you from cutting yourself with the knife.
Mix up enough two part epoxy to cover one side of the knife tang, and coat one side of the tang, place the knife scale in place, coat your pins lightly with epoxy and push them in until they protrude though the scale about a 1/16" or so. Clamp the scale to the tang and set it aside to dry. Cover the second side of the tang with epoxy, and the pins, re-clamp and allow to dry.
Step 10:
Now the shape the handle. Using the 1X30" belt sander, sand the pins level to the knife scales (go slow as you can heat up the brass pins enough to burn the wood). Some people prefer to peen the pins, but I find with the pins fluted and epoxy they have yet to fail.
Using the sanding drums, sand various grits of sandpaper shape the handle until it feels comfortable in your hand. Sand the handle to a finish of at least 220 grit (I usually go as far as 400 grit).
Put at least four coats of a good exterior varnish on the handle (lightly sanding between each coat), remove the tape off the blade, finish sharpen the knife, polish and you are finished.
Step 11:
Holy Moly is an cousin to a previously made Zombie killer, Confetti Machete. This knife has a total length of 19 1/4" with a 13 10/16" blade, and tips the scales at 2.2 lbs.
The work would be a lot faster if I had a metal cutting band saw, or a dream if I had a Zing 16 Laser.
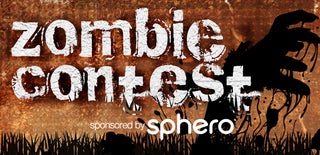
Participated in the
Zombie Contest
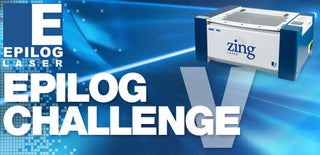
Participated in the
Epilog Challenge V