Introduction: How to Create a Feeding Tube Cover - a Step-by-Step Design Guide
My cousin Rebekah was born with microcephaly, a birth defect where a baby’s head is smaller than expected because their brain did not fully develop in the womb or stopped developing after birth. Some children with microcephaly lead normal lives, but others experience delayed cognitive development and need daily care. At 12 years old, Rebekah can't speak or feed herself, but her smile and her laugh still light up the room wherever she goes.
Because she has trouble swallowing, Rebekah has a feeding tube, and with her child-like curiosity, she likes to grab and pull things that capture her attention (like her feeding tube). A few Christmases ago, my aunt asked if I could make something that would keep Rebekah from disconnecting her feeding tube while she's eating, and now I'm finally able to do that!
My goal for this instructable is not only to show how I made something for Rebekah but also to teach others how to solve similar problems of their own. Maybe they'll create instructables too, and the world will be a better place!
Here's the process we'll walk through together:
- Define the Problem - A disconnected feeding tube means a big mess and a hungry belly!
- Collect Information - What's out there? Have others tried to solve this problem?
- Brainstorm - How could I solve this problem?
- Prototype - Let's try our best ideas
- Gather Feedback - What do other people think of our best ideas?
- Improve the Design - Learn from feedback and make improvements
- Share (I added this step) - Make what you've learned available to others!
If you'd like to make one of the feeding tube covers I designed, here's what you'll need:
- A 3D printer or access to a 3D printer
- Garden-variety PLA printing filament (I used Inland brand from Microcenter)
- An oven that can hold a temperature of about 200*F/95*C
- A cast-iron skillet or pizza stone
- A piece of 1+1/8" dowel that is 2" long
- My file from Thingiverse
Step 1: Define the Problem - Vulnerable Feeding Tube Connection
When Rebekah disconnects her feeding tube, two things happen - she doesn't get the food she needs, and her food makes a big mess in her wheelchair. As I was creating a solution, I wanted to be sure to address those two things.
However, let's go a little bit further and think about Rebekah's situation in general. My aunt and uncle have a lot on their minds already - medication schedules, equipment maintenance, specialized transportation needs, and much more! If I'm going to add something else into their lives, it needs to be beneficial, simple, and very low maintenance.
Here's my list of qualities I wanted my solution for Rebekah to have:
- Keeps her feeding tube connection safe and secure
- Easy to wash and sanitize
- Fast and easy to replace if needed
- Tough enough to stand up to daily use for a while (my goal is 6 months)
- Assembles and disassembles quickly and easily
- Allows for one-handed operation with hands of any size
- Easy to open and close
- Self-explanatory so that anyone can use it
- Adaptable to a wide range of needs
Step 2: Collect Information - What's Out There?
Once I had an idea of what a good solution for Rebekah would look like, I started researching existing solutions for her problem. Here are two things I found:
- The CoriSafe System (http://www.corisafe.com/) - CoriSafe was designed by Mark Belanger and Alexander Slocum, both staff at MIT. Mark's daughter Corissa has a feeding tube, and he designed the Corisafe to keep the connection safe and clean. A CoriSafe is $25 or $20 if you buy more than one.
- Sewn G-Tube Covers (on Etsy and Amazon) - These covers are made of fabric and snap together to cover the feeding tube connection.
Neither of these solutions worked for Rebekah. The CoriSafe isn't large enough to hold her feeding tube connection inside, and the fabric solutions don't do anything to hold the connection together. However, in looking for other solutions, I learned a few things:
- CoriSafe was designed to also keep the feeding tube connection clean, especially for kids with diapers.
- The fabric solutions are made to be comfortable. A feeding-tube leading to the stomach is generally short, and the connection is close to the wearer. That means anything that covers the connection could be irritating if it has scratchy surfaces or sharp edges.
With the new things I'd learned in mind, I started thinking of what I could do to make something new for Rebekah.
Step 3: Brainstorm - How Could I Solve the Problem?
I sat down with my wife to doodle for a few minutes, and you can see our lovely artwork above (don't mind my handwriting)! We considered two-part hinge designs, sliding designs, and snap-together designs. We also measured my wife's hands to get an idea for size
Ultimately, I decided to go with a design where the top and bottom halves of the cover were identical, the hinge would snap together, and the box would snap shut with a friction latch. This would make the cover easy to assemble, easy to clean, and easy to use.
In making the box I also designed it for 3D printing. There are no sharp overhangs, no support needed, and no difficult features. I wanted anyone with a 3D printer to be able to make my design.
Step 4: Prototype - Let's Try Our Best Ideas
I've been learning Fusion 360 lately (which is free for hobbyists and startups!), and I spent a few hours creating a design that I could send to my 3D printer. I've never designed a hinge before, and it took me several tries before I realized that my hinge needs to be aligned with the joint between the cover halves. After I figured that out, I printed my first prototype.
When I picked up the parts from my printer, I realized that I'd made a silly mistake. My hinges fit together, but there was nothing to keep them from coming apart! They were also not aligned properly, and when the two box halves were assembled, they had a funny offset.
I redesigned the hinge, and printed another version. That one turned out much better. The hinge worked, it snapped together nicely, and stayed closed.
Both versions took about 3 hours to print with a 0.5mm nozzle and 0.4mm layer height, and they weighed about 3.5 oz when assembled. I planned to print them with a smaller layer height for the final version, but for rapid prototyping, those settings worked fine.
Step 5: Gather Feedback - Letting Others Try It Out
When I showed my prototype to my friends, family, and coworkers, they gave me overwhelmingly positive feedback, and I was really encouraged that I was on the right track.
As we talked more about the details of the design, I started building a list of improvement ideas:
- What about rounding the corners to prevent scratches?
- Could it be lighter? We don't want the weight to pull on Rebekah's body.
- Could the hinges be put inside?
- What about creating a more secure latching mechanism to keep it closed?
- What about adding something like a loop to attach it to a wheelchair with a carabiner?
With those ideas in mind, I started working on an improved design.
Step 6: Improve the Design - Learn From Feedback and Make Improvements
First, I shrank the box as small as it could go, and I added a loop for a keyring (Check out the small black box in the pictures). That worked out really well until I tried to heat treat it to make it dishwasher safe (more on that process later). As you can see from the pictures, the halves of the box warped severely when they were heat treated, basically becoming unusable.
With that I went back to the drawing board. How could I create something that wouldn't warp? Well, I knew that parts generally shrink along the layer lines. That's why my parts shrank upward into a "U" shape, and that gave me an idea. What if I used a cylinder as my container instead of a box? That way, when the part shrinks along its layers, it will simply reduce the diameter of the circle slightly.
You can see the results in the pictures above. First I printed the larger black parts as a proof-of-concept. Then I printed the smaller white parts. Both of them use simple threads to hold the two halves together, and I had much better results when I heat treated this design.
Finally, I made a few minor modifications, and the rocket ship parts in the last pictures are what I sent to Rebekah for my aunt and uncle to try out.
Step 7: Share With Others
And with that, I present to you my final product! If you'd like to make one yourself for someone you love, simply print my file from Thingiverse using PLA! It's important to use PLA because only PLA will respond correctly to the heat treating process below.
Important! As others have rightly pointed out (here, and here, and here), 3D printed parts have thousands of tiny crevices that make a perfect harbor for small food particles and germs. Any 3D printed part (like a cookie cutter) that comes into contact with food MUST be sanitized to prevent the growth of bacteria. Because this feeding tube connection cover will likely touch food, I strongly advise that you follow the steps below to make your parts safe for the top rack of the dishwasher:
- Place something oven-safe like a cast-iron skillet or pizza stone into your oven and cover it with aluminum foil. That will help hold the heat and prevent large temperature fluctuations.
- Preheat your oven to 200*F or 95*C. You may have to experiment with the oven temperature a little to get good results. The right temperature will vary depending on what brand of PLA you use.
- After the oven reaches temperature, let it sit for half an hour to get a good, steady temperature inside.
- Insert a piece of 1+1/8" dowel that is 2" long into the "cone" of the rocket ship. Then screw the two pieces together. The dowel will help to keep the threads from warping as they're heat treated.
- Set the parts in the oven on the cast-iron skillet or pizza stone. (That's why we covered them with foil earlier).
- Set the timer on the oven for an hour, and shut the oven off when the timer runs out. Leave the parts in the oven!
- With the parts still inside, wait for your oven to cool to room temperature. This allows the parts to cool slowly inside the oven in a process called "annealing."
Congratulations! With that finished, your feeding tube connection cover is ready to use.
Be sure to take a good look at the parts after you run them through the dishwasher the first time. Check for deformation or remaining food particles (ick!). It was so important to me to make this cover dishwasher safe, and I'd love to hear suggestions on how to make the design even easier to clean and sanitize.
Step 8: Final Thoughts
I learned so much through this process! I really honed my CAD skills in Fusion 360. I learned how to 3D print working, snap-together hinges, and I learned how to make parts that can be heat treated.
I learned a lot about the design (and redesign!) process too. When I look back at what I wanted to accomplish, I think I did pretty well! It was really a challenge to make something dishwasher safe. There's still room to improve, though. It would be really cool to create something that can be used one-handed.
Maybe you've seen some opportunities for improvement as you've been reading. What I hope to do in writing this is to empower YOU to make those changes. The world needs more than just my brain and heart - it needs all of us working together for good!
If you've enjoyed my instructable, please vote for me in the Epilog Laser Contest! Winning the laser would give me a whole new tool I can use to create things like this feeding tube connection cover for people who need them.
Thank you so much for reading!
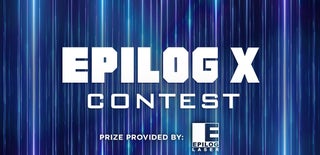
Participated in the
Epilog X Contest