Introduction: How to Make DIY Guitar Pedals - a Homemade Fuzz Effect
In the guitar-playing universe, effects or stomp boxes are used to shape the tone to make it more unique and appropriate. Effects like delay, reverb, or echo can add space to the sound, while effects like overdrive and distortion can make the sound heavier and more rough for genres like rock or metal.
These effects can be implemented through digital software within guitar amplifiers or via analog pedals, harkening back to the vintage era of sound manipulation. With their simple circuit board designs, these old-school pedals can even be crafted at home, making the process both intriguing and accessible.
A fuzz effect is an effect that intentionally distorts the sound signal, resulting in a gritty, noisy, and aggressive tone. It's like taking the normal sound of a guitar and adding a layer of controlled chaos to make it edgy and intense. Musicians, especially in rock and psychedelic genres, use fuzz effects to add a raw and wild quality to their music.
So, dust off your soldering iron, gather your components, and let's embark on this journey to create a fuzz pedal that's truly your own.
Let's get started!
Supplies
Stripboard
Resistors
Transistors
Capacitors
Wire
5mm red LED with it's socket
Potentiometers
Electrical tape
Solder and a soldering iron
3PDT Footswitch
Aluminium enclosure
Guitar jack female sockets
Plastic DC power socket
Metal paint
Varnish
Step 1: Finding an Effect to Make
For starters, you'll need a diagram of an effect to make. Here's a very good website to find circuits for all kinds of different effects, with varying difficulties. There are even tags on the right-hand side of the website, to filter according to type and brands. But here are a few other ones: diystrat.blogspot.com and guitarpedalbuilders.blogspot.com
If you're just getting started in soldering, it's better to first start with easy effects - with a classical one being a Fuzz effect. The fewer components the effect has, the lower the chances of messing something up by overheating or making an accidental solder bridge.
In the photo, you can see all of my failed effects over the years, for some, there is a lot of background noise that's messing up the signal, and for some, there's no signal at all.
Step 2: Gather Your Components.
As with ay electronics project, you'll need some electronics components.
Here are the main ones you'll encounter are, along with a simplified description:
- Resistors: adds resistance to the circuit, to reduce current flow and divide voltages.
- Capacitors: used to store energy for a brief period of time. Their values can be in the range of pico, nano, and micro-Farads.
- Transistors: basically a switch that can be triggered electronically.
- Diodes: a component that only let's current go though in one direction.
- IC's: a commonly needed circuit, shrunken down and placed inside a small chip.
- Potentiometers: manually variable resistors. Made out of a resistive element, and a sliding wiper, that allows the value of the resistance to be changed. The max value is given by the value of the potentiometer, and the type of resistive element used defines the behavior of the potentiometer. There are logarithmic, linear, and inverse logarithmic potentiometers out there, represented by the letters A, B, and C. The logarithmic type is sometimes used with audio equipment, as it conveys better the way the human ear perceives volume.
If you want to get started with effect-building, but don't want to commit to buying a bunch of components, you can also buy kits online, that ship with all the components needed for the circuit, as well as the enclosure and the other bells and whistles.
Step 3: Preparing the Board
Once you have the effect that you want to build, you can prepare the board to solder your components to, by cutting out a piece of stripboard. It's a very convenient type of board to use, as all the holes on one line are connected with a piece of copper that runs the whole length of the board.
If cuts are needed in the tracks, cut them out by drilling on the copper track, and removing the last bits with a sharp knife. When marking their locations, keep in mind that if the copper is on the backside of the board, the holes need to be marked in mirror.
Step 4: Soldering the Components
When it comes to soldering, it's a very straightforward process. Simply find the right component in your inventory, and add it to the board, soldering it from the back.
To make placing the components easier, it's better to start with smaller components, that are closer to the circuit first, and keep the bigger components for later.
Here's the order I usually follow:
- Wires to connect tracks
- Resistors
- Resistors
- IC's (if there are any)
- Capacitors
Step 5: An Option to Help With More Fragile Components
To minimize the risk of overheating sensible components like transistors or IC's you can use this kind of PCB sockets. Simply solder the socket in first, then plug in the component without having to make it come in contact with heat at all.
Step 6: Connecting the Effect to the Enclosure
To make the effect alter the guitar signal and be usable on stage, we'll have to do some additional wiring for power, the signal, and the power. Here's a universal schematic to hook up your effect.
Step 7: Choosing an Enclosure Size
To make the pedal look and feel like the real deal, you can use an aluminum enclosure. They come in different sizes, with the common ones being the 1590A, 1590B, 125B, and 1590BB. I choose to use the 1590A size, as it's the smallest one, and also the same size that a lot of cheaper Chinese that I already have. If your effect has more than one potentiometer, it will be a really tight fit, so, a bigger enclosure would be a lot more comfortable to use.
To ensure an authentic and professional aesthetic, utilizing an aluminum enclosure is a fantastic choice. These enclosures are available in various sizes, with the 1590A, 1590B, 125B, and 1590BB being among the most common options. If you're aiming for a compact design like the 1590A, you'll also be able to find a lot of Chinese pedals with the same enclosures to complement your pedal board.
However, it's worth noting that if your pedal involves multiple potentiometers, the compact nature of the 1590A can lead to a really snug fit, potentially making it impossible to fit everything in there. In such cases, opting for a slightly larger enclosure would offer for a much more stress-free build experience.
Step 8: Drilling
In the enclosure of your choice, mark out the holes for the footswitch, potentiometers, the LED, and the cable jacks. Then, drill them out. For larger holes, you can use a step drill bit.
Step 9: The Power Socket Polarity
For the power jack, most effect pedals use a center negative power cable (and the positive is outside). So, the cable socket should be isolated like these plastic ones, to avoid it coming in contact with the grounded enclosure. As I didn't have any of those on hand, I insulated my metal socket from the enclosure with tape, but it's a really sketchy solution.
Step 10: Painting
To give your pedal some character, you can use some metal paint.
First, sand the enclosure lightly. Then, apply a few coats of metal paint, with a light sanding in between.
To customize my pedal, I decided to scribble a few drawings and annotations using a white Posca marker. For a more professional result, people have used waterslide decals, to print out a design and transfer it to the pedal.
Finally, cover your design with a layer of varnish.
Step 11: Putting Everything Together
Now that everything is ready, comes the last step: mounting everything in the enclosure.
Start with the components that need to be mounted with nuts on the surface, then the circuit board and its connections.
Step 12: Done!
And we are done! You now have a functioning guitar effect in your pedal connection, that you made and customized yourself. Hopefully, you also learned something along the way about soldering in general.
Personally, I'm quite happy with the result. The only thing I wish I had done differently is the design of the pedal enclosure. In the end, it's arguably the most important part of the building process - even when turned off, a cool-looking pedal on a pedal board is going to bring you joy simply by looking at it. I was too focused on getting the paint job done in one evening. I should have taken my time to make sure the design was perfect before mounting all the components. Also, I haven't ever tried the waterslide decal method. I feel that being able to import perfect designs from the computer could really level up the appearance of my homemade pedals in the future.
As for the sound, the pedal works as it should, here's a sound demo of it :)
Thank you for reading my Instructables. Stay creative, and have a wonderful day! :D
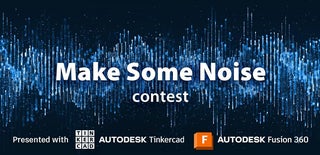
Runner Up in the
Make Some Noise Contest