Introduction: How to Make a Hydrophonic Testbench
This adjustable test bench for hydroponics agriculture investigates the behaviour of plants when certain variables are set. The 4 variables that can be tested are:
- Light intensity
- Substrate density
- Day cycle (time)
- The speed of flowing water
By investigating these variables an optimal growing environment can be found for the tested plants. With this test bench we test rocket but other plants could also work. For more (dutch) information on how this project came to be you can go to this blog: https://idcplanter07.wordpress.com/blog-feed/
This system is made by 3 students of Howest University College (Belgium).
If you are planning on making a system we would recommend you also look at the pictures from al the steps. There are usefull tips on these pictures. If you have questions send a message.
Supplies
the system is composed of 5 subassemblies. The components and parts for these assemblies are listed below.
- The housing
- Water
- Density control
- 3 mm thick ABS sheets 300 mm x 450 mm or similar
- 3D printed parts: Density 3D
- Lasercut files: Density Lasercut
- Substrate that you want to test. This can be al sorts of porous material
- Flow velocity
- 3D printed parts: Velocity
- Screws
- PVC tube
- Electrical system
- Led lamp
- Led power supply
- Plug and Play LED dimmer
- Timer
- Distributor plug
- 3D printed part to hang lamp inside case
- 4x M6 bolts
Tools needed
- Table saw
- Lasercutter with extraction.
- 3D printer
- Paint brush
- Basic Tools
Step 1: Housing
To create a controlled environment, the plants are raised in an environment closed off from sunlight. For this reason a housing is built. This housing is made of concrete plywood. Concrete plywood is watertight up to a certain level. As the plants grow in a humid environment this is important.
The first step in making the exterior is cutting the panels to size. For this you can use the enclosed technical drawings for the measurements. The panels are brought together according to the drawings. To connect the panels you use pieces of the wooden profile and the wood screws. You do this on sight and use your common sense to determine the location of these screws and profiles. Before you start with fixed screws you first drill a pilot hole that is slightly smaller than the screws used. We do this because it helps to prevent splits in the wood.
The second step to make the housing is the connection of the hinges. We want to make the housing accessible for the person who is doing the experiments. The location of the hinges can be found on the technical drawings.
The third step is the connection of magnets on the vertical panel. We do this to prevent that this panel opens on its own thanks to gravity. The slanted panel doesn't need these magnets because for this panel gravity is our friend.
Step 4: The plants need to breath. Therefor we add an air intake.The 3D print "air intake" can be used as a template for cutting
Step 5: To close the box from light and water spills we used a black silcone sealant on al the edges of the system.
In the last step we add 3 grips, so the system is a little bit easier to handle. These handles are connected to the top and slanted panel. These handles are 3D printed but a homemade or even store bought handle will also work.
As an optional step you can paint all the wooden profiles to match the concrete plywood. It wil also lengten the use of these profiles.
Disclaimer: If you like to use a different sheet material, go ahead and experiment, but for us, concrete plywood was the best option for its properties and it was easy to obtain at our local hardware store.
Step 2: Density Control
One of the things we want to test with our system is if the density of the growing ground affects plant growth. There for we made systems where we can change de density of a part of the plants. This allows us to compare different densities
The first thing we need for this subassembly are the 3d files called "density 3D". You will need to print them with an infill density of minimum 20%.
For the second step we will use the 3 mm thick ABS sheet and a lasercutter. The lasercut files are called "density laser"
The third step is to repeat the first and the second step because we need the system 3 times.
The assembly order is shown in the pictures above. The pictures are numbered with the steps. We chose coconut fibers. For substrate but you can experiment with other materials.
Step 3: Electrical System
One of the goals of this project was to make the system as cheap as possible. We wanted to make an electronics system where there was just one plug for the whole system. Normally this is done with a dedicated power supply for the whole system. This was a high cost so we didn't use it. In stead we used a distributor plug and the plugs that are allready used in the electric components that we are using. If cost isn't a issue for you you can work with a dedicated power supply and even add optional sensors to make the system more smart.
Because we chose to use a plug and play system the assembly of the electronics are very straightforward. The most important thing is that the lamp is connected with a timer. to simulate a day. The pomp isn't used in the timer. because plant are always growing and need water. This is the first thing thats needs to be done.
For the second step we are hanging the lamp to the roof of the box. For this we used the 3D printed part "lamp attachement" or a scrap piece of wood if you don't like to use a 3D printer. This part is screwed to the roof of the housing. With 4 M6 bolts.
The third step is to hang the dimmer on a reachable location with the dimmer holder. There is a 3D printable holder for this attached above. This is optional because the system will also work without it.
We chose to hang the distributor plug on the outside of the box because we wanted to reduce the risk of water damage. You can also opt for a big water tight box but we found that the distributor plug on the outside was more practical. We hung this distributor plug with 4 M3 bolts on the outside and a 3D printed hook specific to our box.
Step 4: Water
Because we want to test out hydrophonic growing, there needs to be a water system. We used store-bought flowerpots to create a water reservoir, but you can use other containers that would fit inside your housing. For circulating the water you use a small aquarium pump along with some tubing. To connect the tubing to the planter you can use the provided 3D part.
Step 1: Make sure your planter fits with your water reservoir. You can easily modify your flowerpots with a saw or knife. You’ll want to create a little waterfall to provide oxygen to the water.
Step 2: Secure the water pump inside the water reservoir. Add some hot glue to make sure it won’t come loose.
Step 3: Drill a hole in the planter(Ø9). To receive tubing, there needs to be a nipple on the planter. 3D print the provided file and glue it in place. Use silicon or hot glue.
Step 4: Drill holes in the planter to create the waterfall.
Because the water level can vary, drill multiple holes at different heights. You use rubber seals to control the flow.
Step 5: Cut the tubing to length and connect it to the pump and planter.
Attachments
Step 5: Flow Velocity
This subassembly is needed to level the plants, so this must be
easy adjustable in height. Of course we also have to put the lowest setting into account. Also, because the planter moves sideways on this point, we need something it can slide on, so we chose for a smooth curved piece from a PVC tube.
We use a gliding motion within a tube to adjust the height. With the help of some holes and a pin, the height can be adjusted.
The outer part, which is connected to the ground plate is a squared steel tube, the inner part is 3D printed.
The first step in making the outer part of de sliding tube. For this we used a square steel, black coated tube, which already had a plate on it, so it’s easy to connect to the ground plate. The lowest point for this place is 9cm, so we cut it at about 8cm, so the inner part sticks out.
Then, at every 1cm height difference we drill a hole of 5 mm. In the center of the tube. After this we remove the little sharp part with sandpaper so we can not cut ourselves while adjusting.
The second part is the inner part, which slides into the tube. To make this we measured the inner width and length of the tube.
Now that we know the measurements we can create a part that also has 5 mm holes and and extra bent layer on the top to create a round gliding effect.
We used a 3D-printer to create this part. Already with the curve and holes
The third step is cutting the PVC tube. We did this with a simple box cutter. The only demans fort his is that it’s wider than the planter, so it can easily glide on it no matter what angle.
Step 4: We connect the center piece of PVC with the inner part. In this case we used strong glue.
Then, we connect the outer tube with the ground plate, because this tube already has an extra plate with screw holes, we can simply screw it to the ground plate. Again with M3 bolts.
Step 5: All parts should be put together now, make sure it slides well inside the tube.
In the last step we need something that can hold it in place, luckely we already made holes, so a simple pen or loose screw will do.
Carefull: Make sure you put this part on the end of the planter, so the weight of the water doesn’t release the planter from it’s hooks.
Attachments
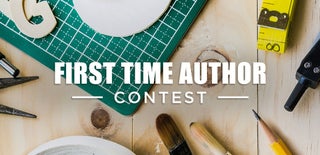
Participated in the
First Time Author Contest