Introduction: How to Make a Portable Auxiliary Work or Camping Light
Video tutorial on how to make portable auxiliary lights for your vehicle. For this I am using two flood lights from Oedro, 4 inch 27 watt led light from their Brave Man T1 series. These particular portable auxiliary lights can be mounted anywhere on your vehicle, trailer, recreational vehicle, and possibly boat, however these use a magnetic base so they can only be stuck to steel components. These lights are perfect for working on your vehicle, camping, farming, going out on the trails, loading a vehicle, etc. They use a 12v power supply from your vehicle, receiving power from a cigarette light socket, but you can always install battery post clamps instead depending on your preference.
Tools/Supplies Needed:
- wiring
- adhesive filled heat shrink
- regular heat shrink
- soldering iron
- solder
- relay
- switch
- lights
- weatherproof connectors
- wire cutters/strippers
- cigarette lighter plug
Step 1:
First starting with the wiring, depending if you are using 1 or 2 lights will affect how you want to wire up these lights. For the most part I am also trying to repurpose some components I had laying around. One is what’s left from a generic wiring for auxiliary lights and the other is a cigarette lighter plug which I had saved from something.
For these lights I am using weatherproof connectors so this can be used in the rain with no issues. Cut the wires to length if need be and strip the casing.
Install the seal for the weatherproof connectors. These weatherproof connectors can be purchased off eBay, I have used the same ones in my light bar installation video as well. They look cleaner than spade connectors and the connections are protection from the elements. But they do need a special crimper to install the terminals.
Install the terminals and pinch them in place by hand, then using the terminal crimpers for the connection. Once done, install the connector casing and retaining clip.
Step 2:
Next is to cut the wires which will be for the y’d harness. We have two lights, these will need to go into one. For wiring size, a gage chart will be needed. This will be dependant on the light draw and distance the wiring will be ran. The wiring I am using is oversized, but this will allow me to use this harness on other lights as well if I wish.
One side of this pair will have a weatherproof connector and the other side will be soldered.
Now the second pair of wires will be cut slightly long, these will be incepted by the shorter pair of wires.
The longer pair gets a connector on both sides.
One side will be to connect to one light and the other connecting to the main supply wire. This y’d harness can be removed and one light can be used instead, so I have two options if I wish. The two separate lights will allow me to illuminate are area from two directions or in two opposite directions.
Considering this is a much heavier gage wire, instead of using my soldering iron which will take much longer to heat up the wire, I am using a handheld soldering torch. Install an adhesive filled heat shrink to help protect the connection from the elements.
For the main power wire, the length will depend on where you want the wire ran. If it needs to go to the rear of the vehicle or trailer, ensure it is long enough. But remember it must be the correct gage of wire, otherwise you may experience a voltage drop or the wiring will overheat becoming a fire hazard.
Add a connector to the one side and the other will be soldered.
The wiring kit did have some wires cut off, so I will need to add those back in. I have the relay, with the pigtails from the connector and the only wires I do not need to run is for the switch. This switch can be mounted anywhere, you will need to pick something that has a case or the contacts hidden so the circuit cannot short. Unlike my light bar wiring guide, this will remain a switched power and the switch also has illuminated leds. Three wires go to this switch, one is the power in, power out, and a ground wire.
Solder in the supply power wires to the relay.
For me, this part will remain inside the vehicle so there really isn’t a need to use adhesive filled shrink tube to protect it from excessive moisture. Your setup might be a little different.
Next soldering on the cigarette light plug, simply unscrew the tip to expose the contacts inside. I removed the hold wiring and will be adding the new wiring so everything matches.
I want to keep the wiring clean looking, so I have added a rubber casing. The ground wire goes on the outside spring clip and the power is the main center probe. I also added some liquid tape to help protect the exposed conductor for the power wire as added safety. We do not need to fuse this harness as it’s already fused for the cigarette lighter output in the video. Be sure to check what the rating of the circuit is in your owner’s manual and do not overload the vehicle’s circuit.
The total length of the harness will be about eight feet, this included the power from the cigarette light plug, to relay, and then to the light. So according to my wire gage chart, the wiring can handle up to a 20 amp light.
Step 3:
In between my wiring I prepped these magnets so the coating would have time to dry. These magnetic bases were originally intended for a hook mount and are rated for 10 lbs each.
Give them a wipe down with a wax and grease removed. This will ensure the coating will stick with no pealing issues. Apply a tape edge if you wish and give them another wipe down with wax and grease remover.
For the coating, I am using Plasti Dip. You could apply a vinyl coating, felt pad, rubber pad, or some form of a protection to prevent the vehicle’s paint from being scratch. I would recommend at least 3 coats to provide that cushion when the magnet is attached to the paint. You’ll also need to be careful installing the magnets on metal, if they snap in place you may cause denting too.
Step 4:
Remove the brackets on the lights to install the fasteners. As you can see these particular brackets also have a horizontal adjustment which is handy for work lights.
Install the center fastener, Oedro does supply the hardware but I found the center bolt was too long so I used a couple I have laying around instead. You can apply some threadlocker if you wish to these bolts. Ensure the head of the fastener will not interfere with the surface it’s mount on too.
Reinstall the lights on the brackets, I may switch these socket head bolts out for hex heads as I can’t really get my allen key in there to tighten them. For the most part I won’t be using this setup on a moving vehicle so they’ll experience minimal vibrations.
Step 5:
Now for a quick demo, they mount perfectly on top of the box, we can face each light in opposite directions and even alter the horizontal angle of the beam. The switch wire is long enough I can leave it outside of the vehicle. The lights can even pick up a power source from a trunk area in a vehicle and the switch wire is long enough to reach to the driver.
The camera shows it darker than it actually is. Flipping on the lights, we have an extremely well lit area, perfect for working on your vehicle, camping, farming, going out on the trails, or loading a vehicle.
Stay up to date with my latest tutorials, don't forget to FOLLOW my profile and be sure to check out my YOUTUBE page as well for all your DIY needs.
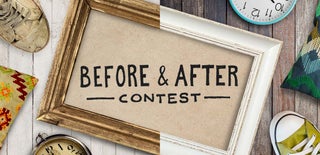
Participated in the
Before and After Contest 2017
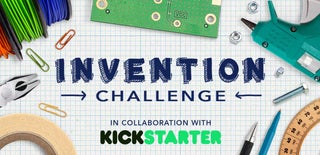
Participated in the
Invention Challenge 2017
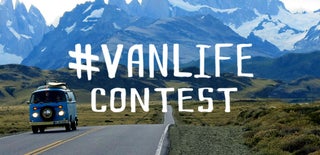
Participated in the
#Vanlife Contest