Introduction: How to Make a Small Tap Wrench on a Lathe (with Drawings)
Most tap and die sets come with a 12" tap wrench, which is fine for most things but such a big driver can be a liability for small taps leading to broken taps and stripped holes. A small (in this case 100mm/4") tap wrench can be very useful.
In this Instructable I will explain how to make a traditional double-end adjustable tap wrench on a lathe.
A tap wrench is a classic first lathe project and for good reason; there are fairly high tolerances and very little material is used yet the result is a useful tool that will last a lifetime and is in my opinion aesthetically far superior to the modern T-handle style wrenches you can buy today.
Additionally, whilst I have provided my drawings, you could easily adapt the same method to produce a variety of different designs in different sizes and from different stock.
Supplies
Materials:
- 3/8" steel bar 150mm length or larger. Tool steel is preferable but mild steel works fine.
Tools:
- A lathe with some means of holding the steel bar; a 3 jaw chuck would work well but I used a collet.
- Right hand turning tool
- Radius turning tool
- M6*1 tap and die; you could also use 0BA or 1/4" BSW or UNC.
- A die stock and a tap wrench (ironically)
- A drill to match your tap and a 4mm drill.
- A small (<5mm) square or triangle file
Optional tools:
- Milling machine
Step 1: Design
Attachments
Step 2: Making the Set Screw
With about 45mm of stock sticking out of the collet turn the 4mm section. Due to the high aspect ratio of the part you will need to take very light cuts as you approach final dimension. Without a travelling steady or similar you will probably get a lot of chatter; thankfully this part cannot be seen when the wrench is assembled so it doesn't matter too much.
Next turn the 6mm section to size. I cut a small gulley just behind the 6mm section that ensures that there will be no partially formed threads near the shoulder, this would in principle allow the screw to be threaded in further but since such travel shouldn't be necessary, it's largely an aesthetic choice.
Finally thread the 6mm section with a die and part-off the screw to length and de-burr. Cross drilling the part will be covered in a later step.
Step 3: Turning the Handle to Shape
Start by forming the long end of the handle.
Face the part then scribe two lines at 20mm and 40mm from the faced end.
Set the cross slide to cut a 6° taper.
Using a convex radius tool of approximately 8mm radius make a shallow plunge cut just to the right of the inner scribed line then using the cross slide cut a taper to the left, repeat until it looks aesthetically pleasing to you (although make sure the thinnest part is at least 6mm across.
Now measure the thinnest part of the tapered section.
Rotate the stock in the chuck
For the short end of the handle, turn the part around and face it to 90mm in overall length.
Now scribe lines at 10mm and 30mm from the end.
Repeat the taper process from the last time but instead of aiming just for a nice looking part, aim for the dimension you measured last time using the cross slide micrometer dial; this should make sure your part ends up symmetrical.
Step 4: Boring the Parts
First cross drill the handle to 5mm half way between the tapered sections. I did this using a cordless drill and a bench vice starting with a centre punch and 4mm pilot hole. Cross drill the set screw to 4mm using the same method.
Then with the part in the lathe spot drill the short end of the handle. Then drill a 9mm deep hole of the size needed for your tap (5mm for M6).
Then drill a 4mm hole until it breaks out into the 5mm cross-drilled hole.
Tap the large bore to the required dimension.
Finally use a file to cut a 90° notch in the end of the 5mm hole nearest to the long handle (see drawing).
At this point the tap wrench is useable, however for best performance at least one side of the central round should be filed or milled flat.
Step 5: Milling (optional)
Using either a milling machine (pictured) or a file, make one side of the central section of the handle flat. This means that the wrench will be able to grip taps with shorter shanks than it would otherwise and in my opinion makes the wrench look a lot better.
With this done all that is left to be done is to de-burr and clean the wrench. If you used tool steel it should now be heat treated.
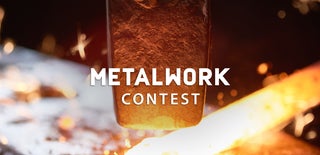
Participated in the
Metalworking Contest