Introduction: How to Re-Engineer Paper Back Into Wood
Recycling vs Upcycling.
According to the Environmental Protection Agency, the average person produces about 4.38 pounds of waste per day. Multiply that by the 300 million consumers in the US and we're left with about 250 million tons of waste every year, and only about a third of that gets thrown into the blue bin.
But let's face it, the recycling system in the United States is not perfect. While recycling paper saves money and energy, it also creates a dastardly new substance. Paper inks, cleaning chemicals, adhesives, clays, and dyes are filtered out of the paper fibers and collected into one giant pudding known as paper sludge. Few commercially viable uses exist for this sludge, so companies find loopholes and slip the poisonous substance back into the landfill.
After paper is used, it can be stored and then laminated into Paperwood. This new product can be milled and used as building material for another life. Once it is finished, It can be recycled again into paper because it was laminated with water-based adhesive. This cycle continues outside of the landfill and is a self sustaining material that can be made from the stuff we throw away everyday.
So let's turn that pile of paper into something beautiful....
What you'll need:
- Lots of paper
- Wooden dowel
- Water based adhesive
- Paint tray
- Roller brush
- Bandsaw
Step 1: Gather Your Paper
Try to find paper of the same dimensions because as you start to laminate your paper-log, you don't want random pieces of papers sticking out of your roll.
Look for paper with colors, images, text, and anything interesting in order to add beautiful grain lines to your Paperwood. I used sketches, drawings, diagrams, and renderings from my old architecture projects. Architecture studios create a ton of paper waste.
You can use lined paper, graphed paper, magazines, news paper and packaging. You can even select a specific set of papers to tell a story with your upcycled Paperwood, like I did with my architectural drawings.
Step 2: Laminate Your Paper-Log
This is the most important step (and the most tedious).
I used 8.5"x11" and 11"x17" sheets. The common dimension of 11" was the length of the paper-log.
It is best to find a wooden dowel with a large radius. It is harder to laminate papers around a tighter circle.
Let's begin.
- Prepare a work station (this could get messy).
- Pour a few ounces of your adhesive into the paint tray. I used Palmetto's water based LamiBond
- Start by attaching one edge of your first sheet to the dowel (in my case, this was the 11"). Make sure that the edge is perfectly straight, or else the paper will roll at an angle and create future problems.
- Coat one side of the paper with adhesive (doesn't matter which side) using the roller brush.
- Slowly roll the paper tightly around the dowel, making sure it is straight. Use your fingers to press out and air bubbles and pockets of adhesive build-up.
- Continue this process in 10-20 page intervals. The adhesive must dry so that the layers don't shift when you apply pressure.
This will take a while. I am currently designing a machine that will make the laminating process go much quicker, but for now you must do it by hand.
Step 3: Milling Your Paper-Log
Now that you have your paper-log, it's time to transform it into usable material.
Start by making straight cuts on either side of the dowel, getting as close as possible. Cut your log into sections, and square off the edges.
You should now have several usable pieces of Paperwood. I even used the scraps to make small chips showcasing that beautiful Paperwood grain.
You can cut it, sand it, and finish it; just like natural wood.
Step 4: Create Something New
There are countless way for you to show off your new material.
I cut and welded steel from an old desk, cut glass out of an old window from a demolished house, and upcycled my way to a beautiful new nightstand. This project was entered in the Vellum Furniture Design Competition in San Luis Obispo in 2015.
What will you do with your Paperwood?
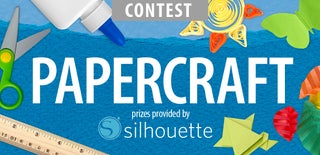
First Prize in the
Papercraft Contest 2017