Introduction: How to Use Creation Workshop V1.0.0.75 for DLP Printers
Entered into 3D printing contest! Check it out here:
https://www.instructables.com/contest/3dprinting2016/
-------------------------------------------------------------------------------
The purpose of this instructable is to explain how to use Creation Workshop. Creation Workshop is a software created to control DLP type printers with ease.
In what follows I will explain how to use this software for a DLP printer, and most of the time reference The LiteFab - the Affordable and Rugged DLP Printer, which is the DLP printer I designed. However, this software works with all types of DLP printers, so all of what follows will apply to a variety of DLP printers, not just the LiteFab.
I attached the software here for reference. This is v1.0.0.75
Attachments
Step 1: The Main Windows
There are 4 main windows in the Creation Workshop (CW).
1. Main model window. In this window you will load models, adjust size, add supports, etc.
2. Preview window. This window displays what your projector will be shining onto the vat, or the gcode. Its basically the preview tab for your part before you start printing.
3. Control window. This window has all your manual controls on it.
4. Configuration window. This window is for configuring your machine and your resin/slicing profiles.
Step 2: Configuring Your Machine
We'll start with how to configure your machine.
In this window, there are several sections used for configuring your specific machine. Below is described what each section is, corresponding to the colors on the image.
-------------------------------------------------------------------------------
RED - This lets you add new machines, or delete ones.
ORANGE - Applies any changes you have made to the currently selected machine (in RED)
YELLOW - Defines your build size. The adjust button will allow you to fine tune your build size. If you print a model that is 20mmx20mm, and it comes out 19.2mmx19.7mm, this button will auto-calculate the adjusted build size to get your model to print out at 20mmx20mm.
GREEN - This is the port that connects to your controller. In the case of the LiteFab, it would be the port that the Arduino with GRBL installed is on.
BLUE - This is just an informational window. It gives you the accuracy based on your projector resolution and your build size.
PURPLE - This lets you select which display you want to shine the picture is on. You will need to have your projector plugged in at this point, or it won't show up on the list. The current one listed is just my laptop screen currently. To remove parts, select the minus button. To pick your display, find it in the list, select it, and click the plus button. This will add it to the Configured Displays list.
PINK - This area is if you have a USB/Serial enabled projector. You can configure it here, so you can control the projector through the computer. Additionally, you can add a Mask here. The mask is a gray-scale image that adjusts the picture output of the projector, to create a more even light distribution. See link here on how you can make a Mask. This isn't required, its more just for enthusiasts.
BROWN - This has a bunch of options that you can select for your printer, if you have them.
Step 3: Configuring Your Resin
There is a wide variety of resins available on the market. To get parts printing correctly, you will have to do a fair amount of experimentation with each resin. Unlike FDM/FFF printing, where you just have to worry about extruder temperature and extrusion speed, DLP/SLA is a little trickier....
Because each projector has a different power output, and that power is spread across the build area which can be all different sizes, each machine will have a different amount of UV per mm2. This means even with the same resin, different machines will have different curing times. Stacked on top of this, each resin manufacturer has different formulas, in other words different amount of UV light required to cure. You'll spend a lot of time in this window, configuring your resin.
-------------------------------------------------------------------------------
RED - These are your profiles. Much like before, + makes new profiles, - deletes them.
YELLOW - Apply changes to your profile here. Also a small help about Gcode commands to the printer, but you usually dont need to worry about that.
ORANGE - Here you can setup sub-profiles. Basically, you can set up Makerjuice G+ as main profile, and then colors as sub-profiles. There isnt really a lot of benefit to this, as you still need to switch colors then save the profile before slicing. You could just make a second profile instead of a sub-profile, and not have to change the colors and save....
The import part in this area is the Calibrate button. This will bring up a smaller window, which you can use to fine tune your profiles. Basically, it prints a bunch of walls, then cures one layer at the various intervals. This will let you see at what curing time the resin needs to cure. Once you set your minimum time, and intervals, hit Print Test Model, and it will generate the code and images for your calibration object. Make sure ALL your other settings are correct, as it will fill in the rest of the required information (like Lift/Sequence, Settings, and Gcode Start/End stuff) from you current settings. When you are ready to print your calibration part, you can hit the play button at the top, like you would for any print.
GREEN - These are your main settings for your resin.
-Slice Thickness - Thickness of each layer in mm.
-Exposure Time - Amount of time (in milliseconds) projector will display each layer (I.E. Curing time)
-Bottom Exposure - This is the same as above, but only for the first X# of layers. This is used so you can over-cure your bottom layers, to help get better adhesion to your bed.
-# Bottom Layers - The # of layers at the beginning of the print to do at 'Bottom Exposure' time.
-Anti-Aliasing - Fades the edges of the layer by X amount (measured ?) so that your part as a smoother surface
-Slice Outline - Prints outline around part
BLUE - Reflects slice image in either axis. Most projectors have this adjustment build in already through the menu settings.
PURPLE - Settings for the machine / Arduino.
-Lift and Sequence time - Time it takes to lift and then retract. This value is auto-calculated based on the below values. I usually add little more time, to give the resin time to settle before trying to cure.
-Z Lift Distance - Distance to lift above the platform, before returning to layer height.
-Z Lift Speed - Speed at which to lift. This speed will depend on how well your parts peel off the vat. Too fast and it may stick to vat due to vacumn forces + adhesion to vat bottom.
-Z Bottom Speed - Lift speed for the bottom layers
-Z Retract Speed - Speed at which to return to next layer. I usually have this set pretty high, because at this point the object shouldnt be attached to the vat anymore.
-Slide/Tilt Value - I dont actually know how this one works, as I dont have this on my machine. Sorry.
-Build Direction - Lets you define bottom-up (I.E. how the LiteFab does it) vs. top-down (how the Chimera DLP does it)
BROWN - Lets you export your slice, if needed. I've never used this.
-------------------------------------------------------------------------------
The next window lets you define the various sections of Gcode the profile will build. The only edit I did to mine was at the end go to 150mm above vat. If you have an endstop configured, you can add homing to Start (G28). If you have a wiper or vat peeler mechanism, you can add it to the lift section.
Step 4: Loading Parts and Arranging Them
And now back to the main window!
Here you will learn how to load parts and arrange them. You can scale, move, rotate, view, etc. all in this window.
-------------------------------------------------------------------------------
First, you will want to load a part to play around with. You can do this by clicking on the folder in the top left hand corner. You will then need to find a STL file to load. I chose a 20mmx20mmx10mm calibration cube.
On the right hand side you will see several menus. Each of these expands to give you several more options to pick from.
Additionally, just to the left of these menus are some view options, for re-centering the view. You can left click to rotate view, and right click to move view. The Home button (top) will return to the front view, and the Top button (bottom) will view the build platform from the top.
-------------------------------------------------------------------------------
SCENE - This gives you a drop down of all the parts you have loaded. The + will, the - will remove the selected part/support, and the X will remove everything selected. Additionally, it will show any support material that is used under it. You will see more about support material in the next step.
OBJECT INFO - This will give you information on the part loaded. The cost is calculated from your slicing profile cost, based on the volume of the part.
MOVE (mm) - This allows you to move the part. There are several helpful buttons for arranging parts included. The first will place the part on the build surface, the second will center the part, and the third will auto-arrange parts onto the build platform. Auto-arrangement will happen automatically when you load new parts. Below these 3 buttons are menus for moving the part in any direction. Set the # of mm to move, then click + or - to move the part along that axis in the specified direction.
MIRROR - Mirror is pretty simple. Just mirrors parts on that specific plane. I.E. Z is the plane created by the X and Y axes. Simply put, it will flip the part upside down for Z, flip it left/right for Y, and forward/backward for X.
SCALE - Scale will let you adjust the size of your part. You can either scale all of the axes at once, or one at a time. Additionally, there is a button for converting a part loaded in inches into mm, and vice versa.
ROTATE - Rotate again is very similar to many of the previous menus. Type your rotation value between 0 and <360, and click +/- to rotate in Clockwise/Counterclockwise direction.
VIEW OPTIONS -
Step 5: Adding Support Material
Next is how to add support material to your model. The large + on the left hand side will bring up the support structure menus, as shown in RED.
-------------------------------------------------------------------------------
Once you have the support structure window up, there are several things you can do. The first, simplest thing is to add a large base (RED Box). This gives a nice, flat area for good adhesion to the bed. If you want to remove support you can use the yellow button near the button to remove all support. Or, you can switch back to Scene menu, select supports individually, and remove them.
The next button is the add manual support. You can select where you want support by clicking on the model where you would like support.
The next button is auto-support. This will automatically add support where it thinks it is needed.
Below the support is a small 2D view of what the support looks like You can adjust the various thicknesses here. Any changes you make will be shown in that view, and next time you add support it will make that version of the support material.
The dropdown menu below will either allow you to do bed of nails, which is a fairly evenly spaced bed, vs. adaptive which will add support where needed, with a single maximum spacing.
-------------------------------------------------------------------------------
Note that MeshMixer also has a great support structure tool, with alot more options. You might make your support there, then add it all at once as a single model.
Step 6: Connecting, Slicing, and Printing.
Now that you have learned how everything else works, its finally time to do some printing.
-------------------------------------------------------------------------------
First, go ahead and connect to your machine. This is done using the the plugged in cord at the top. Once you click it, it should attempt to connect. When successful, the plug should gray out and the unplugged cord should turn white. Additionally a new 'window' should appear on your projector that is all black. This is so that it isn't curing resin before you hit print.
Next you will want to slice the part you have loaded. The small cake looking button to the right of the two cords is the slice button. This will bring up a smaller window that allows you to pick your resin profile to use for slicing. After slicing, the print/pause/stop buttons will turn white (if machine is connected) to indicate that printing is ready. If you want, you can jump over to the Slice View window and take a look at the slices and Gcode before printing.
-------------------------------------------------------------------------------
When you are ready to start printing, go ahead and hit the Print button! It should start immediately printing. Pause will temporarily stop printing, and stop will stop the print entirely.
Thats it!
Step 7: The End - Helpful Hints
On to some helpful hints.
-------------------------------------------------------------------------------
-First off, if you are having issues printing, a good place to look is buildyourownsla.com
-Sometimes, the build platform isnt perfectly level. In these cases, sometimes its a good idea to lift the part up off the platform and print on a bed of nails, like in this example.
Step 8: Appendix a - Change Log
Here I will document any changes to this instructable.
-------------------------------------------------------------------------------
4 May 2016 - Instructable published!
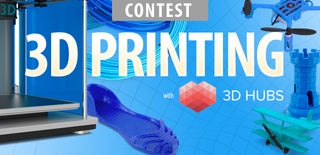
Participated in the
3D Printing Contest 2016