Introduction: How to Make a Magnetic Stirrer That Doesn't Cost Like a Professional One
I needed a magnetic stirrer for my chemistry lab so I made a cheap one that looks almost like a professional one, but doesn't cost very much.
It is made from recycled parts from an old CD-ROM, a printer motor and things from an old CRT screen board (like resistor).
The things you need:
- a CD-ROM metalic case (or what case you want)
- a piece of aluminium sheet
- 10 screws (3 mm diameter)
- 6 screw nuts (for 3 mm screws)
- 2 circular magnets (1 cm thick, 1-1.3 cm diameter)
- a 5.5 cm circular aluminium sheet
- a little passive heatsink (optional)
- a printer motor (almost any motor could be used )
- 1 little screw for motor
- a LM317 chip
- one 0.1 uF capacitor
- one 10 uF capacitor
- one 5K potentiometer
- one 240 ohm resistor
- a universal board for electronics (4 cm width x 2 cm lenght)
- a 12 V AC power supply
-a knob
Step 1: Step 1
Let's begin!!!
Firstly let's drill some holes.
Drill the small holes with a 3mm drill bit, the big one I drill with a 10 mm drill bit and the smallest with 2.5 mm drill bit.
Images have indications about lenght and width, so don't miss them,
Step 2: Step 2
Let's make the circuit.
When the circuit it's done, bend down the potentiometer.
Step 3: Step 3
Here are the magnets and their support.
Drill through the center of circular aluminium sheet.
I used a plastic support for more stability.
Step 4: Step 4 - Assembling
Step 5: Step 5
And there is it. It's done and assembled.
Hope this tutorial was useful for you.
You can use it for stir almost everything.
As stirring bar you can use a magnetic bar from CD-ROM or you can buy a coated one that not reacts with other materials, even neither with acids.
Step 6: The Magnet and the Power
I make my own stirring magnet covering a little magnet with hot glue.
In other photos, you can see the power.

First Prize in the
SciStarter Citizen Science Contest
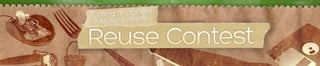
First Prize in the
Reuse Contest
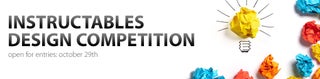
Participated in the
Instructables Design Competition