Introduction: Hybrid Knife Block From Firewood
Welcome Friends! Our (not so) sharp cooking knives keep getting chipped, partially because we need somewhere safe to store them where they won't knock into other cutlery. I read that standard magnetic strip knife blocks / holders tend to chip the edges of knives if you don't carefully place the spine of the knife on first and roll the flat on. I live in a shared house and getting everyone to abide by that isn't going to happen. The other option is a magnetic one with a wooden contact plate. That's kinda difficult to do without very strong magnets, which aren't so easy to come by in the trash.
I had a hunk of ash firewood, and some old hard disk drive magnets, and that sort of shaped the hybrid thing I ended up making.
It displays the natural split edge of the firewood, which my inner nature-boy really likes, but had indents, that, in combination with magnets, holds a front set of knives. It also incorporates a back row of more traditional style 'slot-block' knife storage.
Step 1: Arrange and Assemble Your Favourite Blades
They don't all have to match! I cook a reasonable amount and have used a lot of knives over the years. I haven't hung on to so many. The ones I keep I really quite like.
Design your block around the ones you like and use rather than what looks good or was the most expensive. This knife holder is all about customising to your knife collection - that's the point - you won't be able to go and buy a new set to fill it because it will fit the ones you made it for like a glove.
Grab a lump of firewood and consider options. I went with a split faced ash that had some prominent knots/branch stubs. I think the same concept would look really good in a darker wood too, or any wood that will give a nice contrast between the freshly routed knife retaining indents. I reckon oak would be particularly good.
Arrange them in some shapes that please you and look like they will work with the wood. I went for an arching round the knot sorta thing.....
Step 2: Tools and Materials
You could do this whole thing with hand tools. I think that would be a cool project, but one I don't want to dedicate enough time to. I think it would be a great project to make with a CNC router too, but I don't have one (yet). I used what I had ...
Materials used:
Chunk of firewood
A scrap of plywood (the usual skip bounty) for the template
One pine pallet board, to make the template mounting, and set up cut depths on the table saw.
Three scrap hard disk drive's worth of neodymium magnets.
Glue
Tools I used:
A small router and 10mm guide bushing. A 1/4" shank 10mm straight cutter.
Some chisels, mallet, knife, drill, screws, slide ruler.
Calipers - to check the depth of the indents and the magnet recesses.
My modded bandsaw - to rip the firewood and cut the template
A table saw - to make the back channels, because I have one, but you could just as easily use the router or handsaw and chisels.
Clamps - useful for gluing the back on.
Array of personal protective equipment: goggles, dust mask, ear defenders, full suit of medieval armour, all the usual.
Step 3: Flatten the Knife Block's Back and Bottom
This makes the other steps much easier.
There are various ways to accomplish this. Your capabilities and access to tools may influence which bit of wood you choose. A nice straight grained log can be split by hand and one surface can be hand planed relatively easily.
I got lucky in that the back of mine was already chainsawed quite flat even though the front was quite undulating/ knotty. The base was not too far from flat either. Both surfaces were no trouble to get right on the jointer. Although... when the surface is wider than the jointer (which the back was), it's always a kinda-almost-flat finish that I achieve. I use the flip each pass method, to get the whole surface. It is certainly good enough for this application.
Step 4: Fix Template Supports
We need to be able to mount our soon to be made routing template co-planar to the base. To do this we cut a pallet board in half, rip it to width on the table or band saw, and screw it to either end of the firewood.
It doesn't have to be pretty, just have parallel edges and equal width.
Once that's on we can place a small ply board over it and start work on that. I'm using 10 mm ply I found in a skip. It's a good idea to screw it down, to the supports, and then pencil on some of the main features of the firewood log. A slide rule can be helpful in locating them...
Step 5: Create a Routing Template
Play with your knives (just like your mom said right?!) and make your favoured arrangement - take a while to try various combos and see what shapes you like. You should do this before the previous step, so you can see what they look like on the actual log. Take a photo when you're happy, so you can recreate that on your template.
Lay them in your preferred shape on the ply and draw round them as accurately as possible.
Step 6: Cut Out the Template
Now cut to the lines you drew. I used a bandsaw, but a scroll-saw, jigsaw, or even a hand coping saw would also make short work of thin sheet material.
Take your time, and consider how big your router guide bushing and cutter combo is... I used ones that are basically the same size so could cut straight through the pencil line. If your cutter is smaller than your guide bushing - which is normally the case, calculate how much you need to cut outside of your lines - it will likely be a mm or two.
Step 7: Rout Out the Knife Shaped Indents
With the template complete we are ready to plunge in there with the router and guide bushing.
As I was pushing the limit of cutter stick-out and it was only a 1/4" shanked router bit, I took it nice and slow, no more than 3mm removal per pass.
The guide bushing means you stay perfectly within the lines...
As the plunge depth was close to the limits of the router, I was collecting dust from below with the vacuum hose wedged between the firewood and template.
Step 8: Ripping the Firewood
Ok so in real life I did this before the routing, but I don't think it matters which way round you do it.
By ripping approximately 3/4" (18mm) off the back of the piece, we are getting ready to create the back slots for the three long knives, and gaining access so we can rout pockets for the embedded magnets, which will sit behind the knife indents.
When ripping a big piece like this take the time to set the bandsaw up right, and that the blade is sharp. A good solid fence (ideally the same height as your work-piece helps a lot).
The firewood log was a touch too big to fit through my 12" bandsaw, so I cut a sliver off the bottom first...
Step 9: Rout the Magnet Pockets
The magnet field strength of a magnet is roughly inversely proportional to the distance cubed away from a magnet. In practice it is more complicated and vary with all manner of factors like the orientation, shape and type of magnets but as a general rule of thumb it works. That means if we double the distance the knives are from the magnet, we will greatly reduce the holding force (approximately 1/8 as strong).
All this is to say the distance between the magnet and the knife is pretty damn important. If the wood separating them is too thin then we risk punching through with the router. If it's too thick, the knives are not going to stick. After some tinkering and testing with my salvaged HDD magnets, I settled on aiming for a thickness of 1.5mm (0.06").
It's a thin bit of wood, and so the measuring needs to be quite precise. I used a digital caliper and though it was nerve wracking at times, it worked out well.
As the magnets were all roughly the same size and shape, I made a very rough and ready router template from ply. See the photo notes for details.
Step 10: Cut the Conventional Knife Slots
I cut one extra, just in case of future knife acquisitions...
I marked out the sizes in pencil, with a bit of leeway, and used the tablesaw and cross cut guide. The router would also be good for this step.
Step 11: Glue in the Magnets, Glue on the Back
I used two part epoxy to glue in the magnets. Best practice is to 'wet' sand the epoxy onto the magnet surface, but that's a bit messy. So I just dry sand one side of the neodymiums by hand first. Then I wipe on the epoxy and pop it down in its hole. With that done I had a little epoxy left so I mixed in sawdust to make a putty which I put over and around the magnets just to be sure they wouldn't be going anywhere.
With that done, we need to keep the whole thing that way up, but we are ready to glue on the back!
That's just a question of applying wood glue and clamping down. It's a good idea to use sacrificial softwood pads to protect the knife block from the clamps.
Step 12: Trim the Back and Ends, and Brush Up
The next day it's de-clamp time!
The newly glued on back is then trimmed flush with the front. The ends are curve-ified on the bandsaw and then all the edges are sanded, to be perfectly flush and smooth.
I gave the front a wire brush by hand, and that's all - I may coat it with Osmo wax-oil in the future, I haven't decided yet. I did some tests on an off cut of the same firewood log...
Step 13: Knife Up and Use!
That's it, we're about done.
Mount the new hybrid firewood knife holder on the wall (preferably using keyhole slots or other hidden fastening) or plonk it on you kitchen top.
I hope you found some of that interesting and it gave you ideas for your own projects. If you liked it, subscribe to me here on Instructables and on my youtube channel for lots more unusual projects.
Happy chopping.
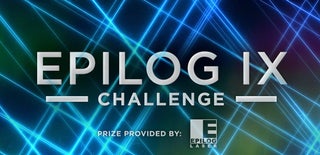
Participated in the
Epilog Challenge 9