Introduction: Induction Demonstrator
According to Faraday’s law, an electromotive force is induced in a coil when the magnetic flux through the coil varies in time: V=-d/dt(Phi_B). For a homogeneous magnetic field, the flux is the product of the field strength B, the area of the coil A, the number of windings N, and the cosine of the angle between the coil axis and the magnetic field: Phi_B=NBAcos(theta).
Electromagnetic induction was discovered in 1831 by Michael Faraday and its importance cannot be understated: practically all electricity is produced by generators that work on induction. In addition, transformers, inductors and pick-up coils are all based on induction.
No physics course is complete without studying induction, and to liven up the classroom, to spark the imagination of the curious students and to distinguish science from non-science, a hands-on lab or a live demonstration is crucial!
One common demonstration of induction is letting a magnet fall through a copper tube and seeing how it slows down: the effect is striking, the material is cheap and robust. However, the demonstrated effect, induction breaking, is more complicated than induction alone, and it really helps to accompany it with a demo that shows the induction directly.
Let’s show induction the way it is defined: an electromotive force is induced by putting a magnet inside a solenoid, producing a current in a galvanometer, and an opposite current is seen when the magnet is removed. The difficulty is practical: in a large classroom, the reading of the galvanometer (if you can find one!) is impossible from the back rows.
The induced current can also be used to light up a lamp. LEDs can produce intense light, but need a potential difference above 2-3V, depending on the color. Faraday’s law says, to get 1 Volt, you have to vary 1 Tesla over 1 square meter in 1 second! That’s the kind of magnet you find in a superconducting MRI machine!
Neodymium magnets have a field strength of about 1 Tesla, but you don’t want it to be larger than a few cm, otherwise they represent a real hazard. To get to 3V, we must use a coil with a large number of windings, and make the magnet move fast through the coil. With 300 windings and getting the magnet in and out of the coil in 10ms, we can indeed reach 3V with a 1T magnet of 1cm^2!
In this demonstration, we drop the magnet through a PVC tube. A couple of coils have been put over the tube, and each coil has two LEDs over its end, in opposite polarity. If the magnet falls through it with high enough speed, both LEDs will give a short but bright flash. One coil is sufficient as a demonstration, but multiple coils give a much more spectacular effect
Step 1: Required Materials
- 1 meter PVC tube of 16mm diameter. It is a standard tube used of electricity distribution in buildings and are available at any hardware store. I paid 90cents for 2m and sawed in two pieces of 1m. The walls are about 1mm, so the inner diameter is 14 mm.
- A 12x20mm cylindrical Neodymium magnet: it easily fits in the PVC tube, and with the same magnet you can do induction breaking demonstrations with a copper or aluminium tube. Ten magnets of 12x2mm stuck together work just as well and allow you to investigate the effect of the magnet size on the induction
- 0.2mm enameled magnet wire (AWG32). You need 15-20 meter per coil, that’s 5-6 grams. So 100meter will get you 5 or 6 coils, 100 grams 15 to 20. I used recuperated magnet wire from the degauss coil from an old TV. If the wire is thicker than 0.2mm it will be hard to get 300 windings in a compact coil. If the wire is thinner than 0.2 mm it will be more fragile, and its resistance will reduce the intensity of the induced current. I think 0.16mm(AWG34) would probably still be fine.
- A sheet of paper. Printed squares of 1cm (or 5mm) are really handy to get the measures right
- Single row DIP circular hole socket, 4 holes per coil
- LEDs, 2 per coil. Red and orange are good for low turn-on. Green and white are the brightest. Regular 5mm LEDs are perfect, but you try out any type.
- Cellotape
- Transparent nail polish
To make a 4-tube wall mount:
- 8 PVC-pipe snap-clips per pipe: sold wherever pvc pipes are sold
- 2 wood blocks
- A box for the magnets to fall into
- Hot glue, double-sided tape
Step 2: Making the Coil Tubes
The coil should be as close as possible to the tube, and it can in principle wound directly on the tube. But it’s much nicer if you can move them around. Paper is actually a very suitable material to make the tube since it is thin and can be made to fit the tube precisely.
For every coil, cut a piece of 4x10cm paper and a piece of 4x5 cm paper. The width of the coil tube will be 4 cm, and 5 cm fits exactly once around the tube (16mm x pi =50.3mm), 10cm fits twice around the tube. The shorter piece of paper is temporary: it is kept between the tube and the coil tube during winding, and will later be removed. Without it, the coil would be too tight on the tube.
Roll the short and the long paper together around the tube, with the short paper on the inside. Cover the central part of the coil tube with two 5cm pieces of cellotape. Make sure all is nice and tight. Take it off the tube. Make a couple more than you need and select the best ones
Step 3: Winding the Coils
The coils need to have at least 300 windings. I did it in 4 layers of 80 windings, wound on the central 2 cm of each tube. You’d expect to get 100 windings of 0.2mm in 2cm, but in practice it’s a bit less. It may be the finite thickness of the isolation, it may little bits of space between the windings. A neat tight coil is much more compact and much more pretty than a rushed messy coil. After some practice and using strong reading glasses, it took me about 1h to wind a coil.
Start fixing the coil tube and the end of the wire to the tube, then start rolling tightly at 1cm from the centre. You can apply some force to keep the windings neat and tight since the inner piece of paper will be removed to give more space between the coil and the tube. When 2cm has been wound, cover the windings with 2 pieces of cellotape, one on top, one on the bottom. This helps to make a good surface for the next layer, and in particular prevent that the windings of the new layer fall into the imperfections of the previous layer. Go on till you have four layers.
When all 4 layers are done, cut off the wire, leaving a few cm sticking out, fix that with cellotape as well. If you are happy with the shape, you can fix the windings by applying a layer of transparent nail polish. Let it dry and remove the coil from the tube. This may take some force! Remove the inner piece of paper. The coil now moves much easier on the tube
Step 4: Putting Connectors on the Coil
You could solder the LEDs directly to the coil, but having some connectors allow many more experimentation: different LEDs, scope traces, or even use the coils for accelerating magnets or iron projectiles.
Start removing the insulator from the final ~1cm of the wire ends. I did this with a mini file, but sandpaper or a sharp knife will work too. Remove it well, otherwise you won’t be able to solder the connectors to the wires.
Cut two pieces of pins each from the pin header. To save space and improve the mechanical stability, bend the legs of the headers. Solder both pins to the end of the wires. Fix them in place with some glue, hot glue is the easiest.
Check the resistance. I had expected that the resistance be 9 Ohm per coil (16m x 0.55Ohm/m), but all 4 of my coils have 13 Ohms. I suspect that the coils are not pure copper.
Step 5: Putting in the LEDs and Trying It Out
Each coil gets two LEDs, since the current pulse produced is bipolar, so the brightest flash is obtained by using both polarities. Normally, LEDs need a series resistor when connected to a voltage source, because the current rises exponentially with the applied voltage, once you are over threshold. The induction voltage may reach 5V indeed, but they are very short. Moreover, the coil has some intrinsic resistance, so there seems no need to use a series resistor. Anyway, the LEDs are easy to replace. Regular 5mm are suitable, although their light is a bit too focussed in my opinion, and the visibility depends on the viewing direction.
I choose red and green LEDs. They are both very bright, but the red LED already lights up at 2V, while the green LED needs 3V. When the magnet moves slowly, you can sometimes see the red LED light up and the green LED not.
For better mechanical stability, cut the leads of the LEDs to ~1.5cm and bend them a bit to match to connectors. Connect the LEDs with opposite polarities so that a flash will be produced both when the magnet gets in as when it gets out. Distribute the coils over the tube. I put little markers on the tube every 10cm, so it’s easy to distribute the coils with even spacing.
Drop the magnet and see the LEDs light up. The more coils you have, the cooler it looks. Make sure to either catch the magnet by had or let it land on a soft surface. Apparently magnets can lose their magnetisation from mechanic shocks.
Step 6: Make a 4-tube Wall Mount
An interesting way to store the tube is to attach them on the wall with clips from whihch thay can be easily removed to be taken to a classroom or to play with it more freely. Moreover, copper and aluminium tubes come in the same 16 mm size, so you can have all 3 tubes next to each other to compare. I made a wall mount for 4 tubes, for a possible 4th tube in the future.
Snap-on clips for PVC pipes are sold ~10cents a piece at hardware stores. I first screwed four of them on a piece of wood, be the iron screw would attract and block the magnet! So either use non-magnetic screws (e.g. aluminium) or glue them. I found hot glue was strong enough. The blocks with clips can then be attached to a wall with double-sided tape.
Step 7: Bonus: a Cool Visual Effect
Check the above video: it's the magnet falling through a copper pipe, seen from above
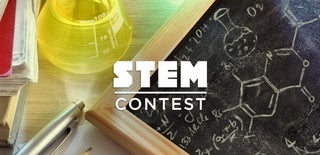
Second Prize in the
STEM Contest