Introduction: Inexpensive Digital Torque Wrench
This short Instructable describes a torque wrench design which is simple to construct whilst being accurate and repeatable. It uses a Digital Luggage Scale both to act as a handle to apply the required force, and to display the resulting torque.
Here in Malaysia, the cost of the parts was less than 6 USD.
Step 1: Parts and Tools Used
Parts:
- 40kg Luggage Scale (link this linear style works well as it's easy to see the display whilst applying the torque)
- 1/2inch Wrench handle (link I used this 250mm T-type)
- 40mm M5 socket-head bolt plus nuts and washers (for securing the scale to the wrench handle)
- 25mm M6 socket-head bolt and washer (for securing 1/2inch socket drive to the wrench handle)
- (1/4inch Ratchet wrench - I had one available so decided to make a second smaller version of the torque wrench)
Tools:
- Drill press and vice
- Steel combination square and scriber (or any method to accurately measure and mark the wrench handles for drilling)
- M5 and M6 tap (I threaded the bar for fixing but this is not essential - see text)
Step 2: Checking Scale Accuracy
I bought a Luggage Scale from two different vendors, and planned to use the most accurate for the wrench. I suspended a large bucket from the scale and checked the display for each litre - 1kg - of water added, up to 20kg. Considering their cost, I was quite surprised to find both scales were accurate to within 3% of nominal, and some of this variation may have been in measuring the water volume.
Step 3: Modifying the Scale
After removing the two small screws on the back of the scale, I separated the front and back of the case. The white blob of epoxy secures the strain-gauge onto the simple load-cell. I removed the luggage strap by unscrewing it from the cell. It used a M4 thread and I decided to drill this out to provide a clearance hole for the stronger M5 bolt. I was careful to support the bottom of the cell in the drill-press vice to stop the cell flexing during drilling, and drilled slowly to prevent any overheating.
In normal use, the strain gauge is extended by the tension due to the weight of the luggage. However, in our application, we will be compressing the M5 bolt to provide the torque. Thus, the cell needs to be flipped over so that the strain gauge still extends in operation. After checking that pressure on the bolt produces a positive reading on the display, I re-assembled the case.
Step 4: Modifying the Wrench Handle
The T-type wrench handle allows a socket to move along and around the bar as required. For our application we need the socket to be fixed at 90 degrees, and, at a set distance from the applied force. I selected 200mm as a convenient distance. The steel balls, which act as stops at each end of the handle, are about 225mm apart.
I held the handle in the drill-press vice and removed one of the balls by drilling a 3mm hole behind the ball and tapping it out with a small screwdriver. As supplied, the 1/2inch socket driver has a 5mm hole in its top. I carefully lined this up with the hole in the handle - previously holding the steel ball - and drilled straight through the top of driver, the handle, and the bottom of the driver, with a 5.5mm drill. Once the thin plating on these cheap tools is breached, the steel drills quite easily. I then tapped the hole, M6, and secured the socket-driver to the handle with the hex bolt. Pinning and gluing would also work.
Using the combination square I accurately marked the handle 200mm from the centre of the square socket driver. It's important that the handle-force is applied at 90 degrees to the axis of any socket used with the wrench. Thus, I ensured that the handle was clamped with both the body of the driver, and the handle, horizontal, before spot drilling the hole for fixing the digital scale. I first used a 3mm drill and then a 4.2mm drill before tapping the hole, M5.
I screwed the scale into the wrench handle leaving about 3mm clearance, and locked it in position with a nut and washer. This completed the construction of the digital torque wrench.
Step 5: Converting Displayed Weight to Applied Torque (and Vice Versa)
The display on the Digital Luggage Scale can be set to indicate weight in kg or lbs. Actually in the S.I. system of measurement kg is a unit of mass. Weight is the force produced by a mass under gravitational acceleration and is measured in newtons. Thus, an indication of 1kg on the scale represents a force equivalent to (1kg x 9.81m/s/s) or 9.81N. This force applied a distance from an axis of rotation produces a moment or Torque in Nm equal to the force multiplied by the distance. Thus in our case, a force of 9.81N at 200mm produces a Torque = (9.81 x 0.2) = 1.962Nm.
Therefore, a display of R kg will represent an applied Torque = 1.962 x R Nm. Conversely, if we need a Torque of P Nm, we will need to apply a force to the scale handle, until the display shows P/1.962 kg
The Engineering ToolBox website has an excellent explanation of torque, together with examples and an interactive calculator link .
Step 6: Digital Torque Wrench 1/4inch Ratchet Version
This version for 1/4inch sockets required the drilling of a single 5mm hole in the wrench handle. Again care was taken to position the hole accurately with respect to the socket driver. In this case, I set the torque distance to 102mm. Since, from the discussion in Step 5:
Torque Nm = Display kg x 9.81 x 0.102 and thus
Conveniently, Torque Nm = Display kg with a conversion factor equal to 1.
Step 7: Using the Digital Torque Wrenches
The Luggage Scale is rated to 40kg which is equivalent to just under 80Nm torque using the 1/2inch wrench. However, a more reasonable maximum would be around 50Nm, limited by how much force can be imparted through the scale handle perpendicularly whilst supporting the wrench and socket against the item being torqued. Though not as robust as a commercial product, I've found the device very useful for those times when something better than 'just feel' is required for tightening. Recent examples: Bolts on daughter's road bike - 8Nm typical, Anchor bolts in a brick wall - 20Nm typical, and the water pump flange shown in the photograph. Servicing the pump gave me the original idea for the torque wrench when I cracked the phenol flange by over-tightening. I can now keep to the 12Nm spec!
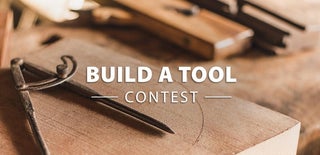
Participated in the
Build a Tool Contest