Introduction: Introduction: Oscillating Tool Saw Blade Sharpener.
About 12 years ago I purchased a Fein Oscillating tool.
A couple years later, disparaging at the price of their saw blades, I made a saw blade sharpener. Once set up, a $27 blade can be resharpened in five minutes.
This was too complicated a project to explain every step, so some of the critical steps and reasoning will be discussed. Questions from any body actually wanting to build such a thing are welcome and will be answered when found.
Step 1: Step 1: Designing
While sitting at church with my two daughters, I suddenly had an epiphany on how to resharpen the used saw blades for the tool. The first plan was drawn out with their crayons, each piece a differing color.
Since singularly the blades cost, (at the time), about twenty seven dollars each, and in a pack of ten about $150, It seemed prudent to me.
It had to make teeth in saw tooth fashion, adjusting sideways for each tooth, quickly, and repeatedly. Most of the material was already in the garage. Most of my inventions are of recycled material.
Step 2: Step 2: Collecting Stuff for Parts.
The work bench always has boxes and buckets of assorted salvaged items that seem valuable, stored beneath, beside, over, on the wall on shelves, basically too much stuff, but it always gets recycled to something.
- The adjustable slide is made of a car seat slide.
- The hack saw blade is a registration device to regulate the teeth being reground into the old blade.
- The altered strap hing has a sharpened, bent, edge that holds against the hack saw teeth.
- A 2" hole saw waste circle is used in two places as adjustable stops. The wing nut at left one, and tall handle on right one, loosen and allow circle to rotate eccentrically on a hole drilled between axis and outer edge. Sand paper had to be glued to the bottom of both eccentrics to prevent movement.
- Just about any old Dremmel type tool can be used to run the sharpening wheel. Drill holes for hose clamp to pass through base. Do not make hose clamp very tight to avoid distorting motor coils.
- The 3/4" plywood of the base is a special sign board type with an impregnated paper coating, very water resistant..
Step 3: Step 3: Collecting More Parts.
- Big "T" shaped knobs came off a Nordic Trac. Heads of carriage bolts are counter sunk a bit on bottom of swing arm, and knobs thread on them to hold blade still, which pivots on another bolt at the hole in the blade.
- The knob on the upward swing limiting eccentric was purchased at Rockler.
- There are a couple springs salvaged from god knows where.
Step 4: Step 4: Assembling.
Seat slide is bolted twice to blade holding arm, but only once at far left to base, so that the right side will pivot. A self locking nut was used to prevent loosening on the moving part.
Blade meets spinning tooth-cutting grinding wheel to remake teeth. This grinding wheel is specially shaped by engaging the side of it with a two inch diamond grit wheel while spinning. The engagement point on the grinding wheel can be adjusted with popsicle sticks hot glued to base along resting points of Dremmel type tool.
Step 5: Step 5: Bottom Side.
Spare strips of wood make feet, preventing bumps on bottom rocking tool.
Extra piece of ply hanging down at bottom of base hooks over edge of table/workbench, so pushing on the swing arm to engage wheel with piece being sharpened doesn't move tool on table. I do still "C" clamp the unit down.
Normally a foot operated switch is used to facilitate on/off.
Step 6: Step 6: Using
- Two big Nordic Track bolts are loosened, and blade to be sharpened is slid between two ply pieces, the hole in the blade going over a bolt just below.Then tighten the bolts.
- Loosen the wing nut on the left swing adjustment, (downward stop), and adjust the swing to make the edge of the dull blade about one fourth of an inch from the sharpening wheel.
The slide will have to be extended out enough that the blade edge will miss the cutting wheel, rising above the cutting edge of the wheel.
Loosen the tall nut, and adjust the up swing stop to allow just more than tooth height past engagement to the grinding wheel. Once that amount of swing is established, tighten the tall nut to hold the stop.
- Holding slide against spring tension to prevent slamming, lift hinge off blade, and allow next hack saw blade tooth to rest against hinge.
- Turn on Grinder, and gently engage swing arm up to grind new tooth. I have found it best to engage, and disengage, every half second or so.
- Once tooth is ground, advance to next place of grinding by again holding slide against spring tension, and lifting hinge arm off hacksaw blade, then advancing one tooth.
- Grind again. Gently, engaging and disengaging five or eight times until no more sparks are cast.
- Advance again.. 8 and 7, over and over until new teeth are all across blade. Be careful not to burn or blue the steel or you will remove all the temper from the teeth, making them soft.
- I do find that it helps to plug in the grinder before trying to engage for cutting.
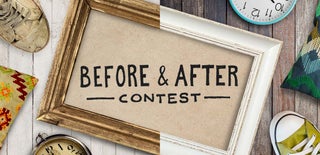
Participated in the
Before and After Contest 2017
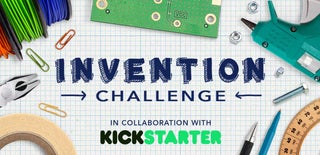
Participated in the
Invention Challenge 2017