Introduction: Jig for Safely Soldering Stone Set Jewelry
When you are working with stone set rings or other stone set jewelry, you run the risk of damaging or even shattering the stones. Most stones don't handle heat very well, even diamond or the premier colored precious family of stones (ruby, sapphire, emerald) can easily shatter or even outright burn ( diamond is after all, just compressed carbon just like the charcoal you burn in your Weber grill ) Opal or pearls are *especially* sensitive to heat having a large water content.
What this Instructable will show you is to build a jig to safely solder rings or other jewelry by submerging the stone(s) under cold water. The jig is very simple and cheap to make but may save you big money by protecting precious stones.
*NOTE* Use this jig at your own risk! Working on jewelry requires some skills and experience. Practice on "flea market" finds before you tackle setting the Hope Diamond! If you shatter a perfect 10 carat blood red diamond or other such bauble, it's on you. As in all aspects of life, nothing is guaranteed.
* Please consider voting for me in the jewelry category if this jig helps you out *
MATERIAL LIST:
Tuna can
5" of 14 gauge "dead soft" copper wire
Alligator clip
Machine screw (#6 X 1/2") with nut and lock washer
TOOL LIST:
Drill with 5/32" drill bit (could substitute punch or nail of proper size for machine screw)
Wire crimper
Wire cutting pliers
Screwdriver
Hammer
What this Instructable will show you is to build a jig to safely solder rings or other jewelry by submerging the stone(s) under cold water. The jig is very simple and cheap to make but may save you big money by protecting precious stones.
*NOTE* Use this jig at your own risk! Working on jewelry requires some skills and experience. Practice on "flea market" finds before you tackle setting the Hope Diamond! If you shatter a perfect 10 carat blood red diamond or other such bauble, it's on you. As in all aspects of life, nothing is guaranteed.
* Please consider voting for me in the jewelry category if this jig helps you out *
MATERIAL LIST:
Tuna can
5" of 14 gauge "dead soft" copper wire
Alligator clip
Machine screw (#6 X 1/2") with nut and lock washer
TOOL LIST:
Drill with 5/32" drill bit (could substitute punch or nail of proper size for machine screw)
Wire crimper
Wire cutting pliers
Screwdriver
Hammer
Step 1: Stone Set Rings
This is a typical stone set ring. The metal portion is 18K gold while the stone is a ruby surrounded by diamonds. While the metal is easily soldered, the stones will *NOT* like a torches heat at all! This ring is being soldered after being resized. A cut was taken out of the ring shank and the ends must be soldered.
Step 2: Eat the Tuna & Wash Out the Can!
Take your empty cleaned tuna can and either drill or punch a hole about 1/4" (6mm) down from the top edge. If you are using a #6 machine screw as in the material list, the hole size should be 5/32" . Just make sure the hole is large enough for the machine screw to fit through (duh!)
Note: You could try to build this jig without first eating the tuna but the fish will make using the jig quite difficult.
Step 3: Obtain the "dead Soft" Copper Wire Via "scrounging"
You can either buy a piece of soft copper wire at a hardware store or find a scrap piece of household Romex wire. You can find this stuff at most any building site and if you ask nicely can usually get a short scrap for free. (free is good) You can split the Romex jacket with a utility knife and pull out the non insulated ground wire. Of course the wire doesn't need to be 14 gauge, it could be heavier of lighter, but 14 gauge works best for me.
Note: the term "dead soft" just means the wire is not hardened and is easily bent. It does *not* require you to "kill it" or anything like that...
Step 4: Make the Copper Component
Take your copper wire and give it a single wind around your machine screw. Clip off the short "tail" where it crosses the loop. Lightly hammer the loop flat but don't over do it. Look at the picture for the proper amount. Lastly bend the wire to the approximate shape shown in picture #3. This is just a starting point, the shape will be fine tuned later.
Step 5: Wrangle That Alligator (clip)
Crimp the alligator clip on the non looped end of your wire. Crimping will assure that it will stay in place even when heated by your torch. The first one I built many years ago, I just soldered the clip on. Not a good idea. Experience is a cruel teacher.
Step 6: Screw It All
Insert the machine screw so the head is on the outside. Next, on the inside of the can, place the loop of the copper wire, followed by the lock washer and lastly the nut. Tighten securely. You want the copper wire "crushed" against the can with the lock washer keeping the nut from loosening. Don't go crazy with tightening, machine screws can be quite easily broken. Don't ask me how I know this.
Step 7: Almost Done Now... Check Your Work.
You should have something that looks like the picture. If it doesn't, consult the troubleshooting chart below:
TROUBLESHOOTING CHART:
If the wire goes the wrong direction, reverse the loop on the screw..
If the wire is not attached to the can, you forgot to put the copper loop on the bolt. Fix it.
If you can't see the can, turn on the lights.
Step 8: "Fine Tune" the Wire Shape
Bend your wire to position the alligator clip near the can's center as shown. Different jewelry jobs will require different arraingements. This is why the "dead soft" wire is specified. It is easily bent to whatever shape pops your cork.
This shape will do for this resoldering job on the ring shank.
Although it is not shown in this Instructable, I usually put a wrap of high temperature fiberglass tape around each alligator clip jaw. This will stop the jaws from scratching the ring shank.
Step 9: Using Your New Toy
Preposition the ring or other jewelry piece in the can. Line up everything so it is ready to solder. Next, pour cold water into the can until it is about 3/4 full. Now you can do the final positioning to place the stone and its setting under water to protect it from the torches heat. Just the portion of the metal to be soldered should protrude above the water's surface. The ring shown in this picture should be lowered another 3/8" (8mm) or so. The deeper the better.
Remember that it is *still* possible to overheat the ring's stone if you keep the torch on the metal too long! It should not take more than a few seconds to solder a well prepared joint. Do your prep work and you should have no problems.
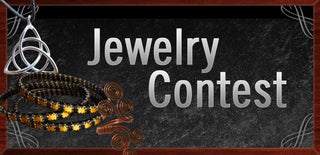
Participated in the
Jewelry Contest