Introduction: Junkyard C-Clamp to Expandable Clamp, Tool Box Treasure
Here is a very simple project to convert a basic "I" beam style C-Clamp into a heavy duty expandable clamp that is very useful.
Step 1: My Junkyard C-Clamp Story
So there I was... strolling through my local junk yard and there sticking out of the mud was an old 6" C-Clamp . I picked it up and took it with me unaware that it was inoperable and truly deserved to be there in the junk pile.
Upon getting it home I set it aside where it sat for a couple years in a forgotten box. Then one day when cleaning my shop I came across it, cleaned it up and was disappointed to see that I had a clamp that was damaged. it was twisted and had a torch cut across the anvil making it weak. Why had I saved this for all this time?
A moment of inspiration came to me, and I thought, "why not make this into an Expandable Range clamp?" after all, we never have enough long range clamps, right!? So here is how you can do the same!
Step 2: The Most Basic of Materials and Tools Are All That Are Needed!
Materials:
1 ea. Doner Clamp
1 ea. 1" x 2" x X", heavy walled steel box tubing, ( X= as long as you have use for)
2 ea. 1/4"-20 x 1.5" Hex Head Cap or Socket Head Cap Screws
2 ea. 1/4"-20 nuts
Basic tools are all that are required.
a drill motor
1/4" drill bit
4" grinder with metal cutoff wheel (or hacksaw and a file)
Optional Tools:
Welder (not required but may be preferred, the unit can be completely bolted together and no welding is required)
Drill press or Vertical Mill
Step 3: Cutting the Clamp and Tube to Length
Examine the clamp you have to use and decide where you can cut it to make one end fixed and the other movable. i chose to make the head end movable, but either one could be made to do the same. The anvil end will be fixed to the tube.
Depending on your material stock you may also need to cut the tube to your finished length. I personally used it as it was found, about 14" long.
Step 4: Slotting the Tube to Maintain Linearity of Adjustment
Take one of the clamp ends and position it on the tube end to see where the web of the "I" beam falls. They are not always centered inside the clamp and may be offset to one side or the other. If this is the case then the slot for it to ride in must also be offset. Pay close attention.
Once you know where the slot needs to be, mark it with a sharpie and using the grinder with cutoff blade long enough for each end to fit into and be able to travel as far as you desire the adjustment to be.
One suggestion on making this cut; do not start at an end, rather the middle of the tube and work toward an end. This is so the tube will remain intact (square) until the vary list bit and your cut will be true.
Step 5: Check the Fit
Do both ends fit into the tube and travel freely? If not, adjust the slot as necessary so the movable section moves freely.
Step 6: Time to Drill the Holes
Next mark your hole pattern onto the tube body spacing them so as to penetrate the clamp beam in the center web. The bolts will provide clamping force while allowing adjustment on the inside width of the finished clamp.
Center punch each point.
Insert the moving section on the clamp into the tube and position into the fully closed position (smallest clamping length).
Clamp the tube and clamp squarely to ensure all at straight before drilling.
Double check your measurements and everything is still square.
Drill the holes down the length of the tube, through the clamp beam and out the other side of the tube.
Step 7: Optional Step - Welding
I chose to weld my fixed clamp end into the tube. I had to weld up the damage to the clamp anyway (from the previous owner who burned thru it with a torch) and i wanted to add some webbing to the end to give it more lateral rigidity.
The end can be bolted in place even easier and work nearly as well.
Step 8: Pre-Paint Cleanup
Clean up the tube and clamp assembly to prepare it for paint. For me I used a soft wheel on my grinder and wiped down with Acetone. I didnt go crazy in making it look perfect as I intend to use this tool and it doesnt have to have perfect paint.
Step 9: Finished Product
So this is what I ended up with, a heavy duty clamp that goes from 0" to about 14.5". I am pleased with this and it will be a useful addition to my clamp collection.
If you enjoyed this build be sure to VOTE FOR ME in the TRASH FOR TREASURE CONTEST!
Thank you for viewing, and best wishes for all your projects!
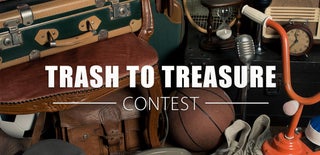
Participated in the
Trash to Treasure