Introduction: Koto's Mallet From Kyousougiga
Just like any proper nerd, I have my geeky passions. One of which is cosplay, a hobby in which people slave to bring our favorite fictional things to life. When I first saw a the hammer weapon in the show Kyousogiga, I knew I wanted to recreate it.
I had seen two people accomplish this feat before. The first example I had seen was using inflated vinyl like a blow up swimming pool. I liked the idea because of the light weight, but was unsure how to heat clamp the inside seam and make sure air did not escape. I couldn't find enough resources online for this process, so I nixed it.
The other hammer I had seen used a wire frame and a vinyl clear tablecloth wrapped around and a lot of clear tape. It was very sturdy, but ultimately I wanted to capture the glass like nature of the hammer and make it almost completely clear.
Both hammers had a clear pipe going through the middle so that was a must, but I had some prior knowdledge of acrylic and I was ready to take on the impossible.
You do not need acrylic knowledge to complete this, that's why I'm writing this for you all! If you are curious to learn more, fish tank are your best friend.
Now, let's get started!
Step 1: What You Need
For the inside of the hammer:
1. x6 (or more) styrofoam balls
2. Acrylic paints (pick your colors)
3. Fishing line
4. Hot glue
For the hammer body and caps:
1. 36"x72"x.093" sheet of clear acrylic
2. (x2) sheets of 20"x32"x.093" acrylic (Home Depot)
3. Epoxy (extra strong)
4. Acrylic glue and applicator (SCIGRIP 3 10799 Acrylic Solvent Cement, Low-VOC, Water-thin, 1/4 Pint Can with Screw-on Cap, Clear)
For the hammer form:
1. (x2) sheets of 4' x8' chipboard (Home Depot)
2. 2"x2"x8' wood (Home Depot)
3. Box of 100 drywall screws (you won't need them all)
For the hammer rod
1. 1.25" dowel rod
2. Banister topper (I found something like this at Home Depot)
3. Table leg (Home Depot)
4. Plastic clear pipe (the more rigid the better, I used plumping tubing) with an inner diameter of 1.25"
5. Semi gloss wood varnish
Tools:
1. Jigsaw
2. Hand drill
3. Dremel
4. Bandsaw
5. Heat gun
Step 2: Inside of the Hammer
With your Styrofoam balls, paint them the desired colors for your hammer. Koto's hammer has tons of different colors inside, so the color choice is really up to you! To paint the balls, I stuck toothpicks in the Styrofoam to not have to hold the ball while painting, and then stuck the toothpicks into cardboard for the balls to dry. I applied about two coats of paint until i couldn't see any white from the Styrofoam. Optional: I added some glitter to the balls because who doesn't love glitter?
Take the fishing line and measure out 50" pieces, I used about 5 and strung 1-2 balls on each strand of fishing line. Cut the fishing line where you want the ball to fall and hot glue the fishing line to the ball. If you have a small hole from the toothpicks in the Styrofoam, this is a great place to place the line to hot glue.
Set your caps up (see Step 3 for cap construction) 36" apart. If you can clamp them into something to hold them still, I highly recommend it. I clamped some L brackets to the table and wedged the caps in between them. Using a 1/16" drill bit, I drilled holes in each cap for the fishing line strands (if you use 5 strands, drill 5 holes on each cap). It is not essential for the holes to line up as the inside of Koto's hammer is already disorganized, so don't worry about lining things up perfectly!
Thread the fishing line through and tie knots on each end big enough to not slip through the hole you drilled. I found this to be the most seamless way to suspend the balls. Secure with an acrylic/plastic or hot glue.
You are now done with the inside of the hammer!
Step 3: Making the Caps
Using your two sheets of 20"x32"x.093" acrylic, measure out two equal circles of 19.1" diameter.
If you don't have a scribe this large, you can improvise and make your own. I used an improvised method and would not recommend it if you can avoid it. If you do have to improvise, make sure to measure your circles all the way around afterwards to confirm the diameter is close to even.
Later on when you attach the hammer body, the size of the caps and the evenness of the cut is going to make a huge difference as you will see later on.
Use a bandsaw to cut out the circles from the acrylic. If you do not have access to a bandsaw, you can also use a jig saw with a blade meant for cutting acrylic.
Sand down the edges so they are even and smooth. If you need to take out larger chunks because of a measuring mishap, I used a dremel with a metal brush attachment. If you use a dremel tip to remove plastic, chances are it will become coated in melted plastic, so be prepared to buy a new tip.
While cutting the caps, cut your 72" sheet of acrylic down to 60" for the 19.1" diameter we will be using. Feel free to adjust the measurements based on your own body size.
Step 4: Making the Form
Originally, I thought I could just bend my acrylic sheet into a cylinder without a mold. We tried once and realized it would be close to impossible to get an even heat or bend. As a side note, if you look into buying your acrylic cylinder, it would cost upwards of $500 and I certainly do not have that money lying around for a single cosplay prop.
I had originally seen this idea for a full "fishbone" mold online, but with my budget and tooling, I decided to make half of the mold. The acrylic would bend into the curvature of the wood and I would keep spinning the acrylic until it became a cylinder.
Using 3 of your sheets of chip, measure out *at least* 20"x12" squares. Using your scribe (or makeshift scribe), measure out at least 6 semi circles of diameter 19.1". Use a bandsaw or a jigsaw to cut out the chip board in the semi circle as shown in the pictures above. To test that your cut is correct, lay your caps inside the semi circle and see that they fit.
I did this all with a jigsaw in my apartment and as shown, it can leave a big mess. Our roomba had a nice meal that night, but make sure you have a vacuum handy.
While you're buying your chipboard, you might benefit from having the place you buy it from cut out (x2) 36"x12" strips. These will become the walls of your mold.
Cut your 2"x2" rod into 12 even rectangles at least 4" tall. Line them up at an even distance apart; a ruler and a T-square will be your best friends. If it's not exactly, it's not the end of the world but you'll have a less likely chance of a sink in your heat forming. From the chipboard into the wood, drill in two dry wall screws with your drill.
If you have trouble drilling the screws in, soap makes a great lubricant!
Take your semicircle fishbones and pick a side of the wood to place them on (one fishbone should be fish to the edge of the wall, and on the other side the wooden 2"x2" should be flush to the wall). Once again, from the chipboard to the wood, drill in two screws to secure the form in place. Start from the far back and move forward to avoid some tough drilling spots.
You can see the finished fishbone mold with the caps suspended above.
Step 5: Making the Hammer Body
Let me start off by saying, IF YOU HAVE ACCESS TO AN INDUSTRIAL OVEN PLEASE GO USE THAT.
I have done a bit of heat forming acrylic before and know the following:
1. Too much heat in one location will cause the acrylic to bubble
2. The thicker the acrylic is, the less likely it is to bend
3. Ovens are better than heat guns.
I tried an oven that is typically used for light fixture thermal testing, but it only got up to 32 degrees C, which is nothing compared to 121C (250F) I would need to even heat my acrylic to a solid point. So despite my knowledge, you do what ya gotta do and I broke out the heat gun. If you are using a heat gun and you have some friends who are willing to help, I highly suggest inviting them over, putting on a few movies, and taking turns blasting the acrylic with heat.
As shown above, I covered my form with a large sheet of fabric. This was so I didn't get any scratches or splinters in my acrylic, and I've always heard felt is a great material to heat form against.
Very slowly push run the heat gun up and down the acrylic exposed to the form and make your way across the length of the sheet. Once again, you will get better results going slowly than breezing through. And that's why you put movies on in the background!
*NOTE* Acrylic gets brittle as you heat form it and it cools again; as you throw the material out of balance with heat and changing shape (molecular arrangement), it's much more likely to break. We were using a metal rod to smooth out the curve of the acrylic in forming and ended up crackle the acrylic in half. This gave use two heat formed half cylinders. However because of the split, the edges with heat forming never quite lined up and the hammer did not make a perfect circle. This caused problems later on, but just know if your acrylic breaks, it does not mean you have to go buy a new sheet and start over!
After it was heat formed, we measured out two circles for the hammer rod at the middle/peak of each semi cylinder. Once again, be careful as the acrylic is brittle, and use a drill bit to make an initial hole. I then used a dremel with a grinder attachment to take away the rest of the material and make a larger circle. As I said, the plastic will melt all over the attachment tip, but it's the safest way (that I found) to make a whole 1 5/8" in the cylinder.
Step 6: Attaching the Hammer Body Together
Your mold isn't just for head forming! You can also use it to support your caps when gluing the hammer.
If you are willing to sacrifice some aesthetic for security, get or make some corner brackets about half an inch tall and drill and screw in 3-5 brackets around the edge of the cap. You won't be able to see these and pictures and they are nice security if the glue fails. Drill holes in the body of the acrylic and add a screw (head in the acrylic) into the acrylic/bracket as you begin the gluing process so you don't need to get into a sealed container later.
Using acrylic glue, glue the the bottom cap to the hammer. If you have never used acrylic glue, please do some reading on the glue before proceeding. Acrylic glue works as a chemical reaction and melts the two pieces of acrylic together. It has the same viscosity of water and will spill everywhere if you are not carefully, and it will destroy most things it touches. Wear latex gloves (and change latex gloves often), and pour the glue into the applicator bottle into an empty sink. Make sure you are working in a well ventilated area, and at the very least open your windows.
You might need to hold the body in place or apply some pressure to it while the acrylic glue sets. When you have a solid bond, VERY CAREFULLY flip the hammer over so the other cap is on the bottom. Just like with heat forming, if you can have a friend to help you with the process, it makes a world of difference. Glue the other cap on.
Now, if your heat forming job was even, you should be able to acrylic glue the seam together.
My heat forming job was not even, so i was able to put enough compression pressure on one seam to use acrylic glue, and I used globs of an extra strong epoxy on the other seam. If the epoxy smears anywehre, you will see it, so try to be as even as you can. If you need to fill a large hole, wait for it to get a little thicker before applying it. If you have any other gaps (like cap to body, as shown above), you can also use epoxy to fill in these holes.
You can see the difference between epoxy and acrylic glue seams in the pictures above.
Note: Acrylic glue can cause microfractures in the acrylic if it can't find anything to melt to. Therefore, if it "spills" down the acrylic at any time, you will notice these fractures. It's not bad for the hammer, and will not show up in pictures. You can also "burn" the acrylic with acrylic glue if you use too much of have part of your gloved hand in the glue as it dries.
Step 7: Making the Rod
Breathe easy, the hardest part is done!
Take your dowel rod and using clay, make bumps about a fists width apart going up the entire rod, leaving at least 7" from the top of the rod to the last bump. The rod in the hammer is bamboo, so the clay bumps are meant to emulate bamboo. You can start with wrapping a ring of clay around the wood and then using your thumbs to smooth the edges up and down, into the wood. If you need the clay to be smoother, dip your fingers in some water and continue smoothing it out. If you are using terracotta clay, it will stain your hands and your clothing orange.
While the clay is sitting to dry, take your table leg and banister heat and make any adjustments you want to their shape. I personally created a dip in the banister head using my dremel sander attachment and then a fine grain sandpaper to smooth it out. You will also want the table leg to come into close to the same diameter as your dowel rod.
Now it's time for arts and crafts! Paint the banister and table leg to a yellowish gold. I mixed a yellow paint with a fleck of brown. Now paint your dowel rod to look like bamboo. I painted a base layer of dark green, and then sponged on (using makeup sponges) lime green and brown. This gave it the streaky nature of bamboo. Leave about 5" of wood unpainted.
When the paint is dried, add a second layer of paint. Then take your wood varnish and over the course of a few days, add a few coats. I wanted my handle and head to be shinier than the rod, so I did about 4-5 coats on those as opposed to about 2 on the actual rod.
When everything is tried, take a dowel screw and attach the table leg (handle) to the end of the rod.
Now take your PVC pipe (cut to 24") and wedge the dowel rod into it the 5" you didnt paint. Using painters tape, paint the bottom 3" of the PVC/dowel the same gold color you painted the banister head. Add a coat of modpodge for shine and sealing.
When the paint is dry, stick the rod and pipe combo into the hole you drilled earlier in the hammer body. You should have ~2" of wood sticking out into the hammer. This is the bare minimum i would suggest if you want to be able to pick up your hammer. This thing is heavy and there is a lot of load bearing on the hammer/rod joint. I'm currently looking for a better way to do this, but a little wood shown is nothing that Photoshop can't fix. Use epoxy to secure the pipe into the holes. Also, use epoxy to add the banister head to the top of the hammer, covering the pipe hole. Let dry, and apply extra coats of epoxy as necessary.
Step 8: Have Fun
Here's a secret that I learned in this project: Cosplay isn't about perfection, it's about having fun and learning.
Of course it's frustrating to work on a project and run into road bumps along the way and think that nothing is turning out the way you envisioned it. But cosplayers don't get knocked down, we keep trying and maybe we even revisit the project years later.
Cosplay is for you and for no one else. I love being able to turn something from fiction into reality, so for whatever your reason is, do it for that and not for others. Also, you will learn the most by tackling large projects. Find something, set your sights, and just do it. Be prepared for failure, and be prepared to learn from that. I hope this instructable can help alleviate some of the potential failures in such a project!
This hammer was a lot for me to take on, and I would love to revisit it with new techniques later on. I talked to a bunch of people in the cosplay industry and I heard options like resin casting the hammer, or just using a different apparatus to heat form.
It should be noted that my hammer was not functional to walk around a con floor, instead I was about to get some nice pictures to prove my accomplishments.
If you are making this project, please start a few months before a convention because con crunch in a project that actually requires sit time in between is more stressful than its worth.
I'm incredibly proud of this hammer, and would love to know if other people have success too! If you have any questions about my construction process or want to suggest new methods of construction, leave a comment below and I'd be happy to chat and hear your ideas! Thanks for reading and best of luck with your project!
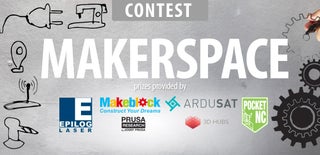
Participated in the
Makerspace Contest
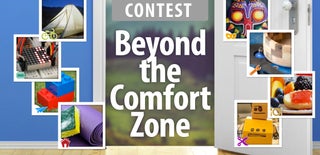
Participated in the
Beyond the Comfort Zone Contest
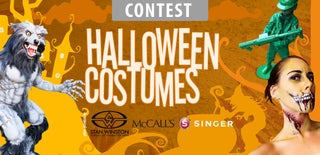
Participated in the
Halloween Costume Contest 2016
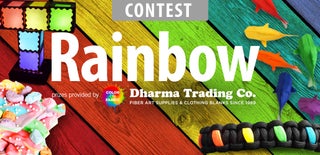
Participated in the
Rainbow Contest 2016