Introduction: LASER CUT LETTERPRESS TYPE
Here's a quick tutorial of sorts for anyone who has access to a laser cutter and wants to create their own letterpress wooden type.
Step 1: Cutting the Type
First of all don't do what I do every time I do type which is laser cut them print side up, in other words make sure the type is backwards. Otherwise you will find yourself cutting new letters again.
I used 6mm birch plywood specially made for laser cutting as the builders merchant stuff has different glue and is often warped. I used the typeface "Impact" which is system font on macs and some pc's. I suggest doing these all caps the first time as descenders (where a y or f go below or above the regular copy) are difficult to get straight.
I really suggest even on laser ply running this through a joiner or a wide sanding roller feed machine you need the type to be exactly the same depth on all letters otherwise you will not get an even print.
On our Denford laser you need to set the type to 6mm cutting depth on general hard wood and the cut lines should be 255 R value (RGB) at 0.01mm line thickness.
Step 2: Mounting the Type
Firstly again really important is to ensure you have the base mounting plate or wood sheet to be a standard thickness across the whole board so the type is on an even base.
Once you have done that plan up all your letters on the board so you have even spaces around each letter. Many printers will use spacers between each letter so I'd advise keeping them the same as you cannot guess space on what letter combinations will be used. These spacers are usually lead but I put some wood ones in too just in case.
Laser cut each rectangle make sure there is an even space from each base too, I'd advise using the laser line tool to etch where each letter goes as this will help when you are gluing up the type.
When each block is cut glue up each letter with a water resistant glue as the type will be washed if water based ink is used. I used Gorilla Glue.
Step 3: Creating a Presentation Box
Firstly I cut the lid slightly larger than the box I needed in case I needed to cut this down this was etched onto 9mm laser ply.
Using etch setting which is R-0, G-0, B-0 to make black I etched the title on the lid and one for the inner base in two styles. One was a line and one was an etch.
Step 4: Creating the Box
Now measure the inner base, the text blocks now glued up and the shelf (if applicable).
When you have this measurement ensure the sides of your box total more that all three.
Now cut all your pieces to length, I created a box jig for the chop saw as the pieces are so thin it has a tendency to cut unevenly or just make odd joints. This jig basically allows you to hold down the wood nearer the blade and keep it flat against the metal chop base and fence.
You'll then need to cut each corner as a miter and glue the sides up, I used a framing clamp which is good to keep things square.
This is where I used the inner base which was line cut rather than etched for the text.
Step 5: (Optional) Drop in a Shelf
One optional thing I forgot to photograph is to have this box with a split level to allow storage of more characters and spacers etc.
To do this buy the thin pre-cut molding from a DIY/home store and again cut this mitring the corners. This will allow you to drop a shelf in which I also laser cut just make sure there is a thumb hole to allow for the shelf to be removed easily!
Step 6: Creating the Lid and Finishing the Box
This is the not so easy bit. I bought these hinges which in hindsight were too large as and only fitted one way which for a box is not good as you need a barrel that can sit either side.
Anyway line up the lid and the box and mark the hinges. The easiest way I've found to install a hinge is to glue it in place with contact adhesive then drill and screw the hinges in. This was you won't accidentally install these incorrectly. When I did this the hinges stopped the lid shutting so I did some dremelling on the inside to create a rebate to receive the hinges, once I did this it shut fine.
One thing to do is to give the whole box BUT NOT the letters a stain and wax to bring out the etching and grain.
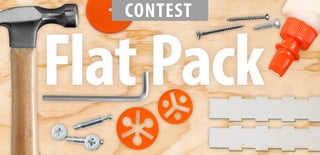
Participated in the
Flat Pack Contest