Introduction: LED Pixel Edge Lit Acrylic Sign
A simple project that demonstrates a simple way to make a customized edge lit acrylic sign. This sign utilizes addressable RGB-CW(red, green, blue, cool white) LED pixels that use the SK6812 chipset. The added white diode is not required, but does create a much nicer white color that really makes the etched/sandblasted areas pop. The sign uses 0.25" clear acrylic in the front and black 0.125" acrylic behind it on spacers. That creates depth and some shadows which add to the effect. Regular vinyl cut material was used as sandblasting mask and colored vinyl was placed onto the acrylic face for additional detail. A piece of aluminum u-channel extrusion holds the pixel strip, the controller, interface button, 18650 battery holder, and a SPST rocker switch for power. Standard 0.25" bolts and nuts are used to hold the two pieces of acrylic together and as spacers.
Updates and More Info Can Be Found On The Project Webpage: https://www.nledshop.com/projects/edgelitsign
Step 1: Supplies and Tools
Electronic Supplies:
- Addressable Pixel Strip - used 60/m SK6812 RGBW type. SK6812 does come in RGB types as well.
- Pixel Controller Ion or Pixel Controller Electron or pixel controller of your choice such as an Arduino
- Tactile momentary push button - included with NLED pixel controllers
- 22AWG wire - red and black for power - www.NLEDshop.com
- 4 conductor ribbon cable for pixel connection - www.NLEDshop.com
- SPST rocker switch, or other type of switch
- 18650 battery holder - BH-18650-PC is the pin type, wire tail type also available from Digikey
- 18650 protected lithium battery
Hardware:
- 0.25" thick clear acrylic, sized
- 0.125" black or colored acrylic, sized about 0.25" taller
- 4x 1" long 0.25" bolts, stainless steel
- 12x matching nuts, stainless steel
- 3/4" x 3/4" x 3/4" alumimum u-channel extrusion, same length as the acrylic. That is 8" for this project.
- Kapton tape for insulating
- Electrical tape for insulating
- Aluminum ducting tape - like tinfoil, for use as a reflector.
- Optional: Shapelock/Polymorph/InstaMorph plastic
Tools:
- Sandblast cabinet & media(never use actual sand)
- Vinyl cutter and vinyl material or cut mask - not all vinyl films will work for sandblasting, but most do.
- Drill and bits
- Saw to cut the extrusion
- Electronics tools
- Hot glue and gun
Software for NLED Controllers: Other controllers will require different applications.
- NLED Aurora Control - LED sequencing software, create custom color sequences for NLED controllers.
Step 2: Design and Layout
The idea with this project was to utilize a left over piece of 0.25" clear acrylic that already had four holes in it. An Adobe Illustrator file was created with the known dimensions and hole positions. It was decided the sign will be lit from the top rather than the bottom. The sign was to feature the NLED logo with mock northern lights along the top and some details to make it resemble a PCB. With a final layer of colored vinyl(used light blue / cyan) to add additional details and make some aspects stand out better.
Since this was going to be sandblasted using vinyl it has to be designed as clean vectors. Clean is referring to no double lines, overlaps, or anything that will mess up the vinyl cutting. Laser etching may not be as affected by overlapping vectors.
Not covering the graphic design just a few tips for vinyl cutting
- Use vectors with minimal points. If converting from a raster to a vector it can be very jagged with so many points a vinyl cutter will just chew/tear the edges. Use Object -> Path -> Simplify in Illustrator to minimize.
- After all the vectors are placed, select any that overlap and use Pathfinder -> Unite to merge them into one so there are no overlapping cuts.
- Bleed out the edges so the etched area extends past the edges, that makes it easier to place the vinyl down, which is never perfectly placed or straight.
- Vinyl graphics is an art not a science. It is difficult to impossible for 100% straight or perfect placement.
Attachments
Step 3: Acrylic Preparation
Front Acrylic:
- Was already cut and drilled, just needed to remove the protective film. Do that last to prevent scratches
- Fire polish the edges if required.
- Apply the sandblasting mask to the acrylic front. A hinge technique is helpful for better placement. Tape the acrylic down, without removing the mask's backing paper, align it to the acrylic, hold one edge down and flap the mask back and fourth, eyeballing and adjusting the placement.
- Sandblast the acrylic, using your method and media of choice. Never use actual sand.
- Check the etching is sufficient, it doesn't need to etch that deep, but needs to be even and consistent.
- Once it was good the vinyl mask was carefully removed.
- Cleaned the surface of any dust or grease.
- Applied the blue colored vinyl with the "NLED" and the website.
Rear Acrylic: Is optional but adds additional depth and effect.
- Found a scrap piece of 0.125" black acrylic, had a few scuffs but that won't be seen
- Cut it to the same size as the clear acrylic, except it is 0.5" taller on the top side. That allows the u-channel to slide up to that edge and leaves a 0.5" space between the clear acrylic and the pixel strip. Cut was done with a table saw and special radial blade for plastics.
- Marked and drilled four matching holes.
- Cleaned the surface since it was a scrap.
- Did a light over-spray of silver/mirror spray paint to give a star field effect.
Step 4: Electronics
Could be done many different ways.
Power: https://www.nledshop.com/projectguide/batteries/
Chose to power the pixels directly from an 18650 without any boosting to 5 volts. The SK6812 and almost all other 5 volt chipsets do work fine with the lower voltages of a single lithium. Which range between 4.2v to 3v. Once the battery discharges below 3.3v the blue LEDs stop working. Essentially that reduces the amount of usable power from the battery, but still plenty of runtime for the 12 pixels in this sign. Battery can be removed for charging.
Electronics: This guide has much more information for LED projects https://www.nledshop.com/projectguide/
- Start with test fitting all the components into the u-channel extrusion.
- Clean and remove grease from the extrusion for better adhesion of the strip and any glue.
- Once placement is figured out, holes were drilled for the battery holder to pass wires through the extrusion.
- Two holes for 4n40 screws were drilled and tapped to mount the battery holder to the extrusion.
- Used hot glue and shapelock/instamorph plastic to mount the rocker switch to the battery holder.
- Applied kapton tape to either end of the pixel strip to prevent any shorts to the extrusion.
- Used the self adhesive of the pixel strip to affix the strip the the u-channel. It is positioned directly over the clear acrylic.
- Measured, cut, soldered, and shrink tubed the battery holder and switch wires and passed them through the holes in the extrusion. Careful the holes may have sharp edges, debur or insulate.
- Soldered the power wires to the pixel strip.
- Soldered the 4-wire(only use 3 wires) from the pixel strip to the controller. The length and positioning of the wire and controller was carefully considered.
- Positioned the controller so the USB port was accessible
- Soldered the tactile button onto the Pixel Controller Ion or Pixel Controller Electron, length of the wire was considered to prevent any extra slack.
- Wrapped the controller in e-tape, but should have used shrink tube.
- Tested the controller, power, and pixels. Make any corrections.
- Hot glued the tactile switch into place, it is accessible from the the end of the extrusion, same as the USB port.
Step 5: Assembly and Sequencing
Assembly:
- Applied a flap of aluminum duct tape to the clear acrylic on the inside, folding it in on itself so there is no sticky side exposed, and the top edge of the clear acrylic is not covered. This flap is a light reflector.
- Did a final clean of all surfaces.
- Used the 0.25" nuts and bolts to attach the clear and black acrylic together. Two nuts are spacers, one nut and lock washer on the backside to keep it together.
- Slide the u-channel and electronics assembly onto the top, ensure the flap bends inwards and doesn't touch the pixels.
- Power up and test.
Adding Color Sequences: Fairly simple to do with NLED Aurora Control. Or use the color sequencing software your device supports.
Find additional resources for using the NLED Aurora Control software on the webpage or on Youtube for tutorial videos.
- Start NLED Aurora software and connect to the controller over the USB port, listed as a COM or serial port.
- The controller's name and details will be populated to the Hardware Config tab. Adjust the configuration modules for your controller, pixels, and other settings. It is required to set the Pixel Chipset and the Color Order for your pixels. GRB is default for WS2812 and others, GRBW is required for SK6812.
- Optional: Load an example sequence file. On the Software Tab click the "Load Sequence File" button, navigate to the /saves folder. Select a sequence file to use or use as a template "electron-v2a-rgb-768-channels.txt" is default for the Pixel Controller Electron. Or "ion-v2a-rgb-510-channels.txt" is the default for the Pixel Controller Ion.
On the software tab set Default Channel Amount for the number of channels required for your pixels. For 12 RGBW pixels that is 48, for 12 RGB pixels it is 36.
- Go to the Graphic Layout or the Timeline tab and click the "Sequences" icon in the upper right corner.
- Create a new color sequence or select one to load and edit.
- Follow the software manual and the Youtube tutorial videos to edit and create your sequences.
note could add optional IR receiver, but not yet
Step 6: Completion
NLED controllers and software are in constantly improved and updated. Contact Us with any feature requests or bug reports.
Thanks for reading, please visit www.NLEDshop.com for Made In The USA LED Controllers and LED Products. Or find more projects that utilize NLED products on our Instructables Profile or the Projects Page on our website. For news, updates, and product listings please visit www.NLEDshop.com Please Contact Us with any questions, comments, or bug reports. NLED is available for embedded programming, firmware design, hardware design, LED projects, product design, and consultation. Please Contact Us to discuss your project.
Updates and More Info Can Be Found On The Project Webpage: https://www.nledshop.com/projects/edgelitsign
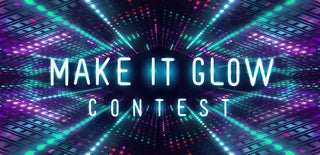
Participated in the
Make it Glow Contest 2018