Introduction: TV Backlight RGB LED Panel Conversion
An attempt to reuse a broken LED backlit LCD television for use as an RGB LED panel. A LCD TV was disassembled, the white LEDs removed, and regular 12 volt RGB LED strip was installed in rows. All the LED strip rows are connected together into a single RGB color channel. Any number of constant voltage LED controllers could be utilized, but a NLED 16-Bit RGBW Lamp Controller with infrared remote control support was used here. The TV's plastic frame was either broken or discarded so a new decorative one was made out of scrap polystyrene.
Check out the LED Project Design Guide by NLED for info on designing LED based projects.
Updates and More Info Can Be Found On The Project Webpage: https://www.nledshop.com/projects/tvbacklightpanel
Step 1: Tools and Supplies
Supplies:
- LCD TV with LED backlight, any size, for tear down - used a 16:9 xx"
- 12 volt RGB LED Strips - 30 or 60 per meter - used 30/m, did not want it very bright.
- LED Controller - Used a NLED 16-Bit RGBW Lamp Controller - or other constant voltage LED strip controller
- Power Supply - 12 Volt @ approx. 2 Amps
- DC Barrel Receptacle - 2.1mm x 5.5mm
- Shrink Tube / Electrical Tape
- Optional: Infrared receiver and hardware. For the NLED controller does not have native I.R. remote input and requires an add on card. Device Webpage - Github Project
Tools:
- Screw Drivers
- Pliers & Wire Cutters
- Electronics Tools - Soldering Iron, Solder, etc
Frame Supplies(All reused, not easily recreated):
- Circle high impact polystyrene scraps
- Solvent based glue for polystyrene - Testors
- Spray paint, 8 colors.
Step 2: TV Teardown
LCD TV: CAUTION THE POWER SUPPLY CAN STILL CONTAIN A DANGEROUS VOLTAGES
- Broken ones can be found in the trash or from friends and family.
- First consider repairing the T.V. before making it into waste. Many TVs can be repaired by replacing bad capacitors or sourcing new sub-boards from places like eBay or ShopJimmy.
- If the TV is less than about 2" thick, it is not the type that will work for this. Some TVs have plastic panels for the backlight, some have a white reflective interior space, which is required for this project.
- Only use TVs with LED backlights. Older TVs may use fluorescent bulbs containing mercury. If you are unsure, do not disassemble the TV and dispose of it properly.
Teardown: Lots of information out there on this, will keep it simple.
- Disconnect any cables, preferably let it sit for a few days to discharge the power supply.
- Remove any screws that would appear to be holding the plastic cover on.
- Carefully remove the plastic, most of the time by prying it gently. Spudgers can be used to pry without damage to the plastic.
- Ensure the power supply is fully discharged before handling or touching.
- Remove all the control boards and sub-boards(these could be harvested for reuse, if they still work). Dispose of electrical components properly, most can be recycled.
- Keep removing parts until the front diffuser assembly can be removed.
- Remove the front diffuser sheets, keep them stacked and prevent dust or debris from getting between the layers. Set them aside.
- Now you should have access to the white plastic reflector.
- Remove any more components that will get in the way of the strips.
Step 3: LED Strip Installation
Strip Layout:
- Measured the width and height of the area where the LED strips will be placed.
- Estimated how many strips or rows to use. Utilized CAD software to calculate the row spacing.
- Printed the row spacing onto some paper.
- Cut the LED strip to length. This project used 8 rows of 7 sections, which is 21x LEDs.
- Using 4-conductor, 22AWG ribbon cable, the strips were connected together back into a single strand. The ribbon cable was long enough to allow each row to reach the next row.
- Carefully used hot glue to secure the ribbon cables to the strips, to provide insulation, and to provide some strain relief.
- Two halves of the strand are connected together using the regular 4-pin header connectors that most LED strip comes with. Each half can be tested individually that way. Easier to troubleshoot if required.
Power Wire:
- One end of the strip will connect to the controller to recieve power.
- The far end has a 22AWG wire connected from the +12v of the strip that will also connect to the controller. Considered 'power injection', and is required for consistent colors along the strand.
Step 4: Controller, Power Supply, & Wiring
There are many options for constant voltage LED controllers out there. Most any controller for LED strip will probably work, such as the many options on Amazon.
Controller: Used here is a NLED 16-Bit RGBW Lamp Controller
- Find a location it will fit and consider any additional components that may be required. Such as the I.R. receiver, power supply connector, and any other user interfaces.
- There was not enough room for the controller, so the electrolytic capacitor was removed to reduce the height. Another similar capacitor was added on and laid flat.
- A location was found the the IR receiver, and it was wired on with a 4-pin dupont jumper wire.
- A hole was drilled in the frame so the IR receiver could be mounted. It may have been a better idea to put the IR receiver inside the LED panel, rather than drill a hole.
Power Input: Also many options, used here is a standard panel mount DC barrel jack.
- Find the best location, usually at the bottom or the side.
- For panel mount jacks, drill a hole the correct size.
- Prepare the DC jack, used 22AWG black and red wire, and shrink tube.
Power Supply:
- Used 56 sections(of 3 series LEDs each) of 12 volt RGB LED strip. Each section draws a max of 60mA when set to full white. That makes the max current usage 3.36A, at 12 volts that is about 40 watts.
- https://www.nledshop.com/projectguide/powersupplies/
Step 5: Optional: Decorative Frame
This was a solution to not having the original TVs plastic frame, it was tossed out or not suitable. Did it quick and easy, but turned out well.
Frame:
- Used scrap cut outs of high impact polystyrene, they were cut round about 9" diameter.
- Cut each circle into two.
- Used an acrylic/heat bender with a stop block to bend the parts 90 degrees.
- Played with the placement on the backlight. Overlapping all the way around, had to cut some in half the ends.
- Used Testor's plastic cement(red tube) and glued up the pieces as best as possible. They didn't lay flat.
- Clamped it to the backlight frame so it was the correct size.
- Once that dried, flipped it over and glued up loose areas and applied a lot of clamps.
- Painted it satin black using high quality Krylon Dual Superbond spray paint. It sticks better to plastics than other brands.
- Before the black was completely dry, used 8 colors of spray paint to create a rainbow effect. Applied an over-spray so the black was still the primary color.
Step 6: Color Sequencing & Control
Color Sequences:
This device is expected to run stand-alone color sequences. NLED controllers are compatible with the NLED Aurora Control Software. NLED controllers come loaded with numerous color sequence presets.
Most NLED Controllers are compatible with the NLED Aurora Control software. The software is used to create a multitude of patterns and sequences on a computer then, upload them to the compatible controller for the device to run by itself, without a computer connection. The simple GUI makes it easy for anyone to create custom color sequences of any sort and upload them to the controller over the USB connection. Great for any LED project that requires custom color sequences. In addition to standalone sequences, it also supports USB Live Control, send packets over USB to the device for direct control of the outputs. It supports single color, RGB, or RGBW LED configurations.
Control:
- Utilizes a custom 24-key IR remote. It is a standard Chinese one with a custom printed decal.
- Also could have installed the button or rotary encoder that is standard with the NLED 16-Bit RGBW Lamp Controller
Configurations:
- These define the hardware functions of the LED controller. Things like PWM mode, IR mode, DMX, etc.
Step 7: Finished
NLED controllers and software are in constantly improved and updated. Contact Us with any feature requests or bug reports.
Thanks for reading, please visit www.NLEDshop.com for Made In The USA LED Controllers and LED Products.
Or find more projects that utilize NLED products on our Instructables Profile or the Projects Page on our website.
For news, updates, and product listings please visit www.NLEDshop.com
Please Contact Us with any questions, comments, or bug reports. NLED is available for embedded programming, firmware design, hardware design, LED projects, product design, and consultation. Please Contact Us to discuss your project.
Updates and More Info Can Be Found On The Project Webpage: https://www.nledshop.com/projects/tvbacklightpanel
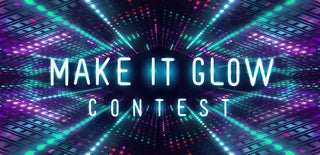
Participated in the
Make it Glow Contest 2018