Introduction: LED Spotlight Conversion
I was browsing through the local thrift store and came across one of those 1 million candlepower handheld spotlights. I always wanted one, however it didn't work, but was otherwise undamaged so I still grabbed it for a future project. I think I paid maybe $4 since I left got some other things from there too.
Fast-forward 6 months later. I had some spare parts lying around from a project I abandoned so I put them to good use and decided to do an incandescent to LED conversion.
I will be converting the light and power source from an incandescent lamp and a lead acid rechargeable battery to a high power LED and lithium ion batteries. This presented some pretty difficult design hurdles to overcome that I didn't expect, but it made for a great project to share.
Supplies
For the supplies and tools, you need:
A "host" or the spotlight you want to modify. You want to choose it carefully since it will determine how much customizing you'll ultimately be doing. Size is also important. It needs to be able to hold everything!
Batteries. You can use whatever type and size you want, nickle cadmium, nickle metal hydride, or lithium ion/polymer. I chose Samsung INR18650 25RM lithium ion batteries because of the capacity and current-handling capabilities. The driver I'm using requires high current from the batteries, up to 8 amps. You can use as many cells as you need depending on your driver choice and its input voltage requirements.
LED driver. This is critical since you need to control the LED's brightness and current. I'm using a 22 mm diameter generic Chinese buck driver designed for a flashlight. Your driver choice depends on the LED you're using and how much power you want to run through it. Note that a higher power driver requires high power from your batteries.
For the LED I went with the Cree XHP 70.2. You can use any LED you want, from a small 1 watt to a crazy 100 watt one, or even multiple LED's. Keep in mind, the more power, the more complicated your project will get since you need to feed and cool that powerful LED.
Heat sink and fan (optional) for cooling the LED and driver. These are also critical pieces since at high power the emitter and driver generates lots of heat. You can use passive or active cooling (no fan, or with a fan). A passive cooler will be bigger than a fan-cooled one and have shorter run times in between step downs or cool downs. I am using one with a fan.
Auxiliary reflector (I had to add it later on). This was from another host I had
Heat shrink tubing of various sizes. I mainly used 2 mm and 4mm.
Digital multimeter for measuring and checking voltages. Nothing really fancy is needed for this
Sheet metal, 16 gauge is fine, 1.5 to 1.8 mm thick is fine. You can use top cases for hard drives, CD drives, etc. This is for modifying the reflector to take the LED.
22 and 18 gauge silicone wires, 2 feet each red/ black. Find it at your local hobby shop, but Amazon, eBay or Aliexpress are significantly cheaper
Battery balance/protection board. Get these from eBay or Aliexpress for cheap
Nickle battery tabs/strips for making the battery pack from eBay, Amazon, or Aliexpress. Make sure they are pure nickle, not nickle plated steel.
Dean's T connector or other connectors for the battery and fan if using one eBay or Amazon or Aliexpress
3S balance connectors, male and female from eBay or Aliexpress
.25 in. aluminum couplers and appropriate screws or other standoffs. I got mine from the hardware store in the screws and bolts section
.45 mm copper sheet for making the driver holder. You can get this from old computer heatsinks for laptops or from the plumbing section. It's possible to cut pieces of copper pipe and beat it flat and solder it together.
Adhesive or Velcro. Can be hot glue too. I used Velcro for securing my battery and JB Weld and cyanoacrylate (super glue) for bonding other items
Plastic standoffs for mounting the reflector and fan. Scavenged from broken electronics and toy, they are basically round plastic rods with holes drilled on either end for running screws into. They hold case halves or covers in place.
Tools:
Dremel tool with cutoff wheel, grinding and sanding disks or stones, and high-speed steel cutters
Hobby or razor knife
Screwdrivers
Needle or fine detail files
40-60 watt soldering iron or station. I have one I bought a Quicko T12 942 off Aliexpress that takes Hakko T12 tips. Runs at up to 70 watts depending on the power supply.
Lead-based solder. I use Kester 44 63sn/37pb .31 mm diameter
Drill
Balance charger for lithium batteries
Drill bits. I used 8 mm, 2 mm, 2.5 mm, and 6 mm sizes. I also used a 1/2 inch size.
Belt grinder (optional)
Hot glue gun (optional)
This is just my list of tools and materials. Yours might be different, but this is what I used to finish the project. I'd have loved to have a lathe or a milling machine as it would have made this go much faster.
Step 1: The Host
The spotlight I chose is a 1 million candlepower with a pistol grip. The light source is an automotive type H3 35 watt halogen lamp. It had a wide shallow reflector made from thin steel to handle the heat produced by the incandescent lamp. The power source is a 6 volt sealed lead acid battery. It was trashed and all the electrolyte had dried up. The battery was charged by an external wall charger and all the power and charging regulation is based on a resistor array. There's no low voltage shut down or protection, and this is very hard on the lead acid battery because the battery is constantly deep-cycled, deep discharged and then fully charged, or topped off if partially discharged. The charger plugs into the back of the housing through a 5.5 mm by 2.1 mm barrel Jack. I'll reuse this part.
This housing was great for the conversion since it's easy to disassemble and reassemble without breaking things. Plus I like the cool camo paint. There's adequate room inside for all the conversion parts. Plus the housing is made from very tough ABS plastic. The reflector is held on by the housing and captured when the halves are screwed together with no mounting posts or screws.
There was a couple repairs I had to make. One of the screw posts had decided to shear off and prevent the screw from seating and closing the housing. I glued it on using my super strong instant super glue epoxy (more on that later). The case was also slightly melted so I had to bend it back. The bezel was also missing. Overall, it seems doable so let's get to it!
The only other modifications were removing some inner tabs to make room for the battery and cutting an opening for the balance socket.
Step 2: The Power
I'm using a 3S2P lithium ion battery pack made from 6 18650 batteries as the power source. I really like lithium batteries because they have higher voltage than nickle cadmium or nickle metal hydride (4.2 vs. 1.5 fully charged), can take lots of current, and have good capacity. The batteries I'm using are Samsung INR 1865025RM, 2500 mah capacity rated at a 20 amp CDR (continuous discharge rating). Since I have 3 in series for 12.6 volts and 2 in parallel, this gives 5000 mah, which should power the light at max power for 45 or 50 minutes. This is more than enough for my purposes. Also, the current handling capabilities are doubled.
You don't need to use a series-parallel configuration. You could do series, or run them in parallel if using a boost driver. I'm using the series-parallel because my driver is a "buck" driver and the battery voltage must be higher than the output voltage. In this case it's 12.6 volts being reduced to roughly 6.5 volts
I made an Instructable on how to build this type of battery pack, so check that one or four more information. Start by building your pack according to your host dimensions. I had to get creative with arranging mine to get it to fit properly. I connected the cells together by soldering, which is not the recommended way, but I didn't have a spot welder. This is why a 40-60 watt iron and good quality lead based solder is essential since a lower power one won't get hot enough to properly solder the cells and you'll apply too much heat trying to get the solder to melt. This is dangerous and can ruin your batteries or even worse, cause them to overheat and vent. Use the biggest chisel tip your iron can take and crank the heat up. Don't hold the iron on the cells for longer than or takes for the solder to flow. Use pure nickle strips for this since the current from the battery will be up to 10 amps when the voltage gets low and it's run on max output. Steel strips have higher resistance.
The photos show the initial design of the battery that used 16 gauge wires to connect the series/parallel cells, but I removed those for the final version and used nickle strips in their place since they lay flat and don't stick out.
Once your battery is together and you check the connections, you're either done if using a single cell or multiple in parallel, or in my case, need to add the battery management system or board (BMS). This is critical in series connections since you need each cell to charge and discharge evenly, and also to monitor the individual cells for low voltage. If you don't use a BMS, then you won't get optimal performance from your batteries and could end up damaging them from over discharging or overcharging.
I also added the balance connector lead which is necessary for charging the cells properly with a balance charger. I highly recommend using a balance charger for li-ion batteries since it will hemp them last a long time. I added input leads for the charging socket and output that run to the driver board. I also added a lead and a 2.1mm JST connector for the cooling fan.
Last step was insulating the bare connections with electrical tape and heat shrink tubing, and wrapping it up in masking tape.
Step 3: The Light Engine
The "light engine" is the LED and driver package. Although you can run an LED without a driver, for the best results LEDs really need drivers. For flashlights, drivers add a user interface for controlling the output of the LED. Since you probably don't want your LED to run at full power all the time, you need a driver with a user interface with modes built i to control it.
For the LED I'm using a Cree XHP 70.2 emitter. It's the 5000k color temperature (neutral white). It's mounted on a 16 mm diameter direct thermal path circuit board on top of a 1.5 mm thick piece of copper. This is called the MCPCB or metal core printed circuit board. All LED's running over 350 to 400 miliamps will need one made of copper or aluminum. This one has a special base that allows all the heat from the LED to go directly to the heat sink. This is important to help the LED operate at maximum output and last a long time.
The forward voltage is 6.3 or so volts and Cree rates the drive current very conservatively at 5 amps (30-32 watts). This emitter will easily take 10-20 amps (12 volt/6 volt) with good cooling! My driver only runs it at 5 amps, around 32 watts. You can also run this LED on 12 volts with a different circuit board.
The driver I'm using is from Aliexpress, which is a great place for them. They can also be found elsewhere, but the price can go up quite a bit. I got mine for around $7 USD. It's pretty basic, 2-3 lithium ion cells in series input (8.4 to 12.6 volts) and 6.5 volts output (depending on the mode). The current is set to 5 amps on the output, but remember this is a non-linear driver and output does not vary based on battery levels! This means the draw from the battery will be high at 100% power, up to 8 amps when the voltage starts getting low! This is why we need high output batteries. It has 5 modes, low, medium high (100%), a SOS mode, and a strobe mode. It gets pretty hot at 100%, so you need to cool it.
Step 4: Mounting the Reflector and Base
Since the reflector for a LED and an incandescent (filament) or even an arc discharge light source are different, the original reflector had to be modified. LEDs and incandescent light sources project light differently from the source. The filament emits light in a 360 degree pattern whereas an LED emits light in a roughly 120 to 130 degree angle from center. LEDs usually sit at the back of a reflector sitting nearly flush, while incandescent lamps are positioned off the base of the reflector to better gather and focus the light.
Next, I added a spacing ring around the LED to add clearance for the wires to keep them from shorting out on the metal base of the reflector. I used a spacing ring from a computer hard drive as it was perfect for this height-wise, about 3.5 mm. I added thermal paste on the bottom of the ring and set it on the heat sink and JB welded it on. I wanted the base of the reflector to add some thermal mass, so I will put thermal compound on the top of the ring where it sits against the reflector base.
I had to make a 'base' since the incandescent reflector didn't have one. I used the top cover of a computer hard drive since it was thin, but not too thin, and easy to polish, which is important for good light dispersion and focusing. I cut it to shape with my Dremel tool's cutoff wheel (wear eye protection!). You can use tin snips, but that might bend the part and make it unusable. The reflector has to sit nearly perfectly flat against it.
I will polish the base later once all the fit up is done. This is where a belt grinder and a Dremel are super helpful. If you don't have these, use fine grit sandpaper meant for metal.
I started grinding the reflector which was made from thin sheet metal coated with a reflective layer then a layer of clear lacquer. The grinding process is really important for getting the focus right. It's the most tedious part of these conversions. Unfortunately, the reflector was too wide and too shallow to work with an LED so I had to improvise. I took the reflector from another host and ground the base down until I got a nice focus with a good hot spot and lots of spill. I really like the XHP 70.2 for that reason. With a good reflector you can get a lot of throw so the light goes really far and spill that lights up a large area. This reflector will sit inside the remains of the original and act like a housing. I ended up gluing the two together. The bond had to be really strong since it would support the weight of the entire assembly.
Next, I had to engineer a way to mount the reflector and base to the heat sink. It's important to make it easy to disassemble for maintenance or repair, so glue was out of the question. It took trial and error, but I found some .25 inch diameter aluminum cylinders that were threaded on the inside on both ends. They're couplers for threaded rods, but worked perfect for my solution. I ground them down to the correct height (about 5/8 inch) to space them off the heat sink to give clearance for the LED. The mounts were secured to the heat sink with JB Weld. I tried screwing them on, but that didn't work.
Once the base was mounted, I had to mount the reflector to the base. I used some plastic standoffs I salvaged from a laptop computer. These hold the laptop's case together. I had to grind them down to fit the contour of the reflector side and then glued them on. I used my superglue and baking soda cement for this since it instantly sets up and makes a rock-hard cement that's very strong. Just lay down a layer of superglue on the parts, press them in place, then sprinkle baking soda on the parts. The baking soda instantly soaks up the superglue and turns into a super-strong cement, like instant epoxy. Neat! It looked pretty rough and once I got the LED fired up, a lot of light is lost from the sides of the reflector, so I painted it with a couple coats of black paint.I also painted the remains of the outer reflector semi-gloss black.
Once the mounts were secured, I screwed the reflector to the base and tested the focus again. Once aligned, I taped it down and used a fine Sharpie to mark the position of the mounts and drilled holes in the base for mounting. You need to be really precise here or the focus will be off. I sometimes drill the holes larger than they should to give some room for adjustment.
The focus turned out okay! If you look at the finished reflector from the front, you can see the die of the LED.
Step 5: Mounting the LED, Driver, and Cooling Fan
The cooling solution consists of an Intel stock cooler and a 80 mm x 10 mm case fan. I'm using a cooler from an Intel Core i7-3770. I like it because it's not bulky, it's round, thin, and designed to handle 84 watts of power. It is more than enough to handle the LED and driver. I removed the fan by cutting the supports off. I also removed the mounting feet since I won't need them. I kept the original fan's bracket for later.
A thicker 20 or 25 mm fan was a no-go since I needed all the room I could get. The XHP 70.2 is pretty efficient in lumens per watt, but like all high power LEDs, it generates a lot of heat at high drive currents so good cooling is essential. I won't have any external vents for this host, so I over built the system.
First step was mounting the LED. I drilled 4 holes in the heat sink's top. Two for the wires for the LED to pass through from the driver, and two for threading in screws for mounting. I added thermal paste between the LED's copper circuit board (called an MCPCB) and the heat sink for better thermal conductivity between them. This is exactly like you'd do if changing the heat sink on your computer.I drilled two 2.5 mm holes for routing the wires from the driver to the LED, then two more for the mounting screws.
Since the driver is designed to work in a flashlight and needs good cooling, I couldn't just leave it hanging loosely. In a flashlight, the driver mounts to a "pill" which is a tube that's hollow with a shelf on top for the LED and an opening with an open shelf on the bottom for the driver to sit on. It threads into the flashlight body for cooling and the electrical contact for the battery negative. I had to construct a "pill" or holder for the driver that also acts as the battery negative (ground) contact. The center of the driver is the positive contact.
Building and engineering this was really time-consuming. I ended up using some 0.5 mm think copper sheets from an old laptop cooler, soldered two of them together and then bored a 22 mm hole in the middle. I soldered on a third, slightly larger piece with a slightly smaller hole that holds the driver in place. This took a lot of time, grinding with the Dremel and then hand filing to get the fit just right. It had to hold the driver very securely to keep it from falling out and maintain a good electrical connection.
The holder also has mounting tabs for the screws that secured it to the heat sink.I added thermal paste to the bottom of the driver holder for good thermal contact with the heat sink.
It wasn't a perfect solution with the best thermal path, but it works fine.
I used the original frame from the Intel fan to mount the case fan. The old stock frame mounts to the heat sink so I kept it since I wouldn't have to make a new mounting solution for it. Turned out, the diameter was about the same as the mounting hole pattern for the fan I was using. I did have to grind off some materials to get it to fight right. When grinding this type of plastic with a grinder, wear a mask and eye protection and do it outdoors if possible since it makes a really stinky smell and the dust from it goes everywhere. Probably not the best stuff to breathe in.
Last step was JB welding on 4 mounting posts made from plastic standoffs. I ran screws through them to secure the fan. It sits about 6-7 mm above the driver, so there's good airflow and room for the wires. The fan isn't the quietest thing around, but it's good enough.
Step 6: Connecting Everything and Testing
Time to fire up the soldering iron! The electrical connections were pretty straightforward. The momentary switch is really beefy and can handle 125 volts AC and 15 amps, so it wouldn't have any trouble with this setup. It's also an interesting switch to see in a flashlight design since it is an NO, NC, COM type. It can be used as an momentary switch (NO) or as an emergency shut off switch (NC normally closed) which is basically an interrupter, sort of like a manual relay or solenoid.
For the battery connections, I used 18 AWG wire and 22 AWG for everything else. I'm using the switch as a momentary switch. The negative output from the battery goes to the driver holder and the positive to the center of the driver where a spring normally goes. I put a Dean's T connector on the output for easy removal of the reflector assembly. I used heat shrink tubing to cover all of the bare wire connections to prevent shorts in the cramped insides of the host. The test of the LED, fan and driver were just fine! I had previously tested it when doing the focus, so I knew it worked.
The leads from The charging plug ran to the battery positive and negative output side of the BMS board.
Since I designed the battery to be integral to the flashlight, I mounted it with Velcro strips I hot glued to the rear of the host. I used the existing charging jack, but had cut cut an opening for the balance plug. The driver output goes to the LED.
I added a lead with a 2-pin JST HX connector for the fan input and output so I could easily remove it. The fan is powered from the battery output and it's activated when the switch is pressed. Since the fan is meant to run on 5 volts, I couldn't run it off the 12.6 volt battery without it over speeding and being noisy and possibly reducing it's lifespan. I added some series resistors to reduce the voltage to the fan and get it to spin slower.
The reflector assembly consists of the reflector, cooler with the fan, LED and driver. I kept it modular for easy servicing. It mounts inside slots in the front of the host and it secured when the two halves are screwed together.
To charge the battery, I kept the 5.5 mm x 2.1 mm charging jack and added an adapter to my balance charger. It's a clone of the SkyRC iMax B6. It works just fine and charges the battery and balances fine. I used a balance lead extension with two male ends to connect to the battery and the charger. I charge the battery at 1.5 to 2 amps which takes about 2 hours to charge.
Step 7: Final Assembly and Testing!
Once all the connections are made and everything jammed inside the host, it's time for testing! As you can see from the pictures, there's barely any room left inside, but it all fits and there's good enough room for air to circulate. I used Velcro to secure the battery to the host in case I ever need to remove it.
The light is very bright at full power. The driver has 5 programmed modes, low medium, high, SOS, and strobe. Pretty easy to use.
The spill is very wide. It lights up my entire dining and living room. and the light throws a good distance. Not as far as a smaller LEDs, but very good. It easily lights up a tree that's 300 meters away. Heat isn't a problem as the fan removes enough heat to keep it running cool at prolonged operation on high. The batteries will run down before it overheats. Run time is okay, about 60 minutes on highest setting and lots longer on low. The driver had low voltage protection where the output drops and then it shuts off when the battery reaches 9 volts. Lumen output is probably 4300 to 4500 lumens, about twice as bright as the original H3 automotive incandescent lamp and more efficiency per lumen. I am really pleased!
Step 8: Conclusion
I'm really thrilled with this project. Start to finish it took 2 months and probably 100-200 hours of work on the weekends. Total cost was around $60 USD. Comparatively, it's the most expensive project I've done so far, but if you compare this to similar lights of this type, the cost can be much higher when you include the batteries.
$25 for the batteries
$11 for the LED
$5 for the heat sink
$5 for the fan
Drivers were $18 (I bought three since I killed two in the process of figuring out the driver mounting)
$6 for the BMS board
Most of this I got from the USA, but some from China (LED, driver) since it's so much cheaper and easy to find.
The rest of the stuff I already had.
Overall, it's not pretty, a little bulky, but I'l take function over form any day. It's really bright, around 4500 lumens, has good run time, and is really practical. It's a huge upgrade over the old incandescent lamp and lead acid battery and made for a great experience! I learned a lot from this project and my next one will be even better.
Thanks for checking out my Instructable!
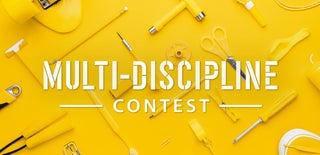
Participated in the
Multi-Discipline Contest