Introduction: LM3886 Power Amplifier, Dual or Bridge (improved)
A compact dual power (or bridge) amplifier is easy to build if you have some electronics experience. Only a few parts are required. Of course it is even easier to build a mono amp. The crucial issues are the power supply and the cooling.
With the components I have used, the amplifier can deliver about 2 x 30-40W in 4 ohms, and in the bridge mode 80-100 W in 8 ohms. The transformer current is the limiting factor.
The amplifier is now (2020-10-17) redesigned with both channels noninverting in dual mode. This also makes it possible to have high impedance input if required.
Step 1: Electronic Design
The story is this; In Sweden we have municipal garbage and reuse stations. This is where you leave all things you want to get rid of (not food waste). So in the container for electronics I found something that looked like a home built amplifier. I nicked it (because it is not allowed to take, only leave). When I got home I checked what it was and I found that the power amp IC was the really popular LM3875. I started to build my own guitar amplifier with it, but the legs of the IC were short and somewhat damaged, so in the end I had to give up. I tried to get a new one, but the only thing on sale was the successor, the LM3886. I bought two, and I started in earnest. The idea was to build a compact guitar power amp, using two LM3886:s, either for two channels or in a bridge circuit. In my own scrap heap I had a CPU heat sink and a PC-fan, so the idea was to use the heat sink and the fan to build an amplifier without any external heat sink.
Step 2: Electronic Design (power Amp)
The design of the power amp is really straight forward, and follows the datasheet example in the absolutely excellent application note AN-1192 from Texas Instruments, which should be your bible if you want to use the LM3886.
The upper circuit is the non-inverting amplifier with the gain of 1 + R2/R1. The lower amp is inverting with the gain of R2/R1 (where R2 is the feedback resistor). For a bridge design the trick is to get the resistor values so that both circuits have the same gain. Using mostly standard resistors (some metal film resistors) and measuring the exact resistance I was able to find combinations that worked. The non inverting circuit gain is 1+ 132,8/3,001 = 45,25 and the inverting gain is (132,8+3,046)/1,015 = 45,27. I introduced a gain switch (SW1) to be able to increase the gain. It reduces the R1 value to get four times higher gain.
Non-inverting circuit : 1,001 k in parallel with 3,001 k gives (1 * 3) / (1+3) = 0,751 ohm. Gain = 1+ 132,8/0,75=177,92 = 178
The inverting gain is 179,1 = 179 , acceptable!
The small (and free) application "Rescalc.exe" can help you with resistance calculations (serial and parallel)
I wanted to be able to use the two amplifiers separately so a switch (SW2) for switching between stereo and bridge was required.
The switch SW2 controls the dual/bridge mode. In "bridge" position the amplifier B is set to inverting, the positive input is grounded and the output of amp A replaces ground on output B.
In dual mode both amplifiers works in noniverting mode. SW1C lowers the gain so that amp A and B have equal gain.
The input tele jacks are connected so that when no plug is in jack A the signal is sent to both Amp A and Amp B (dual mono) .
In low gain mode 1,6 V peak to peak input voltgage gives max output (70 V pp), and 0.4 V is required in high gain mode.
Step 3: Electronic Design (Power Supply)
The power supply is a straight forward design with two large electrolytic condensers and two foil condensers and a bridge rectifier. The rectifier is the MB252 (200V /25A). It is mounted on the same heat sink as the power amps. Both the rectifier and the LN3686 are electrically isolated so no extra isolation is needed. The transformer is the 120VA 2x25V Toroid transformer from the amp that I found in the scrap heap. It can supply 2,4A which actually is a little low, but I can live with that.
In section 4.6 of AN-1192 the output power is given for different loads, supply voltages and configurations (single, parallel and bridge). The reason that I decided to implement the bridge design was mainly because I had a transformer that was not usable in a parallel design due to the low voltage. (The 100W parallel circuit requires 2x37V but the bridge design works with 2x25V).
The small application "PSU Designer II" from Duncan Amps is highly recommended if you want to make a serious calculation of transformer values.
Step 4: Electronic Design (Step Down Regulator and Fan Control)
The requirement of the fan at full speed is 12V 0,6A. The power supply provides 35V. I quickly found out that the standard voltage regulator 7812 will not work. The input voltage is too high and the power dissipation of (roughly) 20V 0,3A =6W requires a large heat sink. Therefore I designed a simple step down regulator with a 741 as the controller and PNP transistor BDT30C working as a switch, charging a 220uF capacitor to the voltage of 18V, which is a reasonable input for the 7812 regulator that provides power to the fan. I did not want to have the fan working on full speed when not needed, so I designed a variable duty cycle circuit (pulse width modulation) with a 555 timer IC. I used a 10k NTC resistor from a laptop battery pack to control the duty cycle of the 555 timer. It is mounted on the power IC heat sink.The 20k pot is used to adjust the low speed. The output of the 555 is inverted by the NPN transistor BC237 and becomes the control signal (PWM) to the fan. The duty cycle changes from 4,5% to 9% from cold to warm.
The BDT30 and the 7812 are mounted on a separate heatsink.
Note that in the drawing it says PTC instead of NTC (negative temperature coefficient) , in this case from 10k to 9,5k when I put my finger on it.
Step 5: The Heat Sink
The Power amps, the rectifier and the PTC-resistor are mounted on the copper plate of the heat sink. I drilled holes and made threads for the mounting screws using a thread tool. The small veroboard with the components for the power amp is mounted on top of the power amps to ensure as short cabling as possible. The connecting cables are the pink, brown, lilac and yellow cables. Power cables are of a higher gauge.
Note little metal stand by the red cable in the lower left corner. That is the single central ground point for the amplifier.
Step 6: Mechanical Construction 1
All major parts are mounted on the 8 mm plexiglass glass base. The reason is simply that I had it and I thought it would be nice to see the parts. It is also easy to make threads in the plastic for the mounting of the different components. The air intake is under the fan. The air is forced thru the CPU heat sink and out thru the slits under the heatsink. The slits in the middle was a mistake and are filled with plastic from a glue gun.
Step 7: Amplifier Without the Case
Step 8: Mechanical Construction 2
The front panel is made of two layers; a thin steel plate from a PC and a piece of mint green plastic that remained when I made a new pickguard for my Telecaster.
Step 9: Front Panel From the Inside
Step 10: Wooden Casing
The casing is made from alder wood from a tree that fell in a storm. I made some planks using a carpenter's plane, and glued them together to get the required width.
The cutouts in the casing is made with an electric wood router.
The sides, the top and the front are glued together, but I also secured the construction with screws thru the small pieces in the corners.
To be able to remove the wooden casing, the back side is separately held in place by two screws.
The grey plastic pieces have threads for the 4 millimeter screws for the bottom and the back.
The small grey piece in the corner is a little "wing" that locks the front panel so that it does not bend inwards when you plug in the tele jacks.
Step 11: The Backside of the Amplifier
On the back there is the mains inlet, the power switch and a (not used) connector for preamp power
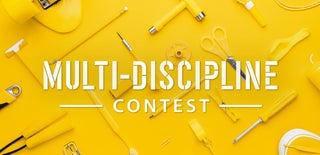
Participated in the
Multi-Discipline Contest