Introduction: Landing a Rocket Vertically, Without Being a Billionaire Aka Rocket Drone
This is my patent pending Rocket Drone.
Since SpaceX and Blue Origin achieved the vertical landing of their own rockets, to obtain the reusability of the Falcon 9 and the New Shepard, I've been fascinated (and obsessed at the same time), by these accomplishments. In short words, I've designed my own rocket (on a small budget) to have the same "fun", on a smaller scale!
Of course, propellers don't work in outer space.
Actually it would be better to say, not above the stratosphere. The maximum altitude reached by an aircraft with propellers is nearly 30,000 meters (moving forward). This altitude has been achieved by the prototype Helios, developed by NASA. In 1972 a Chopper helicopter reached the altitude of 40,000 ft.
Anyway, beyond the provocation of the title of this Instructable, and beyond the pure fun there is in launching and landing vertically the Rocket Drone, I've built it, mainly because I've noticed the drones on the market have a deployment/ascending speed pretty slow (the DJI products are between 4 to 6 meters per second). The Rocket Drone is nearly 3 times faster (12 meters per second), using compressed air and water and it can be even faster using a solid fuel motor (Estes Rockets). The unique feature of the shafts controlled remotely, allows the Rocket Drone to be deployed in a matter of seconds.
I've already created the 3D drawing of it, but (regrettably), I can't afford to buy a 3D printer, therefore all the parts of the Rocket Drone have been built from scratch (mostly using PET soda bottles).
The only parts 3D printed are the hinges (I spent 90£ to print them in nylon).
Having a proper budget this drone should be fully autonomous, using a Pixhawk controller that starts the engines as soon as a barometric sensor detects the apogee. Using a GPS the drone should stop in mid-air for a few seconds, to stabilize itself and using the precision landing IR-Locks and IR Beacons, plus my magnetic platform, should land autonomously.
I believe that a Rocket Drone built in that way could be used by the law enforcement and by militaries (patrol and reconnaissance).
Although I'm patenting the Rocket Drone, I'm open to a collaboration. I think that building a proper prototype and presenting the finished product on any crowdfunding platform, would raise the interest of a lot of funders.
Supplies
A large quadcopter:
Wltoys V262 (cheaper), or a V666 Quadcopter with 6 Axis Gyro.
You need to buy a battery which is light (42 grams) and at the same time powerful enough to withstand the weight of the Rocket Drone (420 grams). I chose a discharging rate of 70C.
https://www.banggood.com/ZOP-Power-7_4V-750mAh-2S-...
4x Permanent magnets 2cmx1cmx2mm (for the landing gear)
https://www.banggood.com/20pcs-N50-20x10x2mm-Neody...
1x 500g 0.1g LCD Electronic Digital Mini Pocket Scale
https://www.banggood.com/500g-0_1g-LCD-Electronic-...
8x Extension Springs: Diameter 0.5cm Length 0.8cm 14+2 Windings for the hooks (Hinges)
2x A4 Correx 4mm sheet black (Fins and pyro rocket motor mount)
2x PET 1.5Litre Soda Bottle
4x Zip ties
1x Lid of cotton buddies 6.8cm diameter (New Battery Holder)
1x Kitchen foil cardboard roll (pyro rocket motor mount)
2x Popsicle sticks (pyro rocket motor mount)
1x Ferromagnetic sheet 50cmx50cm (Landing Platform)
1x Polystyrene (57cmx57cmx4cm) the one used for the packaging of kitchen furniture - Landing Platform
2x Paper clips (Hinges)
1x Lid taken from the soap dispenser (the thread match perfectly the one of the soda bottle)
1x Male Gardena Connector (Water rocket module)
1x Estes Motor (D12-0 for Pyro Module)
2x Launch Lug - 3cm length clear PVC pipe - 6mm diameter
Electrical tape
Duct tape
Hot Glue
UHU POR (foam friendly)
CorrosionX (If you are going to use the water rocket module)
Painting (water based)
Please check for the upgrades I made to make the Rocket Drone more "flyable" (Step 12).
Step 1: Buy a Wltoys V262 (cheaper), or a V666 Quadcopter With 6 Axis Gyro
You can buy a large Wltoys V666 quadcopter here (On sale at just £34.99)...
Or you can go on Ebay and waiting for a good bargain (as I did), of models such as:
a Wltoys V262 (which is generally cheaper than the V666 quadcopter), equipped with 6 axis gyro.
I paid my V262 £30! Not bat, isn't it?
I watched a video on Youtube about how much weight the V262 can handle and, according to RavingMadProduction, the total weight AUW can be 430g (or even more), but the lighter the Rocket Drone will be, the better control you'll have on it.
Step 2: Printing 3D the Hinges
The video above is about the early development of the Rocket Drone. Even though the launch was successful, I want to underline that I've understood immediately the foldable shafts were indispensable, because:
1) They decrease the drag/load on motors and propellers. Using the water rocket module, at 74 psi of pressure, the force at the start of launch tube is 37 Newton. Therefore, the load on shafts is around 4Kg (Torque=ForcexDistance).
In short words, after a few launches (without using the folding shafts), it's inevitable to break the booms.
2) They allow the Rocket Drone to reach a higher altitude (aka straight ascending trajectory), because the rocket is well balanced, having the motors positioned at the CG (Centre of Gravity). A predictable (and straight) trajectory, means more safety during the launching and landing phase.
Therefore it was necessary to create the folding shafts, using some 3D printed hinges (initially designed 2D by me and put in 3D by a friend who is an expert in 3D drawing).
The file is available on MyMiniFactory.com...
https://www.myminifactory.com/object/3d-print-hing...
You need also 8x Extension Springs: Diameter 0.5cm Length 0.8cm 14+2 Windings for the hooks
Step 3: Fitting the Quadcopter Inside the Water Bottle.
As I mentioned before, even though I have "ready to print" in 3D all the parts of the Rocket Drone, I don't have the 3D printer, therefore I have been forced to use recycled parts (mostly PET 1.5 Litre soda bottles).
In fact, printing all the parts will cost me a fortune!!!
Anyway, let's start to attach the quadcopter. Basically, you need to cut 1 PET 1.5 Litre soda bottle in 2 parts.
Using 4 zip ties you will attach the support of the controller to the base of the plastic bottle, covering the pcb with the upper part the water bottle you have previously cut. You have also to cut the neck of the soda bottle, closing the hole with some duct tape and a tennis table ball, cut in half. In this way your Rocket Drone will have a proper nose cone. Cut also 4 x 5mm stripes, to slide the top of the bottle on the shafts of the drone.
Step 4: Cutting the Shafts
This operation requires a lot of patience and accuracy.
You should cut the carbon shaft (please use a protective mask and a wet cloth when you are doing this operation), at 11.2cm from the motors shafts.
Make a mark on the carbon shafts and, using a small hacksaw cut them, without cutting the 4 cables there are inside of it!
Shafts are squared and very thin. You should make small precise cuts on all the sides of it.
Ideally when the shaft is bent, the landing gear should touch the cylinder of the rocket, keeping an angle of 90 degrees.
Step 5: Fitting the Hinges
Again, this job requires a lot of patience.
You should remove the shafts from the quadcopter (take a picture to remember the exact position).
Remove from the controller the motor connectors and the LED connectors.
Using a file and some sand paper, make the surface of the 3D printed hinges smoother.
Using a small screwdriver, make the holes bigger enough to fit a small paper clip inside the hinge and cut it to the right size.
Once you have done that, start to open and close the hinges until the parts will be able to move freely, with no friction at all. Please note that this task is very tediuos.
Now slide the 2 parts of the carbon shaft inside the hinges, reattaching the arms to the controller.
The position of the hinges should be at 11.2cm from the motors Shafts and 6.3cm from the motors holders.
Ideally, when the shaft is bent, the landing gear should touch the cylinder of the rocket.
Anyway, at the end of this process, secure the top of the soda bottle to the lower part of it, using some duct tape.
Step 6: Making a New Battery Holder
The current battery of the V262 has a 25C rate which is not enough to decelerate the Rocket Drone during the descending phase.
You need to buy a battery which is light (42 grams) and at the same time powerful enough to withstand the weight of the Rocket Drone (420 grams). I chose a discharging rate of 70C.
https://www.banggood.com/ZOP-Power-7_4V-750mAh-2S-...
500g 0.1g LCD Electronic Digital Mini Pocket Scale
https://www.banggood.com/500g-0_1g-LCD-Electronic-...
Remove the old battery holder (using the screw) and fit the new one, which is made using a lid of the cotton buddies. With a height of 3.3cm and a weight of just 7.8 grams it's ideal to keep the new battery in place.
Also the diameter of this lid fits perfectly with the support of the controller.
You just need to cut the rectangle on one side, to slide the battery in.
The battery cover will be sandwiched between the drone and the soda bottle, using 4 zip ties.
I've also put some thin foam inside of the new battery holder. In this way the battery won't move during the flight.
Step 7: Making the Rocket Module (Water or Pyro? This Is the Question)
There are a lot of tutorials that explain how to build a water rocket, or a pyro one.
Air Command Water Rockets, US Water Rockets and The King of Random have published fantastic videos on Youtube. You basically need to build a "booster" (aka a rocket without the nose cone), that later is going to be connected to the drone part you have previously made.
The only thing you should consider is that if you want to swap the modules, you should have the same diameter/height. Initially, for my pyro rocket module I've used a cardboard/postal tube for the documents (diameter 79mm), but it was too heavy, therefore, I've swapped it with a PET soda bottle (diameter 80mm).
If you want to use a model rocket motor (Estes Rockets), you should design the fins in a way that are not going to get burnt during the exhaustion phase.
To make your life easier, you can use the 1st drawing (1st fin on the left), for both modules.
To be sure 100% the fins are not going to be melted, glue a small piece of silver foil to the part closer to the rocket motor.
Please be aware that a bigger area of the fins moves the CP (centre of pressure) toward the tail of the rocket.
Once you have built your water/pyro rocket, test it!
To do that, first secure the drone part to the rocket module (pyro/water), using some electrical tape.
Fold the arms and tie a string around the CG (centre of gravity). The CG should be at 27.5cm of height.
Clear the space around you (according to the length of the string) and very carefully start to spin the Rocket Drone.
If everything is ok, the Rocket Drone should fly straight (nose first). If this thing doesn't happen, you should create bigger fins to move the centre of pressure toward the tail. Ideally, the distance between CG and CP should be at least the diameter of the rocket itself.
Attach 4 permanent magnets 2cmx1cmx2mm at the base of the fins. This will keep the Rocket Drone still when it lands on the ferromagnetic platform.
Another important thing for your safety, test the rocket motor holder with a dumbbell that matches the amount of force exerted by the rocket engine.
In my case I'm going to have an initial impulse of 32 Newton, therefore I've decided to put a 3Kg dumbbell to test the solidity of my motor holder.
If you want to use the water rocket module, I would strongly recommend you to waterproof all the electronics of the quadcopter, using some CorrosionX.
You can also paint your rocket module, using your favourite colour.
Don't forget to add the launch lugs that allow you to slide the Rocket Drone into the rod, using 2x 3cm length clear PVC pipe - 6mm diameter.
Step 8: (Ferro) Magnetic Landing Platform / Barge
Of Course I Still Love You!
Ehm... don't get me wrong, but this is my favorite name for SpaceX ASDS (Autonomous Spaceport Drone Ship).
This one and the other one (aka Just Read the Instructions), have been named by Elon Musk after two of
the sentient, planet-sized Culture starships which first appear in Ian M. Banks' sci-fi novel "The Player of Games".
I decided to name mine "You Were Always On My Mind", as I've had this project in my head... for a while.
Anyway, the landing pad is a piece of squared (57cmx57cmx4cm) polystyrene, wrapped with duct tape.
In this way it's water resistant and it can even float as a barge!!!
I also glued a sheet 50cmx50cmx1mm of ferromagnetic material, on top of the polystyrene square.
It will work perfectly with the 4 permanent magnets attached to the fins of the Rocket Drone.
More instructions are available here...
Step 9: Have Fun, Stay Safe
Launch and land the Rocket Drone in "safe places", far from people, animals and properties.
If you are a beginner, to have a better orientation of the Rocket Drone after the launch, leave on the quadcopter the propellers with different colours (Red/Orange Forward and Black Backward).
For the launch pad, please take a look at my Instructables that shows how to build your own one, made of metal.
https://www.instructables.com/id/Pyro-Rocket-Metal...
Last but not least, I've made another tutorial that shows you how I've built a Rocket Launcher Controller.
https://www.instructables.com/id/Scracht-Built-Lau...
For this huge project, nearly everything has been built from scratch... more or less.
Step 10: Add-on Landing Gear SpaceX Falcon 9 Way Aka Something That Looks Like That ;-)
I thought it was really cool to add the landing gear to my Rocket Drone, but I don't have any gimbal that stabilizes the thruster (I use solid fuel motor), therefore I need to use the fins to have a predictable flight path. Basically I've been able to keep the fins (thinner this time), in the right place to have the right CP (centre of pressure). The descend of the landing gear gives a proper structure to the fins, creating a sort of stable tripod. In this way, I've decreased the total weight of 10 grams, adding a cool feature. That's why is called rocket science, you'll never stop to learn something new.
Step 11: Upgrading the Motors to Achieve a Better Thrust/Weight Ratio
Tired of replacing the motors after a few flights, (aka they have to work at full throttle to lift the 420 grams of the Rocket Drone), I've decided to upgrade them to increase the thrust.
After watching a video on YouTube, made by V262 Octaquad (who has replaced the V262 motors using the one installed on the MJX X101 Quadcopter), I found one on Ebay at just £19.99!!!
To remove the motor holders, I have done a-nearly-complete tear down of the quadcopter.
Regreattably, the carbon shafts/booms of the V262 are 4mmx5mm, while the ones installed on the X101 are 4mmx4mm, therefore using a 120 grits sand paper I've had to remove that millimeter.
(Please use a mask and a wet towel / kitchen paper, when you sand the carbon fiber shafts).
I've also replaced the Controller/Receiver, which in the X101 is positioned underneath the frame of the quadcopter, therefore it has to be mounted upside down on the support of the V262 Controller.
To do so, I've desoldered the motors cables from the motors and the LED cables from the PCB.
(If you prefer, you can keep one strip of LED, to see when the X101 quadcopter is bound).
Cut also the plastic frame around the controller of the X101 (please take a look at the picture).
In this way, using 2 zipties, I can attach it to the support of the V262 receiver (upside down), being sure that it has a bit of air to "breathe" (aka, the Mosfets become very warm during the flight) and that tightening the zipties to secure the X101 controller, I don't damage any electronic component. Last but not least, I've re-attached the cables to the motors.
Now, I have more power and I can afford to add a little bit of weight, therefore I've replaced the battery increasing its capacity to 1000 mAh.
ZOP Power 7.4V 1000mAh 70C Lipo Battery JST Plug https://www.banggood.com/ZOP-Power-7_4V-1000mAh-70...
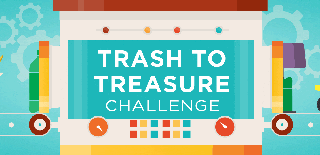
Participated in the
Trash to Treasure
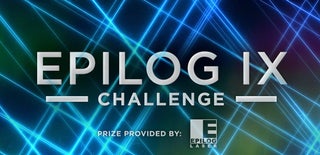
Participated in the
Epilog Challenge 9