Introduction: Laser Cut Propeller for RC Planes and Drones (5"x4")
You know those old-fashioned wooden propellers they used to use on planes?
How awsome would it be to have those powering your RC planes or drones!
In this instructable i will lead you to the production proces of just that; a 5x4 inch wooden propeller. The propeller is made by laser cutting various layers of thin aircraftplywood and glueing them together. This is a working propeller, in the video you can see it powering an RC plane!
All you need to make your own wooden propeller is:
a lasercutter
superglue (or woodglue)
sandpaper
drill and drilbit 3mm
Optional: lacquer
In the first 6 steps I will lead you through the proces of designing the propeller. If you just want to make the propeller I made, you can skip those steps and download the nesting in step 6.
Step 1: Making a 3D Computer Model
In this step I will guide you through the modeling proces of the 3D computer model of the propeller.
I modeled the 3D model in SolidWorks, but this can also be done in other 3D modeling programs. If you want to skip this step you can download the .stl file of the propeller on the end of this page.
I did not design the propeller from the ground up; I don't know enough about propeller desing to design a properly working one. Instead I used the GrabCAD model from Jon Snow and scaled it to the propper demensions. Full credits for this propeller model go to Jon Snow.
The propeller type I wanted to end up with is an 5x4 inch propeller. (5 inch for the lengt of the propeller, 4 inch for the pitch) The original design is an 8x4.5 propeller. To scale it to the correct dimensions I scaled both X and Y axles with a factor of 0.625 and the Z axle with 0.888. Now the hole in the hub is also scaled and need to be brought back to the correct dimensions. The axle of our motor has an diameter of 3mm so I made the diameter of the hole 3mm.
To make sanding easyer I added fillets to the corners where the blades touch the hub. This also makes the propeller a lot stronger.
Attachments
Step 2: Slicing the Model - Import File
To slice the 3D model I used free software from autodesk; 123D Make. You can download the software here.
Step 3: Slicing the Model - Construction Technique
Step 4: Slicing the Model - Manufacturing Settings
In this step you have to configure the materialthicknes and toolthickness you are using.
In our case the materialthickness was 1,2mm and the laser thickness +/- 0.1mm Be sure to set the correct unit (mm/inch)!
Step 5: Slicing the Model - Modify Form
In our case the material we used was to thick; after slicing there were gabs between slices. To repair this, we changed the form of the propeller within 123D Make. Be sure to put the slider (see the second picture) all the way to the left side. This wont affect the performance of the propeller much, becauce the propeller will be sanded down to its original size.
An alternative for this step is using thinner material or making a bigger propeller.
Step 6: Slicing the Model - Export Nesting
In our case the dwg export option did not work, so I used the PDF option and converted it to dwg.
After the export you will need to optimize the nesting; there are automaticly placed dowel holes that need to be removed, and after changing the form in step 5 the holes in the hub are to small. I won't guide you through the proces of making the final nesting, because I assume people with a lasercutter know how to do nesting.
If you want to use the nesting I made you can download it below. Keep in mind that this nesting is ment voor wood with a thickness of +/- 1.2mm.
Attachments
Step 7: Laser Cutting the Plywood
Make sure the grooves of the plywood are in the same direction as the long sices of the propeller slides (look at the picture); this will make the propeller stronger.
If you are using my nesting from the previous step, use the following cutting-order: red, black, blue. This way the laser will always be in focus. The red lines are marking lines, they have to be cut in very light (engraving also possible, but this takes longer).
If you use your own nesting, I recomend you to do the marking lines first, after that the holes and as last the outline of the propeller slices. That way the laser will always be in focus.
Step 8: Bonding the Slices
Step 1: Drill a 3mm hole in a piece of waste wood and put in a M3 bolt. Make sure the bolt is standing up perfectly vertical. (If jou use another diameter for the hole in de hub use that diameter for the hole and the bolt)
Step 2: Stack all the slices over each other, starting with slice number one. Save the two smaller pieces with number 9 for later. Put a nut on the bolt. When all the slices are placed correctly slightly tighten the nut.
Step 3: Use a bit of thin superglue to glue all the slices lightly together. The superglue will be drawn between the slices. Make sure you don't glue the first slice to the waste wood.
Step 4: When you know for sure all the slices are glued lightly together, loose the nut and carefully take of the propeller. Now you can hold one of the blades and fully glue the other blade. Use the same technique as in step 3; just put superglue on the sides of the slices, the superglue will be drawn in between them. When the glued blade is completely dry, hold that one and glue the other one.
Step 5: Glue te smaller slices with the number 9 on it.
This proces may seem a bit complicated, but this way you wont get any superglue sticking to your fingers.
Step 9: Sanding the Propeller
It is best to use no automated machinery for sanding the propeller, that way you are sure you don't sand to much and get a plain surface.
For the convex side of the propeller it may be handy to glue a piece of sandpaper to a piece of wood and sand it that way.
For the areodynamics it is especially important that the comvex side of the blades are as smooth as possible; the air has to move as fast as possible over that side of the blades.
Step 10: Optional: Lacquer the Propeller
To make the propeller sturdier and weatherproof it may be a good idea to lacquer the propeller.
If you have a balancing tool it may be a good idea to balance the propeller.
Have fun flying your RC planes and drones with your homemade and awesome looking propellers!
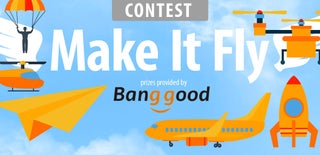
Runner Up in the
Make It Fly Contest 2016