Introduction: Laser Scanning Microscope
Besides other things I'm very interested in lasers, the microscopic world, and to make things visible that aren't visible with normal means. I also find it a sport to use things for purposes where they are not designed for (aren't we all ;) ). Combining the above I came up with a solution for an idea I have for ages: making a Laser Scanning Microscope (LSM)! Nothing fancy as a Fluorescent Confocal Laser Scanning Microscope, but a straight forward LSM.
- An LSM works basicly as follows: highly focussed light from a light source hit point by point, row by row (X-Y plane) an object. The light, reflected from the object, wil travel back the same direction it came. A semipermeable mirror reflects this light containing data of the object to an LDR. The intensity of the reflected light is measured. A computer takes care of steering the light spot and also the image making (pic 2). -
At the same time I was wondered if it is possilble to use a DVD laser pick-up to make an LSM. Well, with some alterations, it is!
The reason I was thinking of a DVD pick-up is that it houses a laser and a lens capable of projecting a spot of visible laser light small enough to "see" a bit on a DVD. And those bits are very small (320nm)! Furthermore it houses coils to steere the lens (sideways and up and down) and a detection part. This steering is necessary to be able of following the microscopic narrow tracks on a CD or DVD while spinning (sideways moving of the lens) and follow height differences while spinning (up and douwn movement of the lens). You can imagine that folowing the track must be very precise considdering the turning speed and the bit size! These characteristics are exactly what we need!
I tested the pick-up as is:
- hooked the laser on
- pulled out the detector
- instead of the detector I put in an LDR (Light Dependent Resistor)
It's turns out to be unusable in this form because:
- a technique in the pick-up to make multiple spots (grating filter, lens fringes)
- one pick-up is for one axis only
- the inertia of the whole pick-up.
At this stage the idea was born to use only the part that houses the lens with the steering coils. With one of these parts you can steer the lens in one axis. The other axis will be steered with another lens/coil part (as you can see later on). The result is one lens that can be moved in an X-Y plane! When (laser)light travels trough the lens when it is moving, the light spot wil follow this movement as well. This is more or less the most important part of an LSM.
Some specs:
- enlargement approx 1300 times (resolution 200 nm)
- image consists of 65536 pxels (256x256)
- very cheap (maybe most parts you have already)
- fun to build
there are some drawbacks to (naturally)
- it is not quick (approx half an hour for an image to complete)
- focussing is difficult
- the image isn't crispy sharp (but I don't care, it's astonishing anyway)
- addiction hazard :)
In this instructable I shall explane how I did this and what difficulties I encountered during the project. I think this instructable is a whole mouth full but building it is'nt really hard.
Pic 1 and 3 shows the model I work with right now. It was in the beginning of my project development a more chaotic contraption, but it did work fine!
Before you start building, a word of advice (pic 4): since this device's main part is a laser and the whole thing operates by means of concentrating and redirection by lenses and mirrors, of laser light, you have to be extremely carefull and take precautions for yourself an any bystanders not to stare directly into the beam or any reflection of it.
Step 1: Things You Need
Like every technical hobbyist most things you need you will have already in your possession. In the past decades I have taken appart several DVD/CD players and have always saved the parts for later use. You never know!
This is the list:
for the lens part:
- two lens/coil parts of a laser pick-up (DVD and/or CD)
- a bit of PCB
- a piece if UTP cable (approx 15cm)
for the electronic part:
- An Arduino UNO
- An LDR
- 2 x 10uF capacitors
- 1 x 220 Ohm resistor
- 1 x 10k resistor
- 1 x 10k pot
- 1 x 200 Ohm trim pot
- 1 breadboard
- 1 switch
- 1 3,5 mm jack plug
- 1 audio amplifier, a cheap computer amp (like the little ones with build-in speaker) wil do.
for the laser part:
- 1 laser* with a good collimating lens
- 1 piece of glas, a quarter of a microscope object glas or so to act as a semipermeable mirror
- the under part of a ballpoint casing to put the LDR in
And preferably a decapitated microscope so you can build the whole thing in a nice housing with an in height adjustable object table. You can also use the adjustable object table of an other microscope for your objects, and position the lens/laser combination in one way or another above it, as I did in the beginning of this project, and that wil work fine, but if you can lay your hand on a scrap microscope you can make things much easyer.
The point is: you really need an in height adjustable object table (otherwise you can get very stressed.). It's even better if the object table can also be adjusted in the X-Y direction.
Keep in mind that to focus with this kind of magnifications, where the focus point lies on around 1 mm distance from the lens, you have to be able to adjust the object table within hundreds of millimeters!
For the computer part:
- Four sketches, two of them for handeling the data stream coming from the microscope ("Arduino" and "Processing"), and two sketches to help focussing.
And to make live easier:
- Hot glue
- UV glue. This is a very handy glue to glue the thin wires on the lens part as you can see later on. I think this is the only glue that can do this job because there is no mechanical stress when applying this glue!
* there are lasers with varying wavelenghts. From long to short wavelenghts there are, among others: infra red, red, green, blue and ultra violet. With ultra violet (in this list the shortest wavelenght) you can theoretical make the sharpest image because you can make the smallest light spot. I have made a few with an UV laser and it did well, but the darker colored objects are harder to capture.
Step 2: The Laser Pick-up, Close Up
Left on the picture you see the complete pick-up with: coils, lens (actually this lens is'nt in anymore), magnets and mounting plate. On the right an other one, I pulled out earlier, without the mounting plate and magnets. Here you can clearly see the coils and suspension wires.
When there is a current flowing through the suspension wires (also acting as power lines) the coil wil move because a coil act as a magnet when powered with electricity. And while the coil is located in a magnetic field the coil wil attract or repel, depending on the polarity of the current, to the magnet and so wil move. Because the lens is attached to the coil he wil move along with it.
Step 3: The Making of the Lens Part (part 1)
It's advisable to first determine the terminals you have to use to let the lens move sideways. If there is no indication on the lens/coil part, use the trial and error methode. Do this with 1 or 2 Volts DC, and start, if there are for instance 5 terminals, with one probe on terminal 1 and the other probe tries terminal 2,3,4,and 5, if nothing happens put the first probe on terminal 2 and the second probe on 3,4 and 5 etc. If you touch the right terminals the lens wil move sideways. We will not use the up and down movement! The lens wil move in the opposit direction if you switch the probes (change polarisation). This is important for the Y-direction lens/coil part as this one has to pull (not push) the whole X-direction lens/coil part! Note which terminals are the right ones for furter use.
When I first shine laser light trough the lens there was no nice enlarged spot but no clear spot at all. It was more like a cloudy dashed line. It seems the lens has fringes (pic 1). I didn't think this would work so I searches for a lens with no fringes. I have found one in a other kind of housing so I have to make an precision operation, partially under a stereo microscope.
- First I pulled out the lens (pic 2)
- Subsequently I pulled out the grating filter (the little square piece of glass, these also makes the light spot unusable, (pic 3)
- Old lens out, donor lens waiting (pic 4)
- Precisely position the new lens (pic 5)
- The new lens is glued (UV glue, pic 7) in place (pic 6)
If you are Lucky you find one with a suitable lens and you don't have to be a surgeon at all.
P.s.
Afterwards I think that pulling out the grating filter is enough to make this thing work. So if you don't have a lens without fringes, pull out only the grating filter (the dashed line will not be there anymore) and give it a try!
Step 4: The Making of the Lens Part (part 2)
When you have taken a closer look to a laser pick-up, earlier in this instructable, you can see that the lens/coil part is suspended by 4 wires. These wires also provide the current to move the lens.
I have used the same principle. But to get this right you have to make suspension wires that are firmer then normal cupper wire, and also more straight. I have made use of a technique that alters the molecular structure and at the same time makes the wire extremely straight. It goes like this:
On pic 1 you see the UTP clable I have used. In the UTP cable there are 8 separate colored wires each of them contains several thin copper wires. For every corner you need one thin wire. So you have to strip of the insulation off of the UTP wire and take out 4 cupper wires of approx 15 to 20 cm. Actually you need 5 because later on you need one other.
The wires are now very floppy and bends easily. You wil see that after the proces they behave very different!
Take one of the wires and clamp it in a vice, then take a plier and grab the other end of the wire. Now pull the wire, in a calm way, with the plier in a straight line away from the vice until the wire snaps (you can actually feel the wire stretching before it snaps). Do this with the the other wires as well.
If all goes well you now have 4(5) beautifull straight and more sturdy wires (pic 2) that can be used for the build. You must be carefull, the wires are sturdyer but they are'nt invulnerable!
The diameter of the wire was before the proces 0,19mm and after 0.18mm.
- Now, take a piece of PCB and dril a hole approx there were the lens would be. Make the hole as big as possible so you have some slack.
- Figure out through which holes the wires has to go in order to glue the wires on the right spot of the lens/coil part. Remember that two lines are transporting current so they may not create a short circuit! Look also on pic 3 where you can see that the soldered lines are on different copper strips. On these strips the wires coming from the microcontroller can be attached.
- Sturdy suspend the PCB, with the cupper side up, high enough from the workbech to insert the straightened wires from above
- make on every wire a hook of about 1 cm and stick them trough the desired holes and solder them in place (pic 3). I secure the wires in place with UV glue prior to soldering, otherwise the light weight wires will stick to the soldering iron.
Step 5: The Making of the Lens Part (part 3)
On pic 1 you see the lens suspended on the wires and the second lens/coil part attached to it. Also with straightened cupper wires. That's the goal!
All work from now on has to be done with extreme care!
- flip the PCB so that the wires stick straight up and use little magnets to secure the PCB on a steel case or so. Make sure that the PCB also rests on magnets so that its parallel with the steel case (pic 2).
- I have used a piece of aluminum profile with a heigth of 15mm, and placed it between the wires as a spacer and on that piece of aluminum I placed the lens/coil part so I can glue the wires more easely (pic 3). Maybe a greater height then 15mm for the spacer is better (less power needed to shift the lens part) but not too long, say 20 to 25mm! When I make an other one in the future I shall surely make them longer. I have put in the holes were the wires stick trough a drop of UV glue as a tension release for the soldering point.
- Make shure the aluminum or whatever you use as a spacer is smooth and free of burrs and damages otherwise you cannot pull it underneith without pulling the the lens/coil part sidewards and damaging the wires!
- to glue the wires to the lens/coil part you can bent the wires to the points where you want to glue them. To do that you must push very gently with a little screw driver or something simular against the wire, as close as possible to the base (PCB), in the direction you want the wire to go to. It's better to let the wire nearly or exactly touch the spot where it will be glued rather than that is pushing!
- now you can cautious apply some UV glue (this can be done without mechanically touching the wire or lens/coil part) (also pic 3).
The white blobs on pic 3 are not UV glue blobs but they were allready there and I use these blobs to glue the wires on so they are insulated as well. If youre's does not have those white blobs you can make them yourself with UV glue as wel. Also notice that I used all the 4 wires for the connecting of the coils. I did this because I was thinking ahead and has also connected the up an down coil with the intention of pendulum correction: like a swing where the shortest distance is straight under the rope. But in practice they turns out to be not necessary (with a swing distance slightly bigger than the width of a human hair there is no noticeable pendulum effect) . So you don't have to solder these wires to the up/down terminals. That wil make it a bit easier.
With the wires glued and the aluminum spacer still in place its time to gently bend the wires with the help of tweezers or a small pliers in such a way that the wires are situated lower then the lens and are routed to the appropriate terminals (pics 4,5 and 6). For this job you need a steady hand! Actually two! But you can rest your hand on a suitable elevated underground, that will help a lot. Note that 2 of the wires (for the up and down movement) as mentioned earlier, don't have to be connected with the terminals, but at this moment I did not know that. But you do! Saves a lot of hassle! ;)
The lens that is now in place is the lens that shall be moving in the X-direction.
The picture sequence makes a little jump but with the next step the aluminum spacer needs to be in place (I forgot to make a picture).
So with the spacer still in place:
- Find a suitable elevation for the other lens/coil part so that this lens is slightly lower than the allready mounted one. In this way the lens that is actually making the image is on the lowest spot. (consider that the whole contraption wil be turned up-side-down later on).
- this second lens/coil part must be mounted in 90 degrees difference with the first one. I have used hot glue for this.
- Now the second lens is in place we must connect it with the first one in order to get an Y-direction movement as well. To do this make (if you did not have already) a simular cupper wire rod as used for the suspension of the first lens, cut them to size so that you can make a triangular shape. Now put the rods in place and secure them with a blob of UV glue on the second lens (this one wil not be used as a lens so can be sacrificed) where two rods comes together and form one angle of the triangle, and two on the housing of the first lens in such a way that it not interferes with the movement of the lens itself (pic 1 and 7 will explain a lot). This second lens/coil part wil move the whole first lens/coil part in the Y-direction.
- Now you can pull away the spacer with one hand while keep the lens part in place with a finger of the other hand and let the lens suspend freely. But do this with great care and bit by bit! Don't force it!
Congratulations! You now have finished the most important and trickiest part to build of the microscope!
Step 6: Testing Lens Movement
On the picture you look down on the PCB (this is the normal working position) and through the hole you see the lens/coil part. A red laser is shining trough the hole at the moment (you can see the red reflection). You also see the grey wires that go to the breadboard:
- The 2 upper left grey ones are for the Y-direction
- The 2 lower left grey ones are for the X-direction
- The black and red ones at the left top are the wires that goes directly to the Y-direction lens/coil part and are connected via the PCB with the upper left grey wires.
- The X-direction coil is fed by the suspension wires.
The black square is insulation tape because I use a crocodile clamp to hold the PCB.
At this stage you don't have a working bread board so testing can be done with the 1 or 2 volt DC you use for determining the terminals as you have done before. If you shine a laser through the lens you can see the movement better.
If everything works we can go further.
Step 7: Electronics
To steere the lens for the purpose of this LSM, the coils must have varialble DC values (256 of them, in both directions). But an Arduino Uno is'nt capable of making analog signals. But Arduino does do PWM (Pulse Wide Modulation). PWM and a low pass filter wil do the job.
For each channel (X and Y) a low pass filter act like a DAC to make from a PWM signal an analog (DC) signal. This is done with a resistor/capacitor combination.
- On pic 1, the schematic of the electronics, you see two of these combinations, one with a trimmer pot for adjustment purposes later on. Here you see everything needed for the electronic part to work.
- The LDR part is also straight foreward and with the potentionmeter you can, more or less, change the contrast. The jack is used to make the scan signal heareable. This makes focussing easier. Switch off with S1 when making the image!
- Pic 2 shows how everything is hooked together.
Step 8: Putting Things Together
On pic 1 you see one of my first contraptions. As you can see it's a little bit chaotic, but it did work rather wel. On the picture you see my son's little microscope I had borowed (for the vertical movement of the object, to make focussing easier), the crocodile clamp with the the PCB holding the lens, the blue tube (ball point housing) containing the LDR, the laser attached with magnets to a CD/DVD lid that on his turn was clamped to a wall shelf, and a whole microscope slide in an angle of 45 degrees to act as a semipermeable mirror. Okay it is'nt an ideal situation, but if you have nothing else for the time it's workable. But be sure that the lens moving plane is parallel with the object table! Then you are ok for now.
Here you see also one of my green lasers, who now is resting in peace after I abused him til dead with 22 Volts instead of 3 V max! He did'nt like that at all! That was a pity because this laser had a very nice round spot and was very good focusable. An other green laser had no good internal optics and therefore not good focusable. I use now a blue laser with even better results. So you see: you have to experiment a little with differend lasers to see wich is the best. By the way, a round laser spot is'nt necessary, rectangular wil do nice.
I use a ball point housing (with the tip a little bit bent) to put the LDR in. It fits snugly and if you put the surface of the LDR a little bit deeper than the edge of the ball point housing you have less stray light hitting the LDR. Make sure you first solder longer leads to the LDR (pic 2).
The close up of pic 3 shows the LDR in the tube, slightly sunken (to prevent stray light).
I've made the semipermeable mirror out of a thirth part of a microscope slide (any little piece of glas wil do) glued to a piece of foam (the black triangle) what I've cut on an angle of 45 degrees (pic 4).
On pic 5 the mirror is in it's place. It's situated above the (black)hole where the laser beam travels through. On the left you see the LDR housing with a piece of aluminum foil. In this foil I have punched a hole with a needle. I explain later why I use sometimes needle punched aluminum foil.
So, in short:
- put the laser in place so that the beam shines straight downwards (the spot on the table lies dead centre under the laser)
- situate the lens part you've build in the laser beam path so that the moving plane of the lens is horizontally, and that there is room above the lens part to put the semipermeable mirror on, and that the beam is traveling obstacle free through the lens part.
- Connect the lens part to the breadboard (see schematics on previous step)
Step 9: Programs
For this project I have made an Arduino sketch and a Processing sketch. The Arduino sketch takes care of the steering of the lens, reads the LDR values, and sending information to the receiving program: Processing! If you don't have Processing installed at this moment, you have to download and install Processing first.
The Processing sketch takes care of receiving the data and translate it to an image.
The sketches are self-explanatory, so take a closer look on them and try to understand the working of them.
I have taken a screenshot of my computer screen to let you see how the programs look like: (pic 1)
- At the left, the Arduino sketch: MicroscopeArduinoPartA.ino
- At the right, the Processing sketch: MicroscopeProcessingPartB.pde
- In the middle lower part of the scheen, two focussing sketches to make focussing easyer. One that makes a big (big? well, a little bit bigger than the cross-section of a human hair!) square and one that makes a small (really small indeed) square: MicroscopeFocussingAidBig.ino and MicroscopeFocussingAidSmall.ino
- In the middle upper part of the screen is the window where the image wil appear.
Step 10: First Test Run
Assuming that you have:
- build the lens part, (step 3,4 and 5)
- build the electronics, (step 7)
- put it all together (without the object table and LDR for now)
- Dowloaded the sketches and have them ready on your computer screen
- everything hooked together
It's time for a test run to see if the lens will move in all directions.
With the laser, the lens part, and all the electronics in place, power on the laser. Now you see a very enlarged spot on the table (the movement of the spot will be enlarged as wel). Load and run MicroscopeFocussingAidBig.ino sketch and, if all is right, you will now see the spot moving in a square pattern. Make use of trimmerpot 2 to make the travel path of the Y- and X-direction as equal as possible. Now the steering of the lens is ok, all is ready for the first test shot.
Step 11: Focussing and the First Test Shot
At this stage you have to place an in height adjustable object table, like the little microscope I mentioned earlyer, the semipermeable mirror, and of course the LDR.
The mirror, the LDR and the lens part are not fixed in place so you can make some adjustment when needed! I still have those parts loose! I recommend you not to fix them in place at all.
As a first shot I recommend to take a microscope slide with a specimen so you can make a transmission shot! This is the easiest way to get familiar with the LSM because you see on you work table the light shining through your specimen and focussing is easier. On picture 1 and 2 you see how you can place the LDR. Everything else stays the same, and also the method shown below stays the same except the bit with the translucent plastic, what is'nt required because you measure not the light what travels back via the mirror.
Put an object with a known pattern like an integrated circuit, or a piece of a CD (to make a CD specimen I carve the label side with a knive and use a piece of sticky tape and place it on the cut. When you pull away the tape the shiny bit of the CD comes along with the tape).
Run one of the focussing aid sketches and elevate, with the adjustable object table, the object to a distance of around 1mm under the lens. Be carefull not to go so high that the object can touch and maybe damage the lens part!
If you use a translucent piece of plastic in the light path coming from the semipermeable mirror you can see the lightspot changes: begin from a distance of around 4mm and gently raise the object. At the same time look at your translucent piece of plastic and all over sudden there appears a light spot, it becomes smaller, bigger, maybe smaller again but on a certain point you see the spot fluctuating. This is what we need! Because the fluctuating is caused by the structure of the object. They are actually reflections of the laser light hitting the object.
Now you wil have to find the sweet spot. The sweet spot is the distance between the object and the lens where the focussing is optimal. On this point the fluctuation of the spot is on it's most. Probably the edge of the spot is fluctuating more.
Take away the translucent plastic and put the LDR in the lightpath, use the switch to let the signal coming from the LDR goes to the amplifier. Now you can hear the sound the of light scratching the surface of the object (you can make use of a needle pinched piece of aluminum foil wrapped arround the tip of the LDR holder to isolate the most fluctuating place of the light spot).
If you listen to the sound when focussing you hear the scratchy sound (besides a trumpet like sound that you have to ignore) varying. Where the sound is the scratchyest it is most certain the focus point . Flip the switch to disconnect from the amplifier, and then start the Arduino MicroscopeArduinoPartA.ino sketch. Wait until the sketch is loaded to the Arduino Uno totally (watch the progres indicator), and then start the Processing MicroscopeProcessingPartB.pde sketch. Now a new 256x256 window appears and from the bottom up the image wil be created.
See the movie.
If you are Lucky you have a reasonable sharp image building up right away, otherwise you have to tingle a little bit with the focus knob and wait a little while (to build up some lines). When you are happy with it you can now begin from the start. If you do so do it like this:
- first stop the Processing sketch (the little 256x256 window with the partially finished image disappears)
- start the Arduino sketch again (the lens is waiting and does nothing at this moment)
- start the Processing sketch (the little window re-appears and the image building is started all over again)
When all goes right you have after half an hour a strongly enlarged image of the specimen.
I use the screen grabbing program (the one delivered along with Windows) to select the 256x256 image and save it to disk. Do this before stopping Processing otherwise the window closes! Now you can use a photo editor to enhance the image, if you wish.
Step 12: Finally...
If all was going wel, you now have your first microscopic picture! Congrats!
If you experience some difficulties with focussing, the same I did, you can combine the optical way (a translusent bit of plastic) with the audio way (routing the LDR signal to an amplifier). Then you can listen, look, listen etc, until you are satisfied.
You have to learn working with this thing, and you will notice that in the course of time it becomes easier. But nevertheless, you have to considder that dispite all effort not every attemp is succesfull!
Some tips:
- the spot with the clearest fluctuation and highest fluctuation speed is the spot with the highest focus and most contrast.
- Specially with shiny objects, such as a CD, I have the lens part a little bit shifted to the side so that the light spot is shifted sidewards also (the beam then travels under a small angle), to prefent reflections between the object and the lens that will disturb the image.
- Have some differend (differend colors) lasers at hand to experiment with. Not all lasers have the same optics specs so you have to find the one that does the job best.
- make it so that the lens part, semi mirror and laser are adjustable in the horizontal directions (don't fix them permanently), because you have to make adjustments so now and then.
- If you use a UV or blue laser, use a fluorecsent marker to make the translucent piece of plastic UV sensitive.
- Be carefull (with the laser power) when using organic specimen because the laser is focussed to an extremely small spot, so even a laser of modest power can ruin your object. I have burned holes in specimen like a hair more than once.
- Don't wait for the picture to complete! If you see after a few lines that the picture would be ok, than do something else. Waiting can be very annoying so I leave the scanning for what it is and after some time I take a look. That makes it a bit exiting to!
Some refection type examples (The images are enlargements of areas with a size of approx 0.05x0.05mm):
With a red laser
Pic 1, an eprom
Pic 2, an other part of the same eprom
Pic 3, a human hair
With a blue laser
Pic 4,5,6 and 7 an integrated circuit (5 and 7 a little bit enhanced)
With an UV laser
Pic 8,9,10 and 11 an integrated circuit. Pic 12 and 13 a CD (pic 9,11 and 13 a little bit enhanced)
Some transmission type examples: (except the pollen one, the microscope slides were bought, not self made.)
With a blue laser
Pic 14 and 15 are pollen grains (pic 15 enhanced).
Pic 16 and 17 is a cross section of a stem of wood (pic 17 enhanced).
Pic 18 and 19 is a epidermis of an onion (pic 19 enhanced).
Step 13: Epilogue
It was a long way for me and I hope that this instructable helps the interrested fellow DIYers to get this thing going in a shorter time that I did when developing this LSM.
But before you consider te build this thing, do keep in mind that the area this LSM wil make a microscopic image of, is extremely small, where the image is often not recognizable. This might not appeal to everyone.
On the other hand, if you are interested in the microworld, this could be a nice project for you to start. It costs allmost nothing (in fact it has cost me zip! All but the microscope stand, you see in this project I had in my posession, the microscope stand I get for free).
Besides it cost almost nothing it wil cost you: time, dedication, maybe speepless nights an a lot of patience (specially when mastering the focussing).
I think that this project has reached a point that I can share it with you and so I did. On the other hand I think that there are improvements possible, like variable magnifications, or more sensitive to light so you can use a laser with less power, to mention something. I will shine my light ;) on that from now.
Thank you for reading my instructable and for those who going to build this thing, I whish you a happy build!
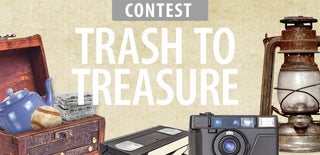
Participated in the
Trash to Treasure Contest 2017