Introduction: Lessons Learned in Tool Making (5 Tools)
In the past years I made several tools. Instead of sharing with you in full detail how I made one particular tool, I would like to share 5 of my projects and focus more on what made a each tool project a success or a failure, especially after using some of the tools for some time now.
If you are thinking of builing one of the tools I made, there a plenty of detailed examples on Instructables or Youtube on how people made such a tool. But on Youtube they usually present their tool project as a success, while I doubt if all of those tools work really well. Hopefully my instructable will help you to avoid some of the problems that for sure can occur in DIY tool making.
I will discuss the following projects:
1. Making a vise (success)
2. Making a work bench / welding table (success)
3. Turning a pneumatic chisel into a pneumatic hammer (failure)
4. Making an insert for a car jack (success)
5. Making a drill press (failure)
Step 1: Making a Vise
I made a large vise from scrap pieces of steel. The construction of a vise is not very complicated. Just take apart any available vise and you can see the required parts you need to make.
The fixed part of my vise consists of a bottom plate and I welded two pieces of angled steel to guide the long U-beam sideways. I welded a plate on top of the angled steel to make sure the U-beam could not tilt or move upwards. Then I used more angled steel to make the moving and the fixed jaw. I added a plate under 45 degrees to give the jaws some more strength. On the jaws I added two small steel strips and used an angle grinder to make some grooves for more friction in holding the work piece.
For the lead screw I used a threaded rod and some nuts. I made a steel box to hold three nuts in place. I did not weld the three nuts to eachother. I needed a spring to keep some tension on the lead screw and made that from a piece of welding rod.
Lessons learned:
- Overall I am really happy with my home made vise. It is much larger than other vises I have, so I can use it to hold large parts and it works well.
- Up front I doubted if an ordinary threaded rod would work, because most vises have a special type of thread which is stronger and requires less rotations to move a certain distance. But my threaded rod works fine. It still moves quite quickly and I can clamp even large pieces of steel in the jaws and keep them really well in place. So using an ordinary treaded rod is no problem as long as you use one which has some good thickness like the one I used. (Mine is M16 thread.)
- In previous projects I used to weld multiple nuts together but that never worked well. When you weld nuts, they warp a bit from the heat of welding and then the treaded rod cannot rotate freely anymore. Therefore I now used a box/ container to hold three nuts in place, so they allow the rod to rotate with almost no friction.
- I also doubted if making a spring from welding rod would work. Normally springs are made of a special type of steel and that is better if you need a good spring, but I only needed a spring for some tension and my solution worked fine for this application.
- The part I struggled with in this project is to get enough clearance between the moving part (U-beam) and the fixed part of the vise to make the U-beam slide smoothly without having too much clearance which would make it wobbel. I first used some piece of paper to get the clearance during welding, but after welding my pieces of paper got stuck. With some force I got them out but still the U beam was stuck. I had to hammer it out from the steel parts that I used as guidance. I tried using force to bend the metal and get the correct clearance, but that also did not work. Finally I grinded my welds out and tried again. That time I still was not happy, so I grinded again and tried a third time. This time the final result was the way I wanted it. So my main lesson learned was: think about the needed clearance and keep welding distortion in mind while making a tool.
- I saved some money by making this tool myself instead of buying it. However, if I would calculate all the hours that it took me to make the tool, it would be an expensive tool. But I really enjoyed making it, so I certainly do not regret spending my time on making this tool.
Step 2: Making a Work Bench / Welding Table
I wanted to have a steel work bench so I could use it for welding and also use it to store some of the tools I frequently use. I bought the needed steel and started the production. I welded some nuts under the legs of the workbench to make the height slightly adjustable and to allow levelling the work bench on any floor. The top of the work bench is made of steel, so I can use it for welding. The storage shelves are made of wood, which is much cheaper than steel. I also made some accessories for example for storage of the cables of my welding machine when that is not in use.
Lessons learned:
- It is not a very difficult project to make a welding table, so it is likely that it is successfull. Still it is a bit of a challenge to get it exactly plum, square and true. That is mainly related to controlling the welding distortion. Of course it is up to you to decide if it is a problem when the legs are not 100% plum or square.
- Just welding 4 legs to a table top will work but that is not ideal. That stucture is not very stable so it is much better to interconnect the legs.
- My table top is 8 mm thick steel (about 1/3 of an inch), but still it can bend a very little bit. If you use a thinner steel sheet, you should support the table top against bending.
- Having an adjustable height for the legs is nice to have, but it is not really needed. My welding table has been in the same spot since I built it two years ago and I never adjusted the height of the legs after putting it in place.
- I love the height of the two shelves on my workbench. The top shelf holds several power tools like for example a drill, and angle grinder.
- I also added an extension cable with power sockets on the legs of the table, so I can plug my power tool in at the work bench and the power cord is never too short.
- The bottom shelf holds large items like my welding machine. I have enough access space to adjust that machine and I hang the cables from the accessorie at the side. I also tied the argon cilinder to one of the table legs, so it cannot fall.
- Under the bottom shelf I sometimes also store something on the floor.
- There is one point that I might improve and that is to add some doors or other covers against dust for the shelves under the workbench. Now it collects quite a lot of dust.
Step 3: Turning a Pneumatic Chisel Into a Pneumatic Hammer (failure)
For my job I sometimes have to build refractory in a steam boiler. This refractory has to be hammered in place and usually I just use an ordinary hammer, but by the end of the day it makes my muscles very tired. Therefore I bought a pneumatic chisel with the idea to turn it into a pneumatic hammer. I just grinded the top of two of the chisels and welded a flat plate there which resembles the shape of the head of a hammer. I tried it and it did not work, because the shape was not good. (The flat head dug itself into the refractory and then all refractory came of when I pulled the tool towards me.) So the next step was to make a half round shape as you can see on the second photo. I used that tool and it worked fine for about 10 minutes and then the weld ruptured and the head came off. I asked a colleague to weld it again while I continued with manual hammering. After the repair I could use the tool again for about 10 minutes and then the weld ruptured again. I thought that was because the steel alloy of the stem was much different from the ordinary contruction steel that I used for the head. So I decided to finish the refractory manually and later make the stem also out of construction steel. That would have been easy on a lathe, but I do not have a lathe, so I used an ordinary manual file. With some patience and elbow grease I made a stem of the right size and I welded the head back on the stem. I tested that on the next refractory job. That time it lasted about 4 hours and it broke again. This time the stem was also deformed a bit because of all the hammering forces and it was stuck in the pneumatic tool. After this experience I decide to ask a specialized company to make this tool accessory for me. They turned the part on a lathe and after that used heat treatment to make it partly hardened, but not brittle.
Lessons learned:
- It is possible to make the stem with manual filing instead of using a lathe. I was quite happy with that.
- Repeated forces on a weld can cause it to fail quite rapidly if the steel is not suited for this application. (Of course it also has to do with the skills of the welder, but especially my colleague is a certified welder who can weld on pressure vessels like steam boilers, so the weld itself was fine).
- Using the right type of steel if the part has to endure large forces is very important.
- Hardening and tempering to get the right properties in the steel is also important.
- I leared a lot from this project, but next time I will ask a specialised company to make it, since I do not have the required tools to get a good result.
Step 4: Making an Insert for a Car Jack
We have a car jack, but the bottom side of our car does not fit so well on the car jack. The car jack has a round top with 4 small elevated areas. It would be much better if it had a groove on the top, so I made a removable insert which fits on the car jack and fits on our car. I made it just by welding some different parts together to make the correct shape. It works perfectly.
Lessons learned:
- This part was a success because it did not really matter what type of steel was used, so the construction steel I have is perfectly suitable for this job. (Contrary to the pneumatic hammer of the previous project.)
- It would probably have been easier to make this part on a lathe or a mill, but I do not have a lathe or a mill and I am happy that it is also possible to make it manually. I enjoyed the process of figuring out how to weld some small individual pieces of steel together to make this tool.
- The tolerances in the measurements were not so tight that it was not possible to do it manually. (Contrary to the drill press of the next project.)
Step 5: Making a Drill Press (failure)
When I started building things in my garage I could not drill a hole plum. It was always way off, so I wanted a drill press. A simple one does not cost a lot, but I liked the challenge of building one myself. (The funny thing is that project took so long that by the time it was finished my skills in drilling had improved a lot and I did not really need a drill press anymore.)
I wanted to make a stand with a sliding part that would be driven by a sprocket and a spring. Many things did not work out as I wanted.
Lessons learned:
- I welded the vertical part to the base plate and struggled to get it completely plum. So being able to control welding distortion is essential.
- My base plate was 6 mm (1/4 inch) thick but it was still possible to bend it slightly. That is not good for precision, so the base plate should be thicker or it should be supported by a U-beam or some other rigid part.
- I welded 4 small angled steel pieces together to make a sleeve that slides over the vertical pole of the drill press. To be able to slide it needed a small gap between the sleeve and the pole, but even my smallest gap still made the drill tip move more than I wanted. I decided to make the outer sleeve in wood and only use one thin sheet of paper as gap size and still it was too much. Tolerances are super important in the vertical moving part of a dril press. Any contruction with just some spacing is likely to have to much movement at the tip of your drill.
- The square tube that I used as central pole is also not everywhere exactly the same size. On some parts my outer sleeve could slide well, but on other parts it got stuck. Steel tube is not suitable if it has to be completely straight. Therefore people use aluminum a lot in DIY CNC projects, because aluminum has much better size tolerances.
- I made a wooden template to drill a long row of evenly spaced holes in my steel tube so the sprocket would fit there. Again size tolerances were not right, so the distance between my holes was not exactly the same everywhere. I also made the sprocket manually and this reinforced the problem. The distance between the teeth of the sprocket were also not identical. The result was that my sprocket would move correctly for about 1 revolution and then it got stuck. Also finding the right springs was a problem. I learned that my drive system is not suitable for a drill press.
- With a drill press it is also important to control the speed of the drill. I used an old drill where the variable speed button was broken and I also did not want to use the trigger of the drill to control the speed, so I used a separate variable speed control. It was a kit which I ordered and build some time before and that worked fine.
- At a certain moment I decided that this project would never get the results that I wanted so I quit the project and bought a drill press.
- I think that many DIY drill presses will have the same issue as I had so that there is too much play. Of course it can drill reasonably straight, but not so good as I would want to have.
Step 6: Conclusion
When will I decide to make another tool:
- If it is not possible to buy the tool I want because nobody sells it.
- If I think I have the right skills and the right tools to get the result that I want.
- If I enjoy the process of making, no matter if the tool will be a success or not.
When is it better not to make the tool:
- If I cannot get the right size tolerances to get a proper functioning tool.
- My experience is that making a tool always takes a lot of time, so if I do not enjoy making the tool, it is more economic just to work in those hours and buy the tool from the money I earn.
What else did I learn:
- There are plenty of examples and instructions on the internet from people who made a similar tool, so I will always check that first for good ideas.
- After that I will use common sense to think about the designs I saw. If for example somebody makes a lathe for metal and he makes it just by welding some parts together, then I am sure he will not get the precision that I want to have for such a tool. Tools that require precision are very hard to make, so there the risk of failure is huge.
I hope you will have some benefit from my experiences.
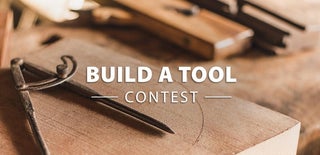
Participated in the
Build a Tool Contest