Introduction: Lissajous Curve Apparatus
Have you ever wanted to see sound? Look no further. The Lissajous ( LIH-suh-zhoo or /ˈlɪsəʒuː/ ) curves pictured above are a family of curves that can be graphed as a point vibrating up and down and side to side due to simple harmonic motion and are excellent for visualizing sound. They were discovered in 1815 by Nathaniel Bowditch but also investigated by the french scientist Antoine Lissajous, who wrote about them in his 1857 publication in the Annales de Chimie et de Physique.
In this Instructable, you will learn a method of producing these mesmerizing curves. This project is great for:
- Jumping into the optics of lasers, mirrors, and lenses*
- Improving your engineering, designing, and building skills
- Exploring the physics of music in a hands-on way
- Finding a practical application for parametric equations
- Seeing the *beauty* in the natural world
and much much more! Keep reading to see how it's done.
*well, how NOT to use a lens. You'll see.
Step 1: Research, and Theory
The concept is simple.
The heart of it is the tuning fork, an unassuming little piece of metal.
Bouncing light, in this case a laser beam, off of a mirror attached to the end of one tuning fork in motion and projecting it onto the wall causes the point of light on the wall to move from side to side very quickly, so fast that it appears as a line.
Due to the law of reflection, the angle of reflection will equal the angle of incidence, and assuming the tines move approximately up and down when they vibrate, the resulting ray should travel from side to side forming a straight line.
Bouncing light off of a different tuning fork, oriented perpendicular to the first, causes the light to move up and down in a line perpendicular to the first line.
Alone, each movement is only mildly interesting, but as soon as you have both motions going at once, a dazzling array of patterns appear! Changing the ratios between the frequencies of the two tuning forks leads to many different possible patterns.
In his 1857 publication, "Mémoire sur l'Étude Optique des Mouvements Vibratoires", Antoine Lissajous describes his set up. While he looked at a candle's reflection in the two mirrors, since then, lasers have been invented, which makes our task considerably easier. In this case, we will be bouncing a laser off the tuning forks, and projecting the image onto the wall.
In the research, I found several designs for similar apparatuses (apparatausi? apparatupodes??). I will be basing my design off one built by Max Kohl in 1900:
Step 2: The Design
While you could theoretically do the experiment with just some clamps and boxes, I wanted my apparatus to be easier to use and more precise. I also wanted it to be a bit of an art piece, something that looks visually pleasing.
I chose to use a simple mitered frame reinforced by four splines at each edge, which add a nice contrast.
The two tuning fork holders are meant to be movable for ease of operation.
See the design above for complete dimensions. The following steps all refer to these measurements.
Step 3: The Math (!) Behind It All
You can skip this part if you want but for those interested in math and music, read on!!
Lissajous curves are parametric curves, which means you can describe them based on a set of two equations which define their x and y positions as the parameter t changes, or as time passes:
x = A*sin(2π*Fx*t )
y = B*sin(2π*Fy*t + φ)
Where:
A is the amplitude of the fork aligned along the x direction, and Fx is its frequency in Hertz,
B is the amplitude of the fork aligned along the y direction, and Fy is its frequency in Hertz,
t is the parameter, which represents time passed in seconds,
and φ is inserted to account for the change in phases of the two vibrations.
Experiment changing these variables with the graphing calculator Desmos here:
https://www.desmos.com/calculator/opwzdxpgnl
-----
Modern musical scales are equal tempered, which means that as you move up one semitone (note on the piano), the frequency of the note is multiplied by the twelfth root of two (2^(1/12)). This means that starting on a note with a frequency f, then after moving up one octave, or twelve semitones, the new note has a frequency f*(2^(1/12))^12 = 2f. In other words, moving up an octave doubles the frequency of the note. This is all good and cool but for the Lissajous figures, this means ratios such as the ratio between the frequencies of C and G are strange: 2^(7/12) = 1.498... . This would lead to a warbling image because 1.498... is NOT equal to 1.5 (3/2).
Lucky for us, the tuning forks I bought from the website are made to have frequencies in perfect whole number ratios to each other. For example, for frequencies, we have G:C = 3:2, F:C = 4:3, E:C = 5:4.
While the tuning forks are not ideal for musical purposes, they work GREAT for science.
-----
Lissajous provides us an interesting diagram showing the results of different frequency ratios. You can find it here: https://www.jnorman.com/pages/books/38038/jules-a...
You will notice that any frequency relation, such as 3:2 doesn't just give one figure. As the phase shift, φ, changes, the figure undergoes a periodic shift between several different shapes.
Thomas B. Greenslade provides very interesting mathematical derivations of the equations of the most simple figures in "All about Lissajous Figures": https://digital.kenyon.edu/cgi/viewcontent.cgi?re...
In his paper, Lissajous goes much more in depth into the math as well.
-----
Food for Thought: The most simple ratios, such as 3:2, 5:4, visually, give much more pleasing shapes to the eye, while the more complicated ratios, such as 19:17 or 123:111, yield messy, cluttered shapes. At the same time, musically, the more simple ratios produce more pleasing harmonies to the ear. Coincidence?!
Step 4: Oops..!
Right off the bat, I have to explain some mistakes so you don't repeat them. Classic.
1. The reflective surfaces
While I originally wanted to polish the ends of the tuning forks to a mirror finish to achieve specular reflection with progressively fine sandpaper and a buffing wheel provided to me by Ms. Shayla Vines, I didn't do a good job (oh well), and the surface was rough. I could tell because the light was scattered when the laser was pointed at it, indicating diffuse reflection. See the diagram above.
The solution is simple: buy a thin mirror sheet that you can cut and stick right onto the forks. This worked much better but I guess I did admit defeat to the metal polishing gods....
Someday I'll get it! Thanks anyway Ms. Vines!!
TLDR: Attach mirrors to the tuning forks. Don't bother with trying to polishing them.
2. Using a Converging Lens
I had also originally wanted to enlarge the image by shooting the out-coming ray through a converging lens, which would enlarge the image as seen in the diagram above. The image by itself is only about 1 inch x 1 inch, so the lens would have been able to magnify this at least 5 times, making the experience significantly better.
Unfortunately, the actual beam of light does have thickness, albeit not a lot, which means the lens also enlarged the thickness of the beam. This means the resulting image was larger but very blurry.
I even bought a 50mm focal length lens, and built the lens holder and stand, all of which ended up being useless. I tried making the beam width smaller by poking a hole in aluminum foil with a needle and putting it on the laser, but the beam became oddly misshaped.
TLDR: Don't use the lens unless you have a very narrow laser beam.
If there is a way to acquire a laser with a very thin beam of light, the lens idea would probably work. If you know how this could be done. Let me know!!
Step 5: Materials
Materials came from various sources:
- 1/2" birch plywood sheet (a good looking one) (Home Depot (HD))
- 1/4" thick wood scraps
- Birch edge banding (HD) - optional
- Scraps of Walnut or any other hardwood.
- Clear bumpers / Rubber feet (HD)
- Hardware: 2x Wing Screw 1/4"-20 x 3/4", 3x Thumb Screw 1/4"-20 x 1", and 5 threaded inserts 1/2" long that fit 1/4"-20 machine screws. (HD)
- Laser pointer and batteries (ebay)
- Adhesive mirror sheet (Amazon) https://www.amazon.com/gp/product/B01BU99K6E/ref=...
- Set of scientific Tuning forks (Home Science Tools) + 1 extra C tuning fork: https://www.homesciencetools.com/product/scientif...
- Screws (Found in the well known and feared "cup" of random hardware you were too lazy to put away)
- 3D printed parts were designed by me in Fusion 360 and printed by my neighbor Mr. George Roberts. Thank you!! See step 16 for details.
- Wood glue, epoxy
- Various sandpapers
- Finish of choice. I used a simple Feed'n'wax from Amazon: https://www.amazon.com/gp/product/B002A94U5A/ref=...
Step 6: Tools
Basic woodworking tools are needed. You'll need at least:
- Table saw with crosscut sled and splining jig (and push sticks)
- Hand drill with various sized drill bits
- Workbench
- Flush cut handsaw
But these will make things easier:
- Band saw
- Drill press
As always, you should only attempt this project after thoroughly studying safety tips or better: with help from someone with experience who knows how to use power tools correctly. Woodworking can be dangerous if done wrong, but safe and enjoyable if done properly.
Without further ado, let's get into it.
Step 7: Box Frame
The frame is simple enough. Four pieces are cut out.
Two are then ripped once more to remove a central slot.
Save the piece you remove, and use it for the tuning fork holders, since they'll fit perfectly.
The pieces are all rejoined together with dowels drilled and glued into the sides.
Step 8: Joining the Frame
The frame is joined using a neat trick from David Picciuto at Make Something! The best part is, you don't have to go buy an expensive and only-useful-for-one-job tool like a 90 degree clamp. All you need is painters tape.
Procedure:
- The table is covered with a protective plastic such as a trash bag.
- The pieces are placed flat on the table in the order they should be glued and are then taped on the OUTSIDE along the joints using blue painters tape.
- Here's the trick: also tape the inside of the pieces right outside the area of the joint, so that all glue seepage will be simply peeled!
- Spread glue inside the joints (finger is still decidedly the best applicator) and close up the box. Tape shut. No clamps are needed, but I recommend you clamp a 90 degree support such as a square to the table to support the sides at the right angle, and walk away.
Once the glue is dried, have fun peeling off the tape. It's just as satisfying as it sounds.
Step 9: Cut Out Back Piece
Now is a good time to cut out a piece of plywood which will be the place where the laser holder attaches. Try to cut it tightly so that the piece fits snugly inside.
If you do this, you won't even have to bother with glue; the tension will hold it in place.
Step 10: Splining Time!
Although you could reinforce the joint with dowels, fancy dovetails, screws, or whatnot, I prefer the aesthetic of splines. They add tasteful accents but also good support if done right.
The procedure for splining can be found elsewhere and I won't go very deep in detail, but the basics are:
- Build a Spline jig. Mine is, once again, Mike Picciuto's design. Search for the video titled: "How to Make a Spline Jig for Picture Frames and Boxes"
- Plan out the spline locations. I decided to take the length of the box, divide it into perfect eighths, and then cut the spline slots along 1/8, 3/8, 5/8, and 7/8ths distances. This gives a good look in my opinion.
- Cut out the splines. I had a piece of walnut already cut to about 1/8" thick leftover from a ukulele side, but you could resaw (cut a slice) from any hardwood. The splines are easy to cut out on a band saw. Sand the splines so they fit snugly in the slots.
- Glue 'em in.
- Use a flush cut saw to cut off the excess and sand down. I always find this step inexplicably enjoyable.
NOTE: The cutting done in image 4 is NOT recommended. Although I was fine and had no issues, the box is NOT securely clamped into the jig and could have kicked back into me. In the future I would never cut splines like this. Let this be an example of what not to do. Please work safely, use clamps here. A wider jig meant for larger boxes would be even better.
Step 11: Edge-banding the Frame (optional)
Although not necessary, edge banding, or gluing a veneer to the edges of the plywood, is a great addition to make the frame that much more aesthetically pleasing. The edge banding does a good job of hiding the gaps and dowel holes from the previous steps.
I prefer iron on edge banding because it is simple to use. Just press with an iron and it's glued!
Don't forget to trim off the excess with an surprisingly sharp but also freakishly small exacto knife from Muji. (Highly recommended)
Please don't cut yourself.
Step 12: Cut Out the Parts for the Holders
Two sliding pieces hold the tuning forks in place. Cut out the pieces from plywood or any wood you have lying around. Pine is fine.
The central piece has a slot which perfectly fits the handle of the tuning forks. For this, just trace the handle on the piece with pencil, then cut with a bandsaw.
Cut smaller, then sand down. You can always take away material but you can't put it back.
Now is the time to glue the piece together. Clamp it lightly, don't use a lot of glue. Squeeze out could block the slot you just finessed.
Step 13: Drill and Set Threaded Inserts
The threaded inserts will hold the hand screws which will be used to hold everything in place.
Drill appropriate sized holes for each threaded insert. I bought two types for some reason:
1. The type that you pound in with a hammer
2. The type that you screw in with a long screw and two nuts.
I have to say, the second variety is easier to use. Just get all of that type.
Drill the holes, add a touch of epoxy, and then screw them in using a long screw with two nuts tightened against each other on one end. This process is ... hard to explain in words, and take a bit of practice, so I recommend trying it out first on a scrap of wood. This site was helpful: https://www.woodmagazine.com/materials-guide/fast...
QUICK TIP: Before setting the front inserts, wrap two tuning forks in plastic wrap and push them into the holders. This way, the threaded insert will not go too far in, blocking the entry. The plastic wrap stops the forks from sticking to the epoxy.
Step 14: Finishing Up
For the extra touch, I chose to properly finish the piece, to increase the tactile pleasure and make the walnut wood pop more.
Sand with fine sandpaper, wipe off the dust, and prepare the area for finishing.
You can use more labor intensive finishes like lacquer or polyurethane, which give exceptional results, but this piece doesn't need that much protection. I used Feed'n'wax, this mix of orange oil and wax that rubs right on. Not only does it smell amazing from the orange, but it really makes the grain pop. After drying a day, the surface is smooth and pleasant to touch.
Whatever finish you choose, tape off four small circles on the bottom, where you will put the bumpers. When the finish is dry, peel and sand lightly before pressing on the rubber bumpers. These are essential so that the box doesn't slide when you hit the forks.
Step 15: Inserting the Holder
The two holders should be done now. I cut out a "washer" from a scrap piece of wood and drilled a hole in it. You can use a real metal one too.
Just insert the holders and tighten the screws (but not so hard that the glue cracks). You should now have holders that accept a tuning fork and also slide up and down to adjust the height or distance. Success!
Step 16: The Laser Holder
I decided to design the piece in Fusion 360 and 3d print it since this was the perfect opportunity to make a custom piece. I had my neighbor Mr. Roberts print it for me - Thank you!!
The laser holder fits right in and can be tightened in place with the screws.
The bottom thumb screw goes into the threaded insert in the back piece. Next time, I would use a washer and longer screw to increase the clamping force. My design wasn't perfect in that regard.
Step 17: Step Back for a Moment
At this point, you have made it this far - step back and admire the simple design and craftsmanship you have put into it.
Pictured here in perspective, from the front, right, and back.
You're so close now.
Step 18: Prepping the Apparatus for Use
To prep the tuning forks, I cut out pieces 1/4" x 3/4" and just pressed them onto the tines. It's that easy.
As for setting up the apparatus, once again refer to the CONCEPT sketch.
Tips:
- This is surprisingly hard, but you can do it with patience. Don't give up so fast.
- I had the laser be always on by taping the button down. A clothespin might be able to do the same job.
- Set in two tuning forks you'd like to test, and screw them in tight. Adjust the positions so that the laser hits the first fork close to the center of the mirror, bounces off, hits the second fork close to the center of the mirror, and continues on, projecting onto the wall. The adjustment process will involve moving the laser, changing the direction it's pointing, and moving the forks too.
- The hardest part is getting the alignment right. Very often you'll have something move right when you don't want to, or the laser hits the edge of the mirror, not the center, causing a weird, distorted image.
- In the future it would be better to cut the mirrors slightly oversize to make it easier.
- Tape a flat, white poster paper to the wall to get a better image.
- Turn off the lights for the best image.
- As soon as the dot of light is visible on the wall, you're ready to go.
Step 19: Producing the Lissajous Figures
This is it! Now you will get the chance to reproduce an experiment that has fascinated curious minds for more than 200 years. To produce the curves, hit the tuning forks with either a mallet, wrench, or flick them with your nail (I prefer this technique), and watch the figure appear on the wall.
It's understandable why Lissajous and Bowditch may have been interested in these curves. There's something mesmerizing about this point of laser light, which expands into a line, and then suddenly into a smooth, oscillating curve, which you observe all the while listening to the harmony of the two tuning forks ringing loud and clear.
The spectacle is very hard to photograph, and I apologize for the "taken with a potato" quality of my pictures. While they're definitely better seen in real life, they're still very beautiful forms to admire.
You will notice the image oscillates between several stages. This is due to the fact that almost certainly one fork will be vibrating in a slightly different phase (or also frequency), which causes the image to shift, almost as if precessing. I think it's a cool effect.
I've always been a visual person, thriving on pictures to explain or model concepts, and this is no exception. Visualizing the combination of two objects in harmonic motion is a great way to see a practical application of parametric curves, as well as get to "see sound".
Try different frequency ratios to see what patterns you can get. Theoretically, if I have 9 forks, I could choose 2 to test in 9!/(2!7!) = 36 ways. Looks like there are plenty more combinations I have yet to try.
I hope you've enjoyed learning about physics, math, woodworking, and more. Feel free to comment any and all questions.
-Javier
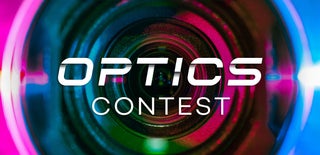
First Prize in the
Optics Contest