Introduction: Long-Lasting Leather Wallet
Do you own a wallet? I'm guessing over 98% of you do, and most of you probably have it on you right now. It keeps your most valuable items safe and close at hand, but is it built to last?
I do a lot of leatherwork, but my most popular items by far are wallets. I'll show you how I make wallets that can last for decades and only look better with age. The process isn't complicated, and the results are limited only by your own imagination.
I'm going to touch on a lot of different leatherworking techniques, but be aware that whole books have been written on these. This instructable will focus on bringing those techniques together to create a wallet.
All of the needed tools and materials are available at leather supply stores, such as Tandy Leather Factory.
Materials:
-4 oz. veg-tanned cowhide (for cover)
-2 oz. pigskin (for lining)
-Stout thread
-Contact cement
-Leather finish
Tools:
-See each step for the needed tools. Tools that are uncommon to find outside of a specialty shop are in bold. Most of what you need can be improvised to some extent, so there's no need to spend a fortune on tools.
Step 1: Plan Out Your Pattern
The first thing you'll want to do is decide what is going into your wallet and what the critical dimensions are. Today we're making a simple bi-fold wallet with pockets for cards and bills. A standard credit card is 3-3/8" x 2-1/8". Add a seam allowance of 1/8" to each side and 1/*" for "wiggle room", and we find that we need at least 3-3/4" of space for each pocket. We'll leave 1/4" in the middle to allow for folding. A Canadian bill is 6" x 2.75", so the overall length is OK, and we'll make the width a little bit taller to allow for the seam along the bottom, and a bit of extra space at the top.
Now here's an important tip: These are the dimensions for the inside of the wallet. The outside piece of leather will need to be about 1/4" longer, due to the thickness of the leather. It seems obvious, but it's easy to forget about this until your leather is cut and it's too late.
Draw up a complete pattern on paper, or use a drafting program and print it out. Hang on to this "master" copy to verify all your pieces are cut correctly.
I went ahead and added two overlapping card pockets on each side. The angled tops are just a style choice I like to use. Make them square if you like. Just be sure that enough of the card will stick out to allow you to remove it!
Step 2: Cut Your Leather
Lay out your pattern on the flesh (rough) side of the leather. Transfer your lines onto the leather using a pencil and ruler.
The leather can be cut with a sharp razor knife and a metal ruler as a guide. Disposable blades are especially good for beginners, as you don't have to bother with re-sharpening.
Sometimes the pigskin is just too supple to cut easily with a knife. Try a pair of sharp sewing scissors.
Test fit all the pieces. Make sure you have enough seam allowance and that the outer piece lines up with the inner lining when folded.
Step 3: Tool the Outside
You can imprint a pattern, or "tool", the outside of your wallet to give it a personalized style. Leather tooling is a subject for another instructable, but here's a rundown of the basics.
Create your design. This is where having a master copy of your pattern comes in handy. Make sure to allow for the stitching around the outside.
Dampen the leather with a sponge. Once the leather is wet, the surface will get stained easily, so avoid touching it.
Place a copy of your design over top of your leather and trace over the lines with a pencil. Remove the paper and you'll discover that the pressure of the pencil has left marks on the leather.
Use a swivel knife to slice through the surface of the leather over the lines. Some very nice designs can be made with just this tool.
The next step is stamping. First, thoroughly dampen the leather with a sponge. Wait about five minutes until the surface returns to it's original colour. This procedure is referred to as casing, and can be tricky. You want the core of the leather to be wet, but the surface dry. With experience you will learn exactly when the leather is ready.
Next, use an edge beveller and mallet to push down the edges of your lines, creating a 3D effect. There are hundreds of different stamping tool shapes, but most of the time, I just use the edge beveller. You can use just about anything to create a mark. Coarse sandpaper creates an interesting texture. The end of a wire or dowel can be used for circles. Use your imagination.
When you are satisfied with your design, allow the leather to dry completely.
Step 4: Sew It Up
The pattern in step 2 has dashed lines indicating where the stitching is done.
Take your top piece of leather, now dried, and slightly dampen the surface again with a sponge. Mark your stitching lines using a stitching wheel, or a something with equally spaced points, such as a fork. A needle and ruler will also work, although it will take longer. The stitching line should be about 1/8" from the edge. Place your stitch holes about 1/4" apart.
Note that we're leaving the middle of the bottom unstitched, to allow the wallet to fold.
Lay out all your pieces. Use a little bit of contact cement to tack the lining pieces in place.
Sewing is done with two blunt needles on one thread and an awl for making holes. As with tooling, sewing is a big subject that could have its own instructable. What we're using here is a basic saddle stitch, which is still much stronger than the lock stitch a sewing machine makes.
Start at the top left corner. Pierce a hole with your awl, then pass a needles from the front through to the back, and the other from the back through to the front. Pull the thread tight. Continue down the side and across the bottom until you get to the edge of the card pocket. For the last side of the pocket, start from the interior and just pierce through the lining leather. At the end of the stitching line, double back a couple of stitches. Finish with both ends of the thread in the bill pocket and snip them short.
Repeat the procedure for the right side, starting at the far right corner. The wallet won't lay perfectly flat, so it will be a little trickier.
Note that there is no need to sew the bottoms of the upper card pockets; the cement will do a good enough job.
Step 5: Crease and Trim
Fit a card into each pocket. Don't worry if you need to force them in; your leather and stitching is strong. With the cards still inside, fold the wallet closed and press it flat. Use some heavy books or something similar to keep it flat. While the books are shaping the outside, the cards are stretching the pockets. Leave your wallet like this for a day or so.
Once the wallet is nicely creased and flattened, inspect the edges for evenness. Trim them as needed so that the lining and outer layer are flush.
Step 6: Slick the Edges
"Slicking" is a process that smooths the edges of your leather and makes a project look cleaner. Essentially, you want to take all the loose fiber ends and compress them all together.
Lightly moisten one edge. rub swiftly back and forth along the length with a piece of coarse fabric while applying light pressure from each side. After a few minutes, the edge will be smooth and shiny. Repeat the process for all four edges.
There are a lot of different techniques for slicking the edges. You can cut a groove in a piece of hard material and use that instead of fabric, or you can purchase an "edge slicker" tool. I've seen dozens of different tools and techniques, all of which work and are correct.
Step 7: Stain and Finish
Now that your wallet is looking like a functional wallet, you can apply a stain if you like. I like to apply just a very light coat of water-soluble stain, so that the natural colour and grain of the leather isn't overshadowed. Some artists suggest applying a generous coat and wiping off the excess, but I like to apply it with a damp sponge or brush. This will water down the stain and accentuate the low spots from tooling. Experiment, as there are no rules. The elephant, map, and horse pictured in this step were all stained with the same bottle, using different techniques.
To seal the leather and make your wallet last much, much longer, apply a finishing coat. Do this whether or not you applied a stain. I use the "Super-Shene" brand from Tandy Leather. The leather will still darken and "age" nicely over time, which is a good thing.
In my experience, while a finishing coat doesn't make your wallet waterproof, it makes the outside a little more water-resistant. I've dropped leather items in puddles and, once dried out thoroughly, they were no worse for wear.
Step 8: Break It In!
Load up your wallet and stick it in your pocket. Take it everywhere with you. Leather is an amazing material. You will find that after a few days, everything in your wallet will fit there perfectly. Pockets that were a little too tight will stretch. The wallet will sit in your pocket like it was built for it.
Pictured in this step are before and after images of one of my first wallets. I've carried it with me every day for over three years.
There are no weak points to worry about. The outer cover won't flake away and the lining won't tear. I've never had a thread break on me, but even if it did, the stitches won't "unravel" like a machined stitch can.
This basic construction method can be used to create all sorts of leather projects. I use a larger one to store my passport and tickets when traveling. If you don't carry cash, forgo the bill pocket and add more space for cards. Experiment, because if you make it yourself, it can be exactly what you want!
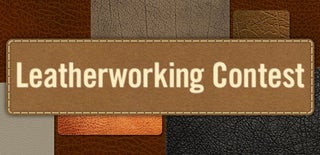
Runner Up in the
Leatherworking Contest