Introduction: Stacked Leather Knife Handle
You may have seen axes and knives with brown, striped handles. While modern copies may be made from plastic or composite material, that striped pattern was originally the result of stacked leather.
A stacked leather handle is incredibly comfortable and durable. It's also a great way to use up scraps of thick leather. It requires a fair bit of planning and some special tools and techniques, but the result is very rewarding and unique. As always, I've tried to provide alternatives to expensive tools and materials where I can. Remember, though, that the quality of your end product will depend on the quality of the material, skill, and time that you put in to it.
Step 1: Tools and Materials Overview
There are a lot of different options for the tools and materials you'll need. I'll get into specific requirements in future steps.
Tools:
- razor knife
- ruler
- rotary tool with drill bits and sanding drums
- sandpaper - various grits from 120 to 600
- knife vise:
- two thick 4" x 4" plates (UHMW, metal, or wood)
- 2' threaded rod (approx. 3/8" thick)
- 4 nuts and 4 washers that fit on rod
Materials:
- thick veg-tanned leather scraps (6-8 oz. or thicker)
- knife blade with hidden tang
- bolster material (I used tagua nut; hardwood is another fine choice)
- leather cement
- Gorilla Glue
Step 2: Choosing Your Knife Blade
If you're going to go through the trouble to make an awesome knife handle, you want to have a good quality blade. The crucial part when choosing a blade is that the tang, or metal part behind the sharp part that extends into the handle, must be as long as you want your handle to be, and be the type that is completely hidden inside the handle.
*SAFETY TIP: Before doing anything with your blade, cover the sharp bit with masking or painter's tape. There's just no need to risk damaging the blade, or yourself, while you work. Take a few minutes at the beginning to make the blade safe and have some peace of mind for the rest of the project.
I found that buying a complete knife was actually cheaper and more readily available that buying just a blade. I chose a knife from Mora. They are good quality, relatively inexpensive, and have a tang that is perfect for a stacked leather handle. After taping the blade, I carefully sawed and whittled away the wood handle until the tang was free.
Step 3: Prepare Your Leather Bits
Decide on the overall thickness that your handle will be, then add about a 1/4" safety margin. Draw this out. Now, measure the with and depth of your tang. In the centre of your drawing, draw the tang. It's important to make sure you always know where this will be.
Cut out a little template from scrap cardboard, including the tang-shaped hole in the centre, and use this as a guide to begin cutting your scrap leather into handle-sized pieces. Make sure you mark the centre hole on each piece.
If you don't have enough scrap, check out any deals on belt blanks or remnant bags before spending money on a whole big piece of leather..
Take care not to rush this step or try and include pieces that aren't quite big enough. Additionally, it's important that each leather piece has a uniform thickness. See the diagram. Even one bad piece can ruin the look of the handle.
To make the hole in each piece for the tang, I found it easiest to use a drill press and make a series of holes. The size of the hole can be a millimetre or two too big; When we compress the leather the hole will shrink a little, and there needs to be a little room for the glue. The important part is that the hole is centered and consistent in its placement.
Make enough leather pieces to make a stack a couple of inches longer than the knife tang. This will account for compression and the inevitable mistakes. Test fit the pieces on the tang to see if they're consistent. It should look absolutely nothing like a handle at this point.
Step 4: Prepare Your Bolsters
You'll need something solid on each end of your leather stack. This material can be anything you wish, but bear in mind that it can be hard to shape an extremely soft material like leather and a hard material at the same time to create one fluid shape. I chose pieces of tagua nut, also called vegetable ivory, for this handle. It's actually much harder than it looks, but still softer than metal. I'd recommend using hardwood.
Cut two pieces of your chosen material, sized according to how you want your finished knife to look. In general, you'll want both pieces to larger than your leather pieces. I made the top piece significantly longer so that I could make a finger guard. As with the leather pieces, it's important to make sure the sides are flat and the pieces are a uniform thickness throughout. You'll also need to drill or cut a hole for the tang. You can use the template you made earlier to help with placement. Dry-fit everything on the tang again. It might vaguely resemble a handle at this point.
You can do some initial shaping at this stage, but I found it easier to shape the whole handle as one piece once it's assembled.
Step 5: Make a Knife Vise
Here's where things get complicated. We need a way to clamp and compress the leather pieces while they're on the tang. The big pointy blade on the end makes this tricky with a normal vise. we're going to make a simple one with some threaded rods and UHMW (Ultra-High Molecular Weight Polythelyne) plates. The plates can be any material, as long as it will not bend or crack. I happened to have some UHMW on hand. It's easy to machine, but it's almost impossible to deform. If you want to use plywood, I'd suggest using 2 pieces of 1/2" ply laminated together for each side.
See the diagram above for vise assembly. As you can see, the vise is extremely simple. The key is to be able to compress the leather without the blade getting in the way. If you want to be an over-achiever, you could make the vise with four threaded rods, one on each corner, but I found that two rods do a more than adequate job.
Step 6: Stack Your Stuff
Soak your leather in a dish or bowl of water. DO NOT use a metal dish, as metal will blacken the leather. Let the leather soak completely through, until you can't see any air bubbles. A few hours at least.
You'll want to do this next part over a sink or bucket. Place your bolsters and leather on your tang and place in the knife vise. Tighten. TIGHTEN. Use a wrench. You should see water being squeezed out of the handle. Once the vise is as TIGHT as you can get it, let it sit for at least a few days. You don't just want the leather to dry, you want the leather to submit to its new shape.
Once a few days have passed, unscrew the vise and carefully take apart the handle. KEEP THE STACK IN ORDER. The leather has got used to its new shape and fits well with its neighbors. In fact, you'll have to pry them apart. Don't be sad, they'll be back together soon!
Now comes the gluing. Stack everything back onto the tang, applying a thin layer of leather cement between each layer of leather. Insert into the vise and tighten again. Let dry for about twenty minutes.
Take your now solid handle off of the tang. Apply Gorilla Glue to the tang, along with a few drops of water. Drip some water into the tang hole in your handle and put it back on the tang (for the final time, I promise). Clamp in the vise again (for the final time, I promise). Let the Gorilla Glue dry overnight.
Step 7: Shaping Your Handle
Your knife should now be a nice, solid, yet ugly, piece. There will probably be excess Gorilla Glue that has foamed up through the end of the handle. Carefully cut this away with a knife and sandpaper.
Now comes the fun part. Use a rotary tool with a sanding attachment to begin shaping the handle to your preference. My handles always end up on the big and chunky side, but I find that this fits my hand better than the sleek handles you see on most knives.
The leather will wear away quickly, so be careful and use a slow speed. A high speed can burn the leather, and a coarse sandpaper can shred a hole in your leather.
After you get a basic shape, switch to hand sanding. I used 120 grit for most of my shaping. It's a slow and messy process. Leather dust is somehow much worse that sawdust.
Step 8: Polishing and Finishing
Once you've got your perfect handle shape, polish with increasingly finer grits of sandpaper, down to 400 or 600.
If you've done any leatherwork before, you may be familiar with the process of burnishing. This is the process of rubbing the edge of a piece of leather to intertwine the fiber ends. This is exactly what we're going to do to the entire handle, since it's all edge. lightly moisten the leather and rub gently and quickly with a cloth. Be careful not to add too much water, as the leather will soak it up like a sponge.
You can add a layer of leather finish if you wish, although I found it wasn't necessary.
Congratulations! You now have a knife handle that will last a lifetime, be warm in the winter and cool in the summer, be easy to grip even when your hand is sweaty, and is uniquely tailored to your hand.
I was initially very careful with my first knife, but soon I started using it to whittle and split kindling. It has held up for years under regular use. Like any leather product, the handles get darker and develop a "patina" as they age.
You could use this same technique to make other items, like a USB drive or a paperweight. Have fun and please feel free to ask questions or leave feedback! Also, please consider voting for me in the Leather Contest. Thanks!
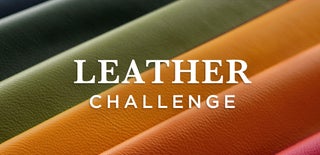
Runner Up in the
Leather Challenge