Introduction: Low Cost Bench Top Magnetic Particle Spectrometer (MPS)
Magnetic Particle Spectroscopy (MPS) is a relatively new technique which can be used to quantify the amount of Super Paramagnetic Iron oxide Nanoparticles (SPIOs) present in a sample. It can also be used to characterise SPIOs for Magnetic Particle Imaging (MPI). MPS systems are available to buy,however they are quite expensive but now you can make it yourself at a fraction of the cost by using off the shelf audio equipment and 3D printed parts to allow for an MPS costing under £1000.
We have broken this down into very small parts to make it easier to follow so please don't be too put off by the length. That said, working flat out it normally takes us about 3 days, including the printing, to complete a system once we have all the equipment assembled. So this perhaps is not an ideal project to start on the dining room table on Sunday morning.
BEFORE YOU READ ANY FURTHER, PLEASE MAKE SURE THAT AT ALL STAGES YOU READ ANY SAFETY INFORMATION WHICH COMES WITH THE EQUIPMENT. WE ASSUME THAT YOU ARE COMPETENT TO UNDERTAKE THE ACTIVITIES IN THIS INSTRUCTABLE AND WILL NOT BE HELD LIABLE FOR ANY INJURIES OR WORSE. THE FOLLOWING STEPS ARE A GUIDE ONLY. WE RECOMMEND CONDUCTING A DETAILED RISK ASSESSMENT FOR ALL THE PROCESS DETAILED HEREIN. WE HAVE COPIES OF THESE WHICH WE CAN SEND ON REQUEST AS A STARTING POINT [WITHOUT LIABILITY OF COURSE :-) ]. Right, now that's out the way, click on.....
Step 1: Gather the Components
Components needed for MPS Setup
- Signal Generator (We use an AFG-2225, but anything which can output sine waves in 100s of Hz should be fine)
- Power Amplifier (Behringer EP4000 Europower Amp, The bigger the better!)
- Pre-Amp (Stage Line MPA-102 Microphone Preamplifier, The lower the noise the better) + 9V batteries (4 needed to run Pre-Amp)
- 24 bit, 192,000 S/s Soundcard (Behringer U-PHORIA UMC202HD, The speed is needed for the higher frequencies and the bit resolution to collect small signals)
Parts needed to build MPS
- 500g 81/0.04mm Silk Covered Stranded Copper Litz Wire (If you can't get this exact makeup, aim for similar numbers and gauge of strands)
- 136mm (minimum) of clear Acrylic tube with OD 70 mm and 64 mm ID
- 97mmx194mm(minimum) of 3mm thick clear extruded acrylic
- 1-Part extruded acrylic bonder (or other means to securely join acrylic together. Try to avoid superglue)
- 5 x BNC Connectors (or other 2 pole connectors)
- 3 x Nuts for BNC connectors
- Metal box with dimentions 1.969" L x 1.969" W (50.00mm x 50.00mm) X 0.984" (25.00mm)
- PCB board
- Black shrink wrap 3.2mm 2:1
- Black shrink wrap 6.4mm 2:1
- Red Shrink wrap 6.4mm 2:1
- Insulation tape (we used black but don't feel constrained by that!)
- Masking tape
- 2 part rapid epoxy
- Retort stand and clamp
Leads and adaptors needed (length of leads may vary depending on how you have arranged your MPS setup):
- 3 x Male to male BNC connectors (or appropriate adaptors for your 2 pole connectors chosen in the last block)
- 2 x XLR male to Phono(RCA) Male leads. Here is a link for 2 x XLR male to 2 x Phono(RCA) leads,You will only need one of these(to connect the sound card to the other components, so if you have a sound card with 1/4in jacks you will need 2 x 1/4in jack to bnc etc.)
- 4 x 1M XLR leads (as before, make sure these are right for your chosen sound card and preamplifier)
- 2 x XLR male to Phono(RCA) Male leads. Here is a link for 2 x XLR male to 2 x Phono(RCA) leads,You will only need one of these.
- 1 x 1/4" Mono jack plug to Phono(RCA) plug lead(As before, make sure these are right for your chosen sound card)
- 4 x BNC to Phono socket adapters(as before, make sure these are right for your chosen preamplifier)
- XLR female to BNC female adaptor (as before, make sure these are right for your chosen preamplifier)
- 1 m long 4 mm plug lead-red (These are sometimes called banana leads)
- 1 m long 4 mm plug lead-black
- 0.5 m long 4 mm plug lead-red
- 0.5 m long 4 mm plug lead-black
Necessary Tools
- 3D printer ,We used a form 2 -> (You can also use an online service. We found surprisingly high metal contamination in all resins other than clear so please do not use other resins. Similarly, SLA is likely to have metallic contamination from the nozzle so is unlikely to work (but if you try and it does please let us know!))
- Soldering Iron, Solder and Flux
- Drill
- Heat gun-we used this one
- Laser cutter - Or access to a lathe, milling machine and competent plastic work skills :-)
- Wire strippers
- Side cutters
- 1ml syringes
- cotton buds
- paper towel
- vegetable oil
- Needles- 1.1x50mm
- A selection of small and larger files
- Oscilloscope (optional)
- Coil Winder (Optional)
Samples to test in the MPS
- SPIOs-We use Synomag-D 70nm-plain surface
- NMR tubes -to put the samples in (available second hand on ebay for a reasonable price)
Step 2: 3D Print the Receive and Cancellation Coil Bobbins
The receive(Recieve_coil.STL) and cancellation coils(Cancellation_coil.STL) are 3D printed from the STL files which are attached. We have also included the preform file with all the printer settings and supports for the receive coil (receive_coil_preform.form) as this takes a while to set up using preform.If using a form labs printer you will need PreForm to print the files.Also if using the from 2 or any form labs printer make sure to use the clear resin as other resins have been found to be contaminated with magnetic materials so will give signal when using the MPS.
The receive coil takes about 18 hours and the coil takes about 6 hours on the form 2.We are adapting the receive coil print to print in two halves so that that the supports are easier to remove. It is very much a work in progress but if you want to try it out, the stl files (receive_left.STL & receive_right.STL) are attached.
If using the form 2,it would be ideal to set the cancellation coil bobbin to print first thing in the morning then take out and set to print the receive coil bobbin overnight.
Whilst the receive and cancellation coil bobbins are printing make the transmit coil by following steps 3-15.
For more information on how to use the form 2 go to https://support.formlabs.com/s/topic/0TO1Y000000IvrUWAS?language=en_US
Step 3: Gather and Cut to Size Materials Needed to Make Transmit Coil Bobbin
You will need acrylic tube with OD of 70 mm and ID 64 mm with a length of at least 126 mm. The tube needs to end up with flat perpendicular edges on either end. We use a laser cutter to do this, so have to start with quite a bit of material either side to grip on the rotary stage. If turning, make sure to pare and smooth both ends.
We then laser cut the flat pieces from a 97 x 194 mm of 3 mm clear extruded acrylic. This will allow you to use the files attached. If cutting by hand you will probably need slightly more...
1) First cut the acrylic tube to a length 126 mm with engraving marks at 105 mm distance apart (see attached file transmittcoilbobbin_engraveandcut.cdr).If you don't have corel and inksape file (which is free software) is also added (transmittcoilbobbin_engraveandcut.svg).The red lines on the design are the engraving marks and the black lines are where the acrylic tube needs to be cut.The engraving marks are to place the bobbin ends in the correct position (see step 4),the length of the transmitt coil will be 105mm. You can do this on a laser cutter or with a lathe.
2) Cut out the bobbin ends from the 3 mm clear extruded acrylic (see file transmitt_bobbinends.cdr or transmitt_bobbinends.svg). Again this can be done using a laser cutter or with a lathe.
Step 4: Put Together Transmit Coil Bobbin
1) Place the bobbin ends on the acrylic tube within the engraving marks on the tube, matching up the gaps on the bobbin ends with the gaps on the engravings on the transmit coil bobbins. Be careful when doing so as it will be a tight fit but this is what you want.
2) Secure the bobbin ends on the transmit coil bobbin using 1- part extruded acrylic bonder (this actually is quite nasty so please make sure you follow the use instructions which are included with it. Not to be a bore but this really should have a COSHH assesment - some useful advice here - http://www.hse.gov.uk/coshh/essentials/index.htm)... to glue the acrylic pieces together.Do this by placing a needle on the end of a 1ml syringe, fill it with the acrylic bonder, place the needle in the gap between the pieces of acrylic and then apply a tiny amount to be just pulled by capillary action in between. If you've hand cut the acrylic, you need to make sure you have nice clean edges on the surfaces you're gluing so there aren't any big gaps, or the bonder doesn't work very well.
Step 5: Starting First Layer of Transmit Coil
Make sure you start the windings at the correct end of the transmit coil bobbin! The start of the transmit coil is the end where the bobbin end is at the very end of the acrylic tube.
1) Pull the start of the litz wire through the gap in the first bobbin end making sure there's plenty of length (approx 250mm) before starting to wind the coil.
2) Secure the litz wire on the acrylic tube with some tape (double sided is quite good, or masking. whatever you use it should be quite thin) at the start of the bobbin.
Step 6: Winding First Layer of Transmit Coil
- Wind 154 turns of the litz wire on the transmit bobbin then thread the wire through the slit on the bobbin end then secure on the bobbin end with tape.DO NOT CUT THE WIRE ONCE 1ST LAYER IS WOUND!!! Make sure the tape is tight and secure and you have some slack at the end of the coil as this will prevent the wounds unwinding.
We used a coil winder to wind the transmit coil but it is possible to wind by hand if you don't have one but of course this will take longer.The coil winder we used was a 200mm CNC Coil Winding Machine ,and the following settings were used:
- Bobbin width: 105mm
- Enter Total windings: 154
- Enter Wire Size: 0.67mm
- Desired Speed: 10rpm
If you're winding by hand it helps to secure the bobbin in a small lathe which you can turn by hand while you keep the wire under tension.
This needs to be as neat as possible. We don't have measured values but anecdotally, a coil with very neat windings tends to perform orders of magnitude better than a very rough one. The entire performance of the system rests with the efficiency of the transmit so take your time and get it right.
Step 7: Mix the Epoxy Resin
You will need some gloves (disposable nitrile ones are good as we have used here), 2 part epoxy resin and a petri dish or similar to mix the epoxy in.
1) Squeeze out a line of resin and a line of hardener, about 3cm long, from each tube. You are better to work in small batches as it sets quite quickly. If you find you are running out well before the resin begins to cure, you could increase the amount you mix in one go but be warned, it goes quite suddenly from liquid to solid.
2) Mix the epoxy together. It will first turn millky as the two components start to react, when it is fully mixed it turns clear again. If you don't get it to start to turn clear again, the epoxy will not be effective. For the rapid cure epoxies like this you need to mix it fairly vigorously (but carefully) to make sure that it is fully combined with enough time to use it.
Step 8: Cover the First Layer of the Transmit Coil With Epoxy
1) Keep your gloves on! Spread the epoxy onto the transmit coil with a spreader (you can use a bit of off cut PCB or the spreader that comes in the epoxy packet),to smooth the epoxy out. You are aiming for a nice even layer.
2) Once the epoxy you've mixed runs out or cures make some more (step 7) and repeat until the all of the litz wire is covered with epoxy.
3) Wait Approximately half an hour for the epoxy to cure. If one or both of your 3D prints are ready you could start removing the supports and cleaning the prints (see steps 16-18).
Step 9: Start the Second Layer of the Transmit Coil
1) Bring the litz wire across to the beginning of the windings and through the gap in the bobbin end at the beginning of the coil.
2) Secure with double sided sticky tape on the acrylic tube,then remove the white top layer of the double sided sticky tape.
3) Pull the litz wire back through the gap in the bobbin end and set up the litz wire as in step 5, ready to wind the second layer.
Step 10: Wind the Second Layer of the Transmit Coil
Wind 154 turns over the top of the previous layer of the transmit coil and secure at the end of the bobbin beyond the end cap with tape.If you can't quite reach 154 turns, somewhere between 145-154 is okay. A quick reminder on neatness.
Step 11: Epoxy the Second Layer of the Transmit Coil
1) Cover the second layer in epoxy (repeat steps 7 and 8 but for the second layer).
2) Once the epoxy is dry cut the litz wire at the end with plenty of length (about 250 mm), wrap around the end of the bobbin and tape down.
Step 12: Make Layers 3-6 of the Transmit Coil
You will need a total of 6 layers of the transmit coil which is made up of three, 2 layer coils. Repeat steps 7 to 11 twice to achieve this. Again, take your time to ensure the layers are neat and don't be tempted to start until the epoxy has set between layers or it tends to push out old litz wire (and make a bit of a mess!).
Once completed you should have 6 loose strands of litz wire, 3 on either end of the transmit coil.
Step 13: How to Solder Litz Wire
Litz wire is an amazing creation which brings some extreme efficiency savings as you start to get into the kHz ranges and with that improved signal transmission. However it is probably quite unlike anything else which you have soldered before! It is comprised of numerous enamelled copper strands (individually insulated) which are held together with a cotton wrap. Follow the steps below to minimising cursing at the wire.
1) First you will need to strip the cotton from the litz wire. The cotton should unwind relatively easily albeit a bit slowly. An alternative method is below which is a bit quicker, but does involve heating up the cotton with a soldering iron so please proceed with extra caution.
- Wet some paper towel and wrap round the end of the litz wire
- Heat up the the litz wire covered in the wet paper towel with a soldering iron with the end of a spool of solder at the end of the litz wire.
- Take of the paper towel and pull back the cotton. (you may need to snip the end of the litz wire where you heated up the end of the litz wire with solder)
2) If you have a temperature controlled soldering iron, now is the time to turn it up to 11 (or actually about 400). Once it's hot, Wrap the litz wire around the wire you intend to solder to and apply the soldering iron. Hold it for around 30 seconds. The enamel should start to bubble off and turn treacle brown. Once you can see this, apply the end of the solder spool again until it flows and drips off (be careful with where you have positioned it such that the drips don't burn you or start a fire. This carries away the residual resin and gives you a good connection. If you don't manage to connect all of the strands, the transmit won't work very well so again, take you time and get it right now (are you noticing a theme?!).
Step 14: Solder Banana Leads to the Opposite Ends of the Transmit Coil
You will need a red 0.5 m long 4 mm jack lead and a black 0.5 m long 4 mm jack lead to solder to the ends of the transmit coil which you made in steps 3-12.
Both ends of the transmit coil should have 3 sections of the litz wire. To solder these strands of litz wire to the 0.5 m long 4 mm jack leads,you will need to:
1) Cut and strip the end of one of the 4 mm jack leads.
2) Strip the litz wire as per the previous step
3) Place some shrink wrap (6.4mm ratio 2:1) on the end of the 4 mm jack lead.
4) Wrap the 3 ends of litz wire from one end of the transmit coil round the stripped 4 mm jack lead and then solder the 3 strands of litz wire to the 4 mm jack lead as per the previous step.
5) Pull the shrink wrap to cover the soldered litz wire and heat up the shrink wrap using a heat gun.
6) Repeat 1-5 shown above for the opposite end of the transmit coil. You should then end up with something which looks like the final picture in this section.
Step 15: Remove the Supports of the Receive and Cancellation Coil Bobbins
1) If you printed the bobbins using the form 2, the prints should have been washed with IPA and then further cured in the UV lamp if needed (see the form labs support for finishing for help in finishing of prints) before removing the supports.
2) Use side cutters to remove the supports from both of the prints taking care to remove all of the supports up to the surface of the print.
If you have printed the receive coil in two halves (see step 2) you will need to glue these together with a little more epoxy before moving onto the next step .
Step 16: File the Receive and Cancellation Coil Bobbins
Once the supports are removed use a fine file to carefully smooth down the prints.The parts that need to be smooth so that the thread system works, are the inside of the receive coil and the outside of the cancellation coil. Also the parts of the 3D prints that the coil are wound round need to be smooth. Finish with a fine grid sandpaper but be careful not to remove too much of the print itself, you are just trying to remove the supports. If you printed with an FDM printer, you will need to check that the parts fit into each other well and may need to play with scaling.
Step 17: Clean the Receive and Cancellation Coil Bobbins
To clean the prints use cotton buds and some oil (vegetable oil works fine).
To make sure that the cancellation coil fits inside the thread of the receive coil keep filing and cleaning the inside of the receive coil with a cotton bud and oil. Make sure the cancellation coil is well lubricated by occasionally twisting it inside the receive coil. Once the cancellation coil can go far enough in that it leaves 3 ridges outside of the receive coil smoothly, no more filing is needed. Be careful not to remove any of the thread. it needs to be a smooth but tight fit or you will get poor cancellation later on.
Step 18: Starting to Wind the Receive Coil
This is very much like winding the transmit but for completeness... pull the litz wire through the hole at the top of the bobbin and secure the litz wire leaving plenty of length (enough to reach to the bottom of the 3D print and then about 120mm) at the top part of the print with some tape.
Step 19: Wind the Receive Coil
1) Wind 20 turns in a clockwise direction,if you can't quite get 20 turns 19 is fine. 18 is not...
2) Secure the litz wire on the bottom bit of the 3D print, then cut the litz wire with plenty of length (enough to reach to the bottom of the 3D print and then about 100mm).
Step 20: Epoxy the Receive Coil
1) Cover the receive coil in epoxy (see step 7 and 8 for help on mixing epoxy and covering a coil with it).
2) Put the coil somewhere safe on a surface that doesn't mind a potential drip of epoxy on it (another good reason not to do this on the dining room table!).
3) Leave to cure. While the epoxy is curing move onto the next step.
Step 21: Starting to Wind the Cancellation Coil
1) Secure the end of the litz wire on the thread part of the cancellation coil leaving plenty of length(enough to reach the bottom and about 120mm).
2) Pull the litz wire through the hole at the bottom of the cancellation coil.
3) Pull the litz wire through the hole at the top of the coil bobbin and through the slit at the top.
Step 22: Wind the Cancellation Coil
Do not start to wind as in previous steps! (you thought you'd got this now didn't you!).
1) Wind the same number of turns on the cancellation coil as achieved on the receive coil (19 if you only managed 19) in an anticlockwise direction (opposite to the receive coil).
2) Pull across the litz wire and then secure with some tape (insulation tape works well here) leaving plenty of length (enough to reach to the bottom of the 3D print and then about 100mm).
Step 23: Epoxy the Cancellation Coil
1) Cover the cancellation coil in epoxy (see step 7 and 8 for help on mixing epoxy and covering a coil with it).
2) Put the coil somewhere safe on a surface that doesn't mind a potential drip of epoxy on it.
3) Leave to cure. While the epoxy is curing move onto the next step.
Step 24: Pull the Litz Wire Through the Top of the Receive Coil Bobbin
Remove the tape and pull both of the ends of the litz wire through the hole at the top of the coil.
Step 25: Solder Copper Wire to the Ends of the Receive Coil
1) Once the litz wire is stripped as per step 13, solder one end of the receive coil to insulated copper wire (approx 23 cm length)
2) Cover the soldered wire with some heat shrink (black 6.4 mm ratio 2:1, (green and yellow is used here in the photo as we didn't have any black left)) and heat up with a heat gun to an appropriate temperature as specified in the data sheet for the heatshrink you purchased.
3) Repeat steps 1 and 2 shown above for the other end of the receive coil. It should look like the final picture in this section when you're done.
Step 26: Solder a BNC Connector to the Ends of the Receive Coil
1) Place some heat shrink on the insulated copper wire (black 3.2 mm ratio 2:1) soldered to end of the receive coil at the start (the top) of the receive coil.
2) Solder the insulated copper wire in which you placed the heat shrink on to the central pin of the BNC connector.
3) Once the soldered bit of wire has cooled down push the heat shrink down to cover the soldered section so the middle pin of the BNC is separated from the outer pin.Then heat up with a heat gun.
4) Solder the other length of insulated copper wire to the outer pin of the BNC connector.
5) Put some insulating tape round both of the insulated copper wires.
Now you have completed the receive coil construction. Congratulations. Check it looks like the last photo in this section, then time for a cuppa.
Step 27: Pull the Litz Wire Through the Bottom of the Cancellation Coil Bobbin
1) Remove the tape and take the top end of the litz wire out of the middle of the bobbin and thread through the hole at the bottom of the coil. Also thread the litz wire through the hole at the bottom of the coil. Keep going until they appear at the end of the thread...
2) Pull both ends of the litz wire through the hole at the bottom of the thread until they are just tight
Step 28: Solder a BNC Connector to Both Ends of the Cancellation Coil
1) Repeat step 25 and 26 but for the cancellation coil (MAKE SURE THE ENDS OF THE CANCELLATION COIL ARE SOLDERED TO THE BNC CONNECTOR THE SAME WAY ROUND AS WITH THE RECEIVE COIL or your cancellation wont work!)
2) Put some tape (insulation tape works well here) round the bottom of the thread on the cancellation coil to hold it in place.
It should look like the photo above. If it does then that concludes the coil hardware section of the instructable! Yay. Too soon for another cuppa? Me thinks not :-)
Step 29: Make a Box to Connect Receive Coil to Cancellation Coil
You will need a box with dimensions 1.969" L x 1.969" W (50.00mm x 50.00mm) X 0.984" (25.00mm) or something similar and some BNC connectors and some nuts to lock the BNC connectors in place (see step 1 for links). We used a die case box here but it doesn't really matter (cardboard is probably a poor choice but ABS would be good)
1) First drill 3 holes with Diameter 12.5 mm in the box.You will need a hole drilled in the middle of 3 of the 4 sides.Then mark which hole is which,B is in the middle with A to the left and C to the right when looking at the top of the box (see the images for help).
2) Insert the BNC connectors through the holes in the box making sure A and B are placed so that the pins are facing up and the pins are facing down for C.
3) Screw the nuts onto the BNC connectors to secure them.
Step 30: CHECK THIS STEP PLEASE-Solder the Connections in the Box and Screw Lid On
The BNCs which we use and recommend have a gold inner leg and a silver outer leg. Because yours might not we have included both below.
1) Connect the outer (silver leg) of B to the outer (silver leg) of C by soldering the two legs together,Once soldered cut any excess leg length off.
2) Connect the inner (gold leg) of B to the outer (silver leg) of A by soldering the two legs together,Once soldered cut any excess leg length off.
3) Use a small piece of PCB (approx (12x10) mm) to connect the inner (gold leg) of C and the inner (gold leg) of A. The PCB offers a more secure connection than wire which can lead to some pesky microphonics so substitute this at your own risk.To make it easier you may want to hold the piece of PCB in place with a crocodile clip (do not touch while soldering though as metal conducts heat rather well!) while you solder the legs to it.
Once soldered each connection cut any excess leg length off. If you've used a metal box make sure no wires are touching or, or could touch it when you put the lid on)
4) Screw the lid on to the box and label A,B and C on the lid and the bottom of the box.
Step 31: Connect the Transmit Coil to a Clamp Stand
So that the transmit coil is lifted of the surface use a clamp stand,clamping over the transmit coil windings carefully so as not to damage them.
Step 32: Place the Receive Coil Inside the Transmit Coil
It should fit snugly with a little pressure, however if it is too tight, sand it down with a fine grit paper, a little at a time. If it is too loose, try putting some tape (Insulation tape works well) round the top part of the bobbin that sits inside the transmit coil. It should remain centred when free standing.
Step 33: Insert the Cancellation Coil Into the Screw Thread of the Receive Coil Bobbin
Insert the cancellation coil so that you can see 3 turns of the thread at the bottom and then lower the clamp down so that the cancellation coil is only about 1 cm from the base of the clamp.
Step 34: Connect the Cancellation and Receive Coil to the Box Made in Steps 30 and 31
You can either plug them into the box directly by using a Male to Male BNC adaptor or you can use some BNC leads:If you use leads, make sure they are the same length.
- The receive coil is plugged into A of the box.
- The cancellation coil is plugged into B of the box.
- Connect C to the input of the pre-amp (MPA-102) using a BNC male to XLR male lead (for this you will need An XLR male to phono plug lead and an BNC to phono socket adapter. Alternatively use some other cable assembly which is correct for your pre-amp).
Refer back to step 1 for an overview of the system for more details.
Step 35: Connect the Output of the Pre-amp (MPA-102) to the Sound Card
- Using an XLR lead connect the output of the pre-amp (MPA-102) to input 2 of the sound card (UMC202HD).
- The soundcard needs to be plugged into the PC you will be collecting the MPS data on.
For the complete MPS setup refer back to step 1
Step 36: Connect the Transmit Coil to Input 1 of the Power Amplifier (EP4000)
Power amplifiers such as this have the potential (well current ;-) ) to kill. Follow the instructions which come with it carefully and heed any guidance therein. If you are not sure, or are not confident do not proceed. If you are changing the DIN switches, make sure the amplifier is off. If you are connecting leads, make sure the amplifier is off. If you are not using the amplifier make sure the amplifier is off.
- Connect each end of the Transmit coil to 1m long 4mm jack leads and connect to the power amplifier in bridge mode.
- Mode switches 4 and 5 on this particular amplifier need to be off while the rest should be switched on to achieve this. if you can't figure out what your switches should be if you use a different amplifier drop us an email or a comment and we'll do our best to help you out.
For the complete MPS setup see step 1
Step 37: Connect the Signal Generator(AFG-2225) to the Input of the Power Amplifier(EP4000)
Using a 1/4" male stereo jack to BNC male lead, connect CH1 of the signal generator (AFG-2225) to input 1 of the power amplifier (EP4000) (for this you will need An 1/4" male stereo jack, XLR male to phono plug lead and an BNC to phono socket adaptor).
For the complete MPS setup see step 1
Step 38: Connect CH2 of the Signal Generator to the Soundcard
Using an XLR male to BNC male lead connect Channel 2 of the signal generator (AFG-2225) to Input 1 of the soundcard (UMC202HD) (for this you will need An XLR male to phono plug lead and an BNC to phono socket adapter). if you used a different signal generator with a single output you can achieve the same thing with a suitable attenuator. If you do this, please be careful not to overload the sound card.
For the complete MPS setup see step 1
Step 39: Set the Outputs for the Signal Generator(AFG-2225)
Our prefered settings as a starting point are as below. Keep the frequency of channel 1 and 2 the same but you night want to play a little with the amplitudes if you have used a different power amplifier.
The settings for channel 1:
- Frequency: 170Hz
- Amplitude: 800mV
The settings for channel 2:
- Frequency: 170Hz
- Amplitude: 600mV
Step 40: Optimise the Position of the Cancellation Coil
Adjust the position of the cancellation coil by twisting the cancellation coil until you get the smallest residual signal possible from the MPS.
You can do this by either using audacity (see steps 41-44) or plugging into an oscilloscope (see steps 45-47):
If using audacity, monitor the loudness of the signals and stop when this reaches a minimum
If using an oscilloscope connect the output of the pre amp (MPA-102) straight into an oscilloscope and stop adjusting once the residual sinusoidal signal reaches a minimum
Step 41: Optimising Cancellation Coil Position-Using Audacity (1)
Step 42: Optimising Cancellation Coil Position-Using Audacity (2)
Turn on the power amplifier (EP4000) and turn up the gain on channel 1 about halfway (~24dB) .
DO NOT LEAVE THE AMPLIFIER ON LONGER THAN 30 SECONDS ON GAIN=24dB UNLESS YOU HAVE COOLING (SEE STEP 55) OTHERWISE THE TRANSMIT COIL WILL OVERHEAT
Step 43: Optimising Cancellation Coil Position-Using Audacity (3)
Turn up the gain on the soundcard (UMC202HD) until it saturates and a red light appears, then turn down the gain till the light goes off.Do this for both input 1 and 2 of the soundcard.
DO NOT LEAVE THE AMPLIFIER ON LONGER THAN 30 SECONDS ON GAIN=24dB UNLESS YOU HAVE COOLING (SEE STEP 55) OTHERWISE THE TRANSMIT COIL WILL OVERHEAT
Step 44: Optimising Cancellation Coil Position-Using Audacity (4)
1) Adjust the position of the cancellation coil by twisting it up and down (See step 40)
2) As you adjust the cancellation coil the green bar next to R with get larger and smaller,when this is at it's smallest stop adjusting the coil.
If you have not cancelled it within 30 seconds, stop wait for 4 minutes and then carry on with cancellation.
If you have chosen this method to adjust cancellation coil it would be easiest to test the MPS using audacity (Step 49).
DO NOT LEAVE THE AMPLIFIER ON LONGER THAN 30 SECONDS ON GAIN=24dB UNLESS YOU HAVE COOLING (SEE STEP 55) OTHERWISE THE TRANSMIT COIL WILL OVERHEAT
Step 45: Optimising Cancellation Coil-Using an Oscilloscope,setting Up
- You will need an XLR female to BNC male lead (for this you will need An XLR female to phono plug lead and an BNC to phono socket adapter). Using this lead connect the output of the Preamp(MPA-102) into the oscilloscope.
- Make sure CH1 of the signal generator is on (CH2 should also still be on but for cancellation you only need CH1 to be on)
- The oscilloscope needs to be on 1ms/div and 10mV/div for x and y respectively
Step 46: How to Optimise the Position of the Cancellation Coil Using an Oscilloscope
1) Turn on the amplifier(EP4000) and put it at 10dB and you should see a sinusoidal signal on the oscilloscope.
2) Adjust the cancellation coil (see step 41) to reduce the sinusoidal signal to a minimum:
- As you adjust the cancellation coil the signal will either get larger or smaller.
- Adjust the position of the coil such that this signal gets smaller, once you have reached the smallest possible amplitude of this signal stop and turn off the amplifier.
If you can feel transmit coil getting warm turn off amplifier and wait 4 minutes before continuing cancellation
DO NOT LEAVE THE AMPLIFIER ON LONGER THAN 30 SECONDS ON GAIN=10dB UNLESS YOU HAVE COOLING (SEE STEP 55) OTHERWISE THE TRANSMIT COIL WILL OVERHEAT
Step 47: Finish Optimising Cancellation Coil Position Using Oscilloscope
1) Gradually turn up the gain on the amplifier (EP4000) up to halfway (Gain 24dB) and on each new gain, adjust the cancellation coil to reduce the sinusoidal signal to a minimum (Repeat previous step (step 46) for each new gain) (If you turn up the gain on the amplifier and the signal is still a straight line then turn up again (and feel smug at how good at cancellation you are)).
2) Once on 24dB reduce the volts/div on the oscilloscope to 5mV and adjust cancellation coil to reach a minimum.
If you have not minimised the signal within 30 seconds, or can feel transmit coil getting warm turn off amplifier and wait 4 minutes before continuing cancellation.
If you have chosen this method to adjust cancellation coil it would be easiest to test the MPS using an oscilloscope (Step 50).
DO NOT LEAVE THE AMPLIFIER ON LONGER THAN 30 SECONDS ON GAIN=24dB UNLESS YOU HAVE COOLING (SEE STEP 55) OTHERWISE THE TRANSMIT COIL WILL OVERHEAT
Step 48: Test the MPS
So now the MPS needs testing. Put 0.2 ml of stock of the SPIOs straight into an NMR tube.You can either test the MPS using audacity (step 49) or with an oscilloscope (step 50).
To test the MPS:
1) Once cancelled (steps 40-47) place the sample of the stock of the SPIOs in the sample chamber within the receive coil of the MPS.
2) Turn up the Power amplifier halfway (24dB) and look at the signal generated by the SPIOs,this signal should disappear when you remove the sample.
DO NOT LEAVE THE AMPLIFIER ON LONGER THAN 30 SECONDS ON GAIN=24dB UNLESS YOU HAVE COOLING (SEE STEP 55) OTHERWISE THE TRANSMIT COIL WILL OVERHEAT
Step 49: Test the MPS -Audacity
If you optimised the position of the cancellation coil using an oscilloscope you will need to unplug the oscilloscope and connect the output of the pre-amp (MPA-102) into input 2 of the soundcard using an XLR lead as seen in step 35.
1) Once the sample of SPIOs is inserted in the sample chamber and the amplifier is turned up halfway (see previous step (step 49) press the record button and record for 2 seconds.
2) Take the sample of SPIOs out and hit stop after another two seconds.
3) There should be 2 seconds of signal followed by 2 seconds of no/very little signal.
4) Zoom in on the section of large signal,you should get a signal that looks similar to that shown on the previous step (step 48).The signal received from synomag-D 70nm SPIOs using the MPS shown in this instructable is shown in the pictures above. If you have something like this your MPS works, congratulations and welcome to the MPS club!
DO NOT LEAVE THE AMPLIFIER ON LONGER THAN 30 SECONDS ON GAIN=24dB UNLESS YOU HAVE COOLING (SEE STEP 55) OTHERWISE THE TRANSMIT COIL WILL OVERHEAT
Step 50: Test the MPS -Oscilloscope
1) Plug into oscilloscope and turn up volts/div to 100mV.
2) Turn the power amplifier on and turn up the gain to 24dB as done in step 42.
3) Place the sample of SPIOs (0.2ml of synomag-D 70nm in an NMR tube) into the sample chamber.
4) Look at the signal produced by the SPIOs (an image of this is shown above),it should look similar to the example of what the signal should look like in step 48.
5) Remove the sample of SPIOs from the sample chamber,the signal produced by the SPIOs should now disappear.
DO NOT LEAVE THE AMPLIFIER ON LONGER THAN 30 SECONDS ON GAIN=24dB UNLESS YOU HAVE COOLING (SEE STEP 55) OTHERWISE THE TRANSMIT COIL WILL OVERHEAT
Step 51: Collecting MPS Data
1) Make sure the project rate is on 96000Hz
2)Set the gain on the soundcard for the SPIO signal (gain 2) : Place the highest concentration of SPIOs you will be testing and turn on the amplifier(EP4000) to the gain you will be using and turn up the gain on the soundcard on channel 2 until a red light comes on (this means it's saturating) and turn down slightly.This is so that your signal doesn't get clipped.
3) Record MPS for 10 seconds on audacity, the record and stop buttons are on the top left.
4) To save this data click file,then export,then export as WAV.
5) Make sure the file is saved as a "WAV (Microsoft) signed 24-bit PCM". (another tab "edit Metadata tags" will then pop up just click "ok")
DO NOT LEAVE THE AMPLIFIER ON LONGER THAN 30 SECONDS ON GAIN=24dB UNLESS YOU HAVE COOLING (SEE STEP 55) OTHERWISE THE TRANSMIT COIL WILL OVERHEAT
Step 52: Analysing the Data Using Matlab
Attached are two Matlab programs you will need:
- Get_Audio_PSD.m is to get the power spectral density of the wav file containing the MPS signal you recorded so you can have a look at the harmonics in the MPS signal.
- Get_Audio_peaks integrates the peaks at the odd harmonics of the drive frequency (in this case 170Hz)
If you don't have matlab, you should be able to port the code to python. If you do, let us know!
Step 53: Analysing the Data- How to Use Get_Audio_PSD.m
1) To run Get_Audio_PSD.m type into the Matlab command window Get_Audio_PSD('filename of your MPS recording') and then press enter.
2) You will then get a plot of the Power spectral density of your MPS data showing the odd harmonics of the MPS signal (Be aware this is a log scale!).You can zoom in onto the peaks to get a better look.
Step 54: Analysing the Data- How to Use Get_Audio_Peaks.m
1) To run Get_Audio_Peaks.m and then plot the peaks found using the program type into the command window:
pks = Get_Audio_Peaks('filename of your MPS recording', 12)
plot(1:2:length(pks), pks(1:2:end, 2), 'ko')
xlabel('Harmonic number k')
ylabel('log of sum of harmonic power spectral density, dB')
3) This will display a string of numbers and then bring up a plot of the integrals of the peaks at the odd harmonics of the drive frequency (in this case 170Hz) against the harmonic number,k. Again like with the previous step you can zoom in to get a better look.
And that's it! You should be able to play with different concentrations of samples and get corresponding differences in peak heights, or change to a different SPIO and look at the difference in the harmonic amplitudes. If you make one, pop up in the comments and let us know! There are a couple of optional steps which follow if you need them. Thanks for reading and happy building!
Step 55: Optional - Cooling
You may need cooling if your finding the transmit coil is getting hot, or if you want to be able to make longer measurements. It should be fine if you keep the amplifier at or below 24dB with 800mV or below from the signal generator and don't leave it on longer than 30 seconds with a minimum of 4 minutes with the amplifier switched off before you turn on the amplifier again. However if you are exceeding this you may want to cool the MPS by covering the transmit with piping and have a flow of chilled water through the tubing. In theory, you could air cool the transmit coil but we have found this to be ineffective for heavy use.
Step 56: Optional - Shielding
You can collect MPS data without shielding. However depending on your environment, you may pick up some noise and may want to shield from this.To do this you will need to shield it within a copper box.The thickness of the copper will depend on the frequency you use, this MPS works best at 170Hz which corresponds to 25mm thickness of copper! You will notice this is probably not practical. As you go up in frequency you will find it heads towards a point of becoming realistic. On the plus side, the lower you are in frequency (down to the dreaded 50/60Hz) the less of a problem you should have with noise.
If you want to make a shield, use a calculator like this one and enter the material you want to use and your frequency (for this example its 0.000170MHz) and then multiply the resulting thickness by 7 for excellent shielding or 5 for a reasonable shielding.
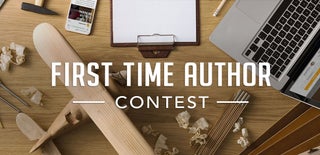
Participated in the
First Time Author Contest