Introduction: Make Accurate Dowels
Store bought dowels can be problematic, they can be expensive, inaccurate as they're often made from not-fully-dried wood, and they can be limited to just a few species - locally I have access to Tasmanian Oak and Pine dowels only.
Making your own lets you use contrasting or complimentary woods, make them from scrap, or custom sizes otherwise unavailable.
Step 1: Tools and Materials
You will need
- Wood - hardwood, softwood, heck even plywood will do if you laminate.
- You'll need something for the jig (~200mm x ~45mm x ~90mm used in my example, you'll need larger for larger dowels)
- Something for the dowels
- Some scrap plywood to clamp across your router table that the jig is screwed into
- Forstner drill bit in the diameter you want the dowel
- "Complimentary" forstner bit to match the dowel (more on that later)
On the machine front, you'll want...
- Table Saw
- Drill press
- Forstner bits
I used - Router/Router table
- Router bit - it doesn't have to be any particular type, a "regular" straight bit works fine
I'm a big fan of this 1/2" spiral upcut bit
To clarify that a little, if you want a 19mm (~3/4") dowel, you'll need a 19mm forstner bit for the outfeed, and a 28mm for the infeed. More details provided in the next step.
Step 2: Lets Get Mathematical
To make the dowels, we feed square stock through a block, over a router table. That requires a bit of maths to get all the bits and pieces lining up right.
If you want a 19mm (~3/4") dowel, you'll need a 19mm forstner bit for the outfeed. For the infeed, you need a drill bit that'd match or exceed (slightly) the diagonal of the dowel size we want.
This works out at roughly diameter * 1.4, which gets us to 26.6mm.
If you want to be more accurate, use
InfeedDiameter = DesiredDowelDiameter * √2
As such a drill bit doesn't exist, the next closest thats larger is 28mm. Be aware that just because a drill bit says its X size, doesn't mean its true. On a scrap, drill a hole and measure with calipers - it may vary by +/-0.5mm and your calculations should be adjusted for the true diameter. That solves the first problem, but we can't have stock thats sloppy inside the infeed otherwise the size of the hole doesn't matter.
InfeedDiameter / √2
That gives us 28 / √2, which comes to 19.79mm, meaning we have to prepare a slightly-larger-than-expected blank.
Step 3: Drilling & Mounting
Once you've got your block, and have marked out all sides, at the drillpress you can drill holes for..
- infeed (the bigger hole),
- outfeed (the desired diameter),
- "escapement" (of chips) & router bit access - make these larger than the bit you're going to use to avoid too much jamming
- Mounting holes for bolts
You can then screw/bolt/whatever it to a longer piece of plywood which can be clamped at the router table. By using a "standard" (standard to you) placement of the mounting bolts, you can create multiple routing blocks and swap out for different size dowels and reuse the piece of plywood.
Step 4: Prepare Your Dowel Stock
You'll want to cut your dowel stock longer than you need so you've got something to grab onto to twirl around, and you'll want to cut it to the dimensions in the previous step. In my case, 19.79mm square.
The easiest/best way to do this is with a tablesaw using a featherboard to keep the pressure even.
Step 5: Make the Dowel
The square stock gets turned round by rotating it against the cutter - in this case/setup this works to be spinning it anti-clockwise.
The router bit needs to be raised up to the height of the outfeed hole.
The easiest way to drive the dowel is using a cordless drill with a socket attachment, but you can rotate it by hand. Once you get to a certain diameter dowel, you'll have trouble actually finding a socket that large, so you might consider cutting a tenon on one end or even drilling and installing a smaller dowel that you can just grab in the chuck.
Once you've got your height set, turn the router on, and slowly feed the square stock through the infeed hole, into the cutter, while rotating (at up to 500rpm).
Don't force it through, you'll feel it go through (or not if you've made mistakes).
On the other side should be your accurate sized dowel!
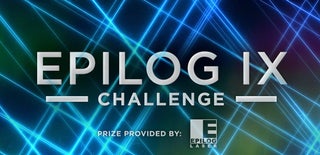
Participated in the
Epilog Challenge 9