Introduction: Make a Gig Ready Travel Bass Guitar With Case
I decided to turn a cheap bargain bass into a travel bass that I could use to practice while on the road and even play at gigs if needed. Other travel bass guitars run $200 or so for cheap ones that do not work well in gig settings or upwards of $800 for decent quality travel guitars. I built this one for less than $100 including the travel case and it sounds just as good as any of my other (economy) basses.
Supplies
- Bass to start with
- Sandpape
- Glue
- Nails
- Paint
- Tape
- Travel case
- Elbow grease
Step 1: Find the Donor Bass
The first part is to find a bass that can be purchased for a good price and does not need too much work. I found this Washburn on FB Marketplace for $45. It came with most everything I was looking for and I couldn't beat the price. Sold!
Step 2: Disassemble the Bass
Take the donor bass apart. Watch where everything goes and keep track any missing or damaged parts. In my case everything was present except for a back plate. I will make that later. This is also a great time to give everything a good cleaning.
Step 3: Mark Your Cut Line
What makes this project work is the smaller body. Establish the line you intend to cut. I prefer to use thin painters tape like this. You could also use a pencil or markers.
Step 4: Cut the Body
I used a scrollsaw for this.
Step 5: Build a New Panel for the Electronics
During the cut of this body I cut away part of the electronics pocket. This left an open space where the side wall used to be. It is time to add a new side wall. I used part of the cut away body since it was already the perfect size, shape and the same material.
I clamped the body to my workbench, used a chisel to create some new grooves for the panel to fit into and then trimmed the new panel until it fit close to perfect.
Step 6: Secure the New Panel
It is important to have a really good connection to the existing body for this to last. I start by gluing the part in place.
I also wanted a mechanical connection so while the glue is curing I drilled 6 holes into the body through the panel. Drilling these holes is critical if you do not want the panel to split when you add the nails. Use a drill bit slightly smaller than the nails.
I hammered the nails in gently and then used a center punch to countersink them in about 1/8 of an inch as I will be shaping and sanding this panel.
I did some sanding here to get the edges pretty flush and then added auto body filler to all new joints so I could sand them smooth and make it look like it was always this way.
Step 7: Make New Back Panel
I used some MDF panel scraps I had laying around and shaped the new back cover panel. I then added some more body filler to make sure the edges were very clean.
I will leave the cover panel in place while I sand and paint the guitar. Later I can use a razor blade with a small hammer to cut in the new edges and then a little sanding and it will fit like new.
Step 8: Paint ... Choices, Choices, Choices
The hardest part about paint is choosing the color. In my case I went through several different colors and then ended up choosing all of them (kind of). Choose whichever color works best for you. You can always sand it down and paint it again.
I have painted several guitars and you can use all kinds of paints, even lacquer, but the most important things to remember are:
- Start with a well-sanded surface. I like to finish with 400-600 grit before paint.
- Paint with several light coats.
- Either let each coat flash cure (10 minutes) before painting the next or wait for a full cure (24-48 hours). Do not use a heater as this will dry the outside coat before the inside coat can cure and cause bubbles.
- Once your light coats get full coverage then wait for a full cure.
- Wet sand (600,800,1000 grit) the surface until smooth.
- Repeat steps 2-5 until satisfied.
- Spray clear on surface. Again do steps 2-5 but I use 1000,2000 grit for this.
- Polish with autobody polish compound for final gloss.
When I am doing a regular paint job I follow these steps. This ended up not like a regular paint job.
Step 9: This Should Have Been the Last Painting Step
Not happy with the red color I decided to add some design to the body. I used tape to layout a nice stripe pattern and some different colors to achieve a kind of flame effect.
If all went well I would have followed my usual practice for clear coating the body at this point and then moved on to reassembly. But something went VERY wrong.
Step 10: I Am Still Working on Recreating This
I washed the body, wet sanded it, dried it and then sprayed my first coat of clear .... and ... it immediately started wrinkling. I sprayed a bit more and it kept wrinkling. Then for fun I decided to spray black paint on it figuring I could sand it all down later and see some cool pattern. I then walked away.
10 minutes later I walked out to find the black paint had settled into the valleys of the clear wrinkles and I had this kinda cool texture. It looked a lot like scales.
I liked it. The flame stripes underneath looked cool and I decided to leave it this way. IF it would stick.
I added coats of clear (somehow these coats were smooth) and then over the next 4 o5 days I made sure it cured in a warm room. A week later it was cured and very durable.
A true one of a kind paint job.
Step 11: Finish the Travel Bass
I cleaned the fretboard and polished all the rest of the parts of the guitar and then reassembled the whole thing.
I changed the wiring to a two knob set up with one knob for volume and one for tone.
I ordered this bag to carry it in.
I have travelled with this and it is much easier than my bigger bass bag and I have played the bass with my band and it sounds fantastic.
One note, you will likely get questions about what is inside the bag from security (being a gun case) but it only gives me the chance to show off this guitar which always gets compliments.
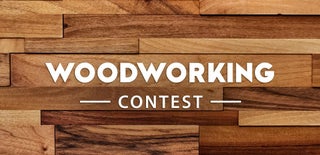
Participated in the
Woodworking Contest