Introduction: Make an Adjustable and Minimal Tablet/Phone Stand Using Digital and Traditional Fabrication - Not 3D Printed
Hi everyone, this has been a real fan project for me. It's a simple and minimal tablet/phone stand that is light and small enough to take with me everywhere. This is a very doable and easy project so come along and make one for yourself or gift to someone special!
Using a laser cutter
If you haven't used a laser cutter in your projects before, well you are in for a treat as I'm sure you'll be amazed at the speed and accuracy and most of all availability of such services near you. In my case, a local guy is running a fab lab you just send him your .dxf file and material specification and you go there to pick the finished parts. You probably have something similar but never thought to search for it, similarly you can even check for local maker spaces.
It is important that you follow the instructions in line as given below, otherwise some operations will become more difficult.
Overall dimensions while folded:
- Width 185mm
- Length 125mm
- Hight 70mm
Supplies
Materials
- 1x 4mm thick sheet of milky white acrylic (300x200mm)
- 2x A4 1mm thick felt, black and gray
- 1x 12mm thick plywood (larger than 120x175mm)
- 4x M6 countersunk machine screws
- 4x M6 locknuts
- 6x 5mm long wood screws
- Superglue
- Adhesive spray
- Sandpaper 180 grit
Tools
- Laser cutter
- Drill press with a 1.5mm drill bit, and a 90° chamfering bit
- Band saw
- Trim router with a 6mm straight bit
- Chisel
- Hacksaw
- M6 Tap
Step 1: Manufacturing
.dxf file dimensions are in mm and should be used in a 1:1 scale
Laser Cutting
There are four .dxf files given with this tutorial, each one corresponds to its material given from the name. Some clarifications on the colors of the lines, the black lines are for cutting, while the red lines are for marking only. If the laser cutter you are using cannot cut 12mm wood then mark it and move on to a band saw cutting it out following the marked lines.
Drilling, Chamfering and Tapping
Drill the pilot holes on the wood using a 1.5mm drill bit to 10mm depth, this will ensure that the wood doesn't split. Now for the chamfering, it is best to use a test piece first to set the maximum travel of the drill press. You should aim to have the head of each screw flash with the rest of the surface. Lastly, use the M6 tap to create threads on all four holes on the two arm links.
Pocketing
Clamp the wood on a bench. Grab your trim router and insert a 6mm flat bit in it. Next, slowly remove material from the shaded area marked with red diagonal lines. Stay clear of the edge. You should use a chisel to create a crisp edge. After you're done with this, break all edges using the sandpaper.
Bending
For this step, you can use an acrylic heat bender. Only two bends are needed, and only the 90° bend is important to be accurate, so take your time.
Quick tip: Over-bend your piece and as it cools it will spring back a few degrees resulting in the desired angle.
Step 2: Assembly
Now that you have all the parts ready is time to assemble them. Start with the base, and superglue the two tabs with the countersink sides facing away from each other. A square can be used here to hold the tabs vertically as the glue sets. Do the same thing on the bent acrylic. Follow that by screwing the wood piece to the acrylic, not too tight otherwise you risk cracking the acrylic. Before you move on from this step, just make sure to tighten all the wood screws such that their heads are lined up and square :).
Take your adhesive spray, apply a quote on the felt pieces, and glue them on their places as seen in the images above. Don't hesitate to peel them off if it's not applied up to spec.
Finally, grab your four M6 machine screws, they need to be 14mm long, so trim them using a hacksaw or sand them down to length. You need to fully thread the tabs and the arm links and then you can move on to tightening all the nuts slowly and uniformly testing the movement and the holding power of the joints on the way. Once you are feeling satisfied you are done!
Step 3: Finished Stand
Photo credits: George Dimoglou @yorgosdaem
Find more at @justmakeitstudio
Too bored to make it, head over to www.justmakeitstudio.com
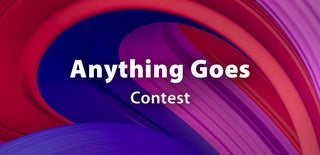
Participated in the
Anything Goes Contest