Introduction: Making a Beefy Peltier Cooler!
I wanted to make a more efficient cooling element for my electrically powered cooler so I went ahead and ordered the necessary parts from Amazon.com.
Heatpipe heatsinks are really good at cooling CPUs (those 2 pictured can handle 160Watt TPD easily) so they are perfect for cooling 40mm Peltier chips. I used a 12volt 6amp rated Peltier for this project.
Step 1: Putting the Heatsinks and Peltier Together.
Using thermal paste that came with the heatsinks, I sandwiched the Peltier between both and bolted everything together while making sure the Peltier was evenly placed between them.
Just a note, the printed side of the Peltier is actually the cold side once the polarity of the wiring is followed.
Step 2: Cutting an Opening on the Cooler Lid.
Marking out the shape of the heatsink, I cut an opening in the cooler's lid. I used a sharp knife to clear the burrs off the edges then my vacuum cleaner to remove all the mess.
Step 3: Bolting the Heat Exchanger to the Lid.
Using 3 inch long stainless steel bolts, washers, nuts and wing nuts, I secured the entire exchanger onto the lid. Once fitted I installed the fan for the cold side heatsink to circulate the air.
Step 4: Putting the Electricals in Place.
I soldered the 12volt and 0volt wiring respectively to give a low impedance and reliable solution. The temperature meter I stuck onto the lid with black silicone adhesive. The thermal sensor I stuck inside the cold heatsink fins.
For power, I used a 12volt plug to allow easy use in the car.
A quick test shows the internal temperature drop to below 9C with an ambient of 28C within half hour. The heatpipe heatsink is very good at cooling a 65watt Peltier! I also included thermal images of this preliminary test.
Step 5: Adding Thermal Insulation.
Most folks don't know this but windshield sun screens, the silver type, are a very good heatshield and insulator. I cut a section of this from my stockpile and silicone stuck it onto the lid, both upper and underside.
Step 6: Fixing the Handle.
Due to the large size of the hot heatsink, I needed to replace the carry handle with a strap. I used an old bag strap to complete my Peltier cooler.
Step 7: Testing.
Letting it run with nothing in the cooler, the ambient being 29C, in half hour it reached to below 17C. I'm quite happy with this cooling performance.
Peltier coolers work best with pre-chilled foods since they can't freeze food on their own in hot environments. Mind you though the cold heatsink is pretty large but I don't mind the loss of storage volume given how well it works.
An interesting note is that at 9 volts the cooler will get colder but take a bit longer to achieve this. This is due to the heating losses within the Peltier being directly proportional to the current used.
Step 8: Improvement!
The inside fan is a nasty heat source and I didn't want to degrade the cooling capacity so I just plain removed it. Now the temperature difference is so much more! Amazing!
I hope you found my instructable interesting and for a total cost of 700TTD, I have a cooler that is rugged and can keep groceries cold until I reach a refrigerator. No more need to buy stupid ice and having to clean the resultant mess.
Update July 2016:
Do to the ridiculous size of the cold heatsink, I reduced its size to about 30% with no loss in performance:
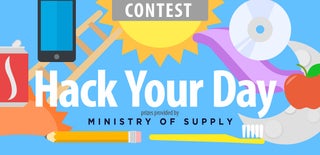
Participated in the
Hack Your Day Contest
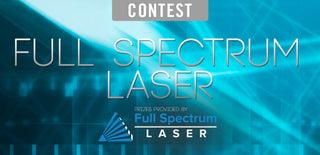
Participated in the
Full Spectrum Laser Contest 2016