Introduction: Making a Lambfoot Pocket Knife (with Templates)
In this Instructable, I discuss the process of making a pocket knife, primarily with hand tools and with no forging. My aim with this project was to make a pocket knife which is legal in the UK (non-locking blade less than 3 inches long), looks nice and is a pleasure to use.
I wanted the best quality blade possible, so I chose a tool steel that met my requirements (D2) and I carefully controlled the heat treatment procedure to produce a blade with a hardness of 60-61 HRC. I used stabilised Red Mallee burr wood for the scales which I dovetailed in place to prevent the scales from warping. I used titanium 6/4 for the spring due to its excellent anti-corrosion properties, elasticity and excellent fatigue resistance. I used commercially pure (CP) titanium for the bolsters to reduce weight over a more conventional material such as brass while still maintaining corrosion resistance. The advantage of using CP rather than an alloy such as 6/4 for the bolsters is simply down to its workability since there is no requirement for high strength. Previous experimentation demonstrated the need for brass liners to maintain a smooth blade action when opening and closing the knife (titanium tended to bind to the blade). The knife is riveted together using a combination of stainless steel rod and brass rod as rivets. To finish it off, I engraved my name in the spring for a touch of personalisation.
Enjoy! And as always, I will do my best to answer any questions you may have.
Supplies
Materials:
Blade: Annealed tool steel plate (3 mm or 1/8 inch thick)
Spring: Titanium 6/4 plate (3 mm or 1/8 inch thick)
Liners: Brass sheet (1.5 mm or 1/16 inch thick)
Bolsters: Titanium plate (4 mm thick CP, or alternative e.g. brass)
Scales: Stabilised wood
Large rivets: Stainless Steel rod (2.5 mm or 3/32 inch diameter)
Small rivets: Brass rod (1.5 mm or 1/16 inch diameter)
Dummy scale: Aluminium plate (4 mm thick)
Equipment:
Vice
Hacksaw (plus a spare blade or two for the titanium!)
Jewellers saw
Files
Ball pein hammer
Scribe
Centre punch
Small countersink
Drill bits
Callipers
Rule
G-clamp
Sharpening stones
Wood shaping tools (e.g. knife, sandpaper, thumb plane)
PPE (Furnace gloves, safety glasses)
Adjustable protractor/combination square
Dremel with a cut-off disc
Hand drill or preferably pillar drill
Furnace/forge
Low-temperature oven (e.g. domestic oven)
Thermocouple
Milling machine (optional)
Engraver (optional)
Consumables:
Wood finish for scales
Oil for lubrication
Sandpaper (various grades)
Metal polish
Spray adhesive or layout blue
Step 1: CAD and Templates
Solidworks 2020 models & STL files can be downloaded from GrabCAD here: https://grabcad.com/library/pocket-knife-21 (courtesy of Hazel Mitchell).
If you want to have a go at making this knife and you don't have access to Solidworks, don't worry! I have included a printable PDF document with templates (ensure you print at 100% scaling) and an image of a labelled exploded CAD render so you can see how it all goes together. I apologize for the mix of units. I usually work in metric; however, the knife has been designed around materials that were easily available to me, some of which were imperial (e.g. rivets).
Attachments
Step 2: Cutting and Shaping the Blade
The first step here is to mark around the template to form the basic shape of the blade. Layout blue and a scribe is a great way to do this, or you could use some temporary adhesive to attach the template to the plate. Roughly cut out the blade with a hacksaw and then file to shape, leaving the tang slightly oversize. The tang can be shaped with a smooth curve (as pictured here), or with a flat on the bottom (as shown in later steps). I decided to file a flat on the tang so the blade can be opened and closed in two stages, rather than one (see diagram). This is obviously down to personal preference but if you like a strong spring, the dual-stage closing certainly feels safer!
Once you are happy with the shape, it's time to file the bevels. This will take some time with hand tools but it is certainly doable with coarse, sharp files. Hold the blade down with a G-clamp, as pictured. I like to regularly swap sides but you could finish one side before starting the other side. I prefer a slight convexity to the faces because it makes the knife easier to control in use. I also like to thin the blade towards the tip. After rough filing, move onto finer files and then sandpaper wrapped around a piece of flat wood. There is no point in going beyond 100 grit sandpaper at this point since the blade will need to be cleaned and surface carbonisation removed post heat treatment.
I cut the nail nick in the blade using a grinding wheel in a Dremel. The pivot hole can be drilled on a drill press and it will need to be slightly larger than the diameter of the pivot so the blade doesn't jam when the pivot is riveted. Try to position the hole halfway between the tangent intersecting the kick to the bottom corner on the tang and the top of the tang, where the spring sits when the blade is in the open position (see diagram). This will ensure the top of the spring sits flush with the top of the knife when the blade is open and closed. Unfortunately, for this to work, the kick needs to be approximately the right size to start with, which might need some trial and error.
Step 3: Making the Spring
The spring is sawn and filed from titanium 6/4 plate with the same thickness as the blade. Titanium 6/4 is very difficult to work with, so make sure you saw slowly to prolong the life of the hacksaw blade. Leave the spring oversized at this stage. It can be brought to size during the trial test fit later. I found a final spring depth of 4 mm resulted in my preferred spring tension (strong). The spring can also be made from the same tool steel used for the blade but tempered to a spring temper.
Step 4: Cutting the Liners and Bolsters
The liners are made from brass sheet. A jewellers saw is perfect for cutting out the shapes. My advice here would be to avoid tin snips. They will deform the edges of the liners leaving much more to file. The bolsters are roughly sawn to shape from 4 mm thick plate. The length of the bolsters is not critical and should be made according to preference, while still allowing room for the rivets.
Step 5: Dovetailing the Bolsters
I used a shop-made jig and a milling machine to accurately machine a consistent angle on the inside faces of the bolsters. I also used the jig to machine a dummy aluminium scale (see picture). I used this dummy scale to help position the bolsters for riveting in the next step. Rather than making a jig, the machine head or vice could also be tilted. Alternatively, the dovetails could be filed.
The angle you should use for your dovetails is dependent on aesthetics and how brittle your scale material is. I chose a steep angle (20 degrees) to exaggerate the dovetailed look but I did have problems with the corner of the scale chipping. I would recommend trying an angle of around 10 degrees.
Step 6: Riveting the Bolsters to the Liners
Use the dummy scale made in the previous step to help align the bolsters for drilling. This will ensure the dovetails are parallel and the bolsters are separated by the same distance for each side. I would suggest drilling the bolsters at the same time as the liners as shown in the first image to ensure the rivet holes align. For the rivets, I used 1/16" brass brazing rod because I had some on hand. I found cutting the rivet 1-1.5 mm longer than the total thickness of the material to be riveted worked best. See "Final Assembly and Finishing" for more details on riveting. The bolsters can be roughly sawn to shape once they are riveted to the liners.
Step 7: Test Fit
The test fit ideally should be done before heat treating the blade to make blade adjustments easier. When the blade is closed, make sure the point of the blade is hidden in the slot but not in contact with the spring. I suggest allowing 3-4 mm of clearance between the tip of the blade and the inside of the spring when the knife is closed to ensure the blade doesn't crash into the spring when the blade is snapped shut. This can be adjusted by removing material from the kick on the blade. Shape the outside of the spring so it's flush with the outside of the knife body. The shape of the blade tang will probably need some tweaking with a file so the spring sits flush both when the blade is open and closed (you can see I didn't get this quite right).
To adjust spring tension, material can then be removed from the inside face of the spring. To adjust the final locking position of the blade when open, remove material from the end of the spring. File a small undercut in the blade where the end of the spring contacts the blade to ensure the blade snaps into position positively when fully opened (see diagram). I decided to make my final opening angle slightly less than fully open to compensate for pivot wear in the future.
Step 8: Rounding the Bolsters
The bolsters can now be rounded to the desired shape with a file. Take care not to bend the liners. Supporting the liners when shaping the bolsters with a piece of scrap wood or metal is a good idea.
Step 9: Heat Treating the Blade
The heat treatment process is dependent on the steel alloy chosen. I had access to a furnace that allowed me to carefully control the temperature. This allowed me to use D2 tool steel which is known for its excellent wear resistance but sensitivity to overheating during heat treatment. D2 also has a high chromium content which gives it some resistance to corrosion. This is very noticeable in use, especially in comparison to the more popular O1 tool steel.
The first step is the solution treatment. D2 tool steel should be heated to 1000-1040 degrees centigrade for the solution treatment. I used a temperature of 1000 degrees centigrade to minimise the risk of overheating. I left the blade in the furnace for 20 minutes to equalise. If a longer time is used, carburisation can become an issue but if the soak time is too short, the blade won't be properly equalised.
Another advantage of D2 over most other tool steels is that it can be quenched by simply allowing it to cool in air. A gas quench can also be performed if the furnace allows it. An air/gas quench is much less likely to cause blade warping, which can be a problem with an oil or water quenched steel.
After quenching, make sure the blade is properly hardened with an old file or try scratching it with a scribe.
I triple tempered my blade, with each interval lasting 30 minutes at 200 degrees centigrade. For this, I used a domestic oven with a large block of copper placed inside to help maintain a stable temperature, which I carefully monitored using a thermocouple. This should result in a final hardness of around 61 HRC with D2. Between each interval, I allowed the blade to cool to room temperature.
Some alloys (e.g. D2 and A2) can benefit from a cryogenic soak after the solution treat but before tempering; however, the main advantage of this technique is to reduce the number of tempering cycles required and does not significantly affect the microstructure [https://doi.org/10.1080/10426910902917421]. Therefore, for the purposes of a hobbyist, it's probably going to be easier to double or triple temper and forgo the cryogenic treatment.
Step 10: Finishing the Blade
Firstly use a Dremel to clean out the nail nick. Lap the faces perpendicular to the pivot with a flat diamond or oil stone. Then, starting on a coarse grade of sandpaper, remove surface discolouration and any surface carburisation. Gradually work your way down the sandpaper grades, each time changing your sanding direction by 90 degrees to make it easier to see when the scratch marks have been removed. Make sure you clean the blade thoroughly between grades. I used autosol for the final polish. A choil (notch in the blade next to the kick) can be added with a Dremel or slip stone if desired. Alternatively, this could be done before hardening with a needle file.
Step 11: Shaping the Scales
Roughly saw the scales oversized. I cut them to length and hand-cut the dovetails, taking care to keep them parallel and the correct angle. (I tried machining the dovetails in the milling machine but the wood had a tendency to split.) Make the scales a snug fit in between the bolsters so you can easily shape them while being held in place. Stabilised wood can be shaped with standard woodworking tools.
Step 12: Final Assembly and Finishing
When you are happy with the action, spring tension and handle shape, use a ball pein hammer to rivet the knife together. Remember to lightly countersink the holes before riveting to allow the rivets to maintain a mushroomed head when flushed off. Lots of light taps are the way to go here. Light taps will cause the rivet to expand into the hole, rather than just mushrooming the ends over (although some mushrooming is desirable). The rivets can be filed flush due to the slightly countersunk holes but I chose to leave the three stainless rivets slightly proud of the surface for extra strength. Take extra care with the rivets that go through the scales, if using wooden scales. It is easy to split the scales from too much riveting, especially with the large stainless rivet. Remember the rivet can be tightened later if needed so it's best to err on the side of caution here and definitely have a practice on some offcuts first. All the smaller rivets were made from 1/16" diameter brass rod and the three larger stainless rivets were made from 3/32" rod.
When riveting the pivot, it is vital that you use a thin shim between the blade and liner to ensure the blade does not get permanently riveted in place. It needs to be able to rotate and this will mean there needs to be some sideways play in the blade. 100-200 microns is a good shim thickness to try. Again, I would suggest practising with offcuts first. Once I was happy that the rivet was properly in place, I removed the shim and gradually kept tapping the main rivet until I just felt the blade action tighten. This ensured the sideways play in the blade was minimised while still maintaining a smooth action.
Finish the scales as desired. I used Danish oil and several coats of gunstock wax but beeswax also works. A drop of oil in the pivot also helps the knife operate smoothly. I used a Gravograph engraver to engrave my name in the back of the spring. This can be done before or after assembly.
Step 13: Sharpening the Blade
I like to sharpen my pocket knife with a single primary bevel on the upside face when I'm using the knife normally (e.g. for sharpening a pencil). I don't touch the other face during sharpening, apart from with a fine stone or strop to remove the burr produced after honing the primary bevel. Most pocket knives are sharpened with an equal-sized bevel on each side which is easier to sharpen but when shaving or carving a piece of wood, you have to tilt the knife at a steeper angle which, in my opinion, reduces control. However, a micro-bevel on the opposite side to the primary bevel does make the knife easier to sharpen while still maintaining the excellent control a single-bevel knife provides.
In the image, I am using a DMT mini diamond stone, which I think are excellent stones for sharpening pocket knives.
Step 14: Acknowledgements
Thanks to Hazel Mitchell for the CAD and my father Alastair Godfrey for the original design.
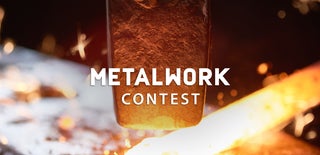
Second Prize in the
Metalworking Contest