Introduction: Makita MAC700 Compressor Motor Repair
A few weeks ago my Makita compressor died on me. When The tank was low on air the compressor motor was supposed to kick in. However all I would hear was an electrical hum but no compressor. After doing some research I discovered it was likely cause one of two things. The compressor motor capacitor was blown or clutch contact plate was dirty or corroded.
The first thing you should check is the clutch contact plate. If it is dirty or corroded you can likely fix this for free. I will be showing you how this is done with this tutorial.
Supplies
180 grit sandpaper
phillips screwdriver
allen keys
adjustable wrench
Step 1: Hose Disconnection
Disconnect the compressor motor hose from the tank. The hose connects to the check valve which is threaded into the tank (as seen in the picture). Use a wrench to support the check valve when loosening the hose. If the check valve is old and corroded it can break off in the tank when loosening the hose. This is a huge pain and will add a ton of time to the project. Don't ask me how I know this... cuz I don't want to talk about it.
Step 2: Disconnect the Power
There is a black plastic cap on the end of the tank with one screw in it. Remove this screw and then remove the cap. You will see 6 wire connected to terminals under the cap (as seen above). You want to disconnect the wires that lead to the compressor motor. There is one ground, and two power wires. the wires you want to disconnect are at the top of the terminal block (as seen above, 2nd picture).
Step 3: Remove Compressor Motor and Cover
There are 4 screws holding the cover and compressor motor in place, 2 on each side of the tank. You will need to use Allen keys to get these off. Take all 4 of them out and the compressor motor and cover will slide forward away from the power terminals. Watch the power cable as it need to slide out a hole in order for the compressor motor to be removed from the tank.
Step 4: The Compressor Motor
This is the compressor motor (picture above). There is a white plastic fan blade which I have removed. There is one screw holding it in place. Loosen this and the fan blade will come off. Attached to the center shaft, as seen in the picture above, is the clutch. Behind the clutch is the clutch contact plate. There is one screw which holds this in place on the shaft. Mark the position of the clutch on the shaft with a sharpie. It needs to be the right distance from the clutch contact plate in order to work properly. Once you have removed the clutch you will see the clutch contact plate. It has two wires attached to it. Mark one of the wires with the sharpie. Also mark the terminal which it is attached to. As soon as this is done disconnect both wires. There are two screws that hold the clutch contact plate in place. Remove both of them and the clutch contact plate can then be removed.
Step 5: The Clutch Contact Plate
The clutch contact plate as seen above touches a copper contact on the pcb board and another which is raised off the pcb board. These are the on off states. You need to clean the contact plate as well as the two copper contacts described. I used 180 grit sandpaper to do this. I just lightly sanded all the contacts until all the black residue was gone. As soon as this is accomplished you can re-install the clutch contact plate.
Step 6: The Clutch and Clutch Plate Contact.
The first image is the clutch and clutch plate contact re-installed after cleaning. To ensure you have the right spacing for the clutch to the clutch plate contact use multimeter to do a continuity test. Touch the two wire on clutch plate contact with the leads from your multimeter. Now slide the clutch down the shaft until it depresses the clutch plate contact. One position will be open (so no sound). The other will be closed (sound). If you get this condition by sliding the clutch up and down the shaft everything should be working and you can re-assemble the motor.
Step 7: Compressor Motor Hose
Re-attach the compressor motor hose to the tank. Be sure to support the check valve when doing this.
Step 8: Re-attach the Power Wires.
Re-attach the power wires to the terminals. When this is done you are ready to power up the compressor and see if you have fixed the issue. If you are still hearing an electric hum and the compressor motor is not kicking in you should look at the compressor motor capacitor. It is under a cover which is screwed into the side of compressor motor. Check the capacitance of the compressor to see if it is still within tolerance. If it is not, replace it.
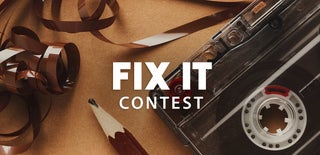
Participated in the
Fix It Contest