Introduction: Marblevator, Hill Climb (and Descent)!
As the old adage says, what goes up, must come down!
"Marblevator, Hill Climb (and Descent)!" reinforces that adage thanks to an N20 styled 200 RPM 6VDC gear motor, a 1000 mAh lipo battery, a speed controller and a lipo battery charger in order to create the physics violating illusion of climb and descent coiled motion.
And how does it work? Well it starts with a 6.35mm (1/4") spherical magnet located within the tower that is rotated by a four finned barrel. Without any assistance, the spherical magnet sits below the barrel fins and does not move. However, when an 8mm ball bearing is allowed to descend to the start of the track, the spherical magnet is attracted to the ball bearing and is lifted up into the barrel fins which rotate the spherical magnet around the tower interior. And thanks to the magnetic attraction between the spherical magnet and the ball bearing, the spherical magnet spirals up the coiled track to the top. At the top, the ball bearing is stopped by the track end cap while the magnetic sphere continues to rotate within the fins until the magnetic force is no longer viable. At that point, the magnetic sphere drops down to the bottom of the tower awaiting the descent of the ball bearing where the process repeats.
As usual, I probably forgot a file or two or who knows what else, so if you have any questions, please do not hesitate to ask as I do make plenty of mistakes.
Designed using Autodesk Fusion 360, sliced using Ultimaker Cura 4.12.1, and 3D printed in PLA on Ultimaker S5s and Ultimaker 3E 3D printers.
Supplies
Soldering iron and solder.
Thick cyanoacrylate glue.
Thick double sided tape.
Step 1: Parts.
I acquired the following parts:
- One 6.35 mm (1/4") spherical magnet.
- One 8mm ball bearing.
- One PWM Speed Controller (https://www.amazon.com/dp/B07WGT8K82?psc=1&ref=ppx_yo2ov_dt_b_product_details).
- One N20 200RPM 6VDC gear motor.
- One 1000 mAh lithium rechargable battery (https://www.amazon.com/gp/product/B07CXNQ3ZR/ref=ppx_yo_dt_b_search_asin_title?ie=UTF8&psc=1)
- One USB lithium charging module (https://www.amazon.com/AITRIP-Lithium-Charging-Protection-Functions/dp/B08DNK398S/ref=sr_1_4?crid=5RL43KP0AXOQ&keywords=usb+charging+module+board&qid=1683937727&sprefix=usb+charging+module%2Caps%2C181&sr=8-4).
- JST 1.25 male and female connectors required to interconnect the electronic components.
I 3D printed the following parts:
- One "Barrel.stl" at .15mm layer height, 20% infill.
- One "Base.stl" at .15mm layer height, 20% infill.
- One "Cap, Tower.stl" at .15mm layer height, 20% infill.
- One "Drive, Motor.stl" at .15mm layer height, 20% infill.
- One "Retainer.stl" at .15mm layer height, 20% infill.
- One "Top.stl" at .15mm layer height, 20% infill.
- One "Tower.stl" at .06mm layer height, 20% infill.
This is an ultra high precision 3D print and assembly model using at times very small precision 3D printed parts in very tight spaces. Prior to assembly, test fit and trim, file, sand, polish, etc. all parts as necessary for smooth movement of moving surfaces, and tight fit for non moving surfaces. Depending on you printer, your printer settings and the colors you chose, more or less trimming, filing, sanding and/or polishing may be required. Carefully file all edges that contacted the build plate to make absolutely certain that all build plate "ooze" is removed and that all edges are smooth. I used small jewelers files and plenty of patience to perform this step. And polish all moving parts!
The model also uses threaded assembly thus an M8 by 1.25 tap and die will assist with thread cleaning if necessary.
Step 2: Top Assembly.
To assemble the top, I performed the following steps:
- Inserted "Tower.stl" into "Top.stl" by aligning the pins in the top with the slots in the tower, then rotated the tower -45 degrees when viewed from to tower top (small dots of glue may be required to hold the tower in position).
- Placed the magnetic sphere in the tower.
- Slid "Barrel.stl" into the tower until the barrel threads exited the hole in the base of the tower.
- Secured the barrel in the tower using "Retainer.stl", making certain the barrel rotated with ease inside the tower.
- Pressed "Cap, Tower.stl" onto the top of the tower.
Step 3: Base Assembly.
To assemble the base, I performed the following steps:
- Soldered a female JST connector to the motor such that when power was applied to the motor the motor shaft rotated counter clockwise when viewed from the motor shaft end of the motor.
- Soldered a female JST connector to the USB charger "B + and -" connectors, red to "+" and black to "-".
- Soldered a male JST connector to the USB charger out "Out + and -" connectors, red to "+" and black to "-".
- Soldered a female JST connector to the "DC In" tabs on the motor speed controller, red to "+" and black to "-".
- Soldered a male JST connector to the "MOTOR" tabs on the motor speed controller, red to "+" and black to "-".
- Followed the motor speed controller instructions to modify the motor speed controller to operate at low input voltage.
- Pressed the gear motor into the base assembly.
- Pressed "Drive, Motor.stl" onto the motor shaft.
- Aligned the motor assembly into the base assembly such that the top of the motor drive was 8mm below the top of the base top edge.
- Pressed the top assembly onto the base assembly (small dots of glue may be required to secure the top assembly to the base assembly).
- Plugged the motor JST connector into the motor speed controller "MOTOR" JST connector.
- Plugged the motor speed controller JST "DC IN" connector to the USB battery charger "OUT" connector.
- Plugged the battery JST connector the USB battery charger "B" just connector.
- Plugged a USBc charger into the USB battery charger.
- Turned on the motor speed controller to test the circuit.
- With the motor running, added the 8MM diameter ball bearing to the track to make certain the motor was operating in the correct direction and the ball bearing climbed and descended the track.
Step 4: Final Assembly.
For final assembly, I performed the following steps:
- Secured the motor speed controller inside of the base assembly using thick double sided tape.
- Secured the USB battery charger inside the base assembly using thick double sided tape.
- Secured the battery inside the base assembly using thick double sided tape.
And that is how I 3D printed, wired and assembled "Marblevator, Hill Climb (and Descent)!".
I hope you enjoyed it!
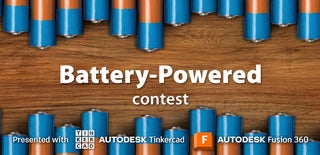
Participated in the
Battery-Powered Contest