Introduction: Martial Art Belt Rack
I made this belt rack for my old color belts that I got in tae kwon do. I am a second degree black belt so and my old belts were sitting in the closet which was upsetting me since I worked so hard to build it so I made this to hold them and it turned out better then I could ever imagine. It is one of the best things I have ever made.
Step 1: NOTE:
If you want the exact same thing as I made just download the pdf files and cut them out and then skip to ASSEMBLY section. For the 3 main boards there will be 2 files because to save time you have to vector the design at high speed and low power and then the other pdf will cut it out so just set those two cuts one after another (without moving the wood at all) so they will then cut in the same place. If you want to use my onshape designs and change them to benefit you, you can download the parts.
Attachments
Step 2: DESIGN STEP 1: Measure
This design process is complicated be warned. Get the measurements (preferably in inches because that is what I am using for instructions but you can technically use any measurement you want) of your belt when rolled up. You need the width (basically the diameter of the belt circle) and the height of the belt. And make sure you know the amount of belts you need.
Step 3: DESIGN STEP 2: Estimate for Mistakes
To make it easier to put the belt in add about .5 of an inch to both the height and width. My measurements of the belts I have were 1.75” height and 4.25” width so I designed the slots for the belts 2.25” and 4.75”. You can do less of a difference area but I wanted to compensate for mistakes which turned out extremely important for me because this design was more complicated the I intended.
Step 4: DESIGN STEP 3: Main Boards
I made mine to fit 9 belts in total so I used ¼” wood and that means that the panels that will hold the belt have a height of ¼” so because it should be able to easily slide in and out so I made the area for the sliding panels .3 in. You also need .25 extra at the top and bottom so you can put the panels into the top and bottom base. So from this knowledge my design looks like this
The first picture is the back panel and the second picture is the side panel. There is an extra ¼” on both sides of the back panel so when you put it together it will fit into the side panels and on the side panels there are ¼ on one side for the back panel to fit in and an extra ½” after that to put another piece of wood to stabilize the back panel when putting together. (also you only have to design 1 of the side panels but you have to cut 2, one works for both). For the side panels you also need a piece that is 20.4” in height and .5” in width to put on the back of the panel to secure it on (we will call these secures just for ease later).
Step 5: DESIGN STEP 4: Creating Shelves
Create inside blocks that can be glues on the inside to make a shelf situation. The easiest way is to make one block 2” by 5”for the two sides and the other block 3.75” by 2” (subtract .5” from width of the inside of the backboard which was 4.25) for the backboard. It sounds weird but trust me this way when you put it together it makes it so it slides in and will stay in place and it's hard to explain just trust me though
Step 6: DESIGN STEP 5: Sliding in Panels (makes It a Shelf)
Create a box measured by the entire interior of the main pieces put together. This means or mine I created it 4.75” by 5”.
Step 7: DESIGN STEP 6: Ends
Ok for this I might of made it a little to complicated in my own design because I wanted to make sure it was perfect and it worked amazingly but you could 100% simplify it. I first created a box bigger than all the sides when they were put together in the final piece. I made mine 6” by 6.35” for security, you could probably make it closer to the panels. I then took the side panels and I I places them so the side panels were parallel and 4.5” apart so the backboard can slide into place and be secure. I also had the 4.5 in piece .5 away from one side. Create another box the same size as the one before which is 6” by 6.35” for the back of the piece before for structural support (we will call it end support)
Step 8: DESIGN STEP 7: Door
Create a box .6” smaller than the main boards (it’s .6” because of the .25”lost when putting on the top and bottom panels and .1” to make sure it can more freely without getting stuck). Then separate that panel into equal parts which for the size of 20.3 board I spaced mine 2.25555555556 (i just divide 20.3 by 9). Then I put text in for every color and made then all the same right of .4” and then i put then .2” away from the bottom of each of the equally spaced boxes
Step 9: CUTTING STEP 1: Put Into Inkscape
Transfer all of the pieces you designed into Inkscape (for the boards it’s easiest to vector the design at a high speed and low power so it is like a raster but takes WAY less time you just have to space them the same amount from one corner and it will cut properly).
You need:
- 2 side panels
- 1 back panel
- 2 end support
- 2 ends 18 (5” by 2”) inside panels
- 9 (3.75” by 2”) inside panels
- 8 slide in panels
- 2 secures
- 1 door (out of clear ¼” acrylic, at least, use a little thicker acrylic if possible)
Every piece except the boards you will vector cut all the lines. For the main boards you only want to raster the design and vector around the entire piece because the lines are only for glue later.
Step 10: CUTTING STEPS 2:
Cut the pieces out and BOOM you are almost there.
Step 11: ASSEMBLY STEP 1: Assembling the Main Boards
Take one of the side inside panels (5 by 2) and glue then into the place. (I forgot to take the picture while first doing it but this is how it will sit in place) I used binder clips to keep the pieces in place while glueing. Glue in all 18 pieces to both the side panels. For the inside panel you have to kinda eyeball the middle of or you can use the width of another piece of wood that you haven’t glues on yet to get the piece to look like this
Then attach the secures to the back of the side boards and make sure the backboard can fit into it. Then glue together the end panels to the end supports so you will have 2 end pieces. I also now painted mine black before putting it fully together and you can do the same if you want. (In the painted picture the pieces are laid down as some of the sliding panels the sideboard, backboard, then sideboard.)
Step 12: ASSEMBLY PART 2: Attaching Main Panels Together
Now put glue in the little area on the side panels between the inside panels and the secures then place the backboard into the slaught.
Do the same to the other side and then place it into the end piece just so when the glue is setting you will know it is setting in the right place making it easier to avoid mistakes later. Then clamp the back together (I also put in the sliding panels just to make sure everything was aligned and they were able to fit in properly also some weren’t painted yet in the picture).
Step 13: ASSEMBLY PART 3: Finish Wood Assembly
Glue on the end pieces to ensure it won’t fall apart if you move the rack. If you can clamp it you should but if you can’t it will probably be fine. I didn’t have long enough clamps so I wasn’t able to clamp it but it was secure after giving it a good 24 hours to dry. You can also glue the sliding panels in if you want to but you obviously can’t slide them anymore but if you chose to you can.
Step 14: ASSEMBLY PART 4: Attaching the Acrylic Door
Ok this was a huge challenge for me and it took some trial and error for the look that I wanted so if you want something different and simpler by all means go ahead with a different way cause attaching hinges to a ¼” acrylic door is really hard.
What I did was:
- Drill holes for each hinge where I wanted it.
- I did it all the way through kinda on accident, but it still works. Although I would recommend drilling almost all the way through but just before so if you run your finger along it you won’t feel a hole.
- Heated up a screw that came with the small hinge and screwed it into the piece of acrylic.
- Heating the screw up then screwing it in prevents the acrylic from cracking by slightly melting it and allowing the screw it easily go in.
- This creates a path so later life will be a lot easier, trust me.
- Cutting the screws down with a dremel
- The screws I had were to long for the acrylic so I cut them down just enough that they would still hold but if I screwed them in all the way they wouldn’t go through the other side.
- I tested that by putting the screw along the side and making sure it wasn’t longer than the width of the acrylic.
- Put on the the hinges with the cut down screws.
- If you did the previous step right then there should be a path for the cut down screw to go in perfectly and sit nicely.
- Now the easy part, set the acrylic on the belt rack and make marks to drill holes so it sits properly.
- Screw on the hinges to the wood piece and BOOM there you have it.
Step 15: OPTIONAL: Magnets
I used magnet tape to keep the door shut when like moving it around or so the ghosts can’t open the door and making a squeaking sound in the middle of the night to scare you (I’m sorry I needed to make these instructions a little entertaining). Anyway I put the magnet tape on the door and the belt rack itself and lined them up by just having them attached together while applying the door one (that probably doesn’t make sense but I can’t find a better way of wording it to be honest). Because I painted mine black the tape kinda blended in because it was a dark grey and that was a big upside.
Step 16: OPTIONAL: Handle
You can add a handle to open the door I didn’t but I honestly might later cause I mean that’s super cool.
Step 17: NOTE: Make It Yours
Be creative and take my design and make it your own by adding stickers, engraving pictures into it, or literally anything because it is a base for great creativity.
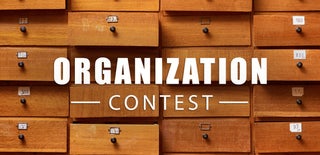
Participated in the
Organization Contest