Introduction: Mesa Coordenada
The need is the mother of creation, so I decided to build a coordinated table for my bench drill, an indispensable tool in a garage workshop.
I started using recycled materials, purchased in an old iron in my city, but in the end I chose to increase a little more and make some more worked pieces, but nothing that prevents being manufactured at home
Step 1:
I went to the ironwork "Shopping" where I found six pieces of 1/14 "(31.75mm) by 1/8" (3,175mm) and about 800mm long.
Step 2:
I used my miter saw adapted with an abrasive disk to cut the angles.
Step 3:
I cut four pieces into the frame of the first axis.
Step 4:
This is how the first frame, first axis, should look.
Step 5:
Two centralized holes to guide the spindle.
Step 6:
Repeating the first steps for the second axis, attached here by an intermediate frame, where the spindle nuts were affixed.
Step 7:
Sticking the piece of angle that had received the cheek of the walrus.
Step 8:
Opening thread 6mm to fix the jaws.
Step 9:
Also bought in the "mall" a massive bar of 20mmx20mm to be the cheek.
Being pierced and countersunk to be affixed.
Step 10:
Here the vise already with the cheeks, being welded the support of the spindle.
Step 11:
For the movement of the spindles, I decided to make flywheels cast in aluminum.
Here my homemade 3D printer, printing the models for casting
Step 12:
First half of the steering wheel model ready, (the blue color at the end is for taking advantage of the remains of filaments of varied colors)
Step 13:
Second part of the steering wheel being printed in blue abs, this in turn was not in good quality which compromised the finish of the piece
Step 14:
Here the two halves of the steering wheel are ready, fix the blue with white plastic mass, to repair the imperfections of the bad abs.
Step 15:
Here by sanding the model that is attached to the bench drill.
Step 16:
Starting the mold for casting.
Step 17:
Finishing casting mold (I intend to make other instructables detailing casting and 3D printing)
Step 18:
Here the furnace for aluminum casting.
Step 19:
We made six pieces in different molds.
Step 20:
Finished piece, just missing the burrs.
Step 21:
Hole for fixing the spindles
Step 22:
Stud fixing hole for locking the spindle
Step 23:
Handwheel crank hole
Step 24:
Cheek grooves.
Step 25:
Painting.
Step 26:
Third frame, the walrus.
Step 27:
Finished piece, ready for use.
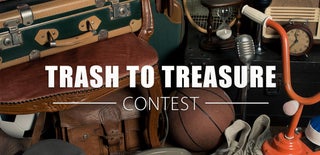
Participated in the
Trash to Treasure