Introduction: Metal Shelf Workstation
I had a need in my workshop for a small space where I could tinker with electronics, this lead me to look for a compact unit that could take all of the required equipment and still be small enough to move if I need the space for one of my larger projects.
I had an old modular metal shelving unit laying around but there were only 2 shelves with it so it wasn't good for much... until now.
As this project is built mostly from scrap and bits I had about the shop it can't really provide a parts list but where I can make recommendations I will.
Step 1: Set the Scene
First, I wanted this shelving system to provide me a work bench, this means I should be able to sit at it, with a quick check of the table in my office I found the standard table height to be 70 cm, I set the bottom shelf to this height and then sat at the 'bench' and set the top shelf at a height where I wouldn't hit my head.
with only 2 shelves the unit was not very rigid so I cut a sheet of aluminium to the width of the rack and long enough to reach fro m the top of the rack to just below the lower shelf. I clamped and riveted it to the back of the rack, this provided strength, as well as stopping stuff rolling off the back of the shelves and giving me a mounting surface for later steps.
Step 2: Let There Be Light
When working on electronics the last thing you need is to be working in the dark, my workshop is poorly lit as it is and now I had fitted a roof to my workspace.
I had an old emergency exit sign that had 6 led strips inside, I had been saving this for just such and emergency.
I stuck the LED strips and the transformer to the underside of the top shelf with some super high tack double sided tape, I also quickly added a plug top to test the lighting and to make the next few images look a bit better.
Step 3: Making the Work Surface Usable
The old shelves were pretty banged up and made from metal, this is not good if you don't want components rolling around the table and the metal provides a huge risk of electrical short, plus a big risk to you if the top comes in contact with mains power.
I cut some 2mm thick textured black plastic, I use this on my other work benches too as it seems to close up quite well if you cut material on it with a knife or if you scratch it.
Next we need power, I added some maxi trunking and sockets along with a switch for the lights above. When wiring sockets and switches to the mains please be careful MAINS POWER CAN KILL. Please also consult the wiring regulations/guidelines for your area, the wiring colors/conventions shown in my images may not apply in your region.
Step 4: Top Shelf Storage
The top shelf is where I would normally store occasional equipment, I had some parts bins and carrier left over from a fitting I did in the shop a couple of years ago and this fit in nicely, I left some space underneath for equipment as you will see in a later step, I know this seems high but I am 6' 3" so I can reach, if you are smaller please keep access in mind.
I also wanted to keep my cabling close by but the rolls can be big and get in the way so I fitted them to a bar up high. At first this seemed like a good idea unit I tried to lift the bar with the cable reels up into the holder, this was not safe. I didn't want them lower as I don't like banging my head.
The solution was to mount the carrier on a swinging arm and use some old gas lift rams I had to hold the whole lot up put of the way, when I need to change the reels I can pull the rail down, insert a pin to hold it in the lower position, safely work on the bar and then let it raise back up out of the way.
Step 5: Making the Work Space Work
There are some things you need to hand while working on electronics, mainly components, tools and some way to improve your vision.
I mounted my components bins to the back wall, I have painstakingly separated all of the components into their drawers and labelled them up, no point in trying to remember resistor color codes or search for an LED when you are in full flight on the build.
I also mounted up my illuminated magnifier, my eyesight leaves a little to be desired and I don't like burning my fingers when soldering small components.
I also added a magnetic tool holder to the back wall, this allow me to keep tools to hand but off the small work space.
Step 6: Stock Up
This is the finished rack, as you can see, I used the space on the top shelf under the parts bins for my power supply and test equipment.
There are some other little additions I would like to make such as:
- a set of helping hands to hold work pieces
- extraction for solder gasses (I am working on one that uses a gas detector via an Edison and turns on the extraction only when smoke is present, keeping the noise down)
- Maybe a very small monitor for use with raspberry pi...
- Suggestions???
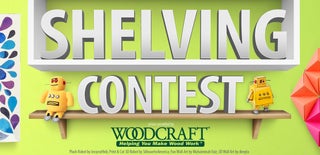
Participated in the
Shelving Contest
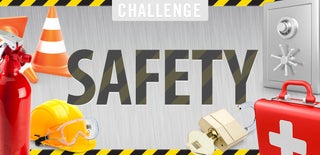
Participated in the
Safety Challenge