Introduction: Microscope Upgrade - Using Fusion 360 to Design 3D Printable Compliant Mechanism
Difficulty level
3D Modelling: Beginner, 3D printing: Intermediate
My motivation for this project
I recently bought myself an Andonstar ADSM302 microscope that I intend to use for soldering and inspecting electronics. The manufacturer states that the microscope provides up to 560x magnification, so I had hopes that I could also use it for hunting Micrometeorites (which are typically round particles of 300-400µm in diameter), but this being a relatively cheap microscope bought from China I was not surprised to find that it didn't actually provide that amount of magnification. I was expecting this to be the case, but I still bought this particular microscope because it enables 1080p video recording (convenient for my YouTube Channel Applied Procrastination) and has an attached screen which is very handy for electronics work. Regardless, it was time for plan B.
My available resources
A few years back I found an old webcam in the e-waste bin at my university. This was one of those high quality "conference call"-type cameras, and the optics inside it looked really nice. I decided to save those optics for a rainy day, because who knows when you will need a few lenses, right? Doing some hand-held tests I verified that two of the lenses could be used to provide extra magnification, one of them probably around 1.5x and the other one looked like at least a 5x boost in magnification (these numbers are not accurate, but I'll continue to use them for clarity).
The design challenge. Why did I need to design a compliant mechanism for the first time?
The 1.5x lens was a fair bit larger than the 5x lens in physical size, and it was therefore trivial to design the necessary attachment mechanism for it. The 5x lens however was a lot smaller than the diameter of the main lens of my microscope. To make things worse, it still had some unevenly distributed plastic artifacts along the rim of the lens (remains from the webcam attachment), making it basicallyimpossible to design a good "press fit"mechanism to hold it centered along the optical axis. I could see a very simple solution to this problem though, a small plastic clamp that could enclose the lens and provide attachment-points for a larger mechanism that fits the microscope's own lens. Turns out though, that for me, an electrical engineering student, getting this right wasn't quite as simple as I had imagined. It took me a few moments to realize that I was actually attempting to design a compliant mechanism that has two states: "open" and "closed". I couldn't find a solution in Fusion 360 that allows me to switch between these two states (such as flexure simulation), so I solved the problem with some math and angles instead. When I figured out how to do this I wanted to write down the solution for future reference, and maybe even help others facing similar design challenges.
How will this Instructable go down?
All this is basically just a long way of explaining that the main focus of this Instructable will the design of a, compliant, plastic clamp. But to provide context, I will show my entire design process for both the 1.5x lens and the 5x lens.
There are a few steps with some math in them. Don't be discouraged by this if you're not used to that kind of stuff. I'll highlight the important results, and explain everything I'm doing. The difficulty of the math problems I faced is roughly high school-level, but here I'll be providing all the formulas and answers, so anyone able to read formulas should hopefully be able to follow.
Supplies
The links are affiliate links to AliExpress
- A broken webcam with lens (or harvest the lens from wherever you can find it).
- A few nuts and bolts, depending on your design. I use M2 here, as it's the smallest I had on hand.
- A 3D printer.
- Microscope. I use Andonstar ADSM302
- Caliper. Cheapo, plastic, digital calipers will be more than enough for this project but I recommend metal ones if you use them often. I use Mitutoyo
- Fusion 360
Step 1: Harvest Optics From an Old Webcam
As explained in the intro, I've had the optics from a high-end webcam laying around for a while. I found the webcam in the e-waste bin of my university, decided to open it up, and saw all these nice looking lenses that I wanted to keep for a "rainy day". In order to get them out, I used pliers and broke off a bunch of plastic, so one of the lenses (the "best" one for my use case, the 5x lens) has some residual plastic along the edges making a press-fit mechanism impossible to design.
The 1.5x lens actually has a built-in mechanism for mounting it to the camera that I would describe as "press in and twist to lock". Designing a mount for this lens was therefore rather trivial and will not be described here in this Instructable, since it's only useful for the specific lens I got my hands on.
The steps involving CAD design will therefore be centered around the challenges I faced when designing a compliant clamping mechanism that provides further attachment-points for the 5x lens.
Step 2: Design CAD Models of the Lenses
This step is optional, but when I'm designing enclosures or interlocking pieces I personally I prefer to have an available CAD model of all the involved objects. That way it's way easier to make sure everything fits, that nothing collides or overlaps, and that it's all possible to assemble.
It's more than enough with a very simple "placeholder"-type mockup model, but sometimes it's also pleasing to make it look nice. This time I spent a little more time on the 1.5x lens than on the 5x lens and the camera lens, but all of them did their job splendidly.
I've annotated the pictures in this step to show specific things that I discovered when designing these 3D models which came in handy at a later stage in the design process. The most prominent thing is a very convenient notch I noticed on the 5x lens that I would have completely missed if I didn't make a mockup of the lens in Fusion 360 before designing the mount.
Step 3: Compliant Mechanism - First Challenge
Since I want to 3D print this clamp in it's "open" position, to give it a natural spring behavior, everything needs to be shifted to account for the deformation we will see when the clamp is held in it's "closed" position. I didn't notice this myself until I started designing the mounting holes on the sides which made me think: "how do I make sure the attachment brackets are parallel and centered?". I only had this thought because I wanted it to look nice, and it's not strictly necessary to make them look nice, but making this effort made it easier to solve the second problem I faced later: "how do I make sure the holes align with their mates in the piece they attach to?". This second problem will be covered in the next step.
So what are we dealing with here? This first challenge can be broken down to two main components:
- We want to design a clamp that has an inner diameter equal to the lens when it's in its closed position.
- We want there to be two brackets along the outer perimeter of the clamp that look parallel to eachother when the clamp is in its closed position.
Component 1:
Let's keep in mind that:
- We don't want to introduce so much natural flex that the 3D print may break when being closed.
- We don't want to introduce so little natural flex that the 3D print may break when being opened.
The diameter of the lens is 20.6 mm where we want the clamp to be placed and, keeping the bullet points above in mind, I decided that a diameter of 22.3 mm was good for the "open" state (this is large enough to slip past the largest diameter of my specific lens). We want to design a clamp where the inner diameter is equal to 20.6 mm when closed and 22.3 mm when open. If we rephrase this requirement it starts becoming more obvious what we're trying to do. We actually want to design an open circle where the inner circumference is equal to the circumference of our lens both when closed and open. So let's bring out a few simple formulas and solve for this equality. The circumference (C) of a circle is given by:
C = π × d, (where π = 3.14 and d is the diameter of the circle).
If we insert the diameter of our lens, d = 20.6 mm, in this formula we get:
C1 = 3.14 × 20.6 mm = 64.68 mm.
If we instead insert the diameter of the clamp in its opened position, d = 22.3 mm, we get:
C2 = 3.14 × 22.3 mm = 70.02 mm.
We can now use the difference between these two circumferences to find out what our opening angle needs to be. To do this, we first determine the arc length, L, of the circle segment we want to remove:
L = C2 - C1 = 70.02 mm - 64.68 mm = 5.34 mm
We plug this info into the formula for the arc length of a circle sector of the largest of our two circles (d = 22.3 mm):
L = θ × π/180 × r, (where L is the arc length, θ is the angle in degrees, π = 3.14, and r = d/2)
5.34 mm = θ × (3.14 / 180) × (22.3 mm / 2)
Solving for θ, this is what we get:
θ = L / ( (π / 180) × (d / 2) ) = 5.34 mm / ( (3.14 / 180) × (22.3 mm / 2) ) = 27.44°.
In my design, I decided to use the nicer looking 27.0° opening instead, removing only 5.25 mm of the total circumference instead of 5.34 mm. This allows for a little slack in the manufacturing process, which is often necessary when 3D printing.
Component 2:
Now, the next thing we need to worry about is where the brackets on the sides will end up when we close the clamp. To solve this, I simplify the problem by assuming that all the flex is happening at the point in the circle 180° across from the opening, as if there was a hinge there. In reality the flex will happen in a larger area than this (I've illustrated my intuitive assumption in the pictures), but we're making our first compliant mechanism here - so doing it 98% correctly is probably good enough!
When we use this simplification we can assume that the brackets will be displaced by 1/4th of the opening angle. This works because we assume that each half of the clamp (left side and right side) will be displaced by 1/2 of the opening angle when we close the clamp, 13.5°. We can therefore imagine that any point along each half will be displaced by a percentage of the total movement of that half. For example, a point at the very top of the clamp (where the opening is) will be displaced by the full 100% of the 13.5°, and a point at the very bottom (180° opposite of the opening) will be displaced by 0%. We are trying to get our brackets to be at the 90°-mark, or 50% of 13.5°, 6.75°, which is more easily recognized as 1/4th of the full 27° opening.
NB: In the screenshot from Fusion 360, 6.75° is rounded up to 6.8°.
NB 2: This component could also be solved with the formula for arc length of circle segments, but personally I found 1/4th of the opening angle to be a more intuitive approach.
Step 4: Compliant Mechanism - Second Challenge
I already introduced this challenge in the previous step, but let's repeat it: "how do we make sure that the holes align with their mates in the piece they attach to?". Have a look at the first picture of this step and keep in mind that we have just determined that the mounting holes will be displaced by 6.75° when we close the clamp. This displacement angle is actually very helpful information, but we still don't know how much the hole itself will be displaced as the clamp "shrinks" from it's 22.3 mm diameter to it's 20.6mm diameter.
My intuitive thought was that the hole would just move "up" to the horizontal line (in the reference frame of the sketches in the pictures), but that's of course wrong. The hole will also move towards the center of the circle as it shrinks. And setting up my sketch to account for this turned out to be the hardest design challenge I faced in Fusion 360 to make this work.
My solution in the end was actually quite simple though: I just made a concentric reference circle in the sketch that shows the inner perimeter of the clamp when it's closed (see the pictures). This way I had set myself up with a reference to both the open and closed state, at the same time. Out from these perimeters we can sketch up an offset hole that can be used to know where the bracket mount will be in each state. As mentioned, we have already calculated the angular offset, so the only thing we need to do is to use a line keeping the offset hole at the same distance from the closed perimeter as the "real" hole has to the open perimeter. I've illustrated this in the images. This hole can then be mirrored along the vertical center axis and we have made a reference sketch containing the offset holes. Meaning: we can now see where the holes will be in both the "open" and "closed" state at the same time. I've attached a screenshot illustrating what I mean by this.
The final "trick", to make everything in our 3D model as realistic as possible, is to make sure that the clamp is displaced with respect to the lens. We want the point that we are assuming will stay still during the opening/closing of our clamp (180° from the opening) to be in the correct place with respect to the other components.
Step 5: 3D Print the Pieces
Split design
In order to make my mount easier to print I made a the design choice to split each lens-mount in half and attaching the two pieces with screws. For the 5x lens I actually split the design in three pieces, so that I could re-use the camera-side bracket from the 1.5x lens. This was only done to save print-time in the event that I made an error in my displacement calculations and needed to re-print the bracket for the 5x lens (I actually had to do this). One fortunate side-effect of this is that I can share the 3D printable design of the camera-side bracket here for anyone with an ADSM302 microscope, and they will only need to make the lens-side themselves. The file is attached here and named "Camera-side-v2.stl".
Tolerances
When 3D printing it is also necessary to keep in mind that most pieces will turn out slightly larger than you design them. This is because the melted filament will "ooze" out to the sides, and it means we often need to design pieces slightly smaller than we want them. Personally I like to use a tolerance of 1/2 the size of the nozzle I'm printing with, so for a 0.4 mm nozzle, I displace any outer perimeter of my design by 0.2 mm. But to be honest this is just a rule of thumb, and totally depends on your slicer settings and actual printer. But keep in mind that scaling down the entire piece does not work because the ooze only happens in the X and Y directions. The height of the model will often be pretty damn accurate.
Attachments
Step 6: Test Fit the Compliant Mechanism
Now we just need to check if the holes align... And they do!
Step 7: Assemble Lens Mounts
I designed my mechanism to be assembled with M2 screws, so let's screw everything together.
If the working distance of your lenses is quite short (like mine are), make sure the screws aren't so long that they will scrape along the surface of what you're trying to look at.
Step 8: Test Fit to Microscope
I designed my pieces to have a slight wiggle (I'm not trying to make professional-grade optics here, and I need to be able to dismount them easily), and I'm super satisfied with the fit. The pictures show how the mounted secondary lenses look on my ADSM302 microscope.
Step 9: See the Result!
Finally. We can harvest the fruits of our work.
The images contain three image sequences and each sequence is ordered so that you will first see an image with the maximum amount of zoom with standard optics. Then with the 1.5x lens, and finally with the 5x lens. As mentioned in the beginning, the numbers 1.5x and 5x are just top-of-my-head estimates used for clarity, and could be completely wrong.
Here is a description of each image sequence:
- This is a 01005 footprint for passive electronic components such as resistors and capacitors. The footprint is from an old PCB ruler I own, and the microscope reveals that it's become quite messy over the years!
- Here we see the same 01005 footprint but we can also see the secondary lens attachment, and the working distance of each.
- This is the end of a "5 mil trace". In electronics a 5 mil trace means that the width of the copper wire is 5/1000th of an inch, or 635 µm. In the reference frame of the image, this 635µm distance is from the bottom of the golden wire to the top of it.
Personally I'm really happy with these results, and I hope that the 5x lens will allow me to identify some micrometeorites (typically spherical and 300-400µm diameter). Micrometeorite hunting is a new hobby of mine so I don't have any pictures of them to show you (yet), but I hope to make an Instructable about how to find them in the future! Hope you learned some tips and tricks about designing for 3D printing in Fusion 360.
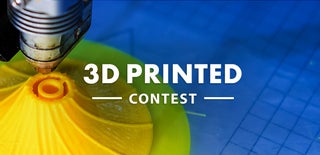
Participated in the
3D Printed Contest