Introduction: "Worlds Simplest" Neuralizer-build (Men in Black Memory Eraser)
Are you going to a costume party in just a few days, but still don't have a costume? Then this build is for you!
With sunglasses and a black suit, this prop completes your Men in Black costume. It's based on the simplest possible electronic circuit that will make a light flash - so you may even have the parts you need laying about at home.
STL and modifyable STEP files available at Printables
Supplies
Electronics:
1x 10W (12V), high brightness, LED. Can be replaced by normal LED if that's what you have available.
1x 330uF electrolytic capacitor. Can be replaced by anything between 100uF and 1000uF
1x Toggle switch. We use a tri-state switch, but you can use anything from a two state toggle to a two button system.
1x 1N4007 diode or similar.
1x 9V battery and connector for the battery
2x resistors (ohm value will vary on your choices above)
Mechanics:
2x Pen. You will harvest springs from them
1x Fat paperclip. You will use it as support for the spring, so it should be of similar thickness as the pen you harvested.
Tools:
3D-printer
Hot glue gun
Sandpaper (optional. Only needed if you want to paint)
Drill or rotary tool (optional, but will make cleaning holes easier)
Spray paint (optional):
Plastic filler
Black primer
Silver
Clear coat
Step 1: Download 3D Files and Print
Files: Printables
The idea is that you could replicate this project using anything from 1 hour (+ printing time of around 6 hours for a 2mm layer 0.4mm nozzle print) to a couple of days, depending on how "polished" you want the looks to be. The electronics can be made in 30 minutes if you have all parts available, the assembly will take minimum 30 minutes, but will take a lot longer if you want to paint and make it look as nice as possible.
We printed all files with the dome upwards. We did not use support material except for the lid-back piece. On the lid-back piece, we used custom support so that we didn't get support inside the opening where we are going to place the LED in the end.
Step 2: Sand and Fill (optional)
In order to get a smooth, metallic looking, finish we sand and fill the 3D print in so that we get rid of those pesky layer lines. If you want to simplify your process further: all steps involving sanding, filling, and painting can be skipped - and you can go for an "out of the box" 3D print look. Just print the parts with a gray filament, and you should be fine.
The sand and fill process will be repeated until you are happy with the smoothness of the print. Keep in mind that the print will actually feel smooth quite some time before it looks smooth. The problem is that you can't really see the dents and irregularities before you use a black primer in a later step. Therefore: be a bit more thorough than you think is necessary when sanding if you want the look to be as good as possible.
We payed extra attention to the domes in either end of the print when sanding, because we wanted them to become as reflective and smooth as possible. The concave grooves along the shaft of the Neuralizer are the most challenging to sand, but we solved this by not sanding down the final layer of filler in these grooves. That means we have a few millimetres of the porous filler in them, but we don't expect that to matter much because they are naturally shielded from the environment and won't easily be scratched.
Step 3: Assemble, Fill, and Prime the Lid With Black Paint
We wanted the area around the LED (around the opening in the lid) to stay black in our final piece, so therefore we assembled this part earlier than the rest of the print. That way we could paint this area with the primer we will use for the remaining parts, then mask it with tape before painting the rest of the print with silver metallic paint.
As one of the pictures show, the lid is not stable when it's been assembled (it's front heavy), so we used a random leftover print as support when we filled the seam between the two parts. This seam will be further filled at a later stage - after we have assembled the rest of the prop.
Step 4: Choose Your Electronics Design
We have provided several alternative circuit schematics.
The simplest possible circuit is really simple. It uses a 3-state switch (shown in the video at the top), where the middle state is "do nothing" and the two other states represents charging and discharging of the capacitor. There is no current limiting resistor to protect the LED because it's specified to run at 12 Volts, and the battery will only provide 9 Volts. In the design we used ourselves we actually did place a small 3 ohm resistor in series with the LED, but as shown in the simplest schematics, that is not strictly necessary. So if you want to make the soldering-job as easy as possible. Go with the simple design.
Alternative Circuit Designs
Schematic Alternative 2 :
In our design we also included a discharge resistor that will make sure that the capacitor doesn't stay charged over long periods of time by evening out the potential stored over the capacitor. The value of this resistor obviously needs to be quite high, so it doesn't allow the capacitor to discharge immediately, but unfortunately I didn't write down the exact value we used, so the 10k in the following schematic is just a guess.
Schematic Alternative 3:
The next alternative circuit is the one that we actually used on the bread board in the video at the top. Here you can see that the 3 ohm current limiting resistor is included, as well as a two button system that replaces the tri-state switch. This allows for a constant current path through the LED, bypassing the charging and discharging of the capacitor - by holding down both buttons at once. This gives the possibility to use the Neuralizer as a flashlight (demonstrated in the pictures).
The switches can also be replaced with simple two-state toggle-switches, but then the R_bleed resistor must be removed because the equivalent to one of the swithes S1 and S2 in the circuit above will always be "pushed" (eg. the toggle switch will always connect one of the two ways). That would mean that R_Bleed will leave a constant current path between the anode and cathode of the battery - draining it.
Schematic Alternative 4:
Next up comes a variant that uses a "normal" LED rated at 2V and ish 20mA. Here, the current limiting resistor must be taken into account, otherwise, the circuit stays the same.
There are more ways to do this circuit, depending on what parts you have available. It is also possible to mix and match between the alternatives posted above. We have included some pictures that shows what happen when you use other capacitor values and other types of LEDs than the 10W versions.
If you want a more detailed walkthrough of the electronics, have a look at the video in the beginning of this Instructable.
Step 5: Solder and Insulate
It's time to solder up the schematics you choose. We chose to include a bleed resistor and a current limiting resistor. The LED, the capacitor and the diode are all polarized - meaning they must be soldered the "correct way" in order to work. For the diode, the white line points toward ground. For the capacitor, there is also a white line pointing towards the leg that should connect to ground. Additionally, the longest of its two legs marks the side that should be connected to the positive potential (towards the battery). The LED has marks that say + and -, but if you use normal LEDs you can use the length of the legs as a guide - using the same trick as for the capacitor.
When you have soldered wires to the LED you should check for shorts by using a multimeter. If you're not careful, it is easy to solder both wires to the heat-sink on the backside of the LED, making a zero resistance path from the positive side of the capacitor to the negative side. This will most likely result in sparks and maybe burnt plastics when the capacitor is discharged (or worst case: a burnt battery if you use a different switch than us).
In order to electrically isolate all open wire, you can use electrical tape, or heat shrink plastics. Don't leave any exposed wire, since these electronics are going to be cramped together inside a sealed plastic container, so it won't be easy to notice if you get any short-circuits in the future.
Step 6: Build and Test Mechanics
In order to make the lid "pop" up when the latch is pressed, we harvested a spring from an old pen, and used a fat paperclip to guide it towards the lid. We glued this system to the switch using hot glue, and cut it to length after the glue had solidified.
Make sure you verify that the mechanics work as intended before the next step, because there won't be a way to fix them as soon as you have assembled the 3D printed parts.
Step 7: Check Fit and Assemble
As mentioned above, be extra careful to check that all parts fit before you seal off the Neuralizer with glue.
We used hot glue to fix the 9V battery in place, and we also used hot glue to mount the two parts of the shaft together. We immediately regretted this desicion, because it solidified way to fast for us to be able to adjust the placement of the two parts relative to each other. However, we were quite lucky, and the misalignment wasn't so bad that we couldn't salvage it. We would still recommend to use a contact glue or something else that doesn't dry up as fast as the hot glue does when it is in contact with such a large surface area.
As soon as we had assembled the entire piece, we placed masking tape on the area that we previously painted black, so that we would not forget to do so later. We also mounted a string to the toggle-switch, in order to make it possible to paint the piece without letting it touch the ground (or our hands).
Step 8: Fill Seams and Sand (optional)
We used hot glue to fill the seams between the 3D printed pieces. This is not recommended, but it was the only thing we had available. The hot glue is not easily sanded, so it takes a long time to get it satisfyingly smooth. And honestly, the smoothness we got wasn't really to the standard we had hoped. If we were to redo this prop, we would buy some putty based plastic filler that could be used for the seams.
After sanding down the hot glue, we added a final layer of spray paint based plastic filler along the seams. This layer was gently sanded with a fine grit sanding-sponge in order to get it as smooth as possible.
Step 9: Prime, Paint and Coat (optional)
We first used a black primer, then a silver paint and finished with a clear coat to give it an extra reflective look, and also to protect the paint. Between each layer we waited approximately 10 minutes - while the piece was hanging outside in a slight breeze. The layers were probably not completely dry within this time, so we wouldn't have wanted to touch it, but they were dry enough for the paint to look nice.
We used some barbeque sticks to hold the print still when we were painting it. The holes where the latch is supposed to be attached are perfect for this purpose, since they will not be visible after the latch has been fitted, and are just large enough to fit the pointy end of the sticks.
When all the layers were sprayed on, we brought the thing inside (just holding the supporting thread we used to hang it up with) and let it hang inside for 24 hours before touching it.
At this point we mounted the latch, using another spring that was harvested from a pen (and cut to length) and a M3 screw and nut.
Step 10: Done!
We were quite happy with the end result. The seams weren't completely gone, as the pictures above will show you, but they were pretty close to be so! Had we used a putty based filler in addition to the spray paint filler we used, we could probably have removed the seams entirely. The layer lines were nowhere to be seen.
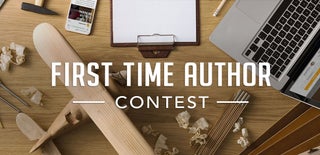
Runner Up in the
First Time Author Contest