Introduction: Mini Root Cellar in Stair Well.
I grew a serious amount of potatoes and carrots this summer. I needed a way to store them. It dawned on me that if I could put a small root cellar in my back stairwell, I would be able to store my produce. I really liked the idea that the door would serve as the door to my root cellar.
It also dawns on me that others have stair wells, and may need root cellars. Further, this build shows some techniques for heat management when insulating such a structure
Step 1: Here Is the Stair Well.
Notice that the door has a doggie door in it. I must build my root cellar narrow enough to leave the doggy door accessible. If I make it slim enough, it'll still serve fine as an emergency exit, though I'm not sure it would be "to code".
Step 2: First Build and Fill the Storage.
I didn't do it this way. I actually had the insulated box half built when it dawned on me that I should build and fill the internal structure first. So I removed the half built box to build this structure.
The structure is quite simple, some 2 * 4s are mounted to the wooden wall of my stair well. (I know, others have cement walls, so you will either have to screw into cement or put in a panel between the 2 * 4s and that wall.)
The width of this structure needs to be calculated. I wanted a 1" gap between the vertical panel (picture 2) and my insulation. This, hopefully, will provide air circulation, eliminating cold spots. The thickness of my insulated wall is about 5", (2" for each styro panel + 1" for the 1 * 4 supports.). So the outside edge of this box needed to be 6" less than the exterior width of my root cellar (5" for insulation, plus the 1" gap.) This width, in my case, being set by where the doggy door is.
The central 2 * 4 is carefully positioned to be under a seam between two panels that make up the floor of each bin. (I don't have a picture of these two panels, sorry.) The back panel is about 2'. The front is just over 1'. At the end of the season, the front panel can be removed, so that the food deep in the bin can be more easily accessed. This, I thought was a really nice trick considering the narrow, deep bins I am making. (Note that I haven't attached these floor panels to the 2 * 4s so that I can remove them as the season goes on for easier access.)
A temporary front flap is put in place (picture 3). To hold it, I just stuck a couple of screws into the outside wall to act as pins for it to rest against. The other side rests against the door jam. It is held towards the outside of the bin by the stored food. When the food gets low, this panel can be removed for easier access.
I built the bin, built the floors of each box, but left them out. I then filled the bottom level with food, put in the first floor, filled that level, put in the floor for the top bin, then filled that level. This made the bins vastly easier to fill then stuffing these deep bins from the front.
Step 3: Very Simple Support Structure
I made an extremely minimalist support structure. I figure that the styrofoam panels are almost structural. The only thing that needs holding, is that the panels need holding in place. It will support no load. Further, even side to side forces are nonexistent. The panels can't move side to side because they bump into the stair well on one side, and into the door on the other. The top panel also bumps into the door jam.
I cut 1 * 4s to the correct size, and put in simple L brackets. The top board sits on top of the vertical board, so if there is any down pressure, it'll go onto the vertical.
The 1 * 4s are mounted to the top of the stair well with one screw each. I didn't even bother to attach the bottom to the bottom of the stair well, its just sitting there like the feet of a chair.
Step 4: Attaching the Inner Panels.
I carefully cut the inner panels to size, and placed them into place. To hold them into place, I made a very simple attachment system. It consists of two screws, two fender washers, and some wire. I drilled a hole thorugh the 1 * 4 and the panel. I pushed a loop of wire through both. On the inside, I stuck the fender washer through the wire loop, then put the screw through the loop. On the outside I did pretty much exactly the same thing. I thought I would have to twist the screw around to tighten it up, but I found that just twisting the wire nice and tight offered sufficient support. (Not much support is needed, all we need is to make sure the panels stay in place, and that it isn't too sloppy. They hardly need to be tightly fastened to the 1 * 4.)
I only placed two of these screw thingies in each styro panel, one through each 1 * 4. Again, it doesn't need to be strong, or particularly tight.
Step 5: The Vapor Barrier.
The biggest challenge to keeping cold out is draft. So in the middle of my insulation sandwich, I placed a plastic vapor barrier.
(I know that the vapor barrier is traditionally placed on the cold side of the wall, however, this is so that condensation doesn't destroy the insulation. With styro insulation, moisture is pretty irrelevant. Further, during winter the cold side is the outside, but in summer, the cold side is the inside.)
First I ran a caulk bead to seal the plastic against the wall of the stair well. Then I laid out the sheet, the sheet is lifted outwards near the door, and pulled outwards at the floor. As far as getting a good seal between the plastic sheet and the door, well, that is covered in a later step.
Step 6: I Installed an Outside Layer of Styro
The outside layer of styro was simply screwed into the 1 * 4 with screws and a fender washer on each. (Styro's nature doesn't work good with a standard screw head, it goes right through. A fender washer works great though.) Again, only 2 screws per panel, one in each 1 * 4.
Oh, about that air gap -- it actually increases the R value of my insulation. Air is a really good insulator.
Step 7: Sealing the Plastic Against the Door.
I needed to make a nice tight seal between the root cellar and the door. To do so, I sprayed foam between the plastic and the outer layer of styrofoam. I sprayed this in while the door was opened, then I closed the door and let it cure. It doesn't harden terribly fast, so I had plenty of time to put it in, then close the door. I get a nice tight seal, but the plastic keeps the foam from sticking to the door. That, of course, would be bad.
Step 8: Styro Door
I put in a styrofoam "door". I thought this appropriate as the temperatures were a bit high in the cellar, and I figured some amount of heat was coming through the door. As winter settles in, I expect the cellar's temperature will drop. When it does, I'll remove this panel to let door heat keep it warm. If that doesn't keep it from freezing (its a bit cold in these parts) I'll put in an arduino controlled heater (another instructable.)
Step 9: It's Working!
With below freezing outdoor temperatures (25 F), the root cellar is a slightly high refrigeration temperature (39 F).
I have been using food from the root cellar. It seems to be in very good shape. If the temperature inside gets too low (about 35) I'll install a little arduino controlled heater, and do an instructable about it.
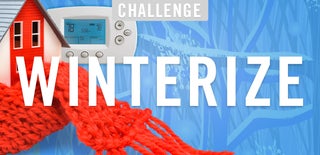
First Prize in the
Winterize Challenge