Introduction: Minimalist Polymer Clay Pendant
I possess neither the patience nor skill required for sculpting polymer clay. They never seem to cooperate with my shaky caffeinated fingers. So I came up with this simple fabrication technique of first giving the clay a sort of bare bones 3D-printed structure, then completing it with polymer clay. No messy sculpting tools or pasta rollers needed!
I'm going to go over 3D modelling a custom shape, filling in the print with polymer clay, then baking and finishing.
Step 1: Tools, Consumables, Software
Tools:
- 3D Printer - I used a Rostock Max V2.
- Exacto knife - you can also use a regular knife or a razor blade
- Oven
- Refrigerator
Consumables:
- 3D Printing Filament - I used Inland's UV color change PLA which changes from natural to purple under the sun! I bet bronzefill or copperfill would also look good.
- Polymer Clay - Sculpey original white.
- Jewellery Findings - brass screw eyes, chain.
- Wax Polish - I used this Renaissance wax because it works really well on both PLA and polymer clay.
- soft cloth - or microfiber. for rubbing in polish.
- Sandpaper - 120, 220, 400, preferably more with finer grits.`
Software:
- Tinkercad - For 3D Modelling. But I attached an STL if you want to go straight to the 3D Printing step.
Step 2: 3D-Modelling a Custom Shape
The goal of this step is to cut out a bunch of holes in a simple 3D-Shape. Tinkercad's Voronoi shape generator is perfect for this.
- Model the solid shape
- drag a box onto the workplane.
- drag a ruler onto the workplane. Click on the box and change its dimensions to 50mm length, 25mm width, and 10mm height. Dismiss the Ruler.
- Generate a Voronoi Patterned "hole"
- Open the Shape Generators tab, then the Tinkercad tab. Find and drag the Voronoi shape generator and drag it onto the workplane.
- Click on "hole" under Inspectors to change the voronoi shape into a hole. While holding down shift, drag the height button from 2mm to 7mm. Then let go of the shift button and drag the height up to 15mm.
- Customize Voronoi pattern
- Drag the voronoi hole over the solid. This gives a preview of the cutouts. As you can see we need to change some parameters. The most important one is cell spacing because the spacing is the positive shape that is going to be printed. If the spacing is too thin then it will exceed the feature size of our FDM 3D printers. I generally do .6mm spacing or greater. I also changed the seed, and increased cell count. Customize your own pattern. You can use the up down left right arrow keys to move the voronoi shape around.
- When you're pleased with the voronoi pattern, select both shapes by dragging over them and click group.
- Model the cutout for jewellery finding
- I'm using these as pendants with brass eyelet screws. So I cut a hole accordingly. I grabbed a cylinder and changed it to a hole, and its dimensions to 2.00 mm diameter with 5mm height. I then rotated it 90 degrees and aligned it with my shape.
- You can also cut a larger cylindrical hole through the shape and hang it straight on a chain.
- Other solid shapes
- I used tinkercad's stock diamond shape.
- The "door" shape is simply a round roof attached to a box.
- I imported a dodecahedron STL from thingiverse.
- Go to Design, then Download for 3D-Printing.
I have attached an STL. You can also edit them on Tinkercad directly. Click "Tinker This" to get your own copy. Select a shape and ungroup to play with the voronoi cutout shape.
Attachments
Step 3: 3D Print
It's a standard and easy print. No support necessary. I did medium resolution of .2mm height, 2 shells, and 10% infill.
Step 4: Fill With Polymer Clay
Make sure your work surface is clean and that you washed your hands before you begin. The clay WILL pick up all the dust.
- Knead clay according to instructions.
- start cramming the clay into the holes.
- flip it over and cram the clay into the voronoi cutouts more. Make sure every opening has clay in them.
- If your clay becomes rubbery and soft like mine did, put it in the fridge for 30 minutes to firm up the clay for easy cutting.
- Slice off excess with your exacto knife. Don't worry about getting it perfect we will sand off excess later.
Step 5: Bake
I baked the the clay according to instructions on the back of my Sculpey box. So roughly 30 minutes for the thinner ones and 1 hour for the dodecahedron and diamond. The temperature isn't hot enough to do anything to the PLA. This is what they look like straight out of the oven.
Step 6: Sand
Sand with the rough 120 grit until clay is flush with PLA. Then move onto finer grits.
Rinse them off with water before sanding with 400 grit. If there is still excess clay sand that facet with the rougher grit and repeat. I only sanded up to 400 but I think it could've used more sanding.
Step 7: Rub in the Wax and Add Finding
Rub in the wax with a soft cloth. Microfiber is ideal for this. The wax gives a nice translucent quality to the PLA and fills in the pores of the polymer clay.
I just used my hands to screw in the brass screw eyes. It fit perfectly and required no glue.
Step 8: Final Thoughts
Next time I make these I'm going to switch to ABS. Clay dust tend to become stuck inside the layer extrusion lines during sanding so I think that using acetone vapor smoothed ABS would eliminate a lot of sanding time. It's still a pretty fast and easy process though, discounting baking and 3D Printing, four beads took about an hour and half to make.
They look best in contrasting colors. The UV color changing PLA works really well and the 3D Printed parts turn purple in the sun it's really cool to watch.
Please share your thoughts, techniques, questions etc.
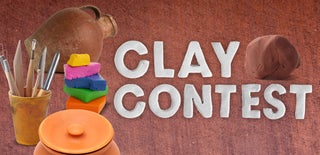
Runner Up in the
Clay Contest