Introduction: Minion Wood Burner
I like junk, I like minions, and I wanted to build a wood burner. That's the full extent of my back story! These three things were what set me on my path for building a minion-shaped wood burner out of scrap metal, an old gas cylinder and a glass baking dish.
Before I started to build this little guy, I came up with a few ideas about what I wanted to achieve:
- I wanted this wood burner to look just like a minion in every way - even down to the cheeky grin. :D
- With the above in mind, the burner also had to be practical - easy to use and clean out after use.
- The fire itself had to be visible - nothing quite beats gazing at the flames of a good fire.
- It had to be made of reclaimed/re-purposed materials. 99% of the projects I've ever made follow this ethos.
Step 1: Sourcing Materials
I am fortunate enough to be something of a hoarder. I rarely throw stuff away if I think it might serve a purpose in future and so my garage is full of what most would consider to be junk. As a result, the only stuff I had to buy specifically for this project was the high temperature paint, the Pyrex glass dish (from a thrift store/charity shop for the equivalent of $3) and a few consumables like welding gas, angle grinder cutting/grinding discs and some masking tape. Everything else came from my stash of bits and bobs I've accumulated from flea markets, boot sales, and skips. In fact, I found this very gas cylinder in a skip. Not a sensible place to dispose of an explosive container so probably just as well that that I was able to rescue it!
In terms of specialist tools for this project you'll definitely need some kind of welding equipment and an angle grinder. The jig saw was very handy for cutting out some of the metal parts but it's not essential. Most parts could be cut roughly with an angle grinder and then filed to shape, and smaller pieces could be cut out with a hacksaw. I'd also recommend using a decent fine tip marker pen for marking out the metal.
In terms of safety, cutting into gas cylinders is NOT recommended. Clearly there must be 100% certainty that there is no gas inside the cylinder before cutting begins. I cannot stress this enough. I'm not going to go into too much detail about this but essentially the only way to be sure is to start with an empty cylinder in the first place and then fill it up with water, thus forcing any remnants of gas out of the cylinder. Do this in a well ventilated area away from heat sources. Empty the water out before cutting into it with your angle grinder as water and electricity don't mix too well either! Also, when it comes to working on the cylinder, bear in mind that heating up the paint and the metal can also give off nasty fumes so again, wear a mask and make sure the area is well ventilated. Also, welding stuff can make things catch on fire, cutting things can throw bits of metal in your face. You get the idea, basically, be sensible and safe.
Step 2: Planning
The planning phase consisted of me typing 'minions' into Google and seeing what came up. I got to know the minion clan quite well, but decided Stuart was the one for me. He's the chap with the single eye and a perfect gas cylinder shaped body. Handy!
The only constraints for this project were the gas cylinder and the Pyrex dish lid. Once I'd established roughly where the lid was going to fit onto the cylinder, I knew I could kind of make the rest up as I went along - making sure that the arms, legs, feet and hands were in proportion to the rest of the burner. All of this was done by eye - I don't actually recall using a measuring tape at any point during this project!
I should add that the reason for opting for Pyrex glass is because it's is resistant to expansion when heated - ordinary glass will almost certainly crack or shatter when exposed to this kind of heat.
As I wanted to load wood into the burner through Stuart's eye, I decided the eye itself would have to be hinged. I also wanted the flue to come out the back of his head (rather than out of the top) as I thought it would be more aesthetically pleasing to keep it out of the way... and poor Stuart doesn't want to look like a chimney! I also needed a way to clear the ash out and a way of lighting the wood and getting some air into the bottom of the cylinder and so the burner was going to need a couple more 'doors' cut into it.
Well, that's it for the planning stage. No CAD files from me I'm afraid, just a rough plan combined with good old trial and error. Let the fun begin!
Step 3: Making the Eye
The eye really is the focus (no pun intended) of this project. It's also the starting point as everything else stems from this, including cutting the cylinder. I started out by placing the Pyrex lid onto a sheet of ~2mm steel and drew round it. Then using a pair of compasses I drew an inner circle. Cut this out so that you're left with a Pyrex dish shape piece of metal that has a hole in the middle of it, let's call this piece 1. Unfortunately I didn't take any pics of this alone but all becomes clear once you see the pics on the next step. Essentially, piece 1 will be welded directly onto the cylinder.
Next, I repeated the processes of drawing around the Pyrex dish onto a piece of sheet metal. For this piece, aptly named 'piece 2' (though perhaps I should've called it the eye-lid) I also needed to include the pupil of Stuart's eye. It turned out that the roll of masking tape I'd bought was perfect for drawing round to form this as shown in the pics. Then, before cutting, I held this up to the cylinder to get an idea of where it would sit and how much metal I would need to leave around the eye in order to fit a hinge, a catch for the door, and to fit mounting brackets for the glass lid itself. Then I cut piece 2 out with the jigsaw. At this point I marked out holes to drill out in each cornea, corner, (sorry) of the eye in order to mount the glass onto the metal. I'll come onto how the glass is fixed to the door a little later. That's the end of the puns for now, eye promise!
Step 4: Attaching Stuart's Eye
I held 'piece 1' onto the cylinder and drew round the inside of it as best I could before cutting this out of the cylinder as shown in the first pic. Then I welded piece 1 onto the cylinder. As you can see, there are lots of gaps in between the cylinder and piece 1. For the larger gap, I used a piece of cardboard to form a template for the fillet needed and then cut this shape out of metal and tacked it into place. The smaller gaps were taken up by filling with molten weld. The idea is to form a good weld around the whole of this piece so that it's airtight and prevents smoke escaping during use.
I welded a heavy duty, steel door hinge onto piece 2 ensuring that with the hinge closed pieces 1 and 2 sit on top of each other neatly with their edges aligned. The other side of the hinge was then welded to piece 1. Voila! One flappy eye door thing attached to a vandalised gas cylinder. This is progress!
Step 5: Adding the Door Catch
This step details how I added the catch to the main door.
The first pic shows the cylinder's base plate cut away from the cylinder. This was re-purposed and used to form Stuarts' head strap. With the head strap in place and a tab welded to it to form a catch for the locking mechanism, it was time to make the mechanism itself which consists of a spring on a spindle. At the end of the spindle is a piece of metal (the end of an old spanner!) and when this catches on the tab, the spring is compressed which keeps the door shut. When the spindle is rotated, the spanner end no longer engages with the tab and the door opens. There are two photos of the catch in the open and closed positions. I used a fairly stiff spring so that the door seals well when shut and stops smoke escaping. This could have been further improved by using some kind of fire rope around the inner circumference of the door.
Step 6: Rear Door
I then went on to form a door in Stuart's, errr, buttocks in order to remove ash from the cylinder. Essentially, the door is formed by cutting out a rectangle shape from the cylinder with the angle grinder (shown in the first pic). A small steel door hinge was then welded in place to allow the door to open/close. To keep the door closed in this instance I used the slide bolt from an old bathroom door (honestly, I throw nothing away). This was welded onto the door and then I welded an old 1/4" socket to the cylinder which the bolt can then slide into.
Step 7: Front Access and Ventilation
I made a small door for the front which I could open to light the fire. This door forms Stuart's front pocket. Again, the door itself was cut out of the cylinder. I then made a hinge using some scrap bits of metal as pictured. I couldn't have easily used another standard hinge for this as placing a flat hinge on a curved surface wouldn't have worked properly.
Essentially the outer tube shown in the photo pivots around the inner bolt. The bolt goes through a couple of small tabs welded onto the gas cylinder. The photo of the finished pocket door explains this much better than I can with words.
I used an old ring spanner to form the handle. There is no latch for this door as tightening the bolt into the tube made the door stiff enough for it to stay where it's put - which is great for modulating air flow into Stuart's torso!
With the doors done it was time to finish Stuart's body. I wouldn't normally suggest putting a smile on someone's face using a high speed cutting disc, but for Stuart I made an exception and got the angle grinder out again. It turned out well and I even went on to polish his teeth with it. Angle grinders can be used to cut some fairly intricate shapes if you're careful - just mind you don't get the disc stuck at an awkward angle as it will likely skip back out at you. It also helped that I was using a fairly worn cutting disc. The smaller diameter disc allows more detailed shapes to be cut out... although the disc starts to wear out very quickly at this point.
Step 8: Legs and Feet
I flipped Stuart onto his head, cut a piece of old tube into two equal lengths and welded them onto his underside. He looks pretty content with the result but I figured I should probably give him some shoes to wear before he got shin splints.
The one benefit of using overpriced, disposable gas bottles for my MIG welder is that I have a stash of empty CO2 cylinders lying around. Again, being careful to ensure that these small cylinders were empty, I chopped a couple up with an angle grinder to form his feet/shoes and welded these to his legs.
For added stability I welded Stuart onto a metal base (about 3mm thick). We don't want him falling over once he's on fire!
I should add that I have since upgraded to a larger, refillable CO2 cylinder for my MIG welder and it works out so much cheaper than the disposable cylinders. Plus I don't have a constant fear of the gas running out mid-weld any more, which is nice.
Step 9: Arms and Hands
Guess what I made the arms with? Yep, another piece of scrap metal. I think this piece had once served it's life as a hand rail. Chop it in half and you've got yourself some pretty convincing minion arms. The great thing about this piece was that the existing curves could be used to imitate elbows without me having to bend the pipe. I welded the arms onto the body, ensuring that these did not obstruct the opening/closing of any of the doors.
The hands were made from chrome tube (an old curtain rail) and some sheet metal scraps. As you can see, the fingers were formed by making cuts part way through the tube. This then allows the fingers to be bent to shape. As you can see on the pics, I had drawn a very rough hand shape on the sheet metal. This gave me some idea of where to weld the fingers to. Once the fingers were in place I literally used a pair of pliers to bend the thin sheet metal round to form a hand. Once the back of the hand was formed, I fettled another piece of scrap to form the front of the hand. Again, there was not an exact science to this. I knew roughly where the fingers were and so I made small cut outs for these before welding the front of the hand into place. This was then bent with pliers to line up roughly with the back of the hand, forming a 3D shape. It was a crude approach but actually quite effective. They looked great once they were sprayed black.
Step 10: Flue
By this point Stuart felt he needed more cosmetic surgery like he needed a hole in the head. Unfortunately, a hole in his head what exactly what he got. I cut a square out with the angle grinder and then formed a circle by making a number of small cuts with the angle grinder. I could've used the jig saw but it wouldn't have been easy to cut out given that this was a curved surface and thick metal. The angle grinder was then used to chop each little piece off and form a round(ish) hole. I then used a piece of metal bar to form an imperfect circle within the hole as shown in the pic. No one is going to see this bit so it doesn't need to be all that pretty! Once this was 'delicately' put into position using a big hammer(!), it was welded into place and I then went on to make the flange. This was simply a piece of sheet metal cut out with the angle grinder again. I think I'd given up with the jig saw by this point as it was painfully slow to use by comparison. I then ground the flange to circular shape, lined up the old boiler flue and then drilled and tapped some holes in the corresponding positions. The flue could then be screwed on once I'd finished spray painting.
Hoarding tip #347: Build up a reputation amongst your peers.
My friend was having his boiler replaced and naturally he called me to see if I wanted any bits from the old one. Perfect! I quickly took the opportunity to grab the flue. The rest of it went to the skip. I know, I know, but I have to set a limit somewhere. I can't keep everything!
Step 11: Pre-paint Prep
The last to thing to do in terms of cutting and welding, was to form the waistband of Stuart's dungarees and add braces. For his dungarees, I wanted there to be an obvious lip between his clothing and his torso so that it looked like he was actually wearing clothes, rather than the waistline just being spray painted on. I achieved this by welding on thin metal strips around his torso as shown in the pics. The braces were then made from strips of thin metal. Using thin metal here worked well as it naturally wanted to bend into the right position. With thicker metal, I'd have struggled to get such a uniform curve across the full length of the strip.
The glass was attached to eye using threaded rod which was bent around the glass and then bolted into place through the holes I made on the door back in step 3. I've added a couple of close up pics of the finished piece to show this more clearly.
I couldn't resist giving Stuart a quick test run. In reality the intention here was to heat the cylinder up to allow the old paint to be removed more easily before spraying it with heat resistant paint as detailed in the next step.
Step 12: Painting
Painting Stuart was a long job. Most of the time was spent masking off each area to maintain a sharp line between the different colours - particularly the blue and yellow. I strongly recommend paying out for good masking tape. You get a much sharper line with the more expensive (coloured) stuff and it peels off without tearing or leaving residue.
I used high temperature primer and paint to finish Stuart. I did three coats of each colour. This paint is able to withstand temperatures of up to 700degC (1292degF) but I had doubts as to how well this would cope with the burner being used long term. The paint also requires heating up to a specific temperature and then left to set. Without a temperature gauge I couldn't do this accurately and so I could have undoubtedly achieved a harder wearing finish if I'd been able to follow the instructions properly. Nevertheless, I was happy with the end result.
Step 13: Fire It Up!
I drew my logo on his front pocket with permanent marker, stuffed his hand full of twigs and then chucked some sand in his eye. I mean that literally, I put sand inside the burner to stop the bottom of the cylinder from rotting though over time. The sand helps to keep the embers off the metal which increases Stuart's lifespan. You've got to be cruel to be kind sometimes!
Since making this instructable Stuart has gone on to live a happy life in my garage. He comes out to say hi on summer evenings and although he's starting to look a little older now that some of the paint has discoloured, he's still got a smile on his face and it's impossible to walk past the little fella without giving him a high-5.
I hope you've enjoyed reading through this instructable. I would welcome comments and questions and if you fancy voting for this project in the Creative Misuse contest, that would be great too.
Thanks,
Rob
...and Stuart!
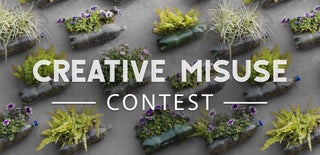
Runner Up in the
Creative Misuse Contest